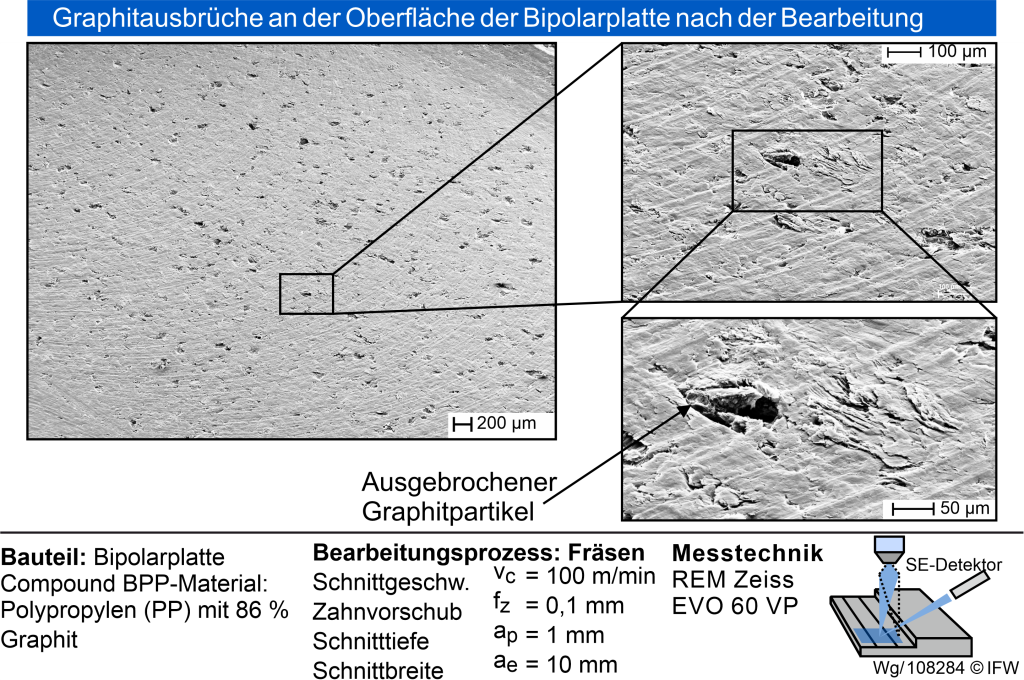
Abb. 1: Ausbrüche von Graphitpartikeln auf der plangefrästen Oberfläche einer Bipolarplatte
Die Brennstoffzellentechnologie bietet vor dem Hintergrund der Dekarbonisierung ein großes Potenzial, herkömmliche Energiewandler durch Wasserstoff als klimaneutrale Alternative zu konventionellen Energieträgern zu ersetzen. Sowohl für stationäre Energieversorgung als auch für die Mobilität kann die Brennstoffzelle eingesetzt werden. Um wettbewerbsfähig zu anderen Technologien zu sein, muss die Leistungsdichte der Brennstoffzellen erhöht und somit der Wirkungsgrad gesteigert werden. Ein möglicher Ansatz ist die deutliche Reduzierung der Verluste im Betrieb. Ein besonderes Potenzial hierfür bietet die Verringerung der ohmschen Verluste im Betrieb der Brennstoffzelle, wodurch eine Erhöhung der Leistungsdichte einer Brennstoffzelle erzielt werden kann. Diese bilden in PEM-Brennstoffzellen (engl.: Proton Exchange Membrane fuel cell), zusammen mit Membranen der Zellen, einen Stack. Durch die Senkung des Kontaktwiderstands zwischen der Bipolarplatte und der Gasdiffusionslage kann der Gesamtwiderstand reduziert werden [1]. Dieser wird bei PEM-Brennstoffzellen mit Bipolarplatten aus Graphit-Compoundmaterial in besonderem Maß durch die Oberfläche der Bipolarplatte beeinflusst.
Angesichts dessen wird im Industrieforum SMART Surfaces am Institut für Fertigungstechnik und Werkzeugmaschinen (IFW) der Leibniz Universität Hannover die Endbearbeitung von Graphit-Compound Bipolarplatten erforscht. Das Industrieforum SMART Surfaces ist spezialisiert im Bereich der Verbesserungen von Bauteileigenschaften durch die spanende Fertigung. Gemeinsam mit Unternehmen aus den Bereichen Fertigungstechnik, Messtechnik und Beschichtungstechnik arbeiten die Wissenschaftler*innen des IFW in einem vorwettbewerblichen Konsortium an der Leistungssteigerung von Bauteilen aus einem breiten industriellen Spektrum. Hierbei werden Grundlagenkenntnisse über die Zusammenhänge zwischen Oberflächen- und Randzoneneigenschaften und Bauteilperformance auf die konkreten Herausforderungen der Unternehmen angewendet. In den aktuellen Projekten wird die Steigerung der Bauteilperformance bei verschiedenen aktuellen Schlüsseltechnologien, wie in der additiv-subtraktiven Prozesskette und der E-Mobilität untersucht.
