Der Industriestandort Deutschland befindet sich im Wandel. Neue, digitale Technologien ermöglichen es, Betriebs-, Zustands- und Ereignisdaten in stetig steigender Menge zu erfassen, aufzubereiten, zu analysieren und für die industrielle Anwendung nutzbar zu machen. Der Instandhaltung bzw. dem industriellen Service eröffnen sie das große Potential, eine bedarfsgerechte Verfügbarkeit von Maschinen und Anlagen datenbasiert effektiver und effizienter zu erreichen als bisher. Dieser Wandel, ergänzt durch organisatorische sowie kulturelle Anpassungsprozesse zur Nutzung neuer Technologien, kann als Transformation zur Smart Maintenance verstanden werden. Auf Basis von digitalen Daten und Erfahrungswissen wird mittels Smart Maintenance die selbständige Weiterentwicklung der Instandhaltungsorganisation angestrebt, mit dem Ziel, den größtmöglichen Wertbeitrag für das produzierende Unternehmen zu leisten.
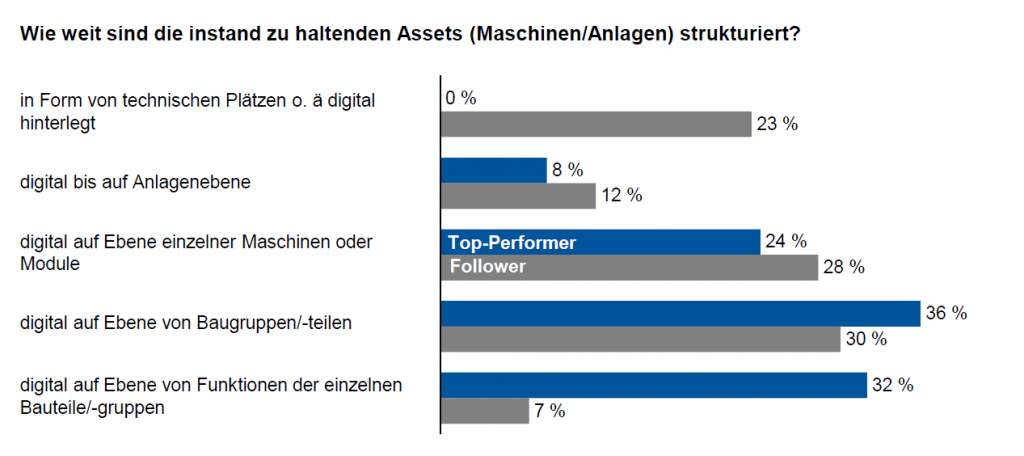
Top-Performer weisen einen höheren Detailgrad ihrer digitalen Anlagenstruktur auf als Follower
© FIR e. V. an der RWTH Aachen
Die Instandhaltung fungiert im Zuge dieser Entwicklung als einer der Haupttreiber für Industrie 4.0, weshalb aktuell viele Unternehmen Bemühungen unternehmen, erste erfolgreiche Schritte auf dem Weg zur Smart Maintenance zu machen. Zwar konnten einige Instandhaltungsorganisationen dahingehend bereits erste oder sogar mehrere Leuchtturmprojekte umsetzen, häufig scheitern sie jedoch an einer Überführung der ausgewählte Usecases in die breite betriebliche Praxis, sodass das vollständige
Potential größtenteils unerschlossen bleibt.
Vor diesem Hintergrund hat das FIR an der RWTH Aachen gemeinsam mit sieben Partnern aus Industrie und Forschung im Jahr 2019 eine umfangreiche Konsortialstudie zum Thema „Smart Maintenance“ durchgeführt. Im Vordergrund stand die Frage: „Was unterscheidet erfolgreiche Unternehmen im Bereich von Smart Maintenance von anderen und wo können Unternehmen auch über die eigenen Grenzen hinweg voneinander lernen?“. Entlang eines eigenen Ordnungsrahmens wurden zentrale Fragestellungen der Smart Maintenance auf den verschiedenen Ebenen der Instandhaltungsorganisation untersucht. Dabei konnten einige vielversprechende Ansätze von erfolgreichen Unternehmen (Top-Performer) identifiziert und mithilfe von Fallstudien zusätzlich übergeordnete Erfolgsprinzipien für die erfolgreiche Transformation der Instandhaltung identifiziert werden.
