Das Wachstum der Windkraftindustrie weltweit und die Einführung von Windkraftanlagen mit einer typischen Leistung von mehr als 1 MW haben zur Folge, dass höhere Belastungen und die damit verbundenen Auswirkungen die Lebensdauer der Hauptwellenlager und der Getriebelager beeinträchtigen. Schadens-und Versagensmodi treten früher auf als erwartet und für viele Windparkbetreiber addieren sich die Kosten unerwarteter Reparaturen, die nicht am Turm durchgeführt werden können.
Die Windkraftindustrie fordert deshalb längere Standzeiten für Hauptwellen- und Getriebelager, und die Hersteller arbeiten an Lösungen für den Markt.
„Betreiber planen eine oder vielleicht zwei größere Überholungen der Windkraftanlage über ihren Lebenszyklus“, sagt Tony Fierro, Anwendungsingenieur der Timken Company. „Die Herausforderung besteht darin, dass viele Windkraftanlagen eine größere Überholung noch innerhalb der ersten 7 bis 10 Jahre benötigen. Das bedeutet höhere Ausgaben für Betrieb und Wartung über den Lebenszyklus der Windkraftanlage.
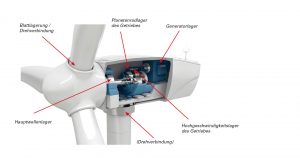
Windkraftanlagen sind mit mehreren verschiedenen Wälzlagern bestückt, die unterschiedlich schnell verschleißen. Die heutzutage in größeren Windkraftanlagen auftretenden höheren Belastungen stellen konventionelle Lagerausführungen auf die Probe – besonders bei Hauptwellenlagern
Kostspielige Reparaturen
Was sind die finanziellen Auswirkungen für Windparkbetreiber, wenn alle sieben Jahre eine größere Überholung erforderlich wird?
„Wenn wir davon ausgehen, dass die mittlere Lebensdauer einer Windkraftanlage 30 Jahre beträgt und die Hauptwelle und das Getriebe alle sieben Jahre überholt werden müssen, bedeutet das vier Überholungen über den Lebenszyklus der Windkraftanlage“, erläutert Fierro. „Mithilfe einer besseren Lagerlösung können Betreiber die Zahl der Überholungen halbieren.“
Wenn die Reparatur von Hauptwelle und Getriebe beispielsweise 300.000 USD kostet (Krankosten eingeschlossen), bedeutet das Gesamtkosten von 1,2 Mio. USD über den Lebenszyklus der Windkraftanlage. Werden diese Überholungen um die Hälfte reduziert, kann der Betreiber bis zu 600.000 USD pro Windkraftanlage einsparen. Für einen typischen Windpark mit 100 Windkraftanlagen können die Einsparungen für Betrieb und Wartung über einen Zeitraum von 30 Jahren bis zu 60 Mio. USD betragen.
Derzeitige Design-Herausforderungen
Modular ausgelegte Windkraftanlagen verwenden normalerweise zweireihige Pendelrollenlager zur Unterstützung und Aufnahme der Hauptwellenlasten. Genauer gesagt, wird der Markt für modulare Windkraftanlagen im Wesentlichen von Pendelrollenlagern in zwei unterschiedlichen Konfigurationen beherrscht, und zwar als Drei- bzw. Vierpunktlagerung. Diese Konfigurationen sind in Abbildung 1 dargestellt.