Im Industrieforum SMART Surfaces wurde hierfür der Einsatz unterschiedlicher mechanischer Feinbearbeitungsverfahren und deren Einfluss auf den Kontaktwiderstand von Graphit-Compound-Bipolarplatten untersucht.
Oberflächendefekte bei der Endbearbeitung von Graphitcompound-Bipolarplatten
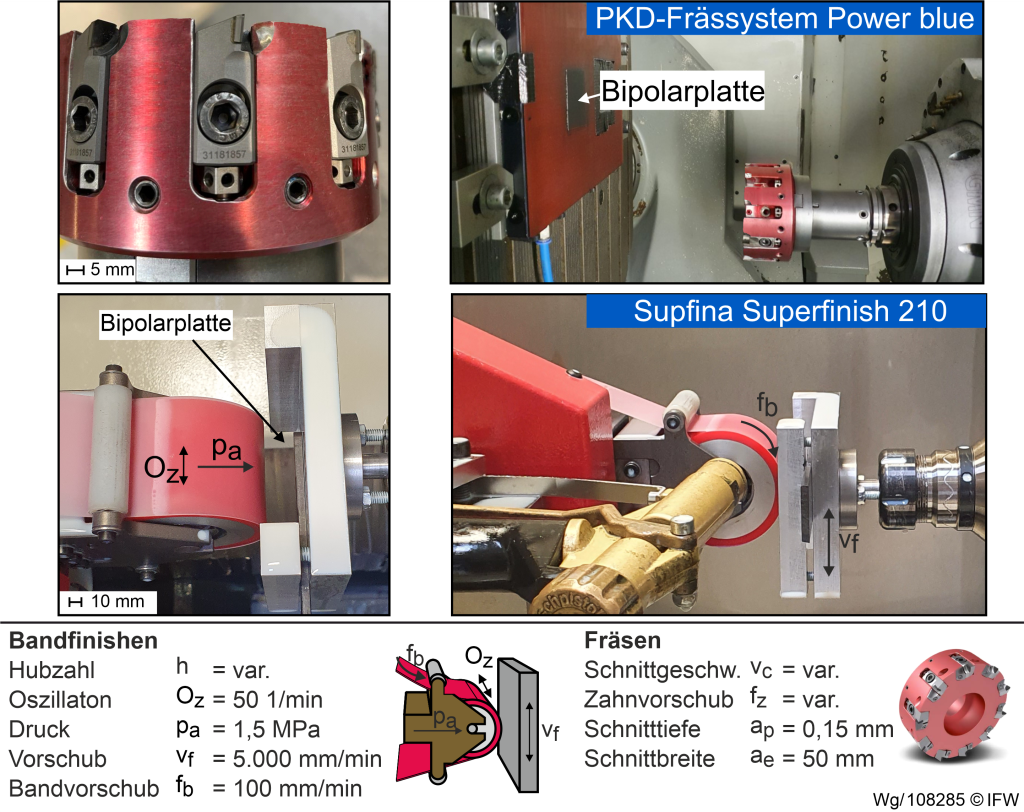
Abb. 2: Versuchsaufbau für die Endbearbeitung der Bipolarplatten durch Fräsen und Bandfinishen
Die Bipolarplatte ist ein Kernbauteil der Brennstoffzelle, da diese gleich mehrere Hauptfunktionen in der Brennstoffzelle erfüllt. Durch die Bipolarplatte wird die Gasverteilung und -trennung geregelt, es wird die Dichtung nach außen und die elektrische Leitung gewährleistet. Ein wichtiger Faktor ist der Kontaktwiderstand zwischen der Bipolarplatte und der Gasdiffusionslage. Im Fokus stehen thermoplastische Graphit-Compound-Bipolarplatten [2]. Die Herstellung von Bipolarplatten aus graphitbasierten Compounds wird maßgeblich von den verwendeten Bindern und Füllstoffanteilen beeinflusst. Insbesondere Compounds mit einer thermoplastischen Bindermatrix haben sich aufgrund ihrer Reproduzierbarkeit und kostengünstigen Fertigung als äußerst geeignet für die Serienproduktion von Bipolarplatten mittels Thermoplast-Spritzgießen erwiesen [3].
