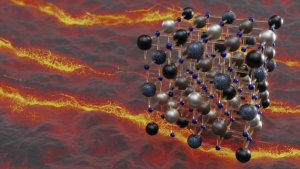
Künstlerischer Blick auf das Kristallgitter einer Hochentropie-Keramik, die so hitzebeständig und elektronisch belastbar ist, dass sie Geräten den Betrieb bei lavaähnlichen Temperaturen ermöglichen könnte. ( © B. Schröder/HZDR)
Ein internationales Forschungsteam hat ein Verfahren entwickelt, um neuartige Materialien zu berechnen, die bei extrem hohen Temperaturen von mehreren tausend Grad Celsius funktionieren. Diese leistungsfähigen Keramiken könnten eines Tages die Grundlage für robustere Beschichtungen, Batterien und strahlungsbeständige Geräte bilden.
Elektronische Geräte, die lavaähnlichen Temperaturen von mehr als 1.000 Grad Celsius standhalten? Eine neue Klasse von Hochleistungsmaterialien könnte das bald möglich machen. Ein Forschungsteam unter der Leitung von Materialwissenschaftler:innen der Duke University (USA) hat eine Berechnungsmethode vorgestellt, mit der sich schnell Vertreter einer neuen Klasse von Materialien entwickeln lassen, die so hitzebeständig und elektronisch stabil sind, dass sie Geräte in die Lage versetzen könnten, bei extremer Hitze zu funktionieren. Bei diesen Materialien handelt es sich um Keramiken aus sogenannten Überangsmetallcarbonitriden oder -boriden. Dieser spezielle Typ von Verbindungen bildet stark ungeordnete Strukturen, sogenannte Hochentropiephasen. Durch die zufällige Verteilung der Kationen im Material kommt es dabei in hohem Maße zu Reflexionen und Interferenzen von Wellen, woraus sich besondere mechanische, elektronische und thermische Eigenschaften ergeben. Weiterlesen