Rüttelt man ordentlich, wird Beton stabiler und tragfähiger. Das heftige Hin und Her lässt Hohlräume zwischen Körnchen und Steinchen schrumpfen, alles wird verdichtet. Auch die Teilchen von Metallpulver in einem 3D-Drucker können so näher zusammenrücken. Wenn der Laser das verdichtete Pulver schmilzt, wird das Bauteil, das Schicht über Schicht aus dem geschmolzenen Metall entsteht, stabiler, die Metallkristalle bilden sich in der Schmelze kleinmaschiger – sofern man alle wichtigen Stellschrauben beim Druckprozess richtig miteinander in Einklang bringt. Dies hat der inzwischen promovierte Fertigungstechniker Oliver Maurer in seiner Doktorarbeit bei Professor Dirk Bähre nachgewiesen. Zum Rütteln verwendete er Schall – schließlich ist beim 3D-Druck Hochpräzision gefragt. „Schall lässt sich sehr exakt kontrollieren und dosieren“, erläutert Oliver Maurer, warum er Schall einer mechanischen Rüttelvorrichtung vorzieht. Weiterlesen
Kategorie: Additive Fertigung
Spannende Beiträge, informative Fachartikel und die neusten Entwicklungen aus dem Themengebiet Additive Fertigung.
Kunststoffe aus Verpackungsabfällen besser recyceln
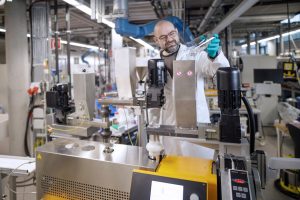
© Fraunhofer IFAM
Am Fraunhofer IFAM werden die gereinigten Kunststoffabfälle im Compounder gemischt, aufgeschmolzen und extrudiert.
Jährlich landen deutschlandweit etwa 5,6 Millionen Tonnen Kunststoffverpackungen nach einmaliger Nutzung im Haushaltsmüll – weniger als ein Drittel davon lässt sich bisher recyceln. Gemeinsam mit der Hochschule Bremen möchte das Fraunhofer-Institut für Fertigungstechnik und Angewandte Materialforschung IFAM den verschmutzten Müll in hochwertige Produkte aus dem 3D-Drucker verwandeln.
Die Menge an Kunststoffmüll steigt, in den vergangenen 30 Jahren hat sie sich deutschlandweit etwa verdreifacht. Besonders Verpackungen aus dem gelben Sack tragen dazu bei: Fielen im Jahr 1994 in Deutschlands Privathaushalten noch 2,1 Millionen Tonnen Kunststoffmüll an, waren es 2023 bereits 5,6 Millionen Tonnen. Umso wichtiger ist es, die Einmalprodukte, die größtenteils auf Basis von Erdöl hergestellt werden, aufzubereiten. Weiterlesen
Mobiles Messgerät prüft Kunststoffpulver in Sekundenschnelle
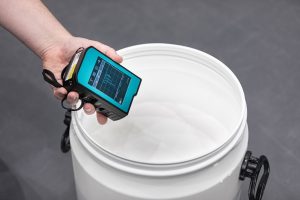
© Fraunhofer IPA/Foto: Rainer Bez Wird das mobile Raman-Spektrometer auf das Kunststoffpulver gerichtet, zeigt das Display des Messgeräts eine Kurve an, die Rückschlüsse über den Zustand des Pulvers zulässt.
Den Alterungszustand von gebrauchtem Kunststoffpulver zu ermitteln, war bisher ein zeitraubendes und teures Unterfangen. Doch nun hat ein Wissenschaftler vom Fraunhofer IPA ein Prüfverfahren entwickelt, das binnen Sekunden Ergebnisse liefert. Die Kosten für 3D-gedruckte Bauteile könnten deshalb sinken.