Bei der Serienfertigung von Bipolarplatten aus Graphit-Compound-Material ist es das Ziel, die vollständige Geometrie inklusive Flowfield urformend zu fertigen. Es konnte allerdings gezeigt werden, dass eine Endbearbeitung bei spritzgegossenen Bipolarplatten zwingend notwendig ist, da diese eine Spritzhaut mit einer elektrisch isolierenden Wirkung aufweisen [4]. Die maschinelle Endbearbeitung ist notwendig, um den Kontaktwiderstand der Bipolarplatte zu reduzieren, was auch auf die Orientierung der Graphitpartikel in der spritzgegossenen Bipolarplatte zurückzuführen ist. Während die Graphitpartikel in den Randbereichen orthogonal zur Flussrichtung ausgerichtet sind, sind die Graphitpartikel im Inneren der Platte in Flussrichtung orientiert. Diese Ausrichtung hat einen wesentlichen Einfluss auf die Eigenschaften der Bipolarplatte [5]. Allerdings resultieren bei der Endbearbeitung mehrere Herausforderungen: Durch die geringe Dicke der Bipolarplatten und die große Funktionsfläche der Bipolarplatte wird eine besondere Herausforderung an die Spanntechnik gestellt. Durch die Einbindung der Graphitpartikel in eine Kunststoffmatrix liegen zwei Werkstoffe im Compound vor, die sehr unterschiedliche Anforderungen an Zerspanwerkzeuge stellen. Wenn Standardwerkzeuge verwendet werden, die diesen Anforderungen nicht gerecht werden, kann es zu Ausbrüchen der Graphitpartikel kommen und die effektive Oberfläche reduziert sich (Abb. 1).
Fertigungsprozesse zur Endbearbeitung von Bipolarplatten
Um den Kontaktwiderstand zu reduzieren, kann die Oberflächentopographie der Bipolarplatte gezielt beeinflusst werden. Hierfür wurden verschiedene Bearbeitungsverfahren angewendet, um die Abhängigkeit des Kontaktwiderstands von den Oberflächeneigenschaften zu untersuchen. In den Versuchen wurde das Material BMA6 der Firma Eisenhuth GmbH & Co. KG verwendet.
Die experimentellen
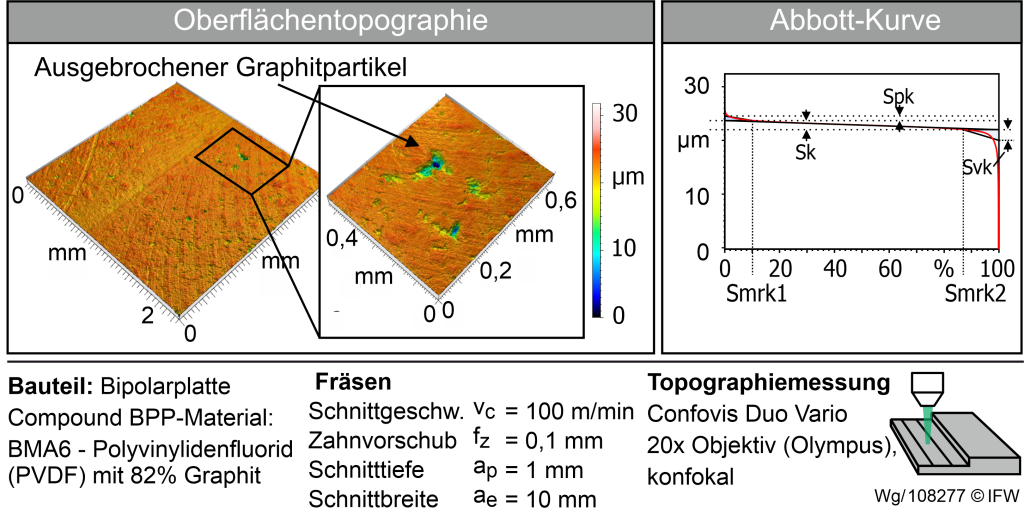
Abb. 3: Anwendung der Abbott-Kurve zur Charakterisierung der Oberflächentopographie der Bipolarplatte und der enthaltenen Oberflächendefekte
Fräsuntersuchungen wurden auf einer Deckel Maho DMU 125P duoBLOCK 5-Achs-Fräsmaschine durchgeführt. Die Maschine wurde ausgewählt, da sie mit einer speziellen Absaugvorrichtung ausgestattet ist, um Graphitpartikel abzusaugen und eine saubere Arbeitsumgebung gewährleistet. Für die Fräsuntersuchungen wurden zwei Werkzeugsysteme von der MAPAL Dr. Kress KG eingesetzt. Einn Eckfräser mit unbeschichteten Hartmetallschneiden um eine besonders scharfe Schneide zu gewährleisten. Das zweite Werkzeug war ein Planfräser der Firma MAPAL, der mit PKD-Fräseinsätzen ausgestattet war. Diese Werkzeuge zeichnen sich durch ihre präzise Keiljustierung aus und ermöglichen die Erzeugung hochwertiger Oberflächen. Beide Werkzeuge wurden mit Wendeschneidplatten verwendet, die eine Breitschlichtschneide aufwiesen (Abb. 2, oben).
