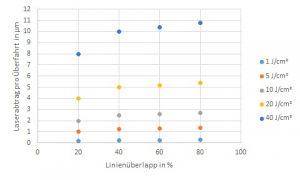
Abbildung 1: Laserabtrag bei einer vollständigen Bestrahlung der Fläche in Abhängigkeit der Fluenz (J/cm²) und dem Linienüberlapp
EINLEITUNG
Hochleistungskeramiken, wie Aluminiumoxid, Siliziumcarbid und Zirkoniumoxid sind für die Herstellung von Produkten in der Elektronikindustrie und Mechatronik fest etabliert. Verschiedene Komponenten wie z.B. Leiterplatten, Düsen, Filter und Sensoren profitieren von den spezifischen Eigenschaften, wie beispielsweise der Verschleißfestigkeit, Säurebeständigkeit, Steifigkeit und elektrischen Isolation. Da die Grün- und Weißbearbeitung nur weite Toleranzen zulassen, ist eine nachgehende Hartbearbeitung unabdingbar, sofern Geometrien mit engen Toleranzen hergestellt werden müssen. Da die mechanische Bearbeitung aufgrund der Härte und Sprödigkeit von keramischen Werkstoffen mit hohem Verschleiß am Werkzeug verbunden ist und lange Bearbeitungszeiten notwendig sind, haben sich in der Keramikverarbeitung Laserbearbeitungsverfahren etabliert.
Bei hochpräzisen Anwendungen, wie z. B. dem Erzeugen von Mikrobohrungen, der Herstellung von genau definierter Kavitäten und dem Laserabtragen bzw. Laserstrukturieren zur Erzeugung von dreidimensionalen Strukturen mit Toleranzanforderungen im µm Bereich, müssen gepulste Laser mit ultrakurzen Laserpulsen eingesetzt werden. Die extrem kurzen Pulsdauern im Piko- und Femtosekundenbereich führen zu nichtlinearen Absorptionsmechanismen und einem nahezu kalten Materialabtrag. Dadurch können dielektrische Materialien präzise verarbeitet werden und thermische Schädigungsmechanismen ausgeschlossen werden. Hierdurch können Keramiken präzise geschnitten, gebohrt und hochgenaue 3D Konturen generiert werden.
In der Studie wird der Einfluss verschiedener Laserparameter auf die Oberflächenqualität und Prozessgeschwindigkeit anhand von Aluminiumoxid (Al2O3) dargestellt. Die identifizierten Parameterregime wurden genutzt, um typische Trenn-, Bohr-, und Abtragsprozesse durchzuführen, so wie sie im industriellen Umfeld durchgeführt werden.
VERSUCHE
Die Versuche wurden an einer industriellen Laserquelle mit einer Pulsdauer von 10 ps und einer Leistung von bis zu 100 W durchgeführt. Die Strahlablenkung wurde über einen Galvoscanner realisiert, um Quadrate mit einer Kantenlänge von 50 mm x 50 mm abzutragen. Hierbei wurde ein Objektiv mit 100 mm Fokuslänge genutzt. Der Laserfokus hat einen Durchmesser von 20 µm. Um die Testquadrate abzutragen, wird die quadratische Fläche linienförmig abgescannt. Die Pulswiederholrate und die Scangeschwindigkeit wurden so eingestellt, dass sich die Laserpulse in der Bearbeitungszone jeweils zu 50 % überlappen. Die Testquadrate wurden hinsichtlich der Oberflächenrauigkeit Ra und der Abtragsrate bewertet, um optimale Laserparameter zu finden. In den Versuchen wurden die Fluenz (J/cm²), die Pulsenergie pro Fläche, und die Überlappung der Scanlinien (%) variiert.
