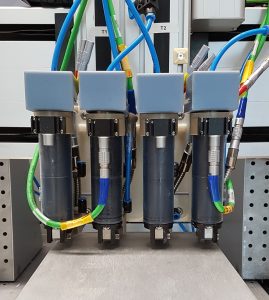
3D-Drucker mit vier Mikordispenser-Einheiten
zum Verdrucken von verschiedenenthermoplastischen Massen.
Anspruchsvolle keramische Komponenten wurden bislang hauptsächlich unter preisintensivem Werkzeugeinsatz spritzgegossen oder mit hohen Materialverlusten aus isostatisch gepressten Formkörpern gefertigt. Neue additive Fertigungstechnologien wie das Fused-Filament-Fabrication-Verfahren oder der Thermoplastische 3D-Druck eröffnen nun völlig neue Wege für die Keramik: Mit komplex geformten, großformatigen oder funktional gradierten Bauteilen kann ihr Einsatzspektrum in den verschiedensten Zielbranchen erheblich gesteigert werden.
Generell gestatten additive Verfahren Bauteilgeometrien herzustellen, die mit herkömmlichen Formgebungsverfahren nicht realisierbar sind. Zudem können auch individualisierte Einzelstücke oder Kleinstserien kosteneffizient gefertigt werden, da die Additive Fertigung ohne kostspielige verschleißende Werkzeuge auskommt. Neben der geometrischen Vielfalt bieten additive Verfahren aber auch die Möglichkeit, Bauteile mit ortsaufgelöstem Eigenschaftsprofil herzustellen, indem die Werkstoffzusammensetzung an jedem beliebigen Punkt des Bauteils variiert wird. Damit werden künftig neue, geometrisch und funktional komplexe Keramikkomponenten verfügbar sein.
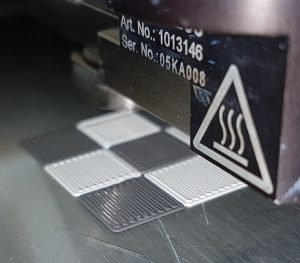
Herstellung einer Schachbrettstruktur mittels T3DP.
Thermoplastischer 3D-Druck (T3DP)
Mit dem Thermoplastischen 3D-Druck wird am Fraunhofer IKTS ein neuartiger Ansatz verfolgt, mit dem sich zum einen komplex geformte, dichte Bauteile, z. B. aus Aluminiumoxid, Zirkonoxid oder Hartmetall, und zum anderen mehrkomponentige und/oder gradierte Bauteile wie Stahl-Keramik-Verbundbauteile fertigen lassen. Das Verfahren beruht auf einer unikalen Technologie- und Anlagenentwicklung, mit deren Hilfe entscheidende Grenzen bestehender Verfahren überwunden werden können. Bei diesem additiven Verfahren werden partikelgefüllte thermoplastische Massen mit einer niedrigen Schmelztemperatur (80 – 100 °C) aufgeschmolzen, wobei die Viskosität der keramischen Ausgangsmassen relativ gering ist. Das Material wird dabei nicht vollflächig aufgetragen, sondern nur an den benötigten Stellen. Die beheizbare Dosiereinheit, die in allen drei Raumrichtungen angesteuert wird, bewegt sich über eine feststehende Plattform. Die thermoplastische Masse wird durch Wärmezufuhr in einen fließfähigen Zustand überführt, an der gewünschten Stelle abgeschieden und erstarrt sofort bei Abkühlung. Dadurch erfolgt die Verfestigung der Masse nahezu unabhängig von den physikalischen Eigenschaften der verwendeten Pulver.
Die für diese Methode angepassten thermoplastischen Aluminiumoxidmassen (Al2O3) haben einen Pulveranteil von bis zu 67 Vol.-% (d50 = 1,5 μm), bei den Zirkonoxidmassen (ZrO2) liegt der Pulveranteil bei bis zu 45 Vol.-% (d50 = 0,3 μm). In aktuellen Arbeiten wird derzeit der Einfluss der Tröpfchenform, -höhe und -weite sowie des Abstands der Tröpfchen untereinander und der Prozessparameter im Hinblick auf die reproduzierbare Herstellung von Bauteilen und zuverlässige Prozessführung untersucht.