Die experimentellen Untersuchungen mit geometrisch unbestimmter Schneide (Bandfinish) wurden auf dem Bearbeitungszentrum Heller H5000 mit einer HSK100-A-Schnittstelle durchgeführt. Zur Bearbeitung wurde das Bandfinishgerät Superfinish 210 von Supfina Grieshaber GmbH & Co. KG am Spannturm der Maschine angebracht und ein Werkstückhalter in der Werkzeugaufnahme verwendet. Durch diese Anordnung war es möglich, das Bandfinishen für Flachbauteile durchzuführen (Abb. 2, unten). Eine translatorische Vorschubgeschwindigkeit von bis zu 5.000 mm/min konnte erreicht werden. Trotz der planaren Bearbeitung der Bipolarplatten konnten charakteristische Kreuzriefenmuster, typisch für das Bandfinishen, auf der Oberfläche erzeugt werden.
Charakterisierung der Oberflächentopographie
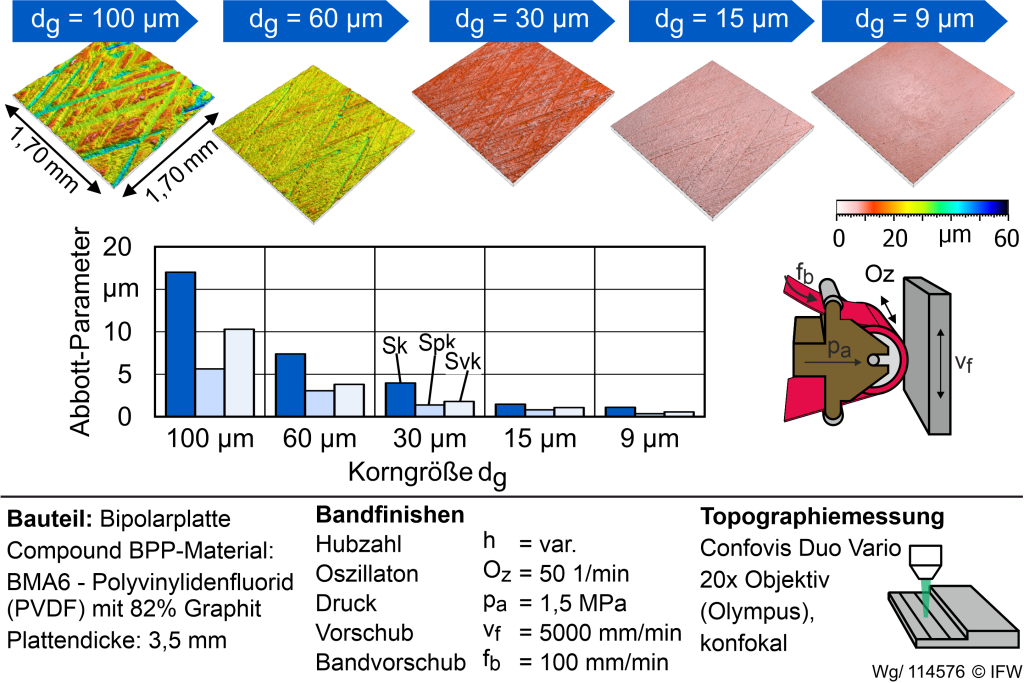
Abb. 4: Oberflächentopographie auf der Kontaktfläche der Bipolarplatte in Abhängigkeit der Korngröße beim Bandfinishen
Zur Analyse des Einflusses der Endbearbeitungsverfahren auf die Oberflächentopographie und die resultierenden Defekte wurden Messungen der Kontaktfläche der Bipolarplatte mit einem konfokalen Mikroskop der Fa. Confovis GmbH, Typ Duo Vario, am IFW durchgeführt, wobei ein 20x-Objektiv verwendet wurde. Zur Beschreibung der Topographie von funktionalen Bauteiloberflächen ist die Abbott-Kurve besonders geeignet. Die Kurve wird gebildet, indem das Profil der Oberfläche von der höchsten Spitze bis zum tiefsten Tal in definierten Abständen von einer horizontalen Ebene aus geschnitten wird. Zu den wichtigsten Parametern der Abbott-Kurve zählen die Kernhöhe Sk, die reduzierte Spitzenhöhe Spk und die reduzierte Talhöhe Svk. Die Kernhöhe Sk beschreibt die Distanz zwischen den höchsten und niedrigsten Ebenen des Oberflächenkerns. Spk gibt die durchschnittliche Höhe der Spitzen über der Kernhöhe an, während Svk die prominenten Täler unterhalb des Kerns kennzeichnet. Für die Charakterisierung von Graphitausbrüchen bietet die Abbott-Kurve einen besonderen Mehrwert, da durch diese Methode das Materialvolumen von Spitzen und das Hohlraumvolumen von Tälern gemessen wird, das Rückschlüsse auf die Menge und Ausprägung der Graphitausbrüche pro Fläche ermöglicht (Abb. 3).