Smart Maintenance betrifft alle Ebenen der Instandhaltungsorganisation
Die zentralen Fragestellungen der Smart Maintenance haben ihren Ursprung auf dem Shopfloor (operative Ebene), wo Maschinen/Anlagen (technische Assets) und Instandhalter aufeinandertreffen. Für die Anwendung datenbasierter Instandhaltungskonzepte muss hier zunächst eine geeignete Basis geschaffen werden, welche sich aus einer (detaillierten) digital erfassten Anlagenstruktur im IPS-System (Instandhaltungsplanungs- und -steuerungssystem) sowie dem systematischen Erfassen von Betriebs-, Zustands- und Ereignisdaten zusammensetzt. Die Studie und Unternehmensbesuche konnten zeigen, dass Top-Performer der Smart Maintenance viel Aufwand in eine klare, strukturierte Datenerfassung sowie einen hohen Detailgrad ihrer digitalen Anlagenstruktur investieren, da genau in diesen „Hausaufgaben“ die essentielle Basis für den Einsatz mobiler Assistenzsysteme oder komplexer Prognosemodelle liegt. Ohne diese digitale Detailansicht des Assets – mit Blick auf die Historie und das Echtzeitverhalten – verfehlen die neuen Technologien oftmals ihre versprochene Wirkung.
Gleichzeitig müssen die Instandhaltungsmitarbeiter durch angepasste Weiterbildungsangebote im richtigen Umgang mit digitalen Daten und den neuen Technologien geschult werden. Aus der Studie geht hierzu hervor, dass Top-Performer zunehmend Schulungen mit Schwerpunkten zu IT-Kenntnissen/Programmierung und Datenanalyseverfahren durchführen, um so den operativen Betrieb im Zuge der fortschreitenden digitalen Vernetzung zu unterstützen. Hierfür greifen sie vermehrt auf digitale Qualifizierungsmaßnahmen wie E-Learning oder Blended-Learning zurück.
Eine weitere wichtige Komponente auf der Ebene der Arbeitsvorbereitung ist die Datenanalyse. Hier konnte festgestellt werden, dass aktuell nicht die Prognose von Ausfallzeitpunkten/-wahrscheinlichkeiten (‚Predictive Maintenance‘) den größten Nutzen in der Praxis verspricht, sondern vielmehr das Ziehen von Rückschlüssen über optimierte Betriebsparameter für Qualität und Produktivität der Produktion. Während der durchgeführten Unternehmensbesuche wurde dieser Zustand ebenfalls von den Interviewpartnern bestätigt. Es wurde in diesem Zusammenhang angeführt, dass der wirtschaftliche Nutzen von Predictive Maintenance hinter den Potenzialen zurückbleibt, die eine Steigerung der Qualität und Produktivität der Produktion aktuell mit sich bringen. Zusätzlich ist es derzeit fraglich, ob Predictive Maintenance und das damit verbundene Sammeln von notwendigen Störungsdaten (durch teure Maschinen-/Anlagencrashs) in kritischen Produktionsbereichen überhaupt einen Vorteil gegenüber effektiven präventiven Maßnahmen verspricht. Top-Performer rücken so die Bedeutung der Instandhaltung für die Performance der Produktion in den Vordergrund und verstärken das ‚Standing‘ der Instandhaltung als direkten Wertschöpfungspartner.
Top-Performer haben verstanden, dass in einer engen Kooperation mit der Produktion die Möglichkeit für die Hebung vielfältiger Potentiale liegt. Nicht alleine für die Optimierung von Betriebsparametern, sondern auch auf taktischer Ebene, z. B. für die Optimierung der Disposition von Instandhaltungsaktivitäten. Auch hier eröffnet die Nutzung von digitalen Daten die Möglichkeit, Abläufe effizienter zu gestalten und Prozesse zu optimieren. Aus der Studie geht hervor, dass Top-Performer deutlich häufiger eine (unterstützende) Automatisierung ihrer Instandhaltungsdisposition vornehmen als Follower. Hierbei werden Dispositionsvorschläge generiert, die von den Mitarbeitern noch stichprobenartig geprüft und anschließend umgesetzt werden müssen. Eine vollautomatisierte Disposition ohne Kontrollinstanz ist dagegen in vielen Betrieben noch Zukunftsmusik.
