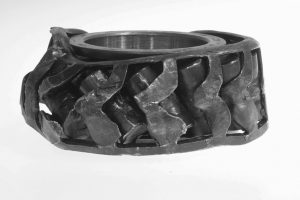
Abb. 1 Bildquelle: The Timken Company
Von Russell Folger, Jerry Rhodes und David Novak, The Timken Company
Lager-„Killer“ sind Bedingungen, die einem Lagersystem Schaden zufügen und dessen Lebensdauer vorzeitig beenden können. Die vier häufigsten Ursachen sind:
Ungeeignete Schmierung, Verschmutzung, Überlast, falsche Handhabung und Installation. Diese Ursachen betreffen eine Vielzahl von Lagertypen, darunter Zylinderrollen-, Pendelrollen-, Nadel-, Kegelrollen- und Kugellagerkonstruktionen.
Die Folgen von Lagerschäden an industriellen Anlagen können erheblich sein:
Verletzungen von Anlagenpersonal, reduzierte Betriebseffizienz, Kosten für Lagerreparatur oder Lagerersatz, Kosten für Reparatur oder Ersatz anderer Komponenten – wie z. B. Gehäuse oder Wellen –, die durch von den beschädigten Lagern ausgehende Vibrationen oder hohe Temperaturen beschädigt werden können, sowie ungeplante Ausfallzeiten von Anlagen.
Die Anlagenbetreiber sollten verstehen, wie lagerschädigende Bedingungen zu überwachen und zu vermeiden sind.
Ungeeignete Schmierung
Der größte Teil der Lagerschäden ist auf ungeeignete Schmierung zurückzuführen, die in acht Hauptkategorien klassifiziert werden kann: Überfüllung, Mangelschmierung, falsche Spezifikation, Mischung oder Inkompatibilität, falsche Schmierungssysteme und -intervalle, überaltertes Fett oder Öl, Verschmutzung durch Wasser oder Fremdstoffe.
Menge, Typ, Sorte, Zuführsystem, Nachfüllintervall, Viskosität und Additive für das Schmiermittel müssen zusammen mit dem Erstausrüster und dem Lagerlieferanten bestimmt werden. Die Schmierstoffe müssen für jedes Lagersystem basierend auf dessen Historie, Belastung, Drehzahlen, Dichtsystemen, Betriebsbedingungen und erwarteter Lebensdauer richtig berechnet werden.
Hersteller oder Fachhändler müssen detaillierte Empfehlungen über Lagerbedingungen, maximale Haltbarkeitsdauer, Zuführsysteme, Filtrationsgrade und andere Vorsichtsmaßnahmen zur Verfügung stellen. Bei sich während des Betriebs ändernden Bedingungen wird immer eine Beratung empfohlen.
Das Mischen verschiedener Sorten oder Marken von Ölen oder Fetten kann katastrophale Folgen haben. Die Schmierstoffe müssen zueinander vollständig kompatibel sein, um über die gesamte Lebensdauer einwandfrei zu funktionieren. Aufgrund erheblicher chemischer Unterschiede in den Formeln (Verdickungsmittel, Grundöle, Additive usw.) können einige Schmiermittel nicht mit anderen gemischt werden. Vor dem Wechsel eines Schmiermittels muss grundsätzlich die Kompatibilität in Zusammenarbeit mit den Schmierstofflieferanten geprüft werden. In einigen Fällen sind spezielle Testverfahren erforderlich. Erhält man für die Verwendung grünes Licht, sollte man sich genug Zeit nehmen, um den alten Schmierstoff vollständig aus dem System zu entfernen. Dies ist auch ein guter Zeitpunkt, um den Zustand von Leitungen, Anschlüssen, Verteilern, Pumpen und Dichtungen zu prüfen und entsprechende Korrekturmaßnahmen einzuleiten. Sobald das Schmiermittel ausgewählt und eingesetzt wurde, wird überprüft, ob der Betrieb störungsfrei ist. Eine geeignete Methode hierzu ist die punktuelle oder permanente Temperaturüberwachung. Wenn die Lagerbetriebstemperatur mehr als 80° C beträgt, kann die Lebensdauer des Öls drastisch abnehmen, selbst wenn Oxidationshemmer verwendet werden. Die Temperaturen können durch hohe Umgebungs- oder Prozesstemperaturen, oder durch schwere Betriebsbedingungen, welche den Rollreibwiderstand verstärken, verursacht werden. Andererseits können sehr niedrige Umgebungstemperaturen ebenfalls zum Problem für das Schmiermittel werden, da es verdickt und möglicherweise nicht gut fließt. Deshalb muss zusammen mit dem Lagerlieferanten der zulässige Betriebstemperaturbereich geprüft werden. Wenn die Lagerschmierung auf irgendeine Weise ungeeignet ist, können verschiedenste Schäden entstehen.
