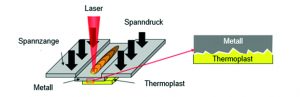
Bild 1: Schematische Darstellung des Verfahrensprinzips
Die Nachfrage nach Kunststoff-Metall-Hybridbauteilen nimmt seit Jahren zu. Hybridbauteile ermöglichen dabei durch eine optimale Ausnutzung der unterschiedlichen Werkstoffeigenschaften von Kunststoffen und Metallen an verschiedene Lastfälle angepasste lokal variable Bauteileigenschaften. Neben konventionellen Fertigungsverfahren, wie dem Verkleben der unterschiedlichen Werkstoffe, stellt das laserbasierte Schmelzkleben einen vielversprechenden und innovativen Ansatz dar [1]. Der Prozess ermöglicht eine flexible und berührungslose Herstellung von Kunststoff-Metall-Hybriden. Die verschleißfreie Wirkungsweise des Laserstrahls führt zu einer lokalen, berührungslosen Erwärmung des zu fügenden Metalls (Bild 1). Das darunterliegende Kunststoffbauteil wird aufgrund der Wärmeleitung lokal aufgeschmolzen und benetzt unter Druck die metallische Oberfläche, sodass nach einer Abkühlphase eine feste Verbindung zwischen den Werkstoffen ohne den Einsatz eines zusätzlichen Klebstoffs entsteht. Der Thermoplast erfüllt somit beim laserbasierten Schmelzkleben sowohl Klebstoff- als auch Bauteilfunktionen. Indem der aus Kunststoff bestehende Fügepartner nicht mittels Spritzguss oder Extrusion, sondern mit Hilfe additiver Fertigungsverfahren hergestellt wird, lassen sich die möglichen Anwendungsfelder von Hybridbauteilen noch zusätzlich erweitern. Additive Fertigungsverfahren, wie das selektive Laserstrahlschmelzen von Kunststoffen (LSS), erlauben die direkte Erzeugung von komplex geformten Bauteilen, die nicht mittels anderer Verfahren realisierbar sind, aus CAD-Dateien ohne formgebende Werkzeuge mit sehr hohen Bauteilfestigkeiten. Im vorliegenden Artikel werden daher metallische Grundkörper und additiv hergestellte Kunststoffbauteile mittels laserbasiertem Schmelzkleben gefügt, um das Anwendungspotential solcher Hybridbauteile zu bestimmen.
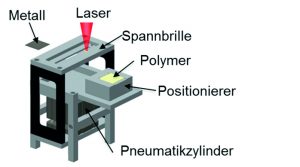
Bild 2: Einspannvorrichtung für den Fügeprozess
Für die Untersuchungen werden Probekörper aus Aluminium (AlMg3) beziehungsweise Chrom-Nickel-Stahl (1.4301) mit Proben aus Polyamid 12 (PA12), welche mittels LSS-Prozess erzeugt werden, gefügt. Die verwendeten Werkstoffe werden in unterschiedlichsten industriellen Anwendungen eingesetzt. Edelstahl zeichnet sich durch eine sehr hohe Korrosionsbeständigkeit im Vergleich zu unlegierten Stählen aus [2], und Aluminium weist als idealer Leichtbauwerkstoff eine sehr geringe Dichte und hohe massenspezifische Steifigkeit und Festigkeit auf. Im Bereich des Laserstrahlschmelzens wird als Pulverwerkstoff meist PA12 eingesetzt, da es ein breites Verarbeitungsfenster hinsichtlich der Schmelz- und Kristallisationstemperatur aufweist und sich hohe Festigkeit bis hin zu den mittels Spritzguss erzielbaren Festigkeiten erreichen lassen [3]. Die Abmaße der Probekörper betragen 50 mm x 50 mm x 1 mm. Um Verunreinigungen wie Öl oder Staub von der Kontaktfläche zu entfernen, werden die Metallteile in einem Ultraschallbad und anschließend mit Aceton gereinigt. Die Probekörper werden mittels einer Einspannvorrichtung im Überlapp positioniert (Bild 2). In den Experimenten wird die Vorschubgeschwindigkeit variiert, wobei die Laserleistung (P = 500 W) und der Strahldurchmesser (d = 6 mm) des verwendeten Scheibenlasers (Pmax = 4 kW, λ = 1030 nm) konstant gehalten werden. In Bild 2 ist der Versuchsaufbau für den Fügeprozess dargestellt. Bedingt durch die Erzeugung der PA12-Probekörper mittels LSS-Prozess aus pulverförmigen Ausgangswerkstoff weisen diese Körper eine hohe Rauheit (Rz = 50 µm) auf. Die hohe Rauheit stellt dabei eine Herausforderung dar, da die für die Wärmeleitung zur Verfügung stehende Kontaktfläche zwischen Metall und Kunststoff im Vergleich zu spritzgegossenen Probekörpern mit einer geringeren Rauheit deutlich kleiner ist.
Für die Bestimmung der Zugscherfestigkeit ist eine geometrische Auswertung der Benetzungsfläche notwendig. Da die Kunststoffprobekörper nicht transparent sind, kann die Benetzungsfläche erst nach der mechanischen Prüfung der Probekörper bestimmt werden. Hierfür werden die Oberflächen der PA12-Probekörper nach der mechanischen Prüfung optisch mittels Scannersystem analysiert, um die Abmaße der Benetzungsfläche zu ermitteln. Die Zugscherfestigkeit ergibt sich aus dem Quotient der Benetzungsfläche und der gemessenen Maximalkraft, bei der die Probekörper versagen.
