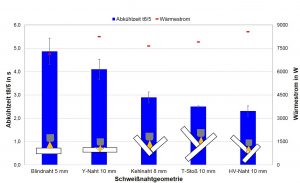
Abbildung 1: Einfluss der Schweißnahtgeometrie auf die Abkühlzeit t8/5 und den Wärmestrom beim MSG-Schweißen (Parameter: Standardlichtbogen bei v D = 10 m/min; PA-Schweißposition; Zusatzwerkstoff d = 1,2 mm G3Si1; Grundwerkstoff: S235; Schutzgas 15 l/min 82 % Ar, 18 % CO2; Schweißgeschwindigkeit 70 cm/min; Kontaktrohrabstand 18 mm)
Einleitung
Um die Wirtschaftlichkeit beim Schmelzschweißen zu erhöhen können Fülldrahtelektroden eingesetzt werden, welche aber gleichzeitig eine höhere Emission an gesundheitsschädlichen Stoffen beim Schweißen bewirken. Das Schmelzschweißen, als eine Möglichkeit Stahlbauteile zu fügen, spielt nach wie vor eine bedeutende Rolle in heutigen Konstruktionen. Fortlaufend wird an neuen Stahlsorten geforscht und vorhandene in ihren Eigenschaften weiter entwickelt. Das große Ziel ist, Stähle schnell und einfach zu fügen um damit wirtschaftlich Produkte herstellen zu können. Das Schmelzschweißen führt im Werkstoff grundsätzlich und unweigerlich zu einer Änderung des Gefüges. Dies hat wiederum großen Einfluss auf die mechanischen Eigenschaften der Schweißverbindung. Für die Charakterisierung des Zeit-Temperatur-Verlaufs kommt dem Bereich zwischen 800 und 500 °C (sogenannte t8/5-Zeit) hohe Bedeutung zu, da dort die Gefahr unzulässiger Aufhärtung bzw. die Verminderung der Streckgrenze besteht. Für ein wirtschaftliches Schweißen müssen diese Kenntnisse vorliegen. Weiterhin besteht für das Personal, welches Schweißarbeiten durchführt, aber auch für Personen die sich in unmittelbarer Nähe des Bereiches der Schweißarbeitsplätze befinden, eine erhebliche Gefahr durch Strahlung und durch die Entstehung von alveolengängigen Schweißrauch. Die Professur Schweißtechnik der Technischen Universität Chemnitz ist mit mehreren Forschungsprojekten in diesen Bereichen aktiv. Einen repräsentativen Einblick aus diesen Projekten bietet der vorliegende Artikel. Weiterführende Informationen sind unter https://www.tu-chemnitz.de/mb/SchweiTech/ zu finden.
Wirtschaftliches Schweißen
Für die schweißtechnische Verarbeitung von modernen Stahlwerkstoffen, zum Beispiel Hochfesten Feinkornbaustählen, werden von den Werkstoffherstellern für Schweißarbeiten enge Toleranzfenster vorgegeben, damit die mechanisch-technologischen Eigenschaften den hohen Anforderungen entsprechen. Um sichere Schweißverbindungen zu erzeugen, muss einerseits der Prozess gleichmäßige und reproduzierbare Ergebnisse liefern und andererseits müssen die Eigenschaftsänderungen bestmöglich bekannt und nachbildbar sein. Dies erfolgt zum einen durch die Abschätzung von Abkühlzeiten [DIN1011-1, SEW088] und Erfahrungswerten sowie zum anderen durch simulationsgestützte Nachbildung des Prozesses. Beide Wege erfordern ein hohes Prozessverständnis, welches an der Professur Schweißtechnik der Technischen Universität Chemnitz aufgebaut und systematisch weiterentwickelt wird.