Man sieht ihm sein Alter kaum an: Das Kunststoffpulver, das beim 3D-Druck zum Einsatz kommt, wirkt meist noch wie neu, wenn es den ersten Druckprozess durchlaufen hat. Beim Selektiven Lasersintern, einem weit verbreiteten 3D-Druckverfahren, wird das Kunststoffpulver flächig aufgebracht, erwärmt und an genau definierten Stellen mit einem Laserstrahl verfestigt. Dieser Vorgang wiederholt sich Schicht für Schicht, bis das gewünschte Bauteil fertig ist. Dabei wird auch das Pulver, das nicht lokal aufgeschmolzen wird, für mehrere Stunden auf eine Temperatur deutlich oberhalb von 100°C erhitzt und am Ende des Bauprozesses wieder auf Raumtemperatur abgekühlt. Dabei altert das Material. Weiterlesen
Material mit neuartigen Dehnungseigenschaften entwickelt
Metamaterialien sind künstlich entwickelte Materialien, die so in der Natur nicht vorkommen. Ihre Bausteine funktionieren wie Atome in herkömmlichen Materialien, haben aber besondere optische, elektrische oder magnetische Eigenschaften. Entscheidend für die Funktion ist die Wechselwirkung zwischen den Bausteinen: Bislang war diese meist nur mit unmittelbar benachbarten Bausteinen, also lokal möglich. Forschende des Karlsruher Instituts für Technologie (KIT) haben ein mechanisches Metamaterial entwickelt, mit dem sich diese Wechselwirkungen auch über größere Entfernungen im Material auslösen lassen. Das Material könnte Anwendung finden, wenn es um das Messen von Kräften oder das Überwachen von Statik geht.
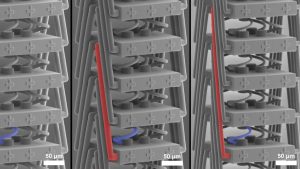
Das neue Metamaterial unter dem Rasterelektronenmikroskop: Eine spezielle Struktur (rot) ermöglicht neue Dehnungseigenschaften. (Abbildung: Jonathan Schneider, KIT)
Mechanische Nachbearbeitung von 3D-gedruckten Werkstoffen aus Metall steigert die Festigkeit
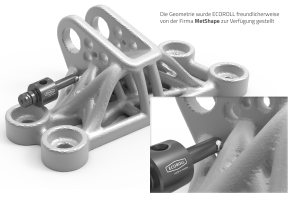
Bild 1: Nacharbeitung eines additiv gefertigten Strukturbauteils durch Festwalzen
Im Trendradar scheint sich der Hype um die additive Fertigung aktuell etwas abzuschwächen, und es kristallisieren sich immer mehr die wirklichen Use-cases heraus. Eine wesentliche Herausforderung besteht allerdings noch immer in der optimierten Konstruktion von Bauteilen. Denn natürlich ist die additive Fertigung aktuell den klassischen Fertigungsprozessen hinsichtlich der Effizienz unterlegen. Die Materialeigenschaft ist hier eine entscheidende Größe und heute noch nicht vollständig überprüfbar. Die Frage ist, wie groß ist die Festigkeit eines additiv gefertigten Bauteils im Vergleich zum herkömmlichen Werkstoff? Weiterlesen
Gebündeltes Licht verbessert 3D-Druck
Thermoplastschäume aus dem 3D-Drucker
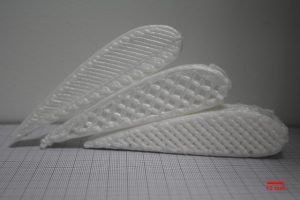
© Fraunhofer ICT Gedrucktes Schaum-Musterbauteil aus PLA…
Das Fraunhofer ICT hat Thermoplastschäume mit sehr geringer Dichte entwickelt. Mittels 3D-Druck könnten daraus individuelle Leichtbauteile gefertigt werden. Weil es bisher problematisch war Schäume bei Additiven Produktionsverfahren einzusetzen, haben Forscher am Fraunhofer IPA eigens dafür eine Verschlussdüse entwickelt.
Für Anwendungen kleiner Losgrößen und individuell angepasster Bauteile ist der 3D-Druck oft die wirtschaftlichste Lösung. Entsprechend kommen zunehmend neue Materialien mit neuen Eigenschaftsprofilen für additive Fertigungsverfahren auf den Markt.