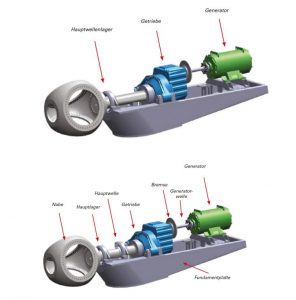
Abbildung 1: Hauptwellenkonfigurationen mit
Drei- und Vierpunktlagerung
Dreipunkt-Design
Im Dreipunkt-Design (Abb. 1: oben) wird die Hauptwelle durch die Drehmomentstützen des Getriebes und durch ein einzelnes Pendelrollenlager vor dem Getriebe unterstützt. Diese Anordnung ermöglicht:
- eine kürzere Maschinengondel und eine reduzierte Masse der Windkraftanlage
- eine hohe Verformung und Fehlausrichtung des Systems
Während dieses Design bestimmte Vorteile wie ein geringeres Gondelgewicht und kleinere Anfangskosten für die Windkraftanlage aufweist, hat die Anordnung mit dem zweireihigen Pendelrollenlager für die Hauptwelle und der Lastübertragung in das Getriebe auch deutliche Nachteile. Ein Problem besteht darin, dass das Lager eine Radialreaktion und eine Axialbelastung durch den Wind nur auf der windabgewandten (DW, Downwind) Rollenreihe aufnehmen muss. Ein weiteres Problem besteht darin, dass die axiale Ablenkung und die Momentlasten aufgrund des zunehmenden Lagerspiels bei fortschreitendem Lagerverschleiß an die Planetenträgerlager des Getriebes übertragen werden. Diese zusätzliche Belastung kann die Planetenverzahnung und somit die Planetengetriebe und die Lagerlasten beeinträchtigen.
Vierpunkt-Design
Im Vierpunkt-Design wird die Hauptwelle durch die Drehmomentstützen des Getriebes und durch zwei Hauptlage vor dem Getriebe unterstützt. Für diese Hauptlager werden häufig Pendelrollenlager eingesetzt, aber andere Lagerausführungen wie Kegel- und Zylinderrollenlager sind ebenfalls üblich. Diese Anordnung bedingt unter Umständen:
- eine längere Maschinengondel und ein höheres Gewicht Windkraftanlage
- eine höhere Systemsteifigkeit
- eine geringere Verformung und Fluchtungsfehler des Antriebsstrangs
Die Leistung der Hauptlager ist im allgemeinen bei Windkraftanlagen mit Vierpunktlagerung besser als bei Anlagen mit Dreipunktlagerung, aber bei einigen Modellen kommt es immer noch zu Störungen, besonders wenn in der hinteren Position ein Pendelrollenlager verwendet wird.
Häufig auftretende Versagensmodi
Micropitting
Die Verwendung eines einzelnen Pendelrollenlagers in der Hauptwellenposition von Windkraftanlagen der MW-Klasse hat sich geändert – während dies früher das bevorzugte Design war, suchen Betreiber jetzt nach einer besseren Lösung. Ein Hauptauslöser dafür sind die vorzeitigen Schäden, die bei dieser Lagerart beobachtet werden, in erster Linie aufgrund von Micropitting (Oberflächenermüdung). Obwohl es keine offizielle Höchstgrenze gibt, gilt ein konventionelles Verhältnis der zulässigen Axial-zu-Radial-Belastung von etwa 25 Prozent als akzeptabel für ein zweireihiges Pendelrollenlager. Die tatsächlichen Axiallasten – in manchen Fällen bis zu 60 % – sind heutzutage in vielen großen Windkraftanlagen erheblich höher als dieser Grenzwert und Betreiber sorgen sich zunehmend um Probleme wie Setzeffekte, ungleichmäßige Lastverteilung zwischen den Reihen, Rollenschränken, Käfigbelastungen, übermäßige Wärmeerzeugung und Verschleiß der Wälzkörper. Bei diesen hohen Axiallasten wird sowohl die Radial- wie auch die Axialbelastung nur von der windabgewandten (DW, Downwind) Rollenreihe aufgenommen. Die windzugewandte Rollenreihe (UP, Upwind) ist oft völlig unbelastet, was zu suboptimalen Betriebsbedingungen führt.