Durch einen stufenweisen Abtrag beim Bandfinishen mit verschiedenen Korngrößen konnte eine defektfreie Oberfläche hergestellt und der notwendige Materialabtrag generiert werden. Es wurden Korngrößen von dg = 100 µm bis dg = 9 µm verwendet. Mit diesen unterschiedlichen Körnungen konnten Kernrauheiten von Sk = 17,0 µm (bei dg = 100 µm) bis zu Sk = 1,1 µm (bei dg = 9 µm) erzielt werden (Abb. 4). Dieses breite Spektrum an Oberflächentopographien wurde genutzt, um den Einfluss auf den Kontaktwiderstand einer einzelnen Bipolarplatte zu untersuchen. Die Endbearbeitung mittels Bandfinishen ermöglicht ein defektfreies Entfernen der isolierenden Schicht von der Kontaktfläche der Bipolarplatte. Der kontinuierliche Bandvorschub verhindert das Zusetzen des Schleifbands bei der Bearbeitung der weichen Bipolarplatten, ein wesentlicher Vorteil gegenüber der Fräsbearbeitung, bei der der Verschleiß der Wendeschneidplatte berücksichtigt werden muss.
Einsatz von PKD-Breitschlichtschneiden
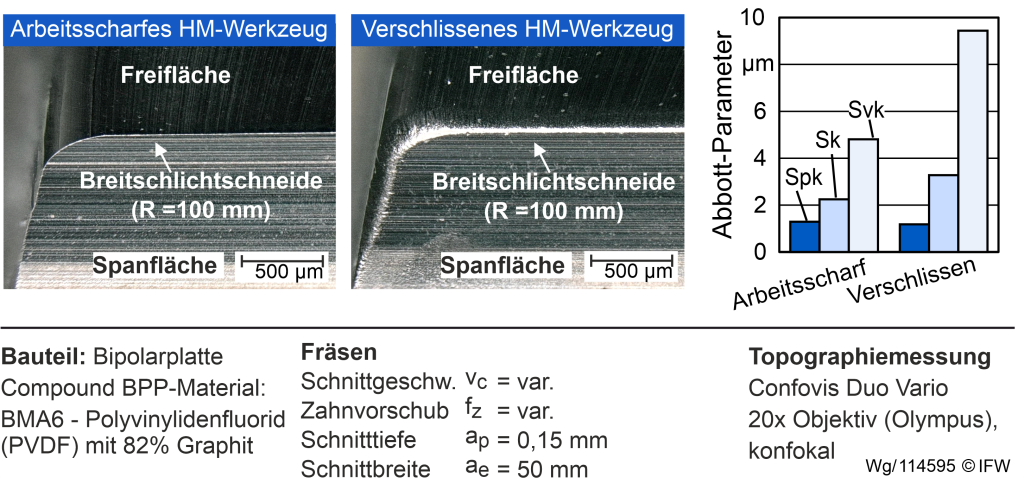
Abb. 5: Einfluss der Geometrie der Breitschlichtschneiden auf die Abbott-Parameter
Bei der Untersuchung des Fräsens als Endbearbeitungsverfahren wurden Werkzeuge mit scharfer Schneidkantenmikrogeometrie und Breitschlichtgeometrie eingesetzt, um Defekte durch Graphitausbrüche zu minimieren. Trotz des Graphit-Anteils im Kunststoff zeigte das Hartmetallwerkzeug nur geringen Schneidkantenverschleiß. Der Vergleich der Oberflächen verdeutlichte, dass der Werkzeugzustand einen signifikanten Einfluss auf die Qualität der Bipolarplatte hat. Insbesondere konnte ein Anstieg des Svk-Werts bei zunehmendem Verschleiß festgestellt werden. Dieser Anstieg der reduzierten Talhöhe Svk deutet auf eine Zunahme von Defekten hin, die durch die verschlissene Schneide erzeugt wurden, aufgrund des Anstiegs der Prozesskräfte. Dies zeigt, dass ausschließlich mit einer besonders scharfen Schneidkantenmikrogeometrie eine defektfreie Oberfläche beim Fräsen von Graphit-Compound Bipolarplatten erzielt werden kann.
