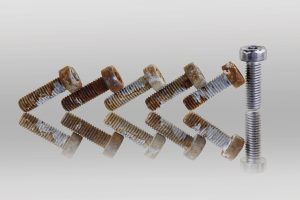
Ohne Galvanotechnik sähen unser Alltag, unsere Arbeitswelt und unsere Wirtschaft alt aus. Sie verhindert allein in Deutschland Korrosionsschäden in Milliardenhöhe und ist durch nichts zu ersetzen. Doch steigende Auflagen bedrohen die Branche.
(Foto: Dr.-Ing. Max Schlötter GmbH & Co. KG.)
Die Galvano- und Oberflächentechnik durchlebt harte Zeiten: Die an sich gesunde Branche kämpft mit permanenten Anpassungsmaßnahmen infolge zunehmend strengerer Umweltauflagen. Das bindet Ressourcen, die an anderer Stelle, beispielsweise der technischen Weiterentwicklung, sinnvoller investiert wären. Schließlich handelt es sich bei der Galvanotechnik um eine Schlüsselindustrie, deren Bedeutung in allen Wirtschaftsbereichen zunimmt. Sie leistet einen wichtigen Beitrag zur Herstellung technologischer Spitzenerzeugnisse in Deutschland. Denn galvanische Oberflächen bieten Vorteile, die ihresgleichen suchen: höchster Schutz und hochwertige Optik bei dünnen Schichten, geringem Gewicht und niedrigen Kosten. Das macht die Galvanotechnik zu einer rundum nachhaltigen Technologie.
Grey-Lists, Black-Lists, Red-Lists sowie Gesetze und Verordnungen, die chemische Substanzen und den Umgang mit ihnen regeln, nehmen zu. In den meisten Fällen ist mit der gesetzlichen Regelung eine eingeschränkte Verwendung oder ein Verbot von Substanzen verbunden. Die Gesetzgebung ist dabei so komplex, dass die oft kleinen bis mittelständischen Unternehmen der Galvano- und Oberflächentechnik die Thematik weder inhaltlich vollständig verstehen noch den damit verbundenen finanziellen Aufwand alleine aufbringen können. Zusätzlich führen die langen Entscheidungswege zu Investitionsstopps, da lange unklar bleibt, wie der gesetzliche Rahmen zukünftig aussieht – und wie lange er so aussieht. Denn im Rahmen von REACH beispielsweise, der Europäischen Chemikalienverordnung zur Registrierung, Bewertung, Zulassung und Beschränkung chemischer Stoffe, autorisiert die EU-Kommission die Verwendung einiger Substanzen nur für eine bestimmte Dauer, die sogenannte Reviewperiod. Was danach kommt, ist ungewiss.
Derzeit sind allein unter REACH etwa 20 Substanzen gelistet, die die Galvanotechnik direkt betreffen. Kurioserweise sind zeitversetzt Substanzen betroffen, die bereits als Ersatz für andere gelistete Substanzen gewählt wurden. Das führt zu einer zusätzlichen Unsicherheit und konterkariert langjährige Forschungs- und Entwicklungsarbeit zur Substitution betroffener Stoffe.
Hinzu kommt, dass es sich bei REACH um eine europäische Verordnung handelt. Das heißt, die gelisteten Substanzen können außerhalb der Europäischen Union verwendet werden und das fertige Produkt – das Bauteil mit Oberflächenschutz – kann problemlos in die EU eingeführt werden. Das gefährdet Europa als Industriestandort.
In Folge dieser komplexen, unübersichtlichen und vor allem nie finalen Situation sind inzwischen auch Endabnehmer so sehr verunsichert, dass sie erwägen entweder im außereuropäischen Ausland Oberflächen einzukaufen oder auf andere Technologien umzusteigen. Eine Substitution erweist sich jedoch als schwierig bis fast unmöglich bzw. ist meist mit Abstrichen verbunden.
Ein Kühlergrill aus Edelstahl beispielsweise an Stelle eines Kühlergrills aus galvanisiertem Kunststoff ist nicht nur schwerer, sondern auch teurer. In der Sanitärindustrie, in der Besteck- und Möbelindustrie oder in der Schmuckbranche würde die Oberflächenvielfalt (Gold, Palladium, Rhodium etc.) und das gute Gefühl von Metall in unseren Händen (Haptik) stark eingeschränkt.
Unersetzliche Schlüsseltechnologie
Bei der Galvanotechnik handelt es sich um eine Schlüsseltechnologie, ohne die sich im täglichen Leben kein Rad mehr drehen würde. 2016 wurden in Deutschland rund 6 Millionen Pkw produziert, weltweit etwa 83 Millionen, davon etwa 16 Millionen von deutschen Automobilherstellern. In einem Pkw befinden sich etwa 3.000 beschichtete Teile. Und auch Fliegen wäre ohne Galvanotechnik unmöglich, befinden sich doch in einem Airbus zwei Millionen beschichtete Teile.