Gedruckte Schaumbauteile sind so eine neue Anwendung. Stand der Technik sind hier mit chemischen Treibmitteln beladene Filamente, die während des Druckvorgangs aufschäumen. Studien an mit chemischem Treibmittel versetztem Polylacticacid (PLA, zu Deutsch: Polymilchsäure) haben gezeigt, dass damit Schaumbauteile mit einer Dichte von etwa 430 kg/m³ erzeugt werden konnten. Im Vergleich zum Kompaktmaterial haben diese Schäume etwa 35 % der Dichte. Weiterlesen
Von Insekten inspirierte Holzbindemittel für den 3D-Druck
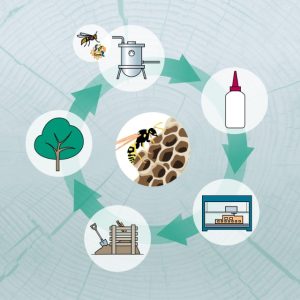
© Fraunhofer IPA
Ein Forschungsteam des Fraunhofer IPA und Fraunhofer IME arbeitet daran, mithilfe von Proteinen und Enzymen aus dem Speichel von Hornissen oder der Seide von Köcherfliegenlarven ein Holzbindemittel herzustellen, das witterungsbeständig und biologisch abbaubar ist. Ziel ist es, einen biologischen Holzklebstoff zu entwickeln, mit dem Holzreste mittels 3D-Drucker zu neuen Naturstoffkomposit-Produkten verarbeitet werden können. Neben der Additiven Fertigung könnte die Kombination aus »Insektenklebstoff« und Holzresten auch für andere Verfahren wie den Spritzguss interessant sein. Potenzielle Anwendungen könnten eine Vielzahl von Produkten aus verschiedenen Branchen sein. Weiterlesen
Nanomaterialien: Glas sinterfrei in 3D gedruckt
Nanometerfeine Strukturen aus Quarzglas, die sich direkt auf Halbleiterchips drucken lassen, erzeugt ein am Karlsruher Institut für Technologie (KIT) entwickeltes Verfahren. Ein hybrides organisch-anorganisches Polymerharz dient als Ausgangsmaterial für den 3D-Druck von Siliziumdioxid. Da das Verfahren ohne Sintern auskommt, sind die dazu erforderlichen Temperaturen deutlich niedriger. Zugleich ermöglicht eine höhere Auflösung Nanophotonik mit sichtbarem Licht.
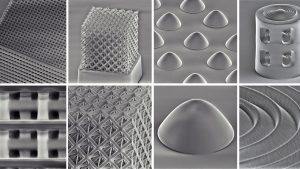
Mit dem neuen Verfahren lässt sich eine große Vielfalt von Quarzglasstrukturen im Nanometermaßstab erzeugen. (Abbildung: Dr. Jens Bauer, KIT
Das Drucken von aus reinem Siliziumdioxid bestehendem Quarzglas in mikro- und nanometerfeinen Strukturen eröffnet neue Möglichkeiten für viele Anwendungen in Optik, Photonik und Halbleitertechnik. Doch bis jetzt dominieren dabei Techniken, die auf dem traditionellen Sintern basieren. Die für das Sintern von Siliziumdioxid-Nanopartikeln erforderlichen Temperaturen liegen über 1 100 Grad Celsius – viel zu heiß für das direkte Abscheiden auf Halbleiterchips. Ein Forschungsteam unter Leitung von Dr. Jens Bauer vom Institut für Nanotechnologie (INT) des KIT hat nun ein neues Verfahren entwickelt, transparentes Quarzglas mit hoher Auflösung und hervorragenden mechanischen Eigenschaften bei deutlich niedrigeren Temperaturen herzustellen. Weiterlesen
Klimafreundliche Kunststoffe für den industriellen 3D-Druck
Mit den Polymer Werkstoffen PA 1101 ClimateNeutral und PA 2200 CarbonReduced von EOS können Unternehmen die Treibhausgasemissionen reduzieren.
Die hervorragenden Eigenschaften der EOS PA 11 und PA 12 Werkstoffe führen zu einer großen Nachfrage dieser für den Plastik 3D-Druck. Eine CO2-reduzierte und sogar klimaneutrale Version davon anbieten zu können, unterstützt Unternehmen dabei, ihre Nachhaltigkeitsziele zu erreichen. Gleichzeitig können sie auf die bewährte Teilequalität und Materialeigenschaften vertrauen.