Da sich auch mehrere Vorratsbehälter und Dispenseinheiten gleichzeitig verwenden lassen, eignet sich der Thermoplastische 3D-Druck hervorragend für die Abscheidung von unterschiedlichen Materialien in einem Bauteil. Die Anpassung des Schwindungsverhaltens der verschiedenen Komponenten erfolgt dabei durch die Einstellung des Pulvervolumenanteils in der Masse sowie durch Anpassung der Partikelgrößenverteilungen und gegebenenfalls Modifizierung der Partikelform. Für einen Zirkonoxid/Stahl-Verbund sind erste Proben hergestellt worden. Damit erweitert das Verfahren die technologischen Grenzen der Additiven Fertigung in der Keramik.
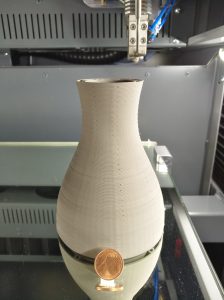
SiC/SiC-faserverstärkter Grünkörper hergestellt durch Fused-Filament-Fabrication
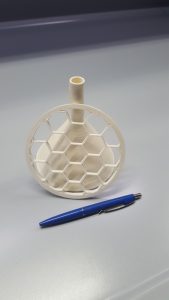
Über FFF gefertigte Al2O3-Trichterstruktur mit geschwungenem Auslass und dazugehöriger
mitschwindender Sinterunterlag
Fused-Filament-Fabrication (FFF)
Unter den bereits kommerziell genutzten Verfahren der Additiven Fertigung ist das Fused-Filament-Fabrication das am weitesten verbreitete Verfahren. Dies gilt jedoch bisher nur für die Herstellung polymerer Bauteile. Daher arbeitet das Fraunhofer IKTS an der Adaptierung dieses Verfahrens für die Additive Fertigung keramischer Bauteile. Mit Hilfe des Fused-Filament-Fabrication ist es möglich, große und komplexe Bauteile mit hoher Materialeffizienz mit relativ geringem Zeitaufwand herzustellen. Dabei wird ein thermoplastisches Endlosfilament in einer beheizten Düse aufgeschmolzen und darunter abgelegt. Der Druckkopf wird computergesteuert bewegt, um die gewünschte Form Schicht für Schicht aufzubauen.
Im Rahmen erster Arbeiten konnten Filamente auf Basis eines Feedstocks aus Siliciumcarbidpulvern (SiC) erfolgreich hergestellt und mit einem Standarddrucker verdruckt werden. Zur Verstärkung des Materials wurden in einem nächsten Entwicklungsschritt SiC-Werkstoffe mit bis zu 30 Vol.-% SiC-Faseranteil verarbeitet. Durch eine anschließende Infiltration mit keramischen Precursoren und deren Pyrolyse wurden die Bauteile weiter verdichtet. Auf Basis dieser Untersuchungen konnte das große Potenzial dieser neuen additiven Formgebungsmethode für keramische Faserverbundwerkstoffe (CMC) für unterschiedliche Anwendungen, z. B. für die Luft- und Raumfahrt oder die Energietechnik, aufgezeigt werden.
Darüber hinaus wurden beispielsweise Bauteile auf Basis von Aluminiumoxid, Wolframcarbid-Cobalt und Siliziumnitrid gefertigt, die nach der abschließenden Sinterung eine relative Dichte von jeweils > 99 % der theoretischen Dichte erreichten. Besonders interessant ist zudem die simultane Verarbeitung mehrerer Materialien, um künftig Eigenschaften wie elektrisch leitend und isolierend, hart und duktil oder verschiedene Farben innerhalb eines komplexen Bauteils zu kombinieren. Auf diese Weise können Bauteile funktionalisiert werden und eröffnen völlig neue Möglichkeiten zur Erschließung neuer Anwendungsfelder. Weiterhin erlaubt das Verfahren die kostengünstige Herstellung von mitschwindenden Sinterunterlagen für große keramische Bauteile. Derartige Strukturen können die verzugsarme Sinterung gerade bei fehlender Standfläche erheblich vereinfachen bzw. die Reibung zwischen Bauteil und Sinterunterlage deutlich reduzieren.
Kontakt
Fraunhofer-Institut für Keramische
Technologien und Systeme IKTS
Dr. Tassilo Moritz
Telefon +49 351 2553-7747
tassilo.moritz@ikts.fraunhofer.de
www.ikts.fraunhofer.de