Denn galvanisch erzeugte Oberflächen bieten eine Vielzahl an hervorragenden Eigenschaften: Korrosionsschutz, Gewichtseinsparung, Abschirmung/Schutz vor elektromagnetischen Störwellen, Verschleißfestigkeit, perfekte Optik, vielfältige Kombinationsmöglichkeiten, Temperaturbeständigkeit, Gleitfähigkeit, Reibungsminderung, Kontakt- und Leitfähigkeit, Lötbarkeit, chemische Beständigkeit, angenehme Haptik … Eigenschaften, die andere Verfahren nicht komplett ersetzen können.
Elektronik ohne Galvanotechnik geht gar nicht. Gedruckte Schaltungen, kurz Leiterplatten genannt, die Herzstücke der Hardware in der Elektronik, bestehen aus Isoliermaterial, das durch galvanisches Verkupfern zunächst leitfähig gemacht wird. Anschließend sorgen galvanotechnisch aufgebrachtes Zinn/Blei, Zinn, Palladium, Silber oder Gold für die optimale Verbindung von Leiterplatte und elektronischen Bauelementen.
Zum Selbstverständnis der Galvanotechnik gehört es natürlich auch, dass für diese hochkomplexen Verfahren moderne, hochpräzise arbeitende und umweltschonende Produktionsanlagen entwickelt und in Betrieb genommen wurden und im entscheidenden Maße dafür sorgen, dass Computer, Handys oder Fernseher für jedermann erschwinglich sind.
Effizient und umweltbewusst
Und auch außerhalb der Elektronik ist die Galvanotechnik im Allgemeinen ein kostengünstiges Verfahren mit ständig weiterentwickelter Chemie und Anlagentechnologie. Je nach Anlagentyp können sehr kleine Teile, sogenannte Massenteile, von wenigen Millimetern Größe bis hin zu mehreren Metern große Einzelteile galvanisiert werden.
Schrauben beispielsweise lassen sich durch das Galvanisieren in Trommeln in großen Mengen kostengünstig bei gleichzeitig hoher Qualität beschichten. Beim herkömmlichen Lackieren müssten selbst kleinste Handyschrauben vereinzelt und jede Schraube individuell lackiert werden, weil sie sonst aneinanderkleben und die Gewinde verkleben oder unbeschichtete Stellen aufweisen würden.
Kostengünstig und gleichzeitig umweltfreundlich sind galvanische Verfahren auch dank ihrer Ressourceneffizienz. Produkte und Gegenstände unseres Alltags sollen immer höhere Anforderungen an Funktion und Design erfüllen. Angenehm in Form und Handhabung müssen sie zudem langlebig sein, äußeren Einflüssen widerstehen und ästhetischen Ansprüchen genügen. Dabei werden häufig günstige Grundwerkstoffe wie Stahl, Messing, Aluminium, Zink-Druckguss oder Kunststoff eingesetzt, die diesen Anforderungen zunächst nicht entsprechen. Erst durch galvanisch hergestellte, dünne Oberflächen aus Kupfer, Nickel, Chrom, Zink, Zinn, Silber oder Gold entstehen aus unedlen Grundwerkstoffen hochwertige und langlebige Produkte. Die Schichten, die die Eigenschaften eines Werkstücks weitgehend bestimmen, werden mit einer Dicke von nur wenigen Mikrometern auf die Grundmaterialien aufgebracht. Die wertvollen Rohstoffe werden also äußerst sparsam und gezielt nur dort eingesetzt, wo sie wirklich benötigt werden. Mit lediglich einem Kilo Zink lassen sich beispielsweise eine Tonne Schrauben, mit 0,1 Gramm Gold an die 5.000 elektronische Kontakte vor Korrosion schützen. Galvanotechnik schont die Rohstoffquellen nicht nur durch die sparsame Verwendung wertvoller Schichtmetalle, sondern auch durch die Langlebigkeit der galvanisierten Gegenstände. Galvanische Oberflächen erhöhen die Gebrauchsdauer von Gegenständen, Geräten und Anlagen beträchtlich. Dies vermindert in großem Umfang den Anfall von Schrott und den Bedarf an Rohstoffen und Energie zur Herstellung von Ersatzprodukten. Ökonomen schätzen, dass die galvanische Oberflächenveredelung allein in Deutschland jährlich Korrosions- und Verschleißschäden in Höhe von 150 Milliarden Euro verhindert.