Die Ergebnisse durchgeführter Forschungsprojekte zeigen, dass der Energieeintrag in das Bauteil von einer Vielzahl an Parametern abhängt und mit den Angaben der gültigen Regelwerke nur unzureichend bestimmt werden kann. Abhängig von den eingestellten Parametern des Schweißprozesses können Abweichungen des Wirkungsgrades (η), welcher allgemein das Verhältnis der nutzbaren zur eingesetzten Energie angibt [HÄL14], von bis zu 20 % entstehen. Hinzu kommt, dass die Verfahren mit nicht abschmelzender Elektrode (zum Beispiel Wolfram-Inertgas-Schweißen oder Plasmaschweißen) durchschnittlich um 25 % höhere Wirkungsgrade und damit verbunden höhere reale Energieeinträge in das Bauteil haben, als die gültigen Regelwerke [DIN1011-1, SEW088] angeben. Schweißverfahren mit abschmelzender Elektrode (zum Beispiel Elektrodenhandschweißen, Metall-Inertgas-Schweißen oder Metall-Aktivgas-Schweißen) sollten in Abhängigkeit von der Lichtbogenart (Kurzlichtbogen η = 0,85, Sprühlichtbogen η = 0,70, Impulslichtbogen η = 0,75) unterteilt werden. Der statische Wert von η = 0,80 [DIN1011-1, SEW088] sollte folglich in den Regelwerken angepasst werden.
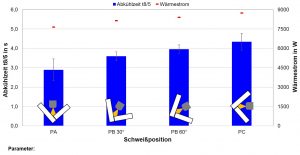
Abbildung 2: Einfluss der Schweißposition auf die Abkühlzeit t8/5 und den Wärmestrom beim MSG-Schweißen (Parameter: Standardlichtbogen bei vD = 10 m/min; Kehlnaht; Zusatzwerkstoff d = 1,2 mm G3Si1; Grundwerkstoff: S235 t = 8 mm; Schutzgas 15 l/min 82% Ar, 18 % CO2; Schweißgeschwindigkeit 70 cm/min; Kontaktrohrabstand 18 mm)
Ebenso hat die Schweißnahtgeometrie einen gravierenden Einfluss auf die Energieeinbringung in das Bauteil. Da der Wirkungsgrad des Schweißprozesses den Quotienten aus eingebrachter Energie in das Bauteil und der Schweißenergie der Schweißstromquelle entspricht, bewirkt eine erhöhte Energieeinbringung in das Bauteil einen größeren Wirkungsgrad. So steigt beispielsweise beim Metall-Schutzgas-Schweißen (MSG-Schweißen) der Wirkungsgrad von η = 0,70 auf η = 0,85, wenn anstatt einer Blindnahtgeometrie eine HV-Naht verschweißt wird. Da während der gesamten Untersuchungen die Schweißparameter und somit auch die Schweißleistung konstant gehalten wurden, kann der Anstieg des relativen Anteils der in das Bauteil eingebrachten Wärme um mehr als 20 % rein auf den Wechsel der Schweißnahtgeometrie zurückgeführt werden (Abbildung 1). Trotz steigender Energieeinbringung in das Bauteil sinkt hingegen die Abkühlzeit der Schweißnaht von 800 auf 500 °C (t8/5-Wert). Während bei einer Blindnahtschweißung ein t8/5-Wert von 4,9 s gemessen wurde, betrug dieser für eine HV-Naht nur 2,3 s. Die Folge dessen ist, dass die Gefahr der Martensitbildung und somit einer Versprödung steigt. Eine qualitätsgerechte Schweißung ist im betrachteten Fall nicht mehr zwingend möglich. Ursache hierfür ist der veränderte Wärmetransport von der Fügezone in das Bauteil. Am Beispiel der HV-Naht erfolgt einerseits der Energiefluss in Blech Längsrichtung und anderseits durch die Nahtvorbereitung gleichzeitig auch gleichmäßig in Materialdickenrichtung. In Folge dessen fließt die eingebrachte Energie schneller aus dem Schweißbereich heraus und der t8/5-Wert sinkt.
Zusätzlich ist der Einfluss der Schweißposition zu berücksichtigen (Abbildung 2). Am Beispiel des MSG-Schweißens wurde deutlich, dass mit gleichen Einstellparametern etwa 12 % mehr Energie in das Bauteil übertragen wird, wenn anstatt in PA- in PB-Position gearbeitet wird. Gleichzeitig stieg die Abkühlzeit (t8/5-Wert) um mehr als 50 % an. Infolgedessen wird empfohlen, einen zusätzlichen Positionsfaktor bei der Berechnung des t8/5-Wertes in die Regelwerke [DIN1011-2] aufzunehmen.
