Motivation und Zielsetzung
Leichtbau ist Gegenstand der Forschung mit dem Ziel eines verantwortungsvollen Umgangs mit Ressourcen. Hierbei sind Gewichts-, aber auch Materialeinsparungen als Vorteile zu nennen. Bei auftretender Biegebeanspruchung werden diese Vorteile wirkungsvoll durch den Einsatz von Sandwichstrukturen umgesetzt. Sandwichstrukturen erhalten ihre hohe gewichtsspezifische Biegesteifigkeit, indem dehnsteife Materialien in den hochbelasteten Außenschichten der Struktur angeordnet werden. Der für ein hohes Biegewiderstandsmoment nötige Abstand der Deckbleche kann durch Abstandshalter oder Füllstoffe erreicht werden. Bei der vorliegenden Sandwichstruktur (Abbildung 1 a) wird der Deckschichtabstand durch kragengezogene Verbindungselemente (Abbildung 1 b) eingestellt. Mit der vorliegenden Bauweise kann ohne zusätzlichen Werkstoff die ertragbare Maximalkraft im 3-Punkt-Biegeversuch mehr als verdoppelt werden.
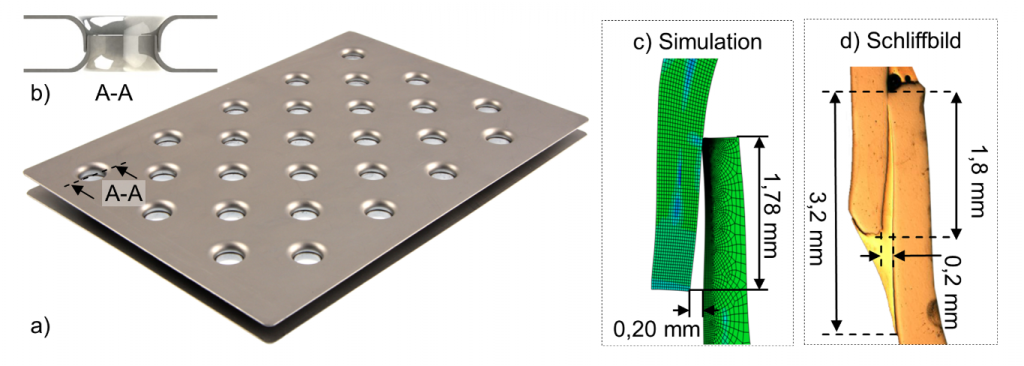
Abbildung 1: a) Isometrische Ansicht der Sandwichstruktur, b) Schnittansicht durch eine Kragenverbindung, c) Ergebnis der Simulation des Kragenziehens sowie der Kragenverbindung, d) Schliffbild einer Kragenverbindung
Prozessbeschreibung
Der Herstellungsprozess der Sandwichstruktur untergliedert sich in fünf Arbeitsschritte. Er beginnt mit der Vorlochherstellung. Beide Deckbleche weisen das gleiche Lochbild auf. Als Folgeschritt werden aus den Vorlöchern Kragen gezogen. Diese weisen, spezifisch für oberes und unteres Deckblech, einen unterschiedlichen Durchmesser auf. So können in einem weiteren Arbeitsschritt, nach dem Ausrichten beider Bleche zueinander, die Kragen ineinander gefügt werden (Abbildung 1 b). Als letzter Schritt wird ein Lotformling in die Kragenverbindung eingelegt. Der Lotformling und die Fügestelle können durch unterschiedliche Verfahren erwärmt und so die Lötverbindung hergestellt werden. Im Rahmen des Projektes wird die Lötverbindung unter anderem durch das Induktionslöten und das Ofenlöten herstellt.
Lötgerechte Auslegung des Kragenziehens
Das Kragenziehen ist in der VDI Richtlinie 3359 als „Fertigungsverfahren zur Herstellung von Blechdurchzügen durch Zugdruckumformen mit Stempel und Ziehring zum Aufstellen von geschlossenen Rändern an ausgeschnittenen Öffnungen“ beschrieben [1]. Dabei dringt der Stempel in ein durch Bohren hergestelltes Vorloch ein und weitet dieses auf den Zieldurchmesser auf. Durch das Aufweiten des Vorlochs nimmt die Blechdicke mit zunehmender Kragenhöhe ab. Als prozessbeschreibende Größe wird das Aufweitverhältnis verwendet [1]. Dies beschreibt den Quotienten von Kragendurchmesser zu Vorlochdurchmesser. Als Werkstoff kommt DC01 der Blechdicke 0,88 mm zum Einsatz. Die Vorlöcher werden gebohrt und ermöglichen auf diese Weise ein größeres Grenzziehverhältnis als durch Stanzen, da eine geringere Materialbeeinflussung vorliegt. In dem vorliegenden Fall können Aufweitverhältnisse bis zu 3,8 erreicht werden.
Die für Untersuchungszwecke hergestellte Sandwichstruktur weist einen Deckschichtabstand von 10 mm auf. Der Abstand der Deckschichten ist durch Kragen möglichst kleinen Durchmessers realisiert, um das Sandwich für eine breite Nutzung zu qualifizieren. Aus dem Ineinanderstecken der Kragen resultiert eine Überlappung von oberem und unterem Deckblech. Diese Überlappung dient als Verbindungsfläche zwischen oberem und unterem Deckblech. Die eingesetzte Lötverbindung soll mindestens die Werkstofffestigkeit der Deckbleche aufweisen. Rechnerisch reicht eine Überlappungslänge in Höhe der Blechdicke aus, um die geforderte Tragfähigkeit zu erreichen. Um sicherzustellen, dass die Tragfähigkeit ausreichend hoch ist, wird die doppelte Blechdicke (1,76 mm) als Überlappung angestrebt. Ein weiteres Ziel ist es, eine lötgerechte Fügestelle zu erhalten (Abbildung 1 c)). Lötgerecht bedeutet in diesem Sinne, dass der Lötspalt maximal 0,2 mm betragen darf. Auf diese Weise reicht der kapillare Fülldruck aus, um beim Einsatz von Flussmittel eine vollständige Spaltfüllung zu erreichen [2, S. 66]. Gelötet wird, wie vorangehend beschrieben, mit eingelegten Lotformlingen. Als Lot wird zu Versuchszwecken aufgrund der niedrigen Schmelztemperatur Ag 155 (DIN EN ISO 17672:2010) verwendet. Des Weiteren muss der verwendete Lotformling vollständig am Lötspalt anliegen, damit sich der kapillare Druck aufbauen kann. Der Lötspalt sollte parallel verlaufen oder verengend gestaltet werden, um eine vollständige Füllung zu erreichen. Einfache geometrische Größen, wie die Kragenhöhe können in Grenzen durch empirische Gleichungen bestimmt werden. Genaue geometrische Aussagen bzgl. des Lötspalts können auf diese Weise aber nicht getroffen werden. Aus diesem Grund wurde für die Auslegung des Lötspalts auf eine Finite-Elemente Berechnung zurückgegriffen. Das Ergebnis der Auslegung der FE-Berechnung mit den oben beschriebenen Zielen ist in Abbildung 1 c in einem axialsymmetrischen Schnitt dargestellt. Für die Fügestelle wurden zwei