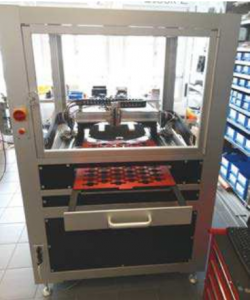
Prüfzelle
Die berührungslose Vermessung von Bauteilen erfolgt mit dem OCT System 50-mal schneller als mit konventionellen Vision-Systemen und genauer als ein Mikrometer. In unserer OCT-Anlage werden in einem Messvorgang Schichtdicken, Abmessungen, Volumen, die Parallelität oder die Planarität von Ebenen exakt vermessen.
Anlage zur Vermessung thermisch umgeformten Bauteilen
Eine Prüfanlage zur Vermessung der Geometrie von thermisch umgeformten Bauteilen (z.B. Prüfanlage für Kaffeekapseln) besteht aus zwei OCT-Kameras mit integrierten ASP Arrays. Die Kameras erfassen das Volumen im exakt definierten Zwischenraum. Der DUAL-Messkopf ist auf einer stabilen Plattform montiert und sitzt auf einem Koordinatensystem mit einer Schrittauflösung von 100 nm.
Zur Prüfanlage für Kaffekapseln gehören 2 Prüftabletts als Messplattformen mit den Kavitäten für die zu prüfenden Bauteile. Die Bedienung der Anlage erfolgt über einen Touchscreen, der am Gehäuse der Prüfstation montiert ist. Die erforderlichen Messprogramme stehen nach Vorgabe des Kunden zur Verfügung.
Die Anlage braucht 1,30 m x 1,20 m Platz und ist 2,10 m hoch (ohne Betriebsanzeige). Sie wird über den Touchscreen, der am Gehäuse der Prüfstation befestigt ist, bedient. Eine Lampe zeigt den Prüfstand an: Rot: Fehlermeldung, Gelb: Warteposition, Grün: Prüfung in Arbeit.
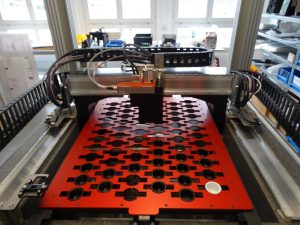
Bauteilprüfung: Die Vermessung eines Flaschenverschluss dauert weniger als 10 Sekunden, die Vermessung einer Kaffeekapsel weniger als 20 Sekunden
Ablauf einer Bauteilprüfung
Ein Batch mit einer Anzahl Bauteile wird aus der Produktion entnommen und manuell oder automatisch in die Kavitäten auf dem Prüftablett eingelegt. Die Vermessung erfolgt durch Bewegen des Messkopfes in x- und y-Richtung (Steaching der Bilder) und in z-Richtung (Vertikal). Die laterale Bewegung (x- und y-Richtung) ist durch das zu vermessende Bauteil definiert. Die Form des Bauteils respektive die zu vermessende Kontur des Bauteils ist im Messrezept für das entsprechende Bauteil programmiert. Ist das „Field of View“ (Gesichtsfeld) der Kamerasysteme kleiner als das zu prüfende Bauteil, werden zur Erfassung der ganzen Fläche mehrere OCT-Bilder aufgenommen (Stitching). Die Vermessung erfolgt bei einer Bildpunktgrösse von 40 µm mit einer reproduzierbaren Genauigkeit von +/- 10 Mikrometer.