Weitere Versuche zur Endbearbeitung von Bipolarplatten wurden mit einem 100 mm Messerkopf und PKD-Breitschlichtschneiden durchgeführt. Das Frässystem war mit einer Einstellvorrichtung ausgestattet, die eine Kompensation des axialen Schneidenversatzes und eine Justierung der Fräseinsätze im Bereich von 5 µm ermöglichte. Dabei wurden drei verschiedene Geometrien der Breitschlichtschneiden in drei Versuchsreihen untersucht, mit Schlichtradien von R = 80 bis 180 mm (Abb. 5). Bei der Untersuchung der Prozessstellgrößen wurde festgestellt, dass der Zahnvorschub einen wesentlichen Einfluss auf die Oberflächentopographie der Bipolarplatten hat. Eine Variation der Schnittgeschwindigkeit zeigt einen konstanten Zusammenhang zu den Rauheitskennwerten, während der Schlichtradius keinen signifikanten Einfluss hat. Allerdings wurde beobachtet, dass bei einer geringen Schnittgeschwindigkeit und einem hohen Zahnvorschub Graphitausbrüche aus der Kunststoffmatrix der Bipolarplatte auftreten, obwohl die PKD-Breitschlichtschneiden mit vergleichsweise scharfen Schneidkanten verwendet wurden. Dies weist darauf hin, dass eine optimierte Kombination von Schnittgeschwindigkeit und Zahnvorschub erforderlich ist, um Graphitausbrüche zu minimieren. Bei den durchgeführten Untersuchungen konnte beim Einsatz der PKD-Werkzeuge kein Verschleiß ermittelt werden. Zusätzlich kann durch die Verwendung des vorgestellten Planfrässystems die Produktivität parallel gesteigert werden.
Kontaktwiderstand der bearbeiten Bipolarplatten
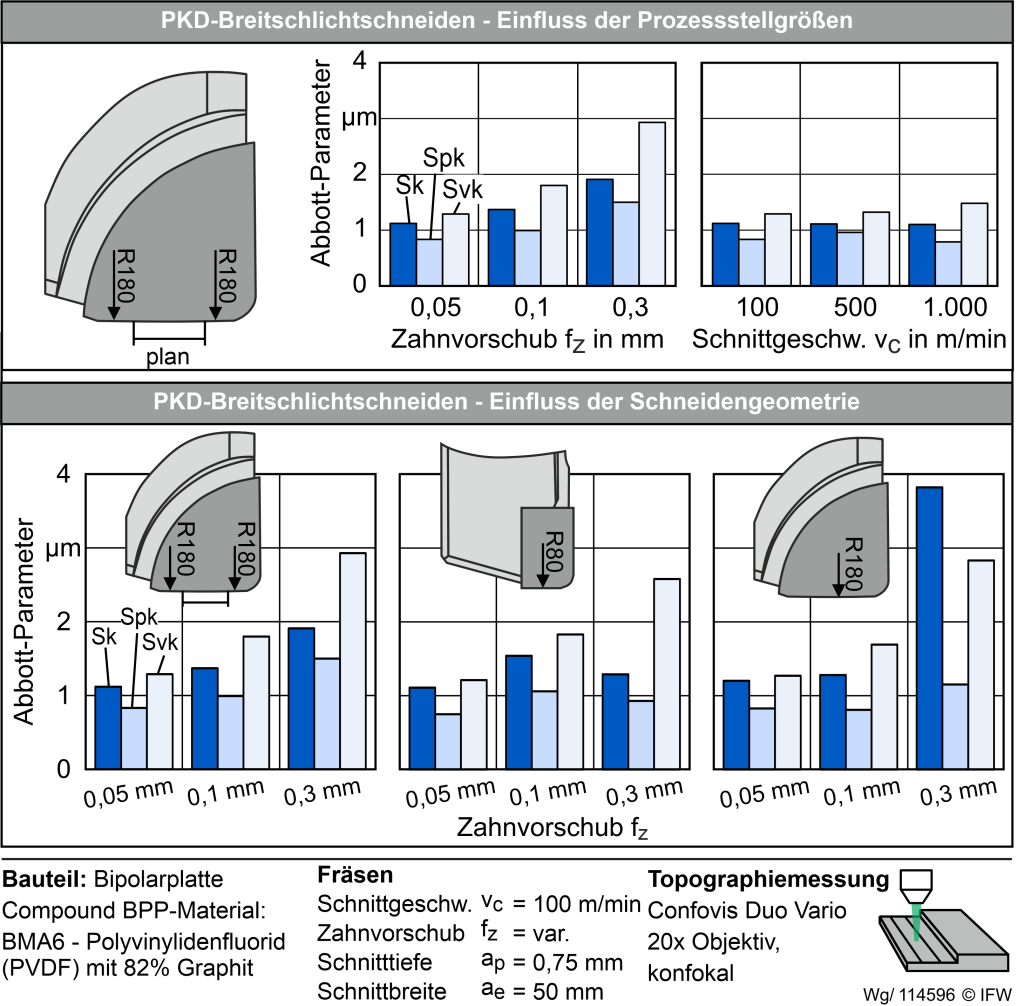
Abb. 6: Untersuchung des Kontakt- und Bulkwiderstands bei unbearbeiteten, einseitig und beidseitig bearbeiteten Bipolarplatten mit der 4-Pol-Messung
In den durchgeführten Versuchen wurde die 4-Pol-Messung eingesetzt, um den flächenspezifischen Durchgangswiderstand der nicht metallischen Bipolarplatten in ihre Einzelwiderstände in Kontakt- und Bulkwiderstand zu unterteilen. Diese Messmethode wurde speziell für die Charakterisierung von nicht metallischen Bipolarplatten auf Basis von Graphit-Compound-Material entwickelt [5]. Dabei wird für einen konstanten