Die Fügetechnologie Kleben ist ein elementarer Bestandteil in Medizin, Technik und Alltag. Gegenüber anderen Fügetechnologien besitzt sie bekannte Vorteile wie eine energiearme Applikationsform und eine gleichmäßige Kraftverteilung innerhalb der Fügefläche. Das größte Potential besitzen Klebstoffe beim Fügen unterschiedlicher Werkstoffe, vor allem von Kunststoffen. Kunststoffe sind heutzutage selbst ein Hightechprodukt, werden den Anforderungen entsprechend maßgeschneidert hergestellt und können mit verschiedensten Fasern und Additiven versetzt sein.
Diese enorme Eigenschaftsbandbreite stellt eine große Herausforderung für eine erfolgreiche Klebung dar, da es zu unerwünschten Spannungen in der Fügefläche kommen kann. Um Aussagen über Qualität und Langlebigkeit solch einer geklebten Verbindung zu erhalten, werden aber i. d. R. nur Probekörper oder einzelne Baugruppen stichprobenartig herangezogen und zerstörend geprüft. Wünschenswert wäre hingegen, reale, belastete Bauteile vor Ort einer zerstörungsfreien Prüfung (ZfP) unterziehen zu können, wie es bei metallenen Werkstücken bspw. mittels Ultraschall möglich ist.[1]
Die ZfP von verklebten (Hochleistungs-)Kunststoffen ist auf Grund ihrer komplexen Strukturen bisher kaum etabliert. Daher bestand das Ziel des hier vorgestellten Kooperationsprojektes zwischen dem Günter-Köhler-Institut für Fügetechnik und Werkstoffprüfung (ifw Jena) und dem Forschungszentrum Ultraschall (FZU Halle) darin, die Spannungen und die dadurch induzierten Veränderungen von Klebverbindungen in Abhängigkeit der Alterungsbelastungen mittels Durchstrahlung (ifw Jena) und mit luftgekoppeltem Ultraschall (FZU Halle) zu analysieren.
Auswahl geeigneter Fügepartner
Kunst- und Klebstoffe lassen sich im Alltag auf Grund ihres geringen Gewichtes häufig in Leichtbauanwendungen, wie etwa dem (Schienen ) Fahrzeugbau, finden. An die Fügung dieser Materialien werden dabei hohe Ansprüche gestellt, da bei einem Bauteilversagen potentiell Menschenleben gefährdet sind. Um dieser Entwicklung, auch vor dem Hintergrund der wachsenden Bedeutung der E-Mobilität, gerecht zu werden, wurden als Fügepartner der schwerentflammbare Kunststoff Maywoflamm® ABS V0 (ABS), der glasfaserverstärkte Kunststoff Sustavacu® 6 GF (6 GF), Aluminium und Edelstahl 1.4301 ausgewählt. Für den Erfolg einer Verklebung spielt neben der geeigneten Klebstoffauswahl die Qualität der Oberfläche, insbesondere die Oberflächenspannung, eine entscheidende Rolle. Kunststoffe besitzen meist eine sehr geringe Oberflächenspannung (< 40 mN/m), wohingegen die Oberflächenspannung gängiger organischer Klebstoffe meist 30–60 mN/m beträgt.[2] Daher wurden sämtliche Fügepartner einer Reihe von Oberflächenvorbehandlungen (Pyrosil®-Beflammung, Atmosphärendruckplasma, Sandstrahl) unterzogen, wobei die Plasmavorbehandlung auf sämtlichen Oberflächen eine Oberflächenspannung ≥ 72 mN/m erzeugte, weswegen alle folgenden Proben auf diese Weise vorbehandelt wurden. Als Klebstoffe wurden der Sikaflex®-268 PowerCure (KS1), der SikaForce®-803 L45 (KS2), der Jowat® 690.00 (KS3) und der technicoll® 9464 (KS4) ausgewählt. Diese Klebstoffe besitzen unterschiedliche Shore Härten, wodurch die ZfP an einer großen Variation von Klebfugeneigenschafen getestet werden konnte.
Aufbau der Probengeometrie
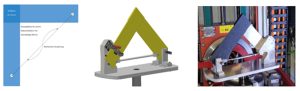
Planung der Probengeometrie (links); Simulation der Konstruktion (Mitte); Einbau der Konstruktion mit Probekörper in die Prüfkammer (rechts).
