
Seit Anfang 2020 liefert ein öleingespritzter Schraubenkompressor vom Typ GA 15 VSD+ FF von Atlas Copco, die notwendige Druckluft für die Fräs- und Arbeitsprozesse. Das VSD steht für Drehzahlregelung beziehungsweise Variable Speed Drive, das FF kennzeichnet die „Full-Feature“-Variante, die bereits ab Werk mit einem Kältetrockner ausgerüstet ist. Die 15 kW starke Maschine ist luftgekühlt, benötigt nicht mehr Stellfläche als ein Kühlschrank und arbeitet besonders geräuscharm. (Bild: Atlas Copco)
Auch in kleinen Unternehmen lohnt es sich, Druckluft möglichst sparsam und CO2-neutral zu erzeugen. So ist es JH Maschinenbau in Georgensgmünd durch den Umstieg auf einen drehzahlgeregelten Schraubenkompressor gelungen, den Energiebedarf für die Druckluftproduktion um mehr als 20 % zu reduzieren. Der CNC-Fertiger setzt eine hocheffiziente Maschine aus der neuen GA-VSD+- Serie von Atlas Copco ein.
„Dass Druckluft teuer ist und deshalb möglichst sparsam verwendet werden sollte, war bereits auf der Meisterschule ein Thema“, erinnert sich Nadine Hausmann, Betriebsleiterin bei JH Maschinenbau in Georgensgmünd bei Nürnberg. Das Familienunternehmen wurde vor 30 Jahren von ihrem Vater, Josef Hausmann, gegründet, beschäftigt heute fünf Mitarbeiter und hat sich als CNC-Fertiger und Spezialist für Frästeile einen Namen gemacht. Kunden kommen unter anderem aus der Medizin-, Labor- und Messtechnik. Nadine Hausmann stieg 2009 ins elterliche Unternehmen ein, seit 2018 führt sie den Betrieb. Mit dem Leitsatz ihrer Ausbildung im Hinterkopf ersetzte die Industriemeisterin zunächst Druckluft- durch Elektrowerkzeuge, um so den Bedarf des kostspieligen Mediums zu reduzieren. Weil das Unternehmen aber gleichzeitig expandierte und die Zahl seiner CNC-Bearbeitungszentren und Automationen erhöhte, drehte sich die Verbrauchsschraube dennoch in die entgegengesetzte Richtung. Hinzu kam, dass der Druckluftbedarf, abhängig von Tageszeit und Fräsaufgabe, sehr großen Schwankungen unterliegt. Diese konnte der vorhandene 15-kW-Kompressor, der mit fester Drehzahl arbeitete, nur bedienen, indem er in kurzen Abständen stoppte und dann wieder anfuhr. Diese Arbeitsweise war nicht nur ineffizient, sondern produzierte außerdem jede Menge Lärm und Abwärme. In dieser Situation sei ihr von Atlas Copco ein Beratungsgespräch zum Thema energieeffiziente Drucklufterzeugung angeboten worden, berichtet Nadine Hausmann. Sie nahm spontan an.
Messung ergab 1900 Start-Stopp-Aktionen pro Woche
„Schon auf den ersten Blick war klar, dass sich die Effizienz hier verbessern lässt“, erinnert sich Özkan Demir, technischer Berater bei Atlas Copco, an seinen ersten Besuch im Unternehmen. „Bei einer Strommessung stellte ich später 1900 StartStopp-Aktionen pro Woche fest. Eine unglaublich hohe Zahl.“ Man könnte das mit einem Postboten vergleichen, der seine Briefe mit dem Sportwagen austrägt – der alle zehn Meter mit Vollgas anfährt, um dann direkt wieder zu bremsen.