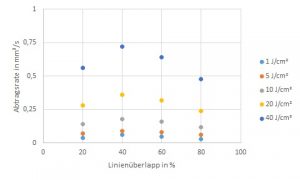
Abbildung 2: Abtragsrate in Abhängigkeit der Fluenz (J/cm²) und dem Linienüberlapp
ERGEBNISSE UND DISKUSSION
Im Folgenden werden die Ergebnisse der Versuche an Aluminiumoxidproben dargestellt. Abbildung 1 zeigt den Abtrag, der in den Testquadraten erzeugt wird, wenn die Aluminiumoberfläche lediglich einmal bestrahlt bzw. abgescannt wird. Die Ergebnisse zeigen, dass der Laserabtrag hauptsächlich von der Fluenz abhängig ist. Lediglich eine Steigerung des Linienüberlapps von 20 % auf 40 % führt zu einer Erhöhung der Tiefe. Durch die Einstellung der Fluenz, in diesem Fall die Pulsenergie, da der Laserfokus konstant bei 20 µm gehalten wurde, kann die Tiefe des Laserabtrags definiert eingestellt werden. Somit sind Strukturen mit Toleranzen im sub-µm Bereich mit dem Laserabtragsverfahren möglich.
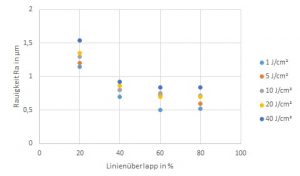
Abbildung 3: Rauigkeit in Abhängigkeit der
Fluenz (J/cm²) und dem Linienüberlapp
Abbildung 2 zeigt die sich ergebene Abtragsrate in mm³/s, als Indikator für die Prozesseffizienz. Hierbei zeigt sich analog zu Abbildung 1 der positive Einfluss der Fluenz. Zudem wird ersichtlich, dass die höchste Abtragsrate bei einem Linienüberlapp von 40 % generiert wird. Dies ist dem Umstand geschuldet, dass bei einem höheren Linienüberlapp mehr Zeit notwendig ist, um die Fläche abzuscannen, aber gleichzeitig der Laserabtrag bei höherem Linienüberlapp nicht ansteigt (vgl. Abbildung 1).
In Abbildung 3 ist der Einfluss der Laserparameter auf die Rauigkeit der Oberfläche als Indikator für die Oberflächenqualität dargestellt. In den Experimenten hat sich gezeigt, dass bei einem Linienüberlapp von 60 % die geringste Rauigkeit erzielt werden kann. Durch Erhöhung des Linienüberlapps auf 80 % kommt es zu keiner weiteren Reduktion der Oberflächenrauigkeit. Zudem zeigt sich, dass geringe Fluenzen zu niedrigeren Oberflächenrauigkeiten führen.
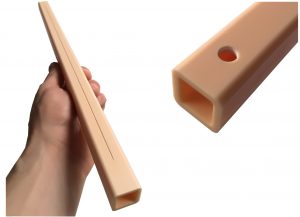
Abbildung 4: Keramikvierkantrohr (Stärke 4 mm) mit einem per Laserabtragen eingebrachten Schlitz mit 0,3 mm Breite und zwei Bohrungen mit Durchmesser 4 mm.
Zusammenfassend kann festgehalten werden, dass in dem vorliegenden Fall ein Linienüberlapp von 60 % ein guter Tradeoff zwischen Oberflächenqualität und Durchsatz besteht. Sollte die Erhöhung der Abtragsrate notwendig sein, empfiehlt sich eine Reduzierung des Linienüberlapps zu 40%, welches aber gleichzeitig die Oberflächenrauigkeit erhöht. Liegen in diesem Fall auch höhere Ansprüche an die Oberflächenqualität vor, könnte eine finale Bearbeitung mit Parametern genutzt werden, die geringere Oberflächenrauigkeiten generieren.
BEISPIELAPPLIKATIONEN
Nachdem in dem letzten Abschnitt fundamentale Zusammenhänge in der Lasermaterialbearbeitung von technischen Keramiken dargestellt wurden, werden im Folgenden einige Beispielapplikationen gezeigt. Abbildung 4 zeigt ein Keramikvierkantrohr mit einer Wandstärke von 4 mm und einer Länge von 400 mm. In das Keramikvierkantrohr wurden zwei Bohrungen mit einem Durchmesser von 4 mm und ein Schlitz mit einer definierten Breite von 0,3 mm eingebracht. Im Gegensatz zum konventionellen Laser- oder Wasserstrahlschneiden wurde der Schlitz über das schichtweise Laserabtragen generiert. Nur so kann die definierte Breite generiert werden und gleichzeitig ein minimaler Wärmeeintrag sichergestellt werden. Bei zu hohem Wärmeeintrag würde es zu deutlicher Rissbildung und Bruch des Rohrs kommen.