Weiterführend ergab die Analyse eines mehrlagigen Nahtaufbaus in einer vorgegebenen V-Nahtgeometrie, dass mit zunehmendem Lagenaufbau der Wirkungsgrad und somit der Anteil der Schweißleistung, welcher am Bauteil real in Wärme umgesetzt wird, sinkt. Grund hierfür ist, dass der Lichtbogen mit steigendem Lagenaufbau zunehmend weniger „gekapselt“ ist und folglich die zusätzliche Bauteilerwärmung über die Nahtflanken reduziert wird.
Zusammenfassend wurde deutlich, dass es unter den gegebenen Voraussetzungen mit aktuellen Regelwerken schwer möglich ist, richtige Annahmen und Ergebnisse zum Wirkungsgrad und zum Wärmeeintrag zu erzielen. Bei der ungünstigsten Kombination der Fehlermöglichkeiten bei der Schweißleistungsbestimmung können die theoretischen Betrachtungen leicht um bis zu 100 % von der Realität abweichen. Insofern keine Anpassungen der Regelwerke und der beschriebenen Berechnungsmethoden durchgeführt sind, bleibt dem Anwender nur die Möglichkeit die Abkühlzeit mit Thermoelementen real zu messen, um beispielsweise temperatursensible Werkstoffe sicher zu verarbeiten.
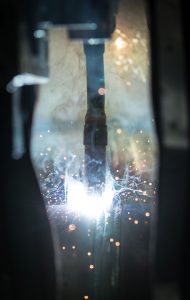
Abbildung 3: Schweißrauchemission beim MSG Schweißen [SREMSG]
Schweißrauchemission
Die Sicherstellung des Schutzes von schweißtechnischem Personal vor entstehenden Schadstoffemissionen bekommt zunehmend eine größere Bedeutung. Durch steigende Anforderungen an den Arbeitsschutz sind Unternehmen häufig gezwungen in kostenintensive Schutzmaßnahmen zu investieren. Sowohl für die persönliche Schutzausrüstung als auch für Arbeitsplatzabsaugungen sind enorme finanzielle Mittel erforderlich. Verschärft wird dies zunehmend durch eine vom Gesetzgeber weitere Absenkung des Staubgrenzwertes für lungengängige Partikel (A-Fraktion) von 3 mg/m³ auf 1,25 mg/m³ basierend auf einer mittleren Dichte von 2,5 g/cm³. Schweißrauchpartikel sind zu 90 % kleiner als 10 µm und werden somit der A-Fraktion zugeordnet. Hierbei stehen Unternehmen vor neuen Herausforderungen. Den gestiegenen Anforderungen an den Arbeitsschutz wird häufig durch unkoordinierte, aufwändige und sehr kostenintensive Investitionen in die persönliche Schutzausrüstung bzw. Arbeitsplatzabsaugungen begegnet.
Durch die exakte Kenntnis des Emissionsverhaltens des verwendeten Schweißprozesses und der verwendeten Schweißzusatzwerkstoffe können die notwendigen Schutzmaßnahmen gezielt an die tatsächlichen Erfordernisse angepasst werden. Dies reduziert die Kosten bei gleichzeitiger Erhöhung des Arbeitsschutzes für das Schweißpersonal.
Die Beurteilung des Gefährdungspotenzials des jeweiligen Prozesses erfolgt nach der Technischen Regel für Gefahrstoffe 528 (TRGS 528) zum einen anhand der chemischen Zusammensetzung des emittierten Rauches und zum anderen anhand der Schweißrauchemissionsrate (FumeEmissionRate = FER). Diese definiert sich nach Formel 1. Wobei ΔmFilter der Masseunterschied des Filters vor und nach der Schweißung und tSchweiß die Schweißzeit sind.