Der Kompressor arbeitete damals mit einem Betriebsdruck von 10 bar. War dieser Druck erreicht, lief die Maschine noch 15 Sekunden im Leerlauf und stoppte dann. Wenn der Druck nach einiger Zeit auf 8 bar abgefallen war, startete der Kompressor erneut. „In diesem Moment zog die Maschine das Drei- bis Vierfache des Nennstroms“, erläutert Demir. „Die alte Anlage hatte 15 Kilowatt und benötigte bei Last regulär 30 Ampere, zum Start jedoch bis zu 120 Ampere. Diese Stromspitzen im Moment des Anlaufens sind fatal, weil der Energieversorger sich diese extra teuer bezahlen lässt.“ Denn Lastspitzen, die unter Umständen nur kurzzeitig auftreten, bestimmen die Höhe des Leistungspreises. Dieser ist aber über das ganze Jahr fällig und kann sich damit empfindlich auf die gesamte Stromrechnung auswirken. Außerdem entsteht jedes Mal beim Anfahren des Kompressors sogenannter Blindstrom. Dieser wird vom Verbraucher nicht genutzt, findet sich aber ebenfalls auf der Rechnung des Energieversorgers wieder.
Auch die Alternative, den Kompressor statt zu stoppen im Leerlauf zu fahren, hielt Demir für problematisch. „Dann wäre der Kompressor immer bis zum nächsten Belastungszyklus nachgelaufen. Und in der Zeit zieht er immer noch ein Drittel seiner Leistung!“, erklärt Özkan Demir. „Die Alternative zwischen Leerlauf und ständigen Stopps ist letztlich die Wahl zwischen Pest und Cholera. Die ganze Situation war deshalb prädestiniert für einen drehzahlgeregelten Kompressor.“ Denn die Drehzahlregelung vermeidet Stromspitzen ebenso wie Druckschwankungen. Der Motor läuft immer mit der für den Druckluftbedarf zum jeweiligen Zeitpunkt benötigten Drehzahl. Das senkt Energiebedarf und Verschleiß gleichermaßen.
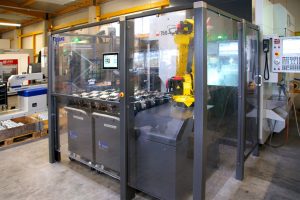
Im neuen 5-Achs-Bearbeitungszentrum können bis zu 60 Teile gleichzeitig vollautomatisch bearbeitet werden. (Bild: Atlas Copco)
Drehzahlgeregelter Industriekompressor bedient Druckluftbedarf auf den Punkt
Die Wahl fiel auf einen öleingespritzten Schraubenkompressor vom Typ GA 15 VSD+ FF von Atlas Copco, der nun in der großen Fertigungshalle steht. Das Kürzel VSD steht für Drehzahlregelung beziehungsweise Variable Speed Drive, FF kennzeichnet die „Full-Feature“-Variante, die bereits ab Werk mit einem Kältetrockner ausgerüstet ist, und das „+“ den ölgekühlten Permanentmagnetmotor des Kompressors. Die 15 kW starke Maschine ist luftgekühlt, benötigt nicht mehr Stellfläche als ein Kühlschrank und arbeitet besonders geräuscharm. „Am Anfang habe ich öfter mal nachgesehen, ob der Kompressor überhaupt läuft, so leise ist er“, berichtet Nadine Hausmann. „Ich kann sogar neben der laufenden Maschine ein Telefonat führen – das war früher nicht möglich.“ Auch die Abwärme, die bei der alten Maschine zum Teil eine große Belastung gewesen sei, habe sich angenehm reduziert. „Der Atlas-Copco-Kompressor ist von der Bauart so konzipiert, das die Wärmeentwicklung äußerst gering ist“, erklärt Demir. „Der niedrige Geräuschpegel liegt zum einen an der Drehzahlregelung und der Schallschutzhaube, zum anderen am Lüftungsventilator, der sich nur dann einschaltet, wenn er benötigt wird.“
Die integrierte Elektronikon-Steuerung regelt den Kompressor so, dass er immer genau die Druckluftmenge liefert, die gebraucht wird. Die maximale Liefermenge beträgt 2,5 m³/min bei 7,0 bar. Momentan werden 0,24 bis 1,0 m³/min benötigt.