Messstrom der Spannungsabfall bestimmt und für die Bestimmung der druckabhängigen Widerstände der Gasdiffusionslagen eine Nullpunktmessung durchgeführt. Durch die simultane Bestimmung des Durchgangswiderstands und des Bulkwiderstands kann der Kontaktwiderstand quantifiziert werden (Abb. 6, links) [5]. Der rechte Teil der Abb. 6 zeigt, dass die beidseitige Endbearbeitung der Bipolarplatte den Kontaktwiderstand erheblich senkte, was den Gesamtwiderstand um etwa 70 % reduzierte.
Weiterhin wurden Proben aus fünf Versuchsreihen mithilfe der 4-Pol-Messung untersucht. Drei Proben wurden mit dem Bandfinishen mit Körnungen von dg = 9 µm, 30 µm und 100 µm bearbeitet. Zwei gefräste Proben wurden ausgewählt: Basierend auf der reduzierten Talhöhe Svk wurde Probe 1 (Svk = 1,10 µm) mit einem geringen Svk-Wert und Probe 2 (Svk = 2,58 µm) mit einem höheren Svk-Wert ausgewählt. Beide Proben wurden mit einem Schlichtradius von R = 80 mm und einer Schnittgeschwindigkeit von vc = 100 m/min bearbeitet, wobei sich der Zahnvorschub unterschied. Die Abb. 7 zeigt, dass die geringsten Rauheitskennwerte der Abbott-Kurve durch das Bandfinishen erzielt werden und damit die größte reale Kontaktfläche aufweisen. Die Untersuchung des Kontaktwiderstands zeigt allerdings, dass die Probe mit der geringsten Rauheit auch den geringsten Kontaktwiderstand erzielte. Es konnte allerdings kein signifikanter Einfluss nachgewiesen werden, da diese Probe gleichzeitig die geringste Plattendicke aufweist. Bei der Endbearbeitung der Bipolarplatten der Versuchsreihe 3 wurde jedoch ein leicht abweichender Gesamtwiderstand gemessen, der auf Schwankungen in der Plattendicke zurückzuführen ist (Abb. 7, unten). Auf Basis dieser Ergebnisse können sich weitere Untersuchungen darauf konzentrieren, optimierte Bearbeitungsstrategien zu entwickeln, mit dem Fokus einer möglichst produktiven Endbearbeitung der Graphit-Compound-Bipolarplatten. Ein Zielkonflikt besteht insbesondere zwischen der Produktivität und der durch Graphitausbrüche verursachten Oberflächendefekte, die unter anderem die Gasdichtigkeit der Bipolarplatte beeinträchtigen können.