Nachdem (digitale) Daten und Information besonders auf operativer Ebene an den Maschinen/Anlagen oder durch den Instandhalter erfasst und für dessen Arbeit aufbereitet werden, müssen Unternehmen langfristig die Verfügbarkeit vor allem von spezifischem Wissen sicherstellen. Auf taktischer Ebene der Instandhaltungsorganisation ist dies eng mit dem Aufbau eines effektiven Wissensmanagements verknüpft. Hierfür wird neben den klassischen Systemen (z. B. digitale Wikis) auch der direkte Erfahrungsaustausch zwischen den Mitarbeitern mittels Social Software (z. B. Slack) aktiv vorangetrieben. Top-Performern gelingt es so bereits häufig, den Erfahrungs- und Wissensverlust, den das Ausscheiden eines erfahrenen Mitarbeiters nach sich zieht, zu kompensieren.
Für die strategische Ausrichtung und die Weiterentwicklung der Instandhaltung zur Smart Maintenance ist es notwendig, den eigenen Wertbeitrag (monetär) beziffern zu können. Top-Performer arbeiten aus diesem Grund verstärkt daran, neben den direkten Instandhaltungskosten (Personal, Material etc.) auch indirekte Instandhaltungskosten (z. B. Ausfallfolgekosten) zu erfassen, um den Wert der Instandhaltung in ihrer eigenen Organisation besser darstellen zu können. Die aktive Einbindung der Geschäftsführung in den Transformationsprozess stellt für erfolgreiche Unternehmen einen weiteren Schlüssel dar, um den Mehrwert von Smart Maintenance (intern) zu betonen. In diesem Sinne muss Smart Maintenance als ganzheitlicher Managementansatz verstanden werden (auch neben den bisher vorherrschenden TPM-Konzepten) und in allen Handlungsfeldern der Instandhaltung vorangetrieben werden.
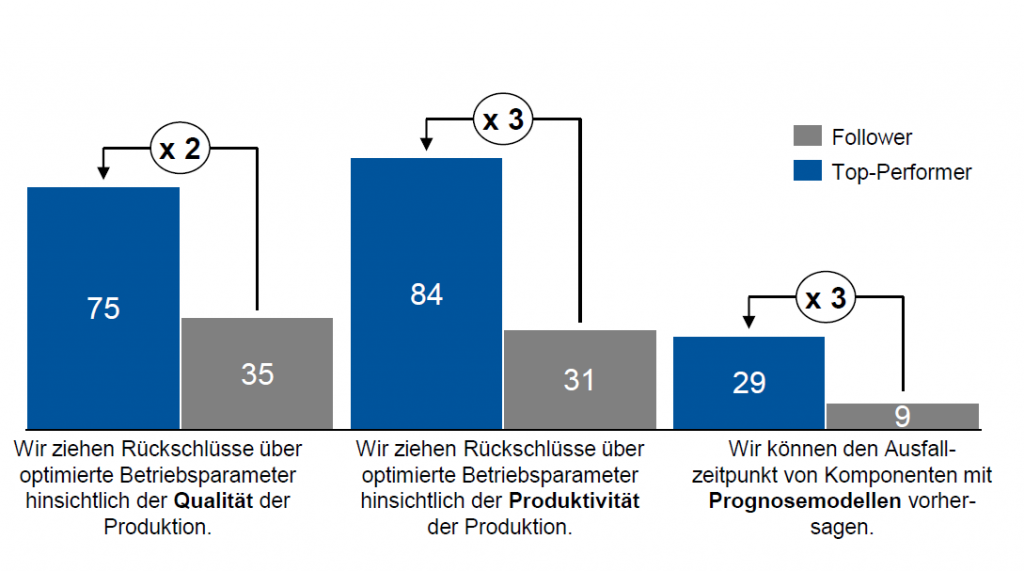
Abbildung 2: Rückschlüsse über Qualität und Produktivität versprechen aktuell den größeren Nutzen als die Vorhersage von Ausfallzeitpunkten (eigene Darstellung) © FIR e. V. an der RWTH Aachen
Eine Smart-Maintenance-Roadmap gibt den Weg für eine erfolgreiche Transformation der Instandhaltung vor
Eine zentrale Erkenntnis der Konsortialstudie „Smart Maintenance“ ist, dass, obwohl die Transformation der Instandhaltung durch technologische Entwicklung ermöglicht wird, ebenso organisatorische und kulturelle Aspekte eine kritische Rolle in der Umsetzung einnehmen. Für die Integration mobiler Instandhaltungsassistenten müssen beispielsweise nicht nur die entsprechenden Geräte erworben, sondern auch die bestehende Prozess- und IT-Landschaft betrachtet und den neuen Anforderungen der Mitarbeiter angepasst werden. Gleiches gilt für die Abkehr von reaktiven Instandhaltungsaktivitäten durch Einsatz von Condition-Monitoring und darauf aufbauenden Analyseverfahren. Im Zuge solcher Änderungen ist es unerlässlich, kulturelle Aspekte im Sinne der Akzeptanz von neuen Arbeitsmethoden nicht zu vernachlässigen.