Eventuelle Bedarfsspitzen deckt ein 500 Liter großer Druckluftbehälter ab. Die passende Druckluftqualität wird durch den integrierten Kältetrockner sowie einen Partikel- und einen Koaleszenzfilter sichergestellt. Den alten Kompressor ließ JH Maschinenbau als Redundanz am Netz, um die Druckluftversorgung beispielsweise im Falle einer Wartung sicherzustellen.
Betriebsdruck um 2,5 bar gesenkt = Stromkosten gesenkt
Mit dem Einzug des neuen Kompressors konnte der Betriebsdruck schrittweise von 10 bar auf inzwischen 7,5 bar gesenkt werden. Die Druckschwankungen sind dank Drehzahlregelung mit ± 0,1 bar minimal. „An unseren Bearbeitungszentren benötigen wir einen Betriebsdruck von 6 bar“, erklärt Nadine Hausmann. „Derzeit ist unsere Druckluftversorgung noch auf 7,5 bar eingestellt, aber wir könnten noch bis auf 7,0 bar runtergehen, denn bislang gab es keinerlei Probleme.“ Mit der Reduzierung des Betriebsdrucks sinken auch die Stromkosten. Dabei spart man pro Bar etwa 7 % der benötigten Energie ein. „So eine Druckreduzierung funktioniert aber nur mit einer drehzahlgeregelten Maschine“, streicht Demir heraus. „Früher hatten wir hier eine Kaskade zwischen 8 und 10 bar. Bei der Drehzahlregelung stellt man statt eines Be- und Entlastungsdruckes nur einen Sollwert ein. Und den kann man dann schrittweise Zehntel um Zehntel reduzieren.“
Zahl der Start-Stopp-Aktionen geht gegen Null
Die Effizienzverbesserung allein durch den abgesenkten Betriebsdruck beziffert der Atlas-Copco-Experte auf mehr als 14 %. Hinzu komme noch die Reduzierung der Start-Stopp-Aktionen gegen Null, so dass die Drucklufterzeugung insgesamt um mehr als 20 % effizienter geworden sei. „Und bei einer drehzahlgeregelten Maschine wäre ein Start-Stopp aufgrund des integrierten Softstarters auch überhaupt kein Problem“, ergänzt Demir.
Die verbesserte Effizienz wurde vom Bundesamt für Wirtschaft und Ausfuhrkontrolle (Bafa) mit einem Zuschuss von 30 % der Investitionskosten belohnt. 2019 wurde diese Förderung sogar auf 40 % angehoben. „Unsere komplette GA-VSD+-Serie ist förderfähig“, erklärt Demir. „Der Kunde erhält von uns einen Energienachweis und eine Herstellererklärung. Außerdem bieten wir ihm eine Anleitung, wie man beim Förderantrag genau vorgehen muss.“
Rundum-Sorglos-Paket für Service und Wartung des Industriekompressors
Service und Wartung des neuen Kompressors liegen in den Händen von Atlas Copco. „Der Servicetechniker hat seinen Standort nur ein paar Ortschaften von hier entfernt“, sagt Nadine Hausmann. „Im Notfall kann er also in sehr kurzer Zeit vor Ort sein.“ Darüber hinaus hat das Unternehmen eine spezielle Instandhaltungsvereinbarung abgeschlossen. Damit übernimmt Atlas Copco nicht nur alle Service- und Wartungs-Leistungen an der Druckluftanlage, sondern gewährt auch eine auf fünf Jahre verlängerte Garantie für die Maschine. „JH Maschinenbau ist ein Musterbeispiel dafür, wie sinnvoll der Einsatz effizienter Kompressoren auch in kleinen Unternehmen ist“, resümiert Özkan Demir. „Unsere GA-VSD+-Maschinen stellen wir inzwischen ab einer Leistung von 5 kW zur Verfügung. Der Anwender profitiert dabei nicht nur von deutlich reduzierten Stromund Blindstromkosten, sondern auch von geringeren Lärm- und Wärmeemissionen. Letzteres ist vor allem dann interessant, wenn für die Druckluftversorgung kein eigener Raum zur Verfügung steht.“
Weitere Informationen: https://www.atlascopco.com/de-de/compressors
Autorin: Stephanie Banse ist Journalistin in Hamburg