Zur Durchführung der geplanten Untersuchungen musste zunächst eine Probengeometrie entwickelt werden, welche sowohl für die 2D- und 3D-Durchstrahlungsprüfung als auch die Ultraschalluntersuchung geeignet ist. Für die scannende Luftultraschalluntersuchung mussten die Proben möglichst groß sein, während sie gleichzeitig die Abmessungen des Untersuchungsraumes der Durchstrahlungsprüfung nicht überschreiten durften. Hierfür wurde ein Klebwinkel entworfen, welcher später über einen Wantenspanner mit einer Sollkraft von 50–80 N belastet wurde. Des Weiteren musste eine Konstruktion entworfen werden, welche eine reproduzierbare Positionierung der Prüfkörper und einen sicheren Transport zwischen den beteiligten Projektpartnern ermöglichte. Abb. 1 zeigt die Entwicklung der Vorrichtung von der Planung der Probengeometrie über die Konstruktion der Vorrichtung bis hin zur Integration der Vorrichtung in den Versuchsaufbau der Durchstrahlungsprüfung.
Verkleben der Prüfkörper
Mit Hinblick auf spätere Einsatzmöglichkeiten wurden als Materialpaarungen Maywoflamm® ABS V0/Edelstahl (ABS/Stahl) sowie Sustavacu® 6 GF/Aluminium (6 GF/Alu) ausgewählt, welche mit allen vier Klebstoffen gefügt wurden. Des Weiteren sollten in einige Klebschichten Drahtgewebe eingebracht werden, anhand derer in der Durchstrahlungsprüfung optisch ein möglicher Versatz der Materialien durch das Verspannen und eine anwendungsnahe Belastung detektiert werden kann. Hierfür wurden in Vorversuchen Drahtgewebe aus Kupfer, Messing, Bronze, rostfreiem Stahl sowie einer Folie aus Weich-Kupfer und Acrylatklebstoff in die Klebfläche eingebracht und mittels 2D- und 3D-Durchstrahlungsprüfung untersucht. Dabei erwiesen sich die Kupfer- und Messinggewebe auf Grund ihres Dichteunterschiedes zu den anderen Fügepartner als am besten geeignet.
Für weitergehende Versuche wurden verschiedene Ausführungen dieser Drahtgitter untersucht, welche sich in Drahtdicke und Maschenweite unterschieden (s. Tab. 1). Als Messparameter dienten hierbei die mögliche Gittergeometrie (Dreieck/Quadrat) sowie die Zuschnittmethode (UKP-Laser/manuell). Bei den Untersuchungen stellte sich heraus, dass sich nur das Kupferdrahtgewebe Cu_m mit einer Drahtdicke von 0,056 mm und einer Maschenweite von 0,198 mm eignete, welches mittels UKP-Laser in eine quadratische Form geschnitten wurde. Manuelle Zuschnitte erwiesen sich als zu ungenau, andere Drahtgewebe waren zu steif oder fielen auseinander und die Spitzen der dreieckigen Formen neigten dazu, sich zu verbiegen.
Für die Verklebung der Prüfwinkel wurden aus den Grundwerkstoffen (Metall und Kunststoff) Proben mit den Ausmaßen 50 x 200 mm mit Bohrungen für ein nachträgliches Verspannen gefertigt. Diese wurden nach der Vorbehandlung mit und ohne zusätzliches Drahtgewebe mit einer Soll-Klebschichtdicke von 5 mm miteinander verklebt.
Analyse der Prüfkörper
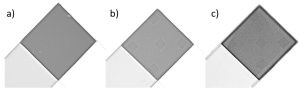
2D-Durchstrahlungsprüfung der Materialkombination a) 6 GF/Alu mit KS1, b) 6 GF/Alu mit KS3 und Drahtgewebe sowie c) ABS/Stahl mit KS3 und Drahtgewebe.
Die verklebten Probekörper wurden mittels 2D- und 3D-Durchstrahlungsprüfung am ifw Jena untersucht, die vergleichenden Untersuchungen dieser Klebwinkel mittels Luftultraschall wurden am FZU Halle durchgeführt.