Vier fortschreitende Schadensstufen sind:
- Eine Verfärbung – ein dunkler Werden des Metalls – tritt ein, wenn der Kontakt von Metall auf Metall zu übermäßigen Lagertemperaturen führt. Deshalb sollte man insbesondere auf eine Verfärbung der Laufringe und der Rollen achten. In weniger schweren Fällen stammt die Verfärbung vom Schmiermittel selbst, das die Lagerflächen färbt. In schwereren Fällen hat die hohe Hitze Anlassverfärbungen erzeugt.
- Riefenbildung oder Schälungen jeglicher Art und Intensität sind Anzeichen für schwerwiegende Schmierungsprobleme und erfordern sofortige Gegenmaßnahmen. In diesem Fall nach Kaltverschweißungen oder Mikrobrüchen auf den Kontaktflächen suchen.
- Eine lokale Riefenbildung entsteht durch hohe örtliche Temperaturen, einen gerissenen Schmierfilm und den direkten mechanischen Kontakt von Bauteilen. Bei Kegelrollenlagern ist dies an einer schlingenförmigen Verriefung am großen Rollenende und dem Führungsbord des Innenrings erkennbar.
- Eine vollständige Blockade des Lagers kann auftreten, wenn hohe örtliche Hitze oder fortschreitender Verschleiß wesentliche Änderungen an der ursprünglichen Lagergeometrie oder der internen Lagereinstellung verursachen. Ein Auslängen der Wälzkörper, die Zerstörung des Lagerkäfigs, Schmelzfluss, übermäßiger Drehmoment- und Kraftverlust und ein vollständiges Festfressen des Lagers (Abb. 1) können die Folge sein.
Verschmutzung
Fremdkörper sind eine weitere wesentliche Ursache für Lagerprobleme. Selbst kleine Mengen an winzigen Fremdkörpern – Staub, Schmutz, Rückstände – können den Schmierfilm unterbrechen, was zu Schäden der Lageroberfläche und einer reduzierten Lagerlebensdauer führt. Besonders schädlich für Lager ist Wasser. Schon 1% Wasser in Fett oder in Öl kann einen erheblichen Einfluss auf die Lagerlebensdauer haben. Zum Schutz gegen Verschmutzungen sind Dichtungen sehr wichtig. Zunächst müssen die richtigen Dichtungen für die jeweilige Anwendung ausgewählt werden – Lieferanten haben die erforderlichen Informationen über die Leistung ihrer Ausrüstung, die Montageanforderungen, das Schmiersystem, die Wellenausrichtung und andere Umgebungsfaktoren haben. Ebenfalls sehr wichtig sind Dichtungsart, Dichtungsmaterial und die Art der Dichtungsmontage.
Vermeiden Sie außerdem eine Verschmutzung durch die folgenden drei Praktiken:
- Wenn Lager zur Inspektion ausgebaut werden, waschen und trocknen Sie sie. Nach dem Waschen und Trocknen von Lagern – oder beim Einlagern – müssen diese mit Öl oder einem anderen Konservierungsmittel überzogen und in Schutzpapier eingeschlagen werden.
- Nehmen und prüfen Sie routinemäßig Öl- bzw. Fettproben. Im Idealfall weisen Öl bzw. Fett gleichbleibende Eigenschaften auf. Wenn Festpartikel vorhanden sind, suchen Sie die Fehlerquelle und führen Sie Abhilfemaßnahmen durch.
- Es reicht nicht, sich allein auf die Filterung zu verlassen, um Verschmutzungen vorzubeugen. Bei harten Bedingungen, bei denen Filter schweren Anforderungen ausgesetzt sein können, müssen Techniker regelmäßige Inspektionen und/oder den Ersatz von Filterelementen sorgfältig planen.