Zum Thema Schweißrauchemissionen und deren Verringerung wird an der Technischen Universität Chemnitz an der Professur Schweißtechnik seit mehreren Jahren geforscht. Dazu wurde für die Ermittlung der Schweißrauchemissionsrate von verschiedenen Schweißverfahren ein standardisierter und teilautomatisierter Versuchsstand entwickelt und aufgebaut. Der in Abbildung 4 dargestellte Versuchsstand ist in Anlehnung an die Gestaltungsempfehlungen aus der DIN EN ISO 15011-1:2010 entwickelt worden [DIN15011].
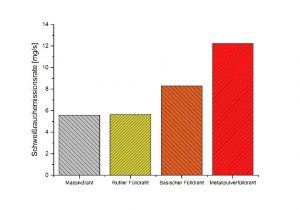
Abbildung 5: Mittlere Schweißrauchemissionsrate in Abhängigkeit vom Füllungstyp bei niedriglegierten Fülldrähten (Parameter: Sprühlichtbogen; vD = 9 m/min; vs = 80 cm/min; M21 mit 18 l/min, d = 1,2 mm)
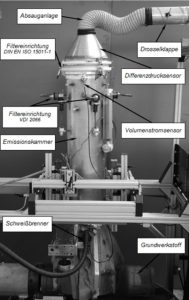
Abbildung 4: Standardisierter und teilautomatisierter Versuchsstand zur Schweißrauchemissionsratenbestimmung
Die Bestimmung der Menge an gesundheitsschädlichen Stoffen erfolgt ebenfalls mit Hilfe der standardisierten Einrichtung. Hierfür wird eine definierte Menge an Schweißrauch gesammelt und anschließend im zertifizierten Labor auf chemische Bestandteile analysiert.
Die Kombination aus standardisierter Ermittlung von Schweißrauchemissionsraten und Bestimmung der chemischen Zusammensetzung des Rauches führt zu einer umfassenden Bewertung des Gefährdungspotenzials. Beispielhaft sind nachfolgend die Emissionsraten für das Metall-Aktivgas-Schweißen (MAG) mit verschiedenen Fülldrahtelektroden in Abhängigkeit vom verwendeten Füllungstyp dargestellt.
Es wurde deutlich, dass zwischen den einzelnen Elektrodentypen signifikante Unterschiede im Emissionsverhalten bestehen und niedriglegierte Metallpulverelektroden bis zu dreimal mehr Schweißrauch emittieren als Massivdraht oder rutile Fülldrahtelektroden, siehe Abbildung 3 [HOE15]. Nach der Technischen Regel für Gefahrstoffe 528 [TRGS 528] erfolgt jedoch keinerlei Differenzierung in der Beurteilung. Hier wird das MAG-Schweißen mit gasgeschützten Fülldrähten lediglich mit einem sehr hohen Gefährdungspotenzial und mit Emissionsraten zwischen 6 … 25 mg/s charakterisiert [TRGS528]. Diese Bewertung führt im Unternehmen zu einem wesentlich höheren Absaugaufwand und auch zu einer erhöhten physischen Belastung des Schweißpersonals durch aufwändige, schwere und zum Teil unkomfortable Schutzausrüstung. Dies kann durch die gezielte Bewertung des Gefährdungspotenzials umgangen und so Kosten gespart werden ohne, dass sich der Schutz des Schweißers verschlechtert. Dieses Beispiel zeigt, dass eine benutzerspezifische Gefährdungsbeurteilung von Prozess und Zusatzwerkstoff für einen effizienten und sehr guten Gesundheitsschutz unumgänglich ist.
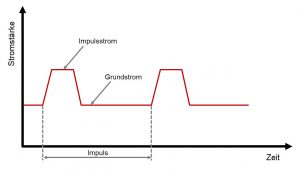
Abbildung 6
Sowohl mit einer genauen Kenntnis über das Emissionsverhaltens des verwendeten Schweißprozesses als auch über eine spezifische Anpassung des Schweißprozesses kann den gestiegenen Anforderungen an den Gesundheitsschutz von schweißtechnischem Personal begegnet werden. Ein innovativer Ansatz zur Reduzierung der Emissionsrate beim Fülldrahtschweißen ist der Einsatz der Impulstechnologie. Beim Impulsschweißen kommt ein pulsierender Gleichstrom mit einstellbarer Frequenz zur Anwendung. Der untere Pegel wird als Grundstrom bezeichnet, der obere als Impulsstrom (Abbildung 6). Durch die Stromimpulse erreicht man einen im Rhythmus der Pulsfrequenz gesteuerten Tropfenübergang [MAT02].