Abbildung 5: Per Laserabtragen hergestellte 3D-Oberflächen in Aluminiumoxid: Links: Treppenstufen im Wolkendesign; Mitte: Lasergravur in Keramikdüse, Rechts: Kegelstrukturen eines Werkzeuges
Abbildung 5 zeigt auf der linken Seite einen schichtweisen und treppenstufenartigen Laserabtrag einer Aluminiumoxidkeramik. Hierbei sollte exemplarisch eine Wolke (das Logo der photonicfab) abgetragen werden. In der Mitte ist eine Lasergravur in eine Keramikdüse dargestellt. Auch hier wurde wieder das Wolkendesign angewendet. Auf der rechten Seite sind kegelförmige Strukturen dargestellt, die durch Abtragen in die Oberfläche eingebracht wurden. Die laserstrukturierte Oberfläche wird für ein Werkzeug genutzt. Diese Strukturen könnten mit anderen Bearbeitungsverfahren nur unter sehr großem Aufwand hergestellt werden.
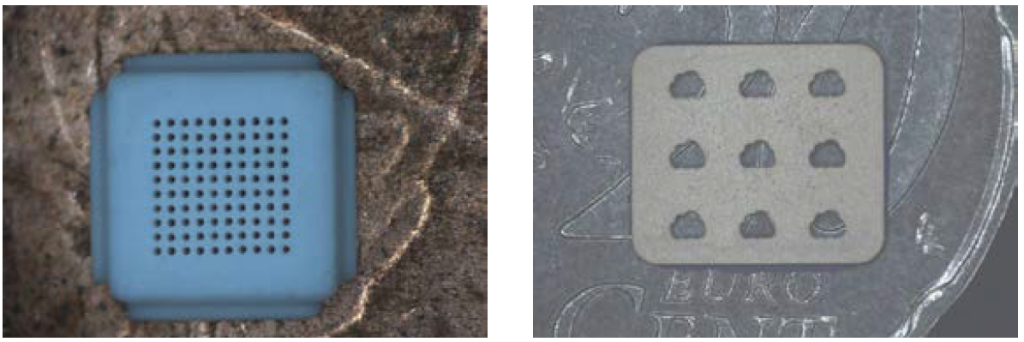
Abbildung 6: Laserbohren in Keramik: Links: Mikrobohrungen mit 100 µm Bohrdurchmesser in Aluminiumoxid; Rechts: Freiformbohrungen in Zirkoniumoxid. Hintergrund Cent Geldstück
In Abbildung 6 sind Laserbohrungen in Keramikplättchen mit einer Dicke von 0,5 mm dargestellt. In dem Bild auf der linken Seite wurden kreisrunde Mikrobohrungen mit einem Durchmesser von 100 µm in Aluminiumoxid gebohrt. Auf der rechten Seite wurden Bohrungen mit freigewählten Bohrgeoemtrie (Logo der photonicfab) in Zirkoniumoxid eingebracht. Um die Größenverhältnisse darzustellen, wurden die Muster auf einem Centstück platziert.
Derartige Bohrungen werden in der Elektronikindustrie für Sensoren genutzt, um vertikale Verbindungen durch die elektrisch isolierende Keramik zu generieren.
ZUSAMMENFASSUNG
In dem Beitrag wurde der Einfluss von ausgewählten Laserparametern eines Pikosekundenlasers auf die Bearbeitung von technischen Keramiken gezeigt, um den Leser einen Eindruck zu verschaffen, mit welcher Qualität und Geschwindigkeit technische Keramiken bearbeitet werden können. Zudem wurden ausgewählte Applikationen aus dem industriellen Alltag aufgezeigt.
Autor:
Carl Gehrmann,
photonicfab
https://photonicfab.de