Deshalb treten bei Hauptwellenlagern in Windkraftanlagen mit Dreipunktlagerung oft dieselben Arten von Schäden auf, darunter Micropitting, Kantenstress, Druck auf die Rollenenden, Ausfall einteiliger Käfige, Käfigverschleiß und Verschleiß des Führungsrings sowie Schäden aufgrund von Abriebrückständen. Diese Schäden führen dann bereits im frühen Lebenszyklus der Windkraftanlage zu erheblichen Betriebsausfällen.
Unzureichende Schmierung
Darüber hinaus sind die Betriebsbedingungen am Hauptwellenlager normalerweise nicht ideal für die Erzeugung eines Schmierfilms. Bei einer maximalen Betriebsdrehzahl von etwa 20 Umin-1 sind die Geschwindigkeit und die Schmierfilmdicke oft nicht ausreichend, um die Rauheitsspitzen der Komponenten getrennt zu halten. Außerdem wird die Position und Richtung der Lastzone durch die sich ändernden Nick- und Gierung ständig verlagert – nahezu ohne Verzögerung. Der Aufbau und die Qualität des Schmierfilms werden dadurch unterbrochen.
Bei einem Pendelrollenlager in einer Windkraftanlage mit Dreipunktlagerung wird dieser Vorgang noch beschleunigt. Pendelrollenlager arbeiten mit geringem Radialspiel, so dass das Risiko für Micropitting oder Verschleiß erhöht ist. Frühe Verschleißstufen sind in Abbildung 2 dargestellt, wo der klar erkennbare Verschleißweg in der windabgewandten (DW) Rollenreihe früher oder später die vorgesehene Kontaktgeometrie verändert, was zu höheren Laufbahnbelastungen als berechnet und letztlich zum Lagerausfall führt.
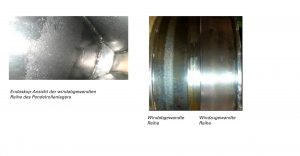
Abbildung 2: Frühe Stufen von Micropitting in einem Pendelrollenlager an der Hauptwelle einer Windkraftanlage
Verbesserte Wälzlager für bestehende Windkraftanlagen
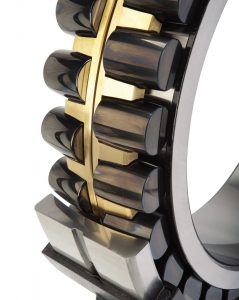
Abbildung 2a: Die verschleißfesten Pendelrollenlager von Timken reduzieren Scherbeanspruchungen und Rauigkeitsinteraktionen und schützen so gegen Verschleiß wie z. B. Micropitting.
Verschleißfeste Wälzlager
Zum direkten Austausch bei bestehenden Windkraftanlagen hat Timken ein verschleißfesteres (WR, Wear Resistant) Pendelrollenlager entwickelt, das spezielle Oberflächentechnik in Verbindung mit optimierten Oberflächenbeschaffenheiten verwendet. Diese WR-Pendelrollenlager schützen die Laufbahnen vor Micropitting, indem die Scherkräfte und die Wechselwirkung der Rauheitsspitzen erheblich reduziert werden. Die behandelte Oberfläche ist eine langlebige und spezielle Beschichtung aus Wolframkarbid und amorphem Kohlenwasserstoff (WC/aC:H).
Diese Beschichtungen sind zwei- bis dreimal härter als Stahl, ein bis zwei Mikrometer stark und haben niedrige Reibungskoeffizienten bei Gleitkontakt mit Stahl. Bei diesen Wälzkörpern mit speziell behandelten Oberflächen dient die Beschichtung zur Glättung und Reparatur von durch Abriebrückstände beschädigten Laufbahnen während des Betriebs. Diese optimierte Oberflächenbeschaffenheit erhöht auch die Schmierfilmdicke, was bedeutet, dass die Rauheitsspitzen effizienter getrennt werden. In Kombination reduzieren diese Verbesserungen die Scherkräfte, die zum Verschleiß führen.
Weitere Merkmale und Vorteile, die insgesamt zu einer verlängerten rechnerischen Lagerlebensdauer und zu einer Reduzierung des Laufwiderstandes führen, sind in Abbildung 3 zusammengefasst.