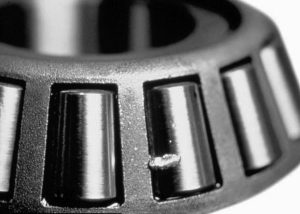
Abb. 2 Bildquelle: The Timken Company
Wenn Lager durch Fremdkörper verunreinigt werden, können vielerlei Schäden entstehen. Kleine Partikel können im Lager z. B. übermäßigen Abrieb verursachen. Sand, aus Schleif- oder Bearbeitungsprozessen stammende Metallspäne oder Karbide von Zahnrädern verschleißen die Rollenelemente und Laufbahnen. Der Abrieb kann auch andere Maschinenelemente beeinträchtigen oder den Dichtungsverschleiß erhöhen, was die Leistung mindert. Eine unzureichende Erstreinigung von Gehäusen und Teilen, eine unwirksame Filterung oder eine unzureichende Filterwartung kann zu einer Ansammlung von abrasiven Partikeln führen. Durch das Lager rollende harte Partikel können eine Eindrückung und eine Beschädigung der Rollen und Lagerringe verursachen. Metallspäne oder große Schmutzpartikel, die nach Bearbeitungsvorgängen und unzureichender Reinigung im Lagergehäuse verbleiben, können frühzeitige Ermüdungsschäden verursachen. Ursachen für eine Verschmutzung aus internen Ablagerungen sind der Verschleiß von Zahnrädern, Keilen, Dichtungen, Kupplungen, Bremsen, Gelenkstücken, unzureichend gereinigte Gehäuse und defekte oder abgeblätterte Komponenten. Diese harten Partikel wandern durch das Schmierungssystem und das Lager und beschädigen schließlich die Oberflächen. Die Metallerhebungen rund um die Vertiefungen steigern dann die Oberflächenbelastungen, was zu Schälungen und reduzierter Lagerlebensdauer führt. Durch Späne oder Metallpartikel hervorgerufene extrem schwere Lasten führen zur Riefenbildung. Diese Verschmutzungen verkeilen sich im weichen Käfigmaterial und verursachen Riefen in den Rollen (Abb. 2). Dieser Zustand führt zu einer unzureichenden Rollkontaktgeometrie; er kann die Lebensdauer reduzieren.
Die Verätzung oder Korrosion ist eines der schwerwiegendsten Probleme von Lagern (Abb. 3). Die kontrollierte Oberflächenrauigkeit auf den Lagerkomponenten macht diese Flächen, wenn sie nicht ausreichend geschützt werden, für durch Feuchtigkeit und Wasser verursachte Korrosionsschäden anfällig. Temperaturänderungen oder unzureichende Lagerungsbedingungen führen zu einer Ansammlung von Kondenswasser im Lagergehäuse, was häufig eine Verätzung zur Folge hat. Längere Zeit nicht verwendete Anlagenteile sind für diese schleichende Schadensart, die sich schnell ausbreiten und zu schweren Abplatzungsschäden führen kann, besonders anfällig.
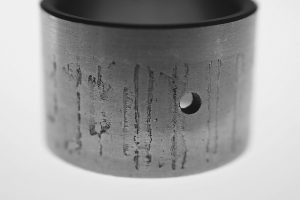
Abb. 3 Bildquelle: The Timken CompanyEin häufig begangener
Überlast
Wenn Lager in Bezug auf Last, Drehzahl oder Temperatur zwangsweise über konstruktive Nenngrenzen hinaus betrieben werden, spricht man von Überlast. Je größer die Überlastung, desto kürzer die Lagerlebensdauer. Umliegende Komponenten können hiervon ebenfalls betroffen sein. In Extremfällen können die Lagerbauteile brechen. Überlast kann bei nicht bestimmungsgemäßem Betrieb verursacht werden oder dadurch entstehen, dass Lagerkonstruktion und Anwendung nicht zusammenpassen. Bei der Auswahl der richtigen Lagerkonstruktion für die Anwendung berücksichtigen der Erstausrüster und der Lagerhersteller die Betriebstemperatur, die Temperaturwechselrate, Art und Intensität der möglichen Verschmutzung, Betriebsdrehzahlen und -beschleunigungswerte, Vibrationen und vieles mehr.
Überlast-Warnzeichen können Geräusche oder Vibrationen, ein Anstieg der Systemtemperatur, Metallspäne in Schmiermittel und Filtern sowie eine verminderte Systemleistung sein. Ein Anzeichen für Überlast sind Eindrückungen oder Abplatzungen des Lagermaterials aufgrund von Materialermüdung. Abplatzungen treten hauptsächlich auf den Laufringen und den Rollen des Lagers auf. Andere Überlast-Anzeichen sind: Rollenbruch, Schälungen, Bruch des Außenringbords, harte Riefen oder das Vorhandensein plastischer Verformungen an den Kanten der Rollen und den Führungsborden sowie Metallverformungen in den Freistichen der Führungsborde.
