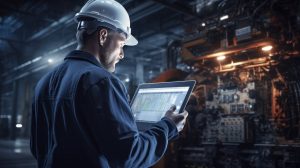
Industrie 4.0 zielt darauf ab, Produktionsprozesse effizienter zu gestalten, die Qualität zu verbessern und die Anpassungsfähigkeit zu erhöhen. Das erfolgt durch die Schaffung von „intelligenten Fabriken“, in denen Maschinen miteinander kommunizieren können, um autonom zu arbeiten, Wartungsbedarf vorherzusagen und Produktionsprozesse in Echtzeit anzupassen. Adobe Stock.com
HDMI-Kabel eingesteckt und schon lassen sich Serien auf einem großen Fernsehbildschirm schauen und nicht nur auf einem kleinen Laptop. Was in diesem Fall schon Standard ist – einfach angeschlossen und schon funktioniert alles – ist bei anderen Geräten, etwa bei Maschinen, die in der Industrie verwendet werden, noch mit großem Aufwand verbunden. Dieser soll im Rahmen von Industrie 4.0 verringert werden.
Dabei geht es um die intelligente Vernetzung von Software, Maschinen und Abläufen in der Industrie durch den vermehrten Einsatz von Informations- und Kommunikationstechnologie. Maschinen sollen nicht aufwändig miteinander verknüpft werden müssen, sondern gemäß „Plug and Produce“ einfach eingesteckt werden und sofort funktionstüchtig sein.
Digitale Zwillinge als Grundlage
Während große Firmen ihren Maschinenpark individuell verknüpfen lassen, arbeitet die Universität Augsburg zusammen mit großen Technologiefirmen wie Intel und mittelständischen Unternehmen an einer kostengünstigeren Vernetzung. Die Forschung an einer Open Source-Lösung soll es allen Firmen ermöglichen, ihre Maschinen über dieses Ökosystem über „Plug and Produce“ zu verbinden. In diesem können Maschinenhersteller, Betreiber und Partner selbst definierte Daten freigeben. Von zentralem Bestandteil ist hierbei der sogenannte Digitale Zwilling. Dieser bildet die Maschine mittels digitalem Typenschild sowie aktuellen Betriebsdaten ab und ist in einer Cloud hinterlegt. Der digitale Zwilling ist beispielsweise dann hilfreich, wenn es zu Änderungen in der Betriebsanleitung kommt, da die Nutzer der Maschine diese sofort einsehen können. Alternativ können Schulungen und Zertifikate hinterlegt werden, sodass ausschließlich geschultes Personal an den Maschinen arbeitet. Zusätzlich können gängige Reparaturen und Wartungshinweise in den Zwilling eingespeist werden, damit alle Maschinenbesitzer von den Erfahrungen profitieren und Zeiten für die Fehlersuche reduziert werden. „Die vom Hersteller gesammelten und verlinkten Daten bieten somit auch anderen Nutzern einen Mehrwert“, erklärt Andreas Leinenbach vom Lehrstuhl für Produktionsinformatik.
Eindeutige Identifizierung zur Ermittlung von CO2-Bilanzen
Um den digitalen Zwilling eines Bauteils, einer Maschine, einer Software oder einer Person zuordnen zu können, wird im Projekt mitunter an einer weltweit eindeutigen Identifizierung zwischen digitalem Zwilling und realem Objekt gearbeitet. Hierbei handelt es sich um eine Art Code, die die eindeutige Zuordnung ermöglicht. „Das kann man sich in etwa so vorstellen wie die Mac-Adresse, die die eindeutige Identifizierung von elektrischen Geräten ermöglicht“, erläutert Leinenbach. Durch diese Identifizierung lässt sich der Weg vom Ausgangsmaterial bis hin zum fertigen Produkt exakt nachvollziehen. Somit ist auch die Ermittlung von CO2-Bilanzen eines Produkts transparent, und kann beispielsweise die Einhaltung gewisser Richtlinien gegenüber dem Gesetzgeber nachweisen.
Bis die Maschinenparks ähnlich gut miteinander verknüpft werden können wie der Laptop und Fernseher mit einem HDMI-Kabel wird es aber wohl noch ein bisschen dauern.
Weitere Informationen: https://www.uni-augsburg.de/de/fakultaet/fai/informatik/prof/pi/