Durch die 2D-Durchstrahlungsprüfung konnten zum einen Fehlstellen in Form von Blasen innerhalb der Klebschicht bzw. an den Grenzflächen vom Material zum Klebstoff festgestellt werden (s. Abb. 2 a) + b)). Diese zeigten sich auf Grund der geringeren Dichte als helle Flecken in der Bildgebung. Zum anderen konnten die Position und die Geometrie der eingebrachten Drahtgewebe gut bestimmt werden. Da der Dichteunterschied zwischen Kupfer und dem Edelstahl recht gering ist, waren die Drahtgewebe bei der Kombination ABS/Stahl deutlich schlechter auszumachen als bei der Kombination 6 GF/Alu (s. Abb. 2 b) + c)).
Mit der 2D-Durchstrahlungsprüfung konnten zwar generell Fehlstellen und Drahtgewebe detektiert werden, über die genaue Position innerhalb der Klebschicht konnten hingegen noch keine Aussagen getroffen werden. Für eine detailliertere Darstellung wurden die Klebwinkel daher mittels der 3D-Durchstrahlungsprüfung untersucht (s. Abb. 3). Die Abb. 3 a) und f) zeigen die beiden Klebstoff-Werkstoff-Grenzschichten. Hier sind nur minimale Fehlstellen zu erkennen, was für eine gute Adhäsion von KS2 an den Werkstoffen spricht. Neben weiteren kleineren Fehlstellen innerhalb des Klebstoffes zeigen die Abb. 3 c)–e) die genaue räumliche Positionierung der Drahtgewebe innerhalb der Klebstoffschicht. Das Wissen über die genaue Position von Fehlstellen ermöglichte zum einen eine Aussage über die Qualität der Klebung, zum anderen dienten diese Informationen als Referenz für die anschließend durchgeführten Luftultraschallmessungen, welche eine vorangestellte Kalibrierung benötigten.
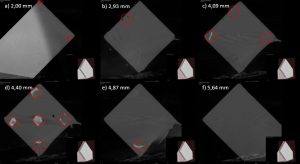
3D-Durchstrahlungsprüfung der Materialkombination ABS/Stahl mit KS2 und Drahtgewebe in a) 2,00 mm, b) 2,93 mm, c) 4,09 mm, d) 4,40 mm, e) 4,87 mm, f) 5,64 mm Tiefe mit markierten Fehlstellen/Drahtgeweben.
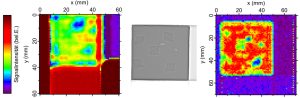
Darstellung der Luftultraschallmessungen der Materialkombination 6 GF/Alu mit KS1 und Drahtgewebe bei verschiedenen Frequenzen (links 200 kHz, rechts 400 kHz) im Vergleich zur 2D-Durchstrahlungsprüfung (Mitte).
Die Untersuchungen mittels Luftultraschall in Transmissionsanordnung zeigten, dass verschiedene Frequenzen zu unterschiedlichen Intensitätsergebnissen führten. Die in Abb. 4 dargestellten Luftultraschallmessungen konnten mit dem Vergleich der 2D-Durchstrahlungsprüfung interpretiert werden. So ließen sich bei einer Frequenz von 200 kHz (s. Abb. 4, links) die erfassten Intensitätsverluste hauptsächlich auf die vorhandenen Drahtgewebe zurückführen, während bei einer Frequenz von 400 kHz (S. Abb. 4, rechts) sowohl die Drahtgewebe, als auch die vorhandenen Lufteinschlüsse detektiert werden konnten. Ein weiterer Interpretationsansatz für die verschiedenen Signalstärken bei unterschiedlichen Frequenzen geht davon aus, dass sich der Ultraschall nicht gleichmäßig in der Tiefe im Probekörper ausbreitet und somit eventuell Rückschlüsse auf die Tiefenlage der Fehlstellen beziehungsweise der eingebrachten Strukturen zulässt. Eine messwertgestützte Verifizierung dieses Ansatzes steht allerdings noch aus. Nach diesen Messungen wurden die Klebwinkel mittels Wantenspannern mit einer Kraft von 50–80 N verspannt und erneut mit den beiden ZfP untersucht. Hierbei konnten durch das reine Verspannen noch keine Veränderungen im Gefüge festgestellt werden. Anschließend erfolgte eine anwendungsnahe Alterungssimulation der Prüfkörper in zyklischen Wechselbelastungen zwischen trockener Kälte und feuchter Wärme. Über 14 Tage wurden so 28 Zyklen mit einer Temperaturänderung von −20 °C bis 80 °C und einer relativen Luftfeuchte von ≤ 10 % bis 95 % durchlaufen.