Falsche Handhabung und Installation
Techniker müssen sicher sein, die für die Handhabung und den Einbau von Lagern richtigen Methoden und Werkzeuge zu verwenden. Lager sind hochentwickelte Bauteile; selbst die kleinste Verformung oder ein Kratzer kann deren Leistung und Zuverlässigkeit beeinträchtigen. Bewahren Sie Lager bis unmittelbar vor der Montage in der vor Korrosion schützenden Schutzverpackung auf. Reinigen Sie Werkzeuge immer in einer sauberen Umgebung. Wischen Sie das Konservierungsmittel auf den Lagern nicht ab. Ein häufig begangener Fehler ist das Abwischen des vom Lagerhersteller aufgetragenen Konservierungsmittels und das Entfernen der Schutzverpackung. Falls das Lager aus irgendeinem Grund aus der Originalverpackung genommen werden muss, tragen Sie Konservierungsmittel auf und stellen Sie eine gute Verpackung der Teile sicher. Wichtig ist auch, Buch über alle Wartungsaktivitäten zu führen. Notieren Sie Datum, Modell und Seriennummer des Anlagenteils, Gruppe und Seriennummer (soweit verfügbar) sowie den Hersteller des Lagers. Fügen Sie Kommentare in Bezug auf die Überholung von Gehäusen, Wellen und anderen ersetzten Bauteilen hinzu. Achten Sie darauf, Lagerbauteile – insbesondere Lagerkäfige – nicht zu beschädigen; setzen Sie zur Handhabung und während des gesamten Montagevorgangs geeignete Geräte und Methoden ein. Beim Ausdrücken von Außenringen aus Gehäusen oder Radnaben kann eine unvorsichtige Handhabung zu Graten oder Aufwürfen in den Außenringsitzen führen. Wenn ein Werkzeug auf die Gehäusesitzfläche drückt, entstehen rund um die Druckstelle Erhebungen. Werden diese Bereiche vor dem Wiedereinbau des Außenrings nicht nachgearbeitet, setzt sich die Erhebung durch den Außenring fort und bildet eine entsprechende Erhebung in der Laufbahn des Außenrings. Dies erhöht den örtlichen Rollwiderstand und kann zu verringerter Lagerlebensdauer, örtlichen Abplatzungen oder – unter extremen Bedingungen – zum Ausfall des Bauteils führen. Die sofortigen Auswirkungen der Aufwürfe und tiefen Kratzer können Rauigkeit, Vibrationen und Geräuschbildungen im Lager sein.
Die nachstehenden spezifischen Schadenstypen können durch falsche Handhabung und falschen Ein- oder Ausbau verursacht werden: Eindrückungen im Außenring, gebrochener Innenringführungsbord, gebrochener Außenringbord, Kerben im Rollenabstand, und Eindrückungen oder Riefen in den Laufbahnen.
Die Lagermontage beginnt mit einer sorgfältigen Beachtung von Passung, Ausrichtung und Lagereinstellung. Eine richtige Ausrichtung während der Montage ist wichtig, da die Lebensdauer eines fehlausgerichteten Lagers abnimmt, wenn die Tragkraft überschritten wird. Die Reduzierung der Lebensdauer hängt vom Grad der Fehlausrichtung ab. Bei einer übermäßigen Fehlausrichtung werden die Lasten im Lager nicht gleichmäßig über Rollen und Lagerringe verteilt, sondern konzentrieren sich nur auf einen Teil der Rollen und Laufbahnen, was zu einer frühen Materialermüdung der Metalle in diesen Bereichen führen kann. Die angrenzenden Flächen, die Sitze und Schultern, sowie die entsprechenden Ausrundungen und Unterschneidungen sind für eine angemessene Unterstützung und Übertragung der Kräfte ausgelegt. Sie müssen innerhalb der vom Lagerhersteller festgelegten Grenzen liegen.
Die Lagereinstellung umfasst die richtige Zuweisung von nominalem und montiertem Radialspiel, axialer Lagerluft und – bei einigen Anlagen – axialer Vorspannung. Falsches Lagerspiel kann zu einer Vielzahl von Bedingungen führen, die übermäßiges Drehmoment, Spannungen, Käfigschäden oder Überhitzung umfassen.
Weitere Informationen: www.timken.com