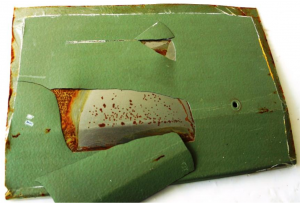
Abb.1: Schäden durch Korrosion und Lackenthaftung lassen sich vermeiden
Die Oberflächenbehandlung ist ein entscheidender Schritt in der Fertigung, da über sie die finalen Eigenschaften des Werkstücks erzeugt werden, sowohl in ästhetischer Sicht, als auch in funktioneller Hinsicht und der Langzeit-Beständigkeit.
In der Fertigung spielt einerseits das komplexe Zusammenspiel zwischen den Materialeigenschaften des flüssigen Lackmaterials und des ausgehärteten Lackfilms und dem Beschichtungsprozess eine große Rolle. Andererseits wechselwirkt der Lack mit dem Grundwerkstoff, sodass bei den Fertigungsprozessen beides berücksichtigt werden muss.
In diesem Beitrag soll dies an ein paar Bespielen, wie dem Zusammenhang der Beschichtung mit der Haftfestigkeit des Lackes, der Ausbildung der Oberflächenstruktur, der Korrosionsbeständigkeit und der zugehörigen Prüfmethodik dargestellt werden.
Prozesseinflüsse auf die Lackhaftfestigkeit in der Kunststofflackierung
Die Haftfestigkeit eines Lackaufbaus wird durch viele Einflüsse bestimmt: Untergrund, Vorbehandlung, Lackaufbau, Prozesseinflüsse. Vor allem letztere werden oft nicht ausreichend berücksichtigt.
So können im Lackierprozess die Zerstäubungsfeinheit und die Trocknungsbedingungen den Gehalt an Wasser und organischen Lösemitteln im Film beeinflussen und somit für die Haftfestigkeit relevant sein. Außerdem beeinflussen diese Parameter auch die Diffusion von Lackkomponenten durch die Schichten und führen damit zu veränderten Eigenschaften in den Grenzschichten.
In systematischen Versuchen am Fraunhofer IPA wurden für verschiedene Lackaufbauten und Substrate die Applikations- und Trocknungsbedingungen verändert und die Auswirkungen auf die Haftfestigkeit untersucht. Wichtig war dabei eine reproduzierbare Versuchsdurchführung mit Robotern, definiertem Kabinenklima und die Dokumentation mittels Ofenschreiber, Luftströmungsmessungen und die Protokollierung von Feuchte und Temperatur.
Verschiedene Versagensmechanismen können dabei auftreten:
- Kohäsionsbruch im Kunststoffsubstrat oder in einer Lackschicht
- Adhäsionsbruch zum Substrat
- Adhäsionsbruch zwischen den Lackschichten
Analytische Messverfahren können zur Untersuchung der Prozesseinflüsse herangezogen werden:
Je nach Wahl der Trocknungsparameter hat die ausgehärtete Basislackschicht ca. 1 % bis 6 % Wassergehalt. Diese Mengen können mit der sensitiven coulometrischen Karl-Fischer-Titration in Kombination mit der Ofentechnik bei 120 °C bis 160 °C gut erfasst werden.
Qualitative GC-MS-Untersuchungen erlauben, eine Aussage darüber, ob und wenn ja welche Lösemittel nach Trocknung noch im ausgehärteten Beschichtungsaufbau verbleiben. Des Weiteren kann nach Kalibrierung einer Auswahl von Lösemitteln mit der MHE-Methode (Multiple Headspace Extraction) der verbleibende Gehalt dieser Lösemittel quantitativ bestimmt werden. Die Infrarotspektroskopie kann zur Kontrolle der Durchhärtung eingesetzt werden, wenn Reaktionsbanden im Spektrum gut abgrenzbar sind.
Für Automobillackierungen ist ferner die Fragestellung interessant, inwieweit der Härter aus dem Klarlack in die Basislackschicht vordringt. Durch Kombination von Mikrotomie-Präparation und Infrarotspektroskopie wurde beispielsweise gezeigt, dass bei dünnerer Basislackschicht die Durchdringung mit Isocyanat aus dem Klarlack bis zur untersten Ebene der Basislackschicht erfolgt, während bei höherer Basislackschichtdicke eine deutliche Abnahme der Isocyanat-Komponente von oben bis unten beobachtet wird, s. Abb. 2.