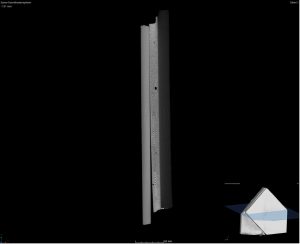
Teilweises Adhäsionsversagen des KS4 am Aluminium nach der Alterung.
Neben rein optischen Veränderungen und Verformungen des Kunststoffes ABS wurde beim KS4 (teilweises) Adhäsionsversagen am Aluminium festgestellt, welches in der 3D-Durchstrahlungsprüfung von Klebwinkeln und realen Bauteilen aufgezeigt werden konnte (s. Abb. 5). Die nach der Alterung durchgeführten Vergleichsmessungen mittels 3D-Durchstrahlungsprüfung zeigten für die mit dem flexiblen KS1 verklebten Klebwinkel eine deutliche gegenläufige Bewegung der Schenkel, welche durch die Verschiebung der festgestellten Fehlstellen (Luftblasen) von 1 mm detektiert werden konnte (s. Abb. 6 a)). Unter Verwendung des starren KS3 konnten hingegen keine Lageveränderungen festgestellt werden (s. Abb. 6 b)).
Fazit
Insgesamt konnte gezeigt werden, dass die 2D-Durchstrahlungsprüfung und die Luftultraschallmessung gut dafür geeignet sind, Fehlstellen innerhalb einer Klebfläche zu detektieren. Während die 2D-Messung keine Aussagen über die genaue Position der Fehlstellen ermöglichte, konnten durch die Luftultraschallmessungen, nach einer geeigneten Kalibrierung, Aussagen zur lateralen Lage dieser Fehlstellen getroffen werden. Die 3D-Durchstrahlungsprüfung konnte mit der Limitierung eines ausreichenden Dichteunterschieds der verwendeten Materialien ein nahezu perfektes Ergebnis über die Ortsgenauigkeit der Fehlstellen in der Klebschicht liefern. Ebenso konnte hierdurch adhäsives Versagen der Klebschicht detektiert werden. Insbesondere bei Bauteilen unter Spannung kann die Durchstrahlungsprüfung wichtige Hinweise auf eine Veränderung der Fügung liefern. Der verfügbare Untersuchungsraum der Durchstrahlungsprüfung limitiert jedoch die mögliche Probengröße für praktische Anwendungen. Für großflächige Proben stellt daher die Ultraschallmessung eine probate Methode zur ZfP von verklebten Bauteilen bzw. zur Bewertung der Integrität der Fügung dar. Ein Aufschluss über die tatsächlich maximal erreichbare Klebkraft kann mit den beschriebenen Methoden hingegen derzeit nicht erfolgen, hierfür sind weiterhin zerstörende Prüfungen unerlässlich.
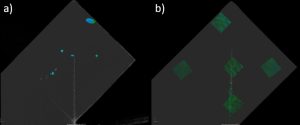
3D-Durchstrahlungsprüfung vor (blau) und nach (grün) dem Verspannen und Altern von a) 6 GF/Alu mit KS1 und b) ABS/Stahl mit KS3 und Drahtgewebe.
Förderhinweis
Die im Rahmen dieser Veröffentlichung beschriebenen Ergebnisse entstanden im Rahmen der Projekte „ASpiK – Analyse von Spannungen in Klebverbindungen“ (Förderkennzeichen 49MF200130) und „SAIKU – Signaturen für die Alterung von Klebeverbindungen mit Ultraschall“ (Förderkennzeichen 49MF200127), welche über das Förderprogramm Innovationskompetenz (INNO-KOM) des Bundesministeriums für Wirtschaft und Klimaschutz gefördert wurden.
Literatur
[1] C. Jadav, S. Patel, Nat. Volatiles & Essent. Oils, 2021, 8, 4899–4918.
[2] W. Brockmann, P. L. Geiß, J. Klingen, B. Schröder, Klebtechnik: Klebstoffe, Anwendungen und Verfahren, Wiley-VCH Verlag GmbH & Co. KGaA, Weinheim, 2005.
Weitere Informationen:
Autor:innen: Dr. Christian Gramse, Dr. Dörthe Jakobi, Andreas Fuchs (ifw Jena)