Zusammenfassung und Ausblick
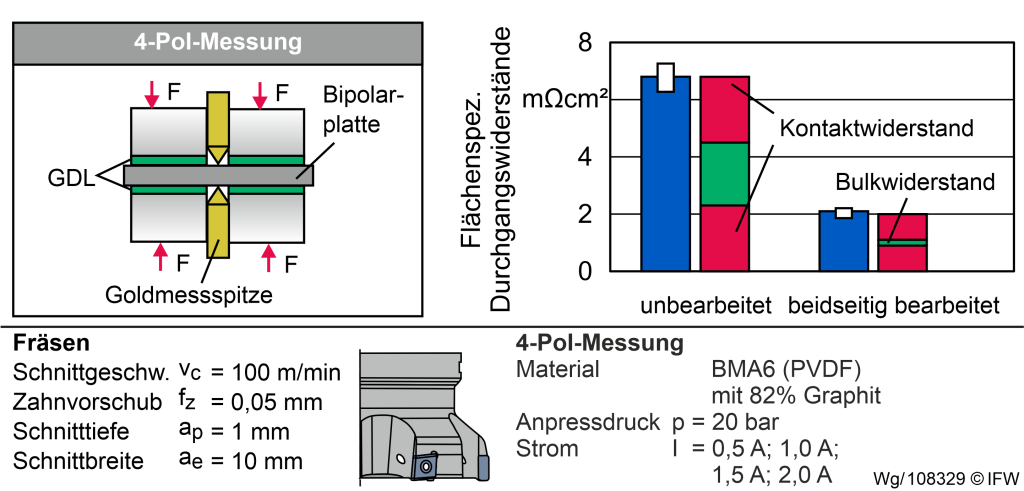
Abb. 7: Untersuchung des Kontaktwiderstands in Abhängigkeit der Oberflächentopographie unter Berücksichtigung der Plattendicke
Im vorgestellten Projekt des Arbeitskreises SMART Surfaces wurde der Einfluss der Endbearbeitung auf den Kontaktwiderstand der Bipolarplatte in einer PEM-Brennstoffzelle untersucht. Es konnte gezeigt werden, dass die geringste Rauheit der Kontaktfläche bei der Bearbeitung mittels Bandfinishen der Bipolarplatten resultiert. Der kontinuierliche Bandvorschub verhindert hierbei gleichzeitig ein Zusetzen des Schleifbands. Durch den Einsatz von PKD-Breitschlichtschneiden konnte eine produktive und prozesssichere Bearbeitung der Bipolarplatten erzielt wird. Mit dem Bandfinishen konnten zwar vollständig defektfreie Oberflächen gefertigt werden, leichte Vorteile hinsichtlich Produktivität und Maßhaltigkeit konnten jedoch durch die Fräsbearbeitung erzielt werden. Der Kontaktwiderstand der Bipolarplatte kann wesentlich durch die Endbearbeitung beeinflusst werden. Die auf der Kontaktfläche eingestellten Oberflächentopographien hatten jedoch nur einen untergeordneten Einfluss auf die Performance der Bipolarplatte. Die hier vorgestellte Methode zur Charakterisierung von Defekten auf der Bipolarplattenoberfläche kann dennoch dazu genutzt werden, um die Qualitätssicherung bei der Herstellung von Bipolarplatten zu verbessern.
Literatur
[1]
Mohr, P.: Optimierung von Brennstoffzellen-Bipolarplatten für die automobile Anwendung, Dr-Ing. Diss., Universität Duisburg-Essen, 2018.
[2]
Kreuz, C.: PEM-Brennstoffzellen mit spritzgegossenen Bipolarplatten aus hochgefülltem Graphit-Compound, Dr.-Ing. Dissertation, Universität Duisburg-Essen, 2008.
[3]
Zentrum für Brennstoffzellen- Technik GmbH; Deutsches Kunststoff-Institut: Charakterisierung hochgefüllter Graphit-Compounds zur Auslegung und Optimierung des Spritzgießprozesses für Bipolarplatten in Brennstoffzellen-Anwendungen, 2011.
[4]
Avasarala, B.; Haldar, P.: Effect of surface roughness of composite bipolar plates on the contact resistance of a proton exchange membrane fuel cell, Journal of Power Sources 188 (2009), S. 225-229.
[5]
Pilinski, N.; Wagner, P.; Grundler, M.; et. al.: Verbundvorhaben NIP II – BePPel – Bipolarplatten für Brennstoffzellen und Elektrolyseure: Abschlussbericht, Oldenburg, 2020.
Weitere Informationen:
Autoren: Berend Denkena, Benjamin Bergmann, Christian Wege, Michael Wöhrle, Dirk Sellmer