Alternative Verfahren haben oft das Nachsehen
Im Automobilbereich sind die Anforderungen an Oberflächen besonders hoch – und steigen kontinuierlich weiter. Eine herkömmliche Lackierung allein reicht heute als Oberflächenschutz nicht mehr aus. Denn erstens haftet der Lack schlechter auf Stahl als auf galvanisch aufgebrachtem Zink oder Zink/Nickel. Und zweitens schützt eine dünne Lackschicht die Karosserie allein nicht vor Korrosion, weil sie anfällig gegen Steinschläge ist und daher über die garantierte Lebensdauer eines Pkw (zehn Jahre plus) nicht porendicht bleibt. Korrosion würde an solchen Poren besonders hart zuschlagen und die Lebenszeit eines Pkw drastisch reduzieren. Zink- oder Zink/Nickel-beschichtete Stahlbänder, die im Karosseriebau zum Einsatz kommen, lassen den Lack nicht nur fester haften, sondern schützen den darunterliegenden Stahl gleichzeitig vor Korrosion.
Im dekorativen Automobilbereich punkten galvanisierte Kunststoffe: leicht, günstig und dennoch „edel“ und hochglänzend. Auch hier gab es Ansätze, die verchromte, galvanische Oberfläche durch Lacksysteme auf beispielsweise Felgen oder im Interieur zu ersetzen – was fehlgeschlagen ist: Die hohe Wärmeentwicklung beim Bremsen hat den Lack auf der Felge schnell aufgeweicht. Und das Salz auf den Straßen im Winter hat ihm den Rest gegeben.
Bei Befestigungselementen geht es ebenso nicht ohne Galvanotechnik. Herkömmliche Lacke führen bei diesen wichtigen Fahrzeugteilen zu Gewindeverschmierungen und schlechten Passgenauigkeiten.
Auch Edelstahl kommt als Alternative zur galvanischen Beschichtung nur beschränkt in Frage. Neben den höheren Kosten ist das höhere Gewicht, vor allem im Automobilbereich, oft ein K.O.-Kriterium. Wegen der hohen Chloridempfindlichkeit eignet sich Edelstahl auch nicht für Anwendungen im Offshore-Bereich, zum Beispiel bei Windkraftanlagen. Auch hier kommen stattdessen feuerverzinkte Schrauben oder moderne Zink-Nickel-Überzüge zum Einsatz.
Für den Verschleißschutz existiert mit der CVD- und PVD-Beschichtung (Chemical Vapour Deposition/Physical Vapour Deposition) bereits seit gut 30 Jahren eine kostengünstige und technisch hochwertige Alternative für die galvanische Beschichtung – allerdings nur in nicht-korrosionsanfälligen Einbaubereichen und nur für Kleinteile. Gute Verschleißeigenschaften gepaart mit sehr gutem Korrosionsschutz bei gleichzeitiger hoher chemischen Beständigkeit bieten letztlich nur galvanische Hartchrom- oder Chemisch-Nickel-Oberflächen. Und große Teile wie Hydraulikstangen im Flugzeugbau oder Walzen in der Druckindustrie sind aufgrund der Geometrie zudem schwierig im Hochvakuum zu beschichten.
Gesicherte Qualität
Die Herstellung galvanischer Oberflächen lässt sich weitgehend automatisieren und weist eine hohe Prozessfähigkeit auf. Die Arbeitsprozesse in der Galvanik werden ständig weiterentwickelt und den Anforderungen der Zeit angepasst: Energiesparende Automaten, weitgehend geschlossene Wasserkreisläufe, sorgfältige Aufarbeitung und Reinigung des Restabwassers sowie Recycling von Wertstoffen aus Abfällen sind Stand der Technik.
Die Galvanotechnik hat also ökonomisch wie ökologisch eine ganz besondere Bedeutung – für alle Industriezweige und für den Industriestandort Deutschland und Europa.
Ihr Schutz ist programmatisch für den Zentralverband Oberflächentechnik e.V. (ZVO). Denn viele Mittelständler – und das ist die Heimat der galvanotechnischen Industrie in Deutschland – sind mit den kontinuierlich steigenden Anforderungen ihrer Endabnehmer, dem Kostendruck aus Billiglohnländer und der stets neuen Gesetzgebung zum Schutze der Umwelt hier in Europa überfordert. Daher haben sich bereits im Jahr 2000 bestehende Vereinigungen unter dem Dach des ZVO zusammengeschlossen. Er setzt sich ein für die Förderung und Weiterentwicklung der Oberflächentechnik in technisch-wissenschaftlicher, wirtschaftlicher und vor allem politischer Hinsicht und ist hierzu national und international, in Berlin und Brüssel aktiv. Denn durch den Austausch mit Entscheidungsträgern in der Politik können die tatsächliche Betroffenheit der Unternehmen durch gesetzliche Regelungen, die Auswirkungen auf die Branche, den Industriestandort und die Gesamtwirtschaft besser verstanden und Lösungen gefunden werden.
Weitere Informationen: www.zvo.org