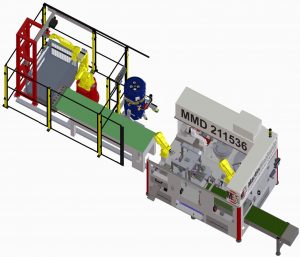
Die Montage von Gleitlagern für die Metallindustrie übernimmt die neue
Anlage MMD 211536 von MartinMechanic vollautomatisch.
Bild: MartinMechanic
Ausgeklügeltes Kamerasystem überwacht Produktion / Neue Anlage von MartinMechanic in Metallindustrie im Einsatz
Vier Roboter und ein ausgeklügeltes Kamerasystemsorgen für die reibungslose Montage von Gleitlagern im Maschinen- und Werkzeugbau. Der eigentliche Arbeitsvorgang dauert gerade einmal sechs Sekunden. Martin Mechanic hat die Anlage MMD 211536für die Metallindustrie entwickelt. Sie könnte allerdings auch bei fast jeder anderen Branche zum Einsatz kommen.
Die Gehäuse für das Gleitlager werden in Gitterboxen zu je 1.500 Stück angeliefert. Der Werker schiebt eine voll beladene Zuliefererpalette in die Anlage. Von da an funktioniert alles vollautomatisch. Ein 3D Area Sensor, der oberhalb der Gitterbox angebracht ist, erkennt die Lage der Teile, die mit der offenen Seite nach unten in den Gitterboxen liegen. Der Sechs-Achs-Roboter vom Typ Fanuc M20iA kann sie deshalb im sogenannten Bin-Picking-Verfahren zielgerichtet aus der Box entnehmen. Ein im Roboter integriertes Kamerasystem stellt außerdem sicher, dass
jeweils nur ein Teil exakt aus der Box entnommen wird und vor allem – je nach Modellart – die richtigen Bauteile montiert werden. Denn es werden zwei unterschiedliche Gleitlager-Varianten auf derselben Anlage gefertigt. Entsprechen die Gleitlagergehäuse den Vorgaben, legt der Roboter sie einzeln auf dem Pufferband ab. Das befördert die Teile direkt in die Anlage, wo ein Roboter vom Typ Fanuc LR-Mate 200iD sie aufgreift und in die
Ausrichtstation legt. Dieser Industrieroboter ist nicht größer als ein menschlicher Arm und für das schnelle Handling von Teilen bis zu sieben Kilogramm Gewicht geschaffen. Kameras vermessen dabei das Gehäuse, das einen Durchmesser von 60 Millimeter und eine Höhe von 100 Millimeter haben sollte. Ist das Gehäuse exakt ausgerichtet, greift der Roboterarm
erneut zu und befördert es in die erste Station des benachbarten Rundtakttisches. Dort durchläuft das Gehäuse vier Stationen, bis es voll bestückt und geprüft ist. Dafür taktet der Rundtakttisch um jeweils 90 Grad weiter.
Als erstes hat ein Scara-Roboter vom Typ Omron-Yamaha mit seinem Doppelgreifer an Station zwei eine Buchse und einen Sicherungsring von der Materialzuführung aufgenommen und über einen Montagedorn gestülpt. Der drückt das Zubehör von unten kraftüberwacht in das Gehäuse ein. Anschließend fährt der Dorn wieder zurück, und der Rundtakttisch dreht zur dritten Station.
Auf einem Pendeltisch, der sich permanent um 180 Grad dreht, werden im steten Wechsel jeweils zwei Lagerschalen und zwei Spannfedern auf einem Dorn vormontiert. Dafür kommt der zweite Fanuc LR Mate 200 iD zum
Einsatz. Er ist mit einem Vierfach-Greifer ausgestattet und arbeitet mit einer Genauigkeit von zwei Hundertstel Millimeter. Dazu bedient er sich zum einen aus den Magazinen, in denen die Lagerschalen horizontal liegen. Sie werden über ein Taktband bereitgestellt, während die Spannfedern über einen Fördertopf vereinzelt dort ankommen, wo der Roboter sie aufgreifen kann. Auch für dieses Zusammenfügen wird das Gehäuse über den Montagedorn an der dritten Station geschoben. Ein Fügemodul überwacht die richtige Einpresshöhe.
Hat sich der Montagedorn abgesenkt, geht es zur vierten Station und damit zur Bauteile-Endprüfung. Hier wird das montierte Gleitlager sowohl auf seine Vollständigkeit geprüft als auch auf seine Höhe und Parallelität vermessen.
Mit seinem Doppelgreifer holt der erste Fanuc-Roboter nun das fertige Teil vom Rundschalttisch ab und legt es auf das Austrageband. Die Teile, die nicht in Ordnung sind, wandern in den Ausgabeschacht und fallen in eine Kunststoffbox, die manuell entleert wird. Anschließend greift sich der Roboter ein neues Gehäuse und die Montage startet von neuem. Das alles in gerade einmal sechs Sekunden.
Die sieben Meter lange und drei Meter breite Anlage von MartinMechanic wurde mit einer SPS-Steuerung ausgestattet. Sie wird über ein mobiles Touchpaneel bedient. Entwicklung, Konstruktion und Bauzeit der MMD 211536 betrugen gerade einmal acht Monate.
Weitere Informationen: www.MartinMechanic.com