Die Komplexität, die sich aus dem Zusammenspiel der verschiedenen Gestaltungsfelder ergibt, führt häufig dazu, dass Unternehmen den Überblick über die einzelnen Schritte des Transformationsprozesses verlieren und folglich die Potentiale der Transformation zur Smart Maintenance nicht erschließen können. Unternehmen benötigen daher eine umfassende und langfristig ausgerichtete Smart-Maintenance-Roadmap, die über den gesamten Transformationsprozess hinweg als Orientierungshilfe dient und so ein strukturiertes Vorgehen sowie eine konsequente Umsetzung von aufeinander abgestimmten Maßnahmen bzw. Projekten ermöglicht. Bei der Gestaltung einer solchen Roadmap ist es besonders wichtig, sich an einigen grundlegenden Aspekten zu orientieren. Hierzu zählen neben einem einheitlichen Verständnis in Bezug auf den konkreten Wertbeitrag der Instandhaltung eine interne und reflektierte Positionsbestimmung sowie eine anschließende Auswahl von Projekten. Das FIR an der RWTH Aachen hat die wichtigsten Prinzipien in einem Werkzeug zur Gestaltung und Umsetzung einer Smart-Maintenance-Roadmap zusammengefasst.
Im Rahmen eines gemeinsamen Zielverständnisses muss zunächst festgelegt werden, welche Ziele sich ein Unternehmen im Rahmen der Transformation zur Smart Maintenance setzen möchte. Hierfür ist es wichtig, ein grundsätzliches Verständnis für den Wertbeitrag der Instandhaltung zu schaffen, da sich dieser nicht ausschließlich monetär erfassen lässt. Vielmehr orientiert er sich an drei wesentlichen Zieldimensionen, die damit auch als Ziele der Smart Maintenance dienen:
- Die Instandhaltung ist dafür verantwortlich, Produktivität in der Produktion bereitzustellen, die produzierende Unternehmen erst dazu befähigt, erfolgreich am Markt teilzunehmen. Hierbei spielen insbesondere die Bestandteile der OEE (Leistung, Verfügbarkeit, Qualität) eine übergeordnete Rolle.
- Vor allem in Asset-intensiven Industrien stellt eine Verlängerung der Lebenszyklen von Anlagen ein großes Potential für die Instandhaltung dar, unternehmensinterne Ressourcen effizient zu nutzen und die Wettbewerbsfähigkeit ganzer Standorte zu sichern.
- Besonders vor dem Hintergrund des zunehmenden Fachkräftemangels ist es die Aufgabe der Instandhaltung, Kompetenzen in Form von Informationen und Erfahrungen im Unternehmen zu sichern, aber auch durch neue Lernmethoden oder Mentoring-Programme kontinuierlich bereitzustellen.
Die Weiterentwicklung der Instandhaltung erfolgt schrittweise und entlang von Reifengraden. Auf diese Weise wird sichergestellt, dass jeweils alle benötigten Fähigkeiten für die Erreichung der nächsten Stufe erworben und keine wichtigen Grundlagen übersprungen werden. Der ‚Industrie 4.0 Maturity Index‘ gliedert den Entwicklungsprozess in sechs aufeinander aufbauenden Reifegradstufen (1: Computerisierung; 2: Konnektivität, 3: Sichtbarkeit; 4: Transparenz; 5: Prognosefähigkeit; 6: Adaptierbarkeit) und hilft so bei einer reflektierten Aufnahme der aktuellen Situation. Die Positionsbestimmung für die aktuelle Instandhaltungsorganisation erfolgt dabei innerhalb der vier Gestaltungsfelder:
- Ressourcen
- Organisationsstruktur
- Kultur
- IT-Systeme
Mithilfe unternehmensübergreifender, aber auch interner (Werks- oder Standortvergleiche) Benchmarkings kann die eigene Position innerhalb der Gestaltungsfelder noch präziser bestimmt werden.