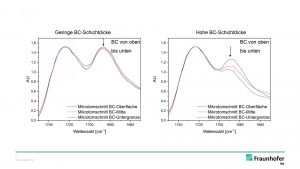
Abb. 2: Infrarotspektren von Basislack-Mikrotomschnitten zur Analyse der Isocyanat-Durchdringung durch den Klarlack-Härter.
Durch die komplexen Wechselwirkungen zwischen Material und Prozess sind mögliche Versagensmechanismen vielseitig, die durch eine Kombination von verfahrenstechnischen Versuchen und chemischer Analytik aufklärbar sind.
Entstehung von Lackfilmstrukturen steuern
Der Lackfilmverlauf zählt zu den wichtigen Kriterien bei der Bewertung der visuellen Beschichtungsqualität. Bei unvollständigem Lackfilmverlauf weist die Lackschichtoberfläche nach der Trocknung und Härtung eine mehr oder weniger starke Welligkeit auf, die als „Orangenhautstruktur“ bezeichnet wird.
Unter den Lackeigenschaften hat das rheologische Verhalten den größten Einfluss auf den Verlauf. Die meisten in der Industrie verwendeten Lacke zeigen ein thixotropes Fließverhalten. Ihre Fließeigenschaften sind scherraten- und zeitabhängig, weshalb sie auch als „Gedächtnisflüssigkeiten“ bezeichnet werden. Eine Beziehung zwischen rheologischer Messung und Verlaufsergebnis zu finden, stellt sich für diese Lacke besonders schwierig dar. Während der Applikation wird die innere Struktur des Lackes durch starke Scherung zerstört – der Lack wird dünnflüssig. Während des Verlaufens kann sich die innere Struktur unter schwacher Scherung erholen, so dass der Lack wieder dickflüssiger wird. Die in der Industrie üblichen rheologischen Messmethoden liefern keine Daten, die für eine Berechnung des Verlaufsverhaltens thixotroper Lacke geeignet sind.
Das Fraunhofer IPA hat ein neuartiges Mess- und Auswerteverfahren entwickelt, mit dem die gleichzeitige Erholung der viskosen und elastischen Eigenschaftsanteile gemessen und für jeden Verlaufszeitpunkt in eine effektive Verlaufsviskosität und eine Verlaufsgeschwindigkeit umgerechnet werden kann. Auf diese Weise kann aus einer Messung mit einem weit verbreiteten standardmäßigen Rotationsrheometer das Verlaufsverhalten vorhergesagt werden.
Es lassen sich damit Unterschiede im Verlaufsverhalten zwischen verschiedenen Rezepturvarianten ohne Lackierversuche vorhersagen. Es lässt sich außerdem ableiten, wie die Fließeigenschaften verändert werden müssen, z. B. mittels rheologisch wirksamer Additive, um die Oberflächenstruktur einer gewünschten Struktur anzunähern.
Das IPA hat nachgewiesen, dass die elastischen Eigenschaften einen signifikanten Einfluss auf die Verlaufsgeschwindigkeit wässriger und lösemittelhaltiger Automobilbasislacke haben. Die effektive Viskosität, d. h. die verlaufsbehindernde Größe, die die viskosen und elastischen Anteile zusammenfasst, kann Werte von mehreren 1000 Pa·s erreichen und liegt damit weit höher als die konventionell gemessene Scherviskosität. Für die Appearance-Optimierung, z. B. verschiedene optische Eigenschaften wie Glanz, Schleier, DOI, Welligkeit… besonders interessant ist, dass sich über den elastischen Eigenschaftsanteil das Verhältnis von kurz- und langwelligen Strukturen steuern lässt (Abb. 3).
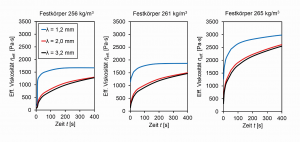
Abb. 3: Aus rheologischen Messdaten berechneter Anstieg der effektiven Viskosität während des Verlaufens eines thixotropen Automobilbasislacks für drei verschiedene Strukturwellenlängen und bei drei verschiedenen Festkörperkonzentrationen (Abdunstungszuständen)
Grundlagen, Oberflächenbehandlung, Beschichtungssysteme und moderne Prüftechnik zum Korrosionsschutz
Dem wirtschaftlich enorm bedeutenden Korrosionsschutz von Metallen mit Beschichtungen liegt das Prinzip der Trennung des Werkstoffes vom angreifenden (korrosiven) Medium zugrunde; dieses Prinzip wird etwa bei 80 % aller vor Korrosion zu schützenden Metalloberflächen angewandt. Eine vielfältige Produktauswahl ermöglicht Beschichtungen, anforderungsgerechten Korrosionsschutz mit individuellen Gestaltungsaspekten hinsichtlich Farbgebung und Oberflächendesigns zu verbinden.
