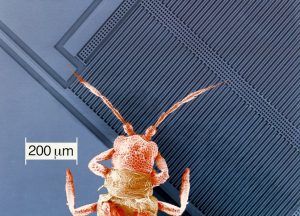
MEMS-Beschleunigungs-Sensor-Kern mit Milbe zum Größenvergleich. Detektionsstrukturen mit Genauigkeitsanforderungen im sub-µm-Bereich. Die gesamte Funktional-Struktur hat Dimensionen von etwa 1mm. Quelle: Bosch
„Mikro-Elektro-Mechanische-Systeme“ (MEMS) begegnen uns in Form von Sensoren überall: Im Auto aktivieren sie den Airbag, im Smartphone erkennen sie Bildschirm-Drehungen. Die Qualitätsprüfung der Sensoren ist allerdings zeitaufwändig. Forschende des KI-Produktionsnetzwerks am Lehrstuhl für Mechatronik arbeiten gemeinsam mit der Robert Bosch GmbH daran, diesen Produktionsschritt mit Hilfe von künstlicher Intelligenz (KI) zu beschleunigen.
Die Herausforderung
Ein Sensor ist nur wenige Millimeter groß, nahezu atomar feine Strukturunterschiede bestimmen seine Genauigkeit. Äußere Faktoren wie zum Beispiel Temperatur wirken sich ebenfalls auf die Sensoren aus. „Der beste Weg, die Messgenauigkeit zu festzustellen, liegt in der Überprüfung der Konstruktionsgrößen aller im Sensor verbauten Komponenten. Wir sprechen von Strukturgrößen von Milliardstel Metern und Massen von Millionstel Gramm“, verdeutlicht Prof. Dr. Lars Mikelsons, Inhaber des Lehrstuhls für Mechatronik, die Herausforderung. Bisher werden diese Größen mit sehr genauen, aber zeitaufwändigen mathematischen Verfahren überprüft. Bei Stückzahlen im Millionenbereich stoßen diese allerdings an ihre Grenzen, künstliche Intelligenz eröffnet hier neue Möglichkeiten.
Die Lösung
Yi Zhang, wissenschaftliche Mitarbeiterin am Mechatronik-Lehrstuhl, erklärt: „Am Computer bauen wir virtuelle Sensoren nach, deren Konstruktionsgrößen wir genau kennen. Mit diesen Sensoren führen wir virtuelle Messungen durch und erhalten Messergebnisse, die wir in einem Datensatz sammeln. Dann kommt die KI zum Einsatz: Alle Messungen geben wir in ein künstliches neuronales Netz. Dieses lernt den Zusammenhang zwischen den Konstruktionsgrößen und der Messung. Die KI weiß am Schluss also, welches Ergebnis X ein Sensor anzeigt, wenn die Konstruktionsgrößen Y sind“.
Das Großartige: Wenn die KI mit genügend Daten „gefüttert“ wurde, kann sie blitzschnell „rückwärts“ von der Messung auf die einzelnen Konstruktionsgrößen und damit die Qualität eines realen Sensors schließen. „Die hohe Geschwindigkeit der von uns entwickelten KI-basierten Analyseverfahren erlaubt es der Halbleiterindustrie, die geforderte kontinuierlich steigende Analysetiefe auch in Zukunft an jedem einzelnen Sensorsystem zu testen und zu ermitteln“, freut sich Mikelsons.
Das KI-Produktionsnetzwerk Augsburg
Das KI-Produktionsnetzwerk Augsburg ist ein Verbund der Universität Augsburg, des Fraunhofer-Instituts für Gießerei-, Composite- und Verarbeitungstechnik IGCV, des Zentrums für Leichtbauproduktionstechnologie (ZLP) des Deutschen Zentrums für Luft- und Raumfahrt (DLR) in Augsburg sowie der Hochschule Augsburg. Beteiligt sind zudem regionale Industriepartner. Ziel ist eine gemeinsame Erforschung KI-basierter Produktionstechnologien an der Schnittstelle zwischen Werkstoffen, Fertigungstechnologien, datenbasierter Modellierung und digitalen Geschäftsmodellen. Der Freistaat Bayern fördert das Projekt mit 92 Millionen Euro im Rahmen der Hightech Agenda Plus.
Weitere Informationen: https://www.uni-augsburg.de/de/forschung/einrichtungen/institute/ki-produktionsnetzwerk/