In dem nächsten Schritt werden, abhängig von den Zielen der Instandhaltung, entlang der sechs Reifegradstufen und innerhalb der vier Gestaltungsfelder des Maturity-Index konkrete Maßnahmen in einer Roadmap zusammengestellt. Die resultierende Abfolge und berücksichtigten Zusammenhänge der Maßnahmen erlauben so eine schrittweise und aufeinander abgestimmte Weiterentwicklung der Instandhaltungsorganisation.
Da sich der Erfolg einer Roadmap erst durch die Umsetzung der Maßnahmen in der Praxis zeigen kann, ist es enorm wichtig, im Anschluss an die Ausgestaltung der Roadmap die „richtigen“ Projekte auszuwählen, um die in der Regel sehr limitierten Ressourcen effektiv einsetzen zu können. Auf diese Weise können gezielt und schnell erste Fortschritte erzielt und für jeden Beteiligten sichtbar gemacht werden. Interessanterweise stehen hierfür am Anfang nicht unbedingt Technologiethemen an erster Stelle, sondern Projekte, die der Anpassung der Ablauforganisation und Steigerung der Akzeptanz der Mitarbeiter dienen.
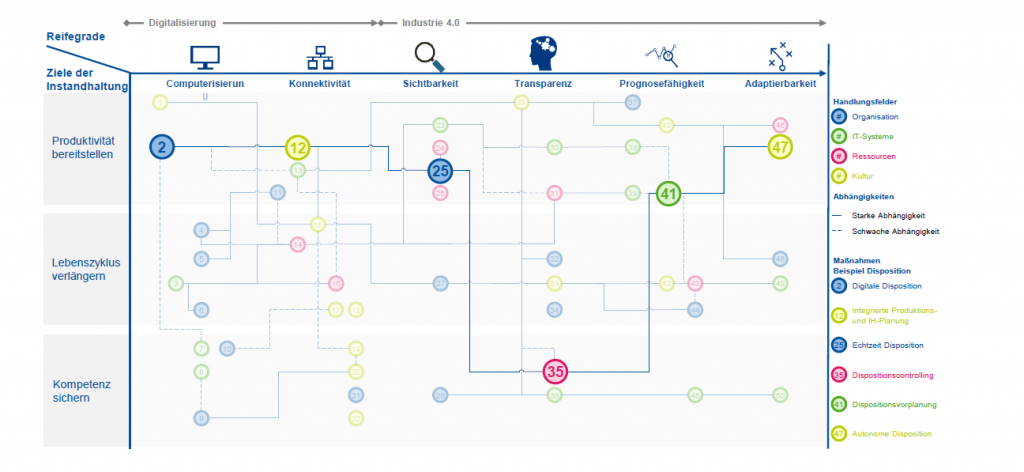
Abbildung 3: Beispiel einer Smart-Maintenance-Roadmap des FIR an der RWTH Aachen (eigene Darstellung)
© FIR e. V. an der RWTH Aachen
Der Weg zur Smart Maintenance ist ein kritischer Erfolgsfaktor für die zukünftige Wettbewerbsfähigkeit
Der Weg zur Smart Maintenance ist gleichbedeutend mit der Entwicklung einer zukunftsfähigen Instandhaltung, in der die Potentiale des technologischen Fortschritts, gepaart mit organisatorischen und kulturellen Anpassungsprozessen, die Instandhaltung mehr denn je zu einem essentiellen Wertschöpfungspartner im Unternehmen machen. Mithilfe einer Smart-Maintenance-Roadmap können die notwendigen Grundlagen sichtbar, die einzelnen Schritte aufgezeigt und Unternehmen so zur erfolgreichen Transformation befähigt werden. Das FIR an der RWTH Aachen unterstützt und begleitet Unternehmen auf diesem Weg mit seiner langjährigen Projektexpertise. Gemeinsam mit den Unternehmen wird die Reife der Instandhaltungsorganisation gemessen, Benchmarks werden betrachtet, individuelle Roadmaps angefertigt und umgesetzt. Smart Maintenance wird somit nach und nach für die Unternehmen greif- und messbar.
Autor*innen
Frederick Birtel
Leiter Competence-Center Instandhaltung
FIR an der RWTH Aachen
Campus-Boulevard 55, 52074 Aachen
E-Mail: Frederick.Birtel@fir.rwth-aachen.de
Tel.: +49 241 47705-204;
Frederik Scholing
Competence-Center Instandhaltung
FIR an der RWTH Aachen
Adresse: Campus-Boulevard 55, 52074 Aachen
E-Mail: Frederik.Scholing@fir.rwth-aachen.de
Tel.: +49 241 47705-204