Materialgerechte Vorbehandlung der zu beschichtenden Oberfläche ist Voraussetzung für dauerhaften Korrosionsschutz und Haftfestigkeit. Diese umfasst gründliche Reinigung der Oberflächen von haftschädigenden Produkten, was z. B. durch Strahlen oder nasschemische Entfettung und Folgeschritten erreicht wird. Eine anschließende Konversionsbehandlung, z. B. durch Zinkphosphatier- oder Dünnschichtverfahren, ermöglicht die Ausbildung eines stabilen Haftverbunds mit der Beschichtung und einen effektiven Korrosionsschutz. Im Stahlbau für Langzeit-Korrosionsschutz gebräuchliche Vorbehandlung ist auch die Verzinkung mit anschließender mechanischer oder nasschemischer Vorbehandlung.
Umfassende Normen, wie z. B. die DIN EN ISO 12944 und GSB Richtlinien sowie Spezifikationen der Maschinen- und Fahrzeughersteller beschreiben die wesentlichen Anforderungen zur Realisierung eines gewünschten Korrosionsschutzes, wie angestrebte Schutzdauer, Vorbehandlung, Auswahl und Prüfungen der Beschichtungssysteme.
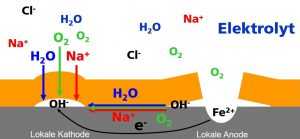
Abb. 4: Ablauf der atmosphärischen Korrosion z. B. unter dem Salzsprühnebeltest (Bild: Fraunhofer IPA)
Beschichtungssysteme bestehen aufgrund unterschiedlicher Funktionen meist aus Mehrschichtaufbauten. Dabei wird der Korrosionsschutz im Wesentlichen durch die Grundbeschichtung (GB) bestimmt. Voraussetzung für guten Korrosionsschutz ist eine gute Nasshaftung des Bindemittelsystems der GB auf der Metalloberfläche, der optimalen Wirkung der Aktivpigmente sowie eine gute Barrierewirkung der Grund- und Zwischenbeschichtung gegenüber dem Eindringen von Wasser, Elektrolyten und Sauerstoff in die Grenzfläche Beschichtung/Metall. Die Deckbeschichtung (DB) schützt den Gesamtaufbau vor Witterungseinflüssen, vor Schadstoffen sowie vor mechanischen Belastungen und hat auch dekorative Aufgaben, wie Farb-/Effekt- und Glanzgebung. Bedeutung im Stahlbau haben auch sog. Duplex-Systeme, bestehend aus metallischen Überzügen auf der Metalloberfläche, z. B. Feuerverzinkung, und einer Beschichtung. Wichtige Grundbeschichtungssysteme bzw. Primer für höchsten Korrosionsschutz sind: Kathodische Tauchlacke (KTL) vorwiegend im Automobil- und Fahrzeugbau sowie bei hochwertigen Land-/Baumaschinen, 2K-Epoxid-Systeme im Bereich Stahlbau und vieler Industriebranchen, EP-Pulverlacksysteme. Für mittlere Anforderungen eignen sich auch Primer auf Basis wasserverdünnbarer Acrylat-Copolymer-Dispersionen, wie auch solche für sog. Direct-to-metal-(DTM)-Einschichtsysteme. Für hochwertige Architektur-Beschichtungen auf Aluminiumsubstraten haben sich Einschicht-Systeme auf Basis von hochwetterfesten Polyester-Pulverlacksystemen bewährt. Zur Prüfung der Leistungsfähigkeit von Korrosionsschutzbeschichtungen sind nach wie vor konventionelle Tests unter Kondenswasser- und Salzsprühnebeleinwirkung unerlässlich. Ergänzt werden diese durch kombinierte, zyklisch ablaufende neuere Korrosionswechseltests, wie z. B. VDA 233-102. Moderne Techniken eignen sich zur schon nach sehr kurzer Prüfdauer möglichen Erkennung von Veränderungen, die zu Korrosion der Beschichtung führen können: Einwirkung von Elektrolyten auf Beschichtungen unter thermozyklischen Bedingungen und Detektion mittels elektrochemischer Impedanzspektroskopie (EIS) und Rasterkelvinsonde (RKS).