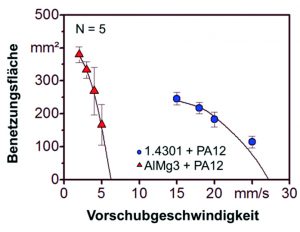
Bild 3: Benetzungsfläche in Abhängigkeit unterschiedlicher Vorschubgeschwindigkeiten
In Bild 3 ist die Benetzungsfläche in Abhängigkeit unterschiedlicher Vorschubgeschwindigkeiten dargestellt. Da die Laserleistung und der Strahldurchmesser konstant gehalten werden, führt eine Erhöhung bzw. Verringerung der Vorschubgeschwindigkeit zu einer insgesamt geringeren bzw. höheren Energieeinbringung. Bei den Hybrid-Bauteilen aus Aluminium und PA12 ist ein näherungsweiser linearer Zusammenhang zwischen der Variation der Vorschubgeschwindigkeit und der Benetzungsfläche bis zu einem Maximum von 379,5 ± 23,9 mm² erkennbar. Für die Probekörper aus Edelstahl ergeben sich geringere Benetzungsflächen im Bereich von 114,2 mm² bis 246,0 mm². Im Vergleich zu Aluminium weist Edelstahl eine höhere Absorption und eine zehnfach geringere Wärmeleitfähigkeit auf. Dadurch wird für den Fügeprozess im Vergleich zu Aluminium deutlich weniger Energie benötigt und die Größe des aufgeschmolzenen Bereichs des PA12 bleibt kleiner, da die Verluste durch Wärmeleitung geringer ausfallen.
Die erreichten Bruchkräfte der Probekörper sind in Bild 4 dargestellt.
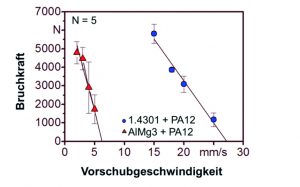
Bild 4: Bruchkraft in Abhängigkeit unterschiedlicher Vorschubgeschwindigkeiten
Hinsichtlich der Bruchkräfte ist für beide Werkstoffkombinationen ein näherungsweiser linearer Zusammenhang zwischen der Vorschubgeschwindigkeit und der Bruchkraft feststellbar. Die maximale Bruchkraft für Aluminium beträgt 4789.8 ± 600.6 N und für Edelstahl 5876.8 ± 560.2 N.
Die sich aus der Benetzungsfläche und der Bruchkraft ergebenden Zugscherfestigkeiten der unterschiedlichen Werkstoffkombinationen sind in Bild 5 dargestellt. Für Aluminium ergeben sich Werte zwischen 10 und 14 MPa. Dabei versagt der Großteil der gefügten Probekörper durch einen adhäsiven Bruch, und nur ein geringerer Teil durch einen Mischbruch, bei dem das PA12 nur teilweise abgeschert wird und der restliche Teil auf der metallischen Oberfläche verbleibt. Die Ergebnisse zeigen, dass für Vorschubgeschwindigkeiten über 5 mm/s der Energieeintrag nicht ausreicht, um den Kunststoff ausreichend aufzuschmelzen, so dass keine stabile Verbindung möglich ist. Die Edelstahlprobekörper weisen hingegen deutlich höhere Zugscherfestigkeiten auf. Da die Bruchkräfte vergleichbar den Kräften beim Aluminium sind, resultieren aus der geringeren Benetzungsfläche durch geringere Wärmeverluste signifikant höhere Zugscherfestigkeiten von bis 23,7 ± 1.4 MPa.
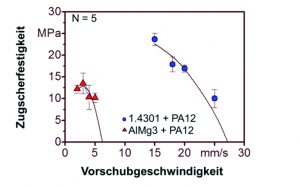
Bild 5: Zugscherfestigkeit in Abhängigkeit von unterschiedlichen Vorschubgeschwindigkeiten
Zusammenfassend kann festgestellt werden, dass das laserbasierte Schmelzkleben von additiv gefertigten Kunststoffbauteilen mit Metallen sehr hohe Verbundfestigkeiten zwischen den ungleichen Werkstoffarten ermöglichen kann, die Verarbeitungsparameter jedoch stark von den Werkstoffeigenschaften der Fügepartner abhängen. Von großem Einfluss auf die Fügequalität ist dabei eine auf die jeweiligen Werkstoffe abgestimmte Energieeinbringung der Laserstrahlung unter Beachtung unterschiedlich hoher Wärmeleitungsverluste im metallischen Fügepartner. Das vorgestellte Verfahren besitzt ein großes Potential, die sich aus dem Einsatz von additiven Fertigungsverfahren ergebenden Vorteile auch für Kunststoff-Metall-Hybridbauteile umzusetzen und dadurch an die unterschiedlichen Belastungsfälle lokal angepasste Bauteileigenschaften zu erzielen.
[1] Amend, P., et al., 2016. Process-Structure -Property Relationship of Laser-Joined Thermoplastic Metal Hybrids. in: “J. Laser Appl.”, Vol. 28, No. 2.
[2] Henkel, G., 2008. Topographie und Morphologie funktionaler Edelstahloberflächen, Expert Verlag.
[3] Drexler, M, et al., (2015). Einfluss des Pulverauftragsprozesses auf den selektiven Strahlschmelzprozess thermoplastischer Kunststoffe. in: „RTeJournal – Fachforum für Rapid Technologie“, Vol. 2015.
Autor:
Dipl.-Wirtsch.-Ing. Tobias Laumer
Kontakt und weitere Informationen:
Bayerisches Laserzentrum GmbH,
Konrad-Zuse-Straße 2-6,
91052 Erlangen
Telefon: 09131/97790-0,
E-Mail: info@blz.org,
URL: www.blz.org