Das Metall-Schutzgas-Schweißen als ein Verfahren des Lichtbogenschweißens wurde bereits in der ersten Hälfte des 20-ten Jahrhunderts angewendet. Gegenwärtig erfreut sich bei diesem Verfahren neben der Verwendung von Massivdrahtelektroden die Nutzung von Fülldrahtelektroden zunehmender Beliebtheit. Argumente für den Gebrauch liegen vor allem in ihrer guten Verarbeitungseigenschaft wie auch der hohen Wirtschaftlichkeit. Zudem zeichnen sich Fülldrahtelektroden durch eine Reihe technologischer Vorteile aus:
- Beeinflussung der Schweißmetallurgie über die chemische Zusammensetzung der Elektrodenfüllung
- hohe Abschmelzleistung
- nahezu spritzerfreier Prozess
- stabile Lichtbogenausbildung
- besseres Aufschmelzverhalten und dadurch erhöhte Flankenanbindung
Demgegenüber treten insbesondere beim MAG-Schweißen von Fülldrahtelektroden hohe Schweißrauchemissionsraten auf. Um der gesteigerten Schweißrauchentstehung begegnen zu können, bietet weiterhin die Nutzung eines Impulslichtbogens enormes Potenzial. Die emissionsreduzierende Wirkung von Impulstechnik bei Massivdrahtelektroden wurde bereits in zahlreichen Untersuchungen bestätigt. Verringerungen der Emissionen von bis zu 50 % sind möglich [SCOPE2015]. Eine Übertragbarkeit der Ergebnisse auf Fülldrähte ist jedoch aufgrund deren Aufbaus nicht gegeben. An dieser Problematik wird in der Professur Schweißtechnik an der Technischen Universität Chemnitz innerhalb eines Forschungsprojektes gearbeitet, bei dem erste Erkenntnisse zur Verwendung von Impulstechnik bei Fülldrahtelektroden erlangt werden konnten.
Hierbei zeigten sich zunächst im Abschmelzverhalten, analysiert durch hochgeschwindigkeits Videoaufnahmen, mehrheitlich zufällige Tropfenablösungen. Ein Stehenbleiben der Pulverfüllung (Füllungslanze) wie in Abbildung 7 dargestellt, ist in Abhängigkeit der Fülldrahtelektrode ebenfalls zu beobachten. Eine gezielte Anpassung der Stromverlaufsführung galt in Folge dessen als unerlässlich.
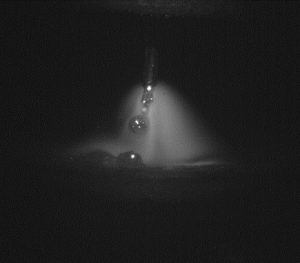
Abbildung 8: Verbessertes Abschmelzverhalten – keine sichtbare Füllungslanze mit steigendem Tropfenabgang
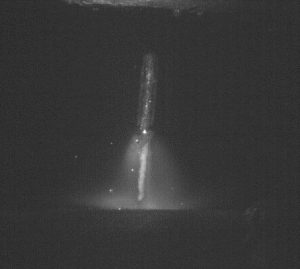
Abbildung 7: Sichtbare Füllungslanze aus nicht aufgeschmolzenem Pulver einer Fülldrahtelektrode
Für diese Impulsgestaltung stehen eine Reihe verschiedener Parameter zur Einstellung zur Verfügung. Sowohl die Anzahl als auch der spezifische Verlauf von Stromplateaus sind individuell programmierbar. Die Menge der einstellbaren Freiheitsgrade stellt dabei eine besondere Herausforderung dar. So sind beispielsweise neben der Höhe einer Impulsstufe sowohl die Stromanstiegsgeschwindigkeiten als auch Zeiten der Stufen regulierbar. Bei idealer Ausnutzung dieser vielfältigen Gestaltungsmöglichkeiten gelingt es, einen Lanzenabbruch zu erzeugen und so das Abschmelzverhalten zu verbessern. Die in Abbildung 8 dargestellte Aufnahme mittels Highspeed-Kamera zeigt ein durch eine spezifisch angepasste Kennlinie verbessertes Abschmelzverhalten. Die überstehende Füllungslanze konnte vermieden und ein gemeinsames Abtropfen von Mantel und Füllung erzeugt werden.