Qualitätssicherung von beschichten Bauteilen gemäß DIN EN ISO/IEC 17025:2018
Die Beschichtung von Bauteilen ist essentiell für deren Lebensdauer. Der Qualitätssicherung kommt daher eine besondere Bedeutung zu. Die DIN EN ISO/IEC 17025:2018 ist weltweit die Grundlage der Arbeit in allen Prüflaboratorien, um eine stetig hohe Prüfqualität und somit auch Produktqualität zu gewährleisten. Sie verfolgt dabei das Ziel, die Ergebnisse aus Prüfungen sowie die technische Glaubwürdigkeit und Kompetenz des jeweiligen Labors zu sichern. Im Mittelpunkt der DIN EN ISO/IEC 17025:2018 steht daher immer die Qualität sowie die Verlässlichkeit der Prüfmethoden.
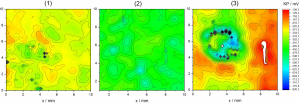
Abb. 5: Kelvin-Potenzial-Verteilungen an Zinkstaub-Grundbeschichtungen: Konv. Zn-Staub-GB (1), Zink-Flake-GB (2) und Zink-Staub/Zink-Flake-GB (Bild: Fraunhofer IPA)
Dazu gehört vor allem ein funktionierendes Qualitätsmanagement, um normgerechte Prüfungen an Beschichtungen durchzuführen zu können. Kompetentes und geschultes Personal ist dabei genauso wichtig wie die Überwachung der verwendeten Prüfmittel und klar definierte Prüfabläufe, sowie die Bewahrung der Neutralität. Für die Metall- und Kunststoffbeschichtungen stehen eine Vielzahl an Prüfmethoden zur Beurteilung der Qualität zur Verfügung. Die Beschichtungen werden dabei z. B. klimatischen und Korrosionsprüfungen sowie physikalisch-technischen Beständigkeitsprüfungen unterzogen oder es werden Kenngrößen von Lackrohstoffen, Beschichtungen und Beschichtungsstoffen ermittelt. Beispielhaft seien hier Beständigkeitsprüfungen gegen Feuchtigkeit, Temperatur, gegen zyklische Belastungen oder gegen Salzsprühnebel genannt. Für die Prüfungen der Haftfestigkeit der Beschichtung auf den unterschiedlichsten Substraten werden Verfahren, wie z. B. Gitterschnitt, Klebebandabriss, Abrieb-, Dampfstrahl- oder Multisteinschlagprüfungen angewendet. Negativen Einfluss auf die Beschichtungsqualität können letztendlich auch lackbenetzungsstörende Substanzen (LABS) haben, welche zu massiven Beschichtungsfehlern, wie Krater, Anquellungen oder Farbveränderungen führen können. Der sichere Einsatz von neuen Betriebsmitteln in Lackierbetrieben ohne mögliche Störungen der Beschichtungsqualität sollte daher zuvor durch ein akkreditiertes Labor nachgewiesen werden.
Auch in der Schadensanalyse kommt der Akkreditierung nach DIN EN ISO/IEC 17025:2018 daher eine entscheidende Rolle zu. Hier kommen dann meist Verfahren der analytischen Chemie und Polymeranalytik zu Einsatz.
Die Akkreditierung nach DIN EN ISO/IEC 17025:2018 ist für ein Labor keine Pflicht, sie dient aber oftmals als Voraussetzung für die Anerkennung der Prüfergebnisse und zeigt die Unparteilichkeit und Rückverfolgbarkeit der Ergebnisse.
Autoren*innen
Dr. Oliver Tiedje,
Dr. Ulrich Christ,
Dr. Volker Wegmann
Fraunhofer-Institut für Produktionstechnik und Automatisierung IPA
Kontakt
Dr. Oliver Tiedje
Gruppenleiter Nassapplikations- und Simulationstechnik
Fraunhofer-Institut für Produktionstechnik und Automatisierung IPA, Abteilung Beschichtungssystem- und Lackiertechnik
Nobelstraße 12, 70569 Stuttgart
Telefon +49 711 970-1773