Das Institut für Oberflächentechnik (IOT) der RWTH Aachen University ist eine der führenden Forschungsinstitutionen auf dem Gebiet der PVD-Beschichtungstechnologie (Physikalische Gasphasenabscheidung). Die F&E-Gruppe PVD-Technologie (Werkzeuge) beschäftigt sich mit der Erforschung und Applikation von PVD-Dünnschichten für vielfältige Anwendungen. Hierbei setzt sie die am Markt üblichen und industriell eingesetzten Verfahrensvarianten, wie Magnetron Sputtern (MS) mit unterschiedlichen Kammervolumina sowie die neueste Generation von gepulsten Hochleistungsplasmen wie das High-Power-Pulse-Magnetron-Sputtering (HPPMS) und Lichtbogenverdampfen ein. Durch die Forschung an großskaligen, industriellen Anlagen, wie in Abbildung 1 (a) beispielhaft dargestellt, gelingt es, den Bogen zwischen Grundlagenforschung und industrierelevanten Beschichtungsprozessen zu spannen.
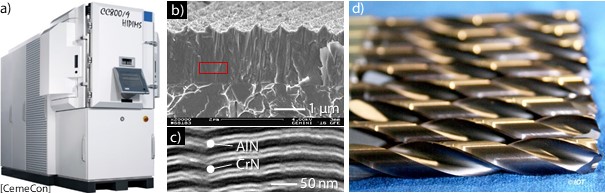
Abb. 1: Großskalige, industrielle Beschichtungsanlage des Typs CC800/9-HPPMS der CemeCon AG (a), laserstrukturierte Beschichtung für den Einsatz in der Kunststoffverarbeitung (b), CrN/AlN-Nano laminat (c) und PVD-beschichtete Langlochbohrer (d
Die F&E-Gruppe entwickelt neuartige Werkstofflösungen, um die Werkzeuge im Einsatz vor Verschleiß und Korrosion zu schützen. Auf diese Weise werden die Standzeit und die Leistungsfähigkeit der Werkzeuge erhöht. Die Gruppe forscht bspw. in Zusammenarbeit mit weiteren Instituten der RWTH Aachen University an der Entwicklung einer durchgängigen Prozesskette zur Herstellung strukturierter, optisch funktionaler Kunststoffbauteile. Hierbei konnte durch Beschichtung des im Mikro- und Nanometerbereich laserstrukturierten Werkzeuges, vgl. Abbildung 1 (b), mittels PVD die Adhäsionskraft zwischen der Werkzeugoberfläche und den verarbeiteten Kunststoffen verringert und die Verschleißbeständigkeit verbessert werden. Abbildung 1 (c) zeigt den Schichtaufbau einer mehrlagigen PVD-Beschichtung, bei der die Einzellagendicke nur wenige Nanometer beträgt. Auf diese Weise lassen sich bspw. die mechanischen Eigenschaften wie die Eindringhärte steigern. Eine weitere typische Anwendung der PVD-Technologie sind Verschleiß-schutzschichten auf Zerspanwerkzeugen, wie sie in Abbildung 1 (d) dargestellt sind. Darüber hinaus werden durch die F&E-Gruppe neue Anwendungsfelder erschlossen. Zum Beispiel wird die Entwicklung neuartiger Sensorschichten erforscht. Hierdurch wird die Funktion der orts- und zeitaufgelösten Temperaturmessung in der Schnittstelle zwischen beschichtetem Werkzeug und bearbeitetem Werkstück in die Hartstoffschichten integriert.
Neben modernsten Beschichtungsanlagen greift die F&E-Gruppe auf umfassend ausgestattete Analyselabore am Institut zurück, mittels der die Bestimmung der physikalischen, chemischen und tribologischen Eigenschaften der eingesetzten Schichtsysteme erfolgt. Zu dem umfangreichen Portfolio zählen etwa tribologische Analysen wie Pin-on-Disk- und Schwing-Verschleiß-Tribometer sowie ein Impact-Tester, mit denen gleichförmige, linear oszillierende und schlagende Belastungen aufgebracht werden können. Weiterhin verfügt das IOT über eine umfangreiche Analytik und Thermoanalytik wozu bspw. ein konfokales Lasermikroskop zählen, mit dem 3D-Tiefenprofile aufgenommen werden können. Weiterhin steht ein Raman-Spektrometer zur Verfügung, mit dem Reaktionsprodukte tribochemischer Reaktionen nachgewiesen werden können.