Somit besitzt die Nutzung von Impulstechnik bei Fülldrahtelektroden nicht nur Potenzial bei der Verringerung von Schweißrauchemissionen, sondern ermöglicht auch die gezielte Beeinflussung des Abschmelzverhaltens und damit auch eine individuelle Anpassung an die Gegebenheiten der Fülldrahtelektroden und Schweißaufgaben.
Die durchgeführten Forschungsarbeiten der Technischen Universität Chemnitz an der Professur Schweißtechnik zum Wirkungsgrad und zu den Schweißrauchemissionen zeigen, dass man bei idealer Auslegung der Schweißprozesse eine hohe Wirtschaftlichkeit bei gleichzeitiger Minimierung der gesundheitlichen Belastung des Schweißpersonales erreichen kann. Dadurch ist ein wirtschaftliches Fertigen in einem Hochlohnland wie Deutschland unter strenger Gesetzeslage im Arbeitsschutz möglich.
Literaturverzeichnis
[DIN1011-1]
DIN EN 1011-1 „Schweißen – Empfehlungen zum Schweißen metallischer Werkstoffe – Teil 1: Allgemeine Anleitungen für das Lichtbogenschweißen“, 07/2009.
[DIN1011-2]
DIN EN 1011-2 „Schweißen – Empfehlungen zum Schweißen metallischer Werkstoffe – Teil 2: Lichtbogenschweißen von ferritischen Stählen“, 05/2001.
[DIN15011]
DIN EN ISO 15011-1:2010: „Arbeits- und Gesundheitsschutz beim Schweißen und verwandten Verfahren – Laborverfahren zum Sammeln von Rauch und Gasen – Teil 1: Bestimmung der Rauchemissionsrate beim Lichtbogenschweißen und Sammeln von Rauch zur Analyse“ Beuth Verlag, 03/2010.
[HOE15]
K. Höfer, M. Kusch, P. Mayr: „Bewertung von Einflussfaktoren auf die Schweißrauchemission von Fülldrähten“, 36 Assistentenseminar der Füge- und Schweißtechnik 2015, 05. bis 07. Oktober 2015, Schneverdingen, DVS Verlag 2017, pp. 33-37, DVS-Berichte Band 320, ISBN: 978-3-945023-57-0.
[HÄL14]
A. Hälsig: „Energetische Bilanzierung von Lichtbogenschweißverfahren“, Wissenschaftliche Schriftenreihe CHEMNITZER FÜGETECHNIK, Band 2, Universitätsverlag Chemnitz 2014, ISBN: 978-3-944640-10-5.
[MAT02]
K.-J. Matthes, et al.: „Schweißtechnik- Schweißen von metallischen Konstruktionswerkstoffen“, Fachbuchverlag Leipzig im Carl Hanser Verlag, 2002, ISBN: 3-446-22046-1.
[SCOPE2015]
URL: „https://www.scope-online.de/trenn–und-verbindungstechnik/schweissprozess-focus-puls-schaedliche-schweissrauche-um-50-prozent-reduzieren.htm“ (Abgerufen: 24. Juli 2018, 11:09 UTC+2).
[SEW088]
SEW 088, Beiblatt 1:1993-10 „Schweißgeeignete Feinkornbaustähle; Richtlinien für die Verarbeitung, besonders für das Schmelzschweißen“, 10/1993.
[SREMSG]
Foto Steve Conrad, ©IFMT.
[TGR528]
Ausschuss für Gefahrenstoffe: „TRGS 528 – Schweißtechnische Arbeiten”, 02/2009.
Autoren:
Dr. Wolf Georgi, Dr. André Hälsig, Kevin Höfer, Daniel Reinhold, Prof. Peter Mayr