Aus der Vereinigung der OCT- Bilder lassen sich für verschiedene Formen folgende Messdaten ableiten:
- Außendurchmesser
- Innendurchmesser
- Durchmesser auf einer definierten Höhe
- Bodendicke (Minimale oder Maximale Bodendicke)
- Dicke des definierter Ebenen auf dem Bauteil
- Dicke der Wand im vertikalen Bereich (Mit dem Zusatzmodul)
- Durchmesser auf einer definierten Höhe oder an einem definierten Ort
- Siegelranddicke und Siegelrandbreite
- Lage von besonderen Merkmalen
- Energiegeber-Höhe
- Ebenheit der Siegelebene
- Ebenheit von Flächen in definierter Höhe
- Parallelität zwischen verschiedenen Flächen in ausgewählter Höhenlage
- Gesamthöhe des Bauteils
- Unterschiede in der Foliendicke
- Volumen des Bauteils
Software (basierend auf Lab View)
In der Grundsoftware zur Anlage sind enthalten:
- Steuerung der Prüfanlage
- Benutzeroberfläche (GUI)
- Barcodescanner (für das Einlesen bereits digital vorhandener Daten)
- OCR-System (Optical character Reader)
- Prüfrezept (das Prüfrezept für ein Bauteil)
- Auswertealgorithmen
- Protokolldatenblatt (Elektronisch und auf Papier) für das definierte Prüfrezept
- Drucker zur Kennzeichnung der aufzubewahrenden Bauteile (Nachweispflicht)
- Internetanschluss (damit ist der externe Zugriff auf die Anlage sichergestellt)
- Zusatz-Software nach Kundenbedarf
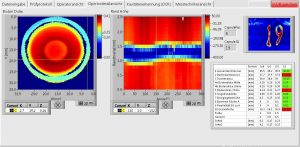
Bildschirm Messdaten
Allgemeine Anforderungen
Auf der 3D-Prüfanlage können flache oder hohe Bauteile in runder, ovaler oder eckiger Form vermessen werden. Die Prüfung der Bauteile erfolgt rechnergesteuert und beinhaltet ein vollständiges Messprotokoll, das den heute geltenden metrologischen Anforderungen gerecht wird. Die Messgenauigkeiten liegen im Submikrometerbereich. Bisher haben wir Standard-Prüfkriterien mit +/- 10 µm eingehalten und die Messmittelfähigkeit bestanden.
Auflösung:
Grundsätzlich unterscheidet man zwischen ‘Pixelauflösung’ und ‘Merkmalauflösung’. Die Pixelauflösung ist eine rein geometrische Rechnung, weshalb zur Bestimmung der Leistungsfähigkeit eines Systems die Merkmalauflösung beigezogen wird. Die Merkmalauflösung ist einiges besser als die Pixelauflösung, weil Merkmale über Ausgleichsrechnungen aus mehreren Pixeldaten ermittelt werden. Aus der lateralen Pixelauflösung von 12 mm ergibt sich rechnerisch ein Pixel von 40 µm, mit der Merkmalauflösung „Kannte“, „Begrenzung“ oder „Radius“ wird das Merkmal genauer als 10 µm bestimmt. (+/- 5 µm). Bei 2D-Messaufgaben wird für die Kantenerkennung typisch mit dem Faktor 10 interpoliert, d.h. +/- 4 µm. Ähnliches gilt für die vertikale Achse. Aus einer Voxelhöhe von 2 µm erzielen wird typisch eine bessere Auflösung als 100 nm erreicht.
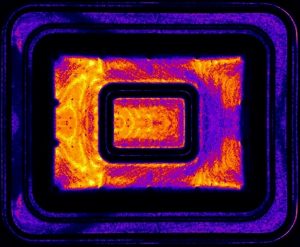
Geometrie
Genauigkeit:
Die Genauigkeit in lateraler Richtung wird normalerweise von den Verzerrungen der Abbildungsoptik begrenzt. Für die 3D-Prüfanlage setzen wir extrem verzerrungsarme Doppel-Telezentrische Objektive ein. Die Verzerrung der Objektive ist kleiner als 0.01% (Herstellerangaben) und damit vernachlässigbar. Die laterale Genauigkeit wird etwa gleich gross wie die Merkmalauflösung (Wert um 10µm, (+/- 5 µm).
Die vertikale Genauigkeit hängt im Wesentlichen von der Genauigkeit des Glasmassstabes ab. Im Falle der 3D-Prüfanlage ergibt sich eine vertikale Genauigkeit von bis zu 100 nm.
Vorteile der OCT-Prüfanlage:
- geringer Platzbedarf
- hohe Genauigkeit, Zuverlässigkeit und Betriebssicherheit
- robust im industriellen Einsatz
- sichere Vorder- und Hintergrundausblendung oder Ausleuchtung
- Der Prüfprozess kann flexibel weiter ausgebaut und automatisiert werden.
- Alle Messungen werden automatisch protokolliert und dokumentiert.
- Fehler werden archiviert und dokumentiert.
- Jeder Prozess-Schritt ist mit Datum, Zeit und Aktion gesichert.
- Das Prüfprotokoll entspricht internationalen Standards.
- Die Prüfteile können automatisch in die Prüfkabine eingeschleust werden.
- Die Prüfteile können automatisch aus dem Produktionsprozess ausgeschleust werden.
- kein Personal zur Prüfung notwendig
- Identifikation der am Kapselboden eingeprägten Werkzeugnummer
- Lokalisation der eingeprägten Noppen am Boden einer Kapsel
- Eindeutige Bauteil- Orientierung (Ausrichtung)
- gleichzeitige Volumenbestimmung
- u.v.m
Kontaktperson und Projektverantwortlicher:
Christian Florin