Neben diesen klassischen Methoden zur Schichtcharakterisierung wird bei der Erforschung und Entwicklung neuartiger Hartstoffschichten der gesamte Weg von der Schichtsynthese bis hin zum einsatzbereiten Werkzeug vollzogen. Dieser Weg beginnt im Plasma, in dem die Atome und Ionen für die Schichtbildung aus dem Ausgangsmaterial, dem sogenannten Target, erzeugt werden. Um die grundlegenden Mechanismen auf dem Syntheseweg in Hochleistungsplasmen besser zu verstehen, werden unterschiedliche plasmadiagnostische Methoden wie die Massenspektroskopie, optische Emissionsspektroskopie und Langmuir-Sondendiagnostik, angewendet. In Abbildung 2 (a) ist die mittels Gegenfeldanalysator bestimmte mittlere Ionenenergie in Abhängigkeit der gepulsten Biasspannung am Substrattisch und der Zeit in einem PVD-Prozess aufgetragen. Hierbei wird die höhere mittlere Ionenenergie bei gesteigerter gepulster Biasspannung sichtbar. Die Plasmadiagnostik wird eingesetzt, um gezielt Prozessfenster zu bestimmen und die Entwicklungszeiten zu verkürzen.
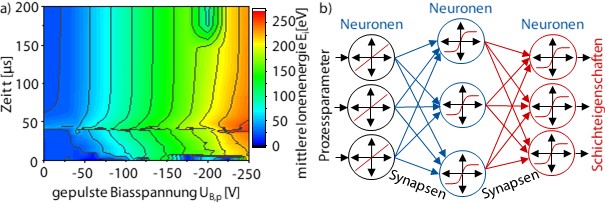
Abb. 2: Zeitaufgelöste und substratseitige Messung der mittleren Ionenenergie in Abhängigkeit der gepulsten Biasspannung (a) und schematischer Aufbau eines künstlichen neuronalen Netzwerkes (b
Um ein umfassendes Prozessverständnis aufzubauen, werden die Ergebnisse aus der Plasmadiagnostik mit den Schichteigenschaften korreliert. Die auftretenden Wechselwirkungen auf dem Syntheseweg vom Atom im Target bis zur aufwachsenden Hartstoffschicht sind jedoch äußerst komplex. Daher forscht die F&E-Gruppe am Einsatz künstlicher neuronaler Netzwerke (KNN), die große Datenmengen effizient auswerten und eine vereinfachte Prozessentwicklung unter reduzierten Entwicklungszeiten ermöglichen. In Abbildung 2 (b) ist der Aufbau einer KNN schematisch dargestellt. Die Prozessparameter werden im KNN über die, durch Synapsen verknüpften, Neuronen mit den resultierenden Schichteigenschaften korreliert. Durch Analyse der hochgradig nicht linearen Verknüpfungen mittels des KNN werden die entscheidenden Ursache-Wirkungs-Zusammenhänge schneller erkannt und können zielgerichteter erforscht werden. Ein umfassendes Prozessverständnis ermöglicht eine effiziente Schichtentwicklung und trägt zu einer Reduktion der Entwicklungskosten von Beschichtungsprozessen bei. Durch Schichtcharakterisierung und Prozessdiagnostik werden die Beschichtungen für die konkreten Beanspruchungskollektive unterschiedlicher technischer Anwendung gezielt ausgelegt.
Autoren:
Prof. Dr.-Ing. Kirsten Bobzin
Dr.-Ing. Tobias Brögelmann
Dipl.-Ing. Nathan C. Kruppe
M.Sc. Marco Carlet
Institut für Oberflächentechnik
RWTH Aachen University
info@iot.rwth-aachen.de