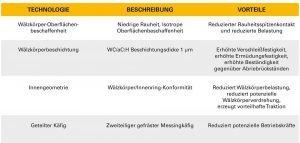
Abbildung 3: Merkmale und Vorteile des verschleißfesten Pendelrollenlagers (WR SRB) von Timk
Eine Kegelrollenlagerlösung
Im Rahmen der Arbeiten an den bei Pendelrollenlagern auftretenden Problemen fanden Timken Ingenieure eine neue Lösung für Windkraftanlagen mit Dreipunktlagerung in Form eines vorgespannten Kegelrollenlagers (TRB, Tapered Roller Bearing).
Das mit einem einteiligen doppelten Innenring und zwei einzelnen Außenringen bestückte Lager kann an Festlagerpositionen auf rotierenden Wellen verwendet werden und ist ein direkter Ersatz für Hauptwellen-Pendelrollenlager des Originalherstellers (unter Verwendung des vorhandenen Stehlagergehäuses des Originalherstellers). Das Lager ist so ausgeführt, dass beide Rollenreihen die Radial- und Axialbelastung zu gleichen Teilen aufnehmen; außerdem wird die Belastung am Getriebeeingang reduziert, da das Lager leichte Winkelfehler kompensieren kann (Abbildung 4).
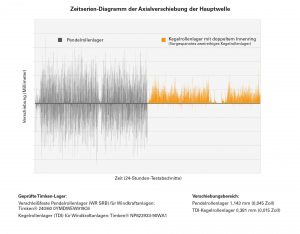
Abbildung 4: Tests zeigen, dass das vorgespannte Kegelrollenlager von Timken die Axialkraft am Getriebeeingang im Vergleich zu einem zweireihigen Pendelrollenlager um 67 % reduziert
In Feldversuchen zeigte das Kegelrollenlager von Timken reduzierten Verschleiß, bessere Fluchtung und geringere Lasteintrag am Getriebeeingang (ohne zusätzliche Last auf die Drehmomentstützen) und eine erhöhte Systemsteifigkeit. Der vorgespannte Zustand dieses hochtrag– fähigen Lagers trägt zur Minderung des Verschleißes und des Gleitens der Wälz– körper bei und sorgt dafür, dass die Last auf beide Reihen verteilt wird, wobei es gleichzeitig größere Fluchtungsfehler als ein Kegelrollenlager mit doppeltem Außenring aufnehmen kann.
Abbildung 5 zeigt dieses Design und die Lösung mit einem zweireihigen Pendelrollenlager im Vergleich:
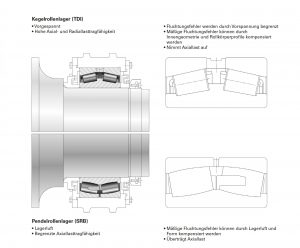
Abbildung 5: Vorgespanntes Kegelrollenlager im Vergleich mit einem serienmäßigen Pendelrollenlager für die Hauptwellenlagerung
Schlussfolgerung
Während Wälzlager ihre betriebskritische Funktion in modernen Windkraftanlagen der MW-Klasse erfüllen, führen dynamische und unvorhersehbare Belastungen zu vorzeitigen und kostspieligen Reparaturen. Damit die Windkraftindustrie ihr Wachstum fortsetzen kann, muss die Zuverlässigkeit der Hauptwellenlager verbessert werden. Die Marktnachfrage treibt die Entwicklung neuer Lösungen zur Umrüstung einzelner Pendelrollenlager in Anlagen mit Dreipunktlagerung voran, entweder mit verschleißfesten Pendelrollenlagern oder mit einem vorgespannten Kegelrollenlagerdesign.
Autoren:
Douglas Lucas: Advanced Engineering Technolo–
gist, The Timken Company
Guillaume Badard: Group Leader Application
Engineering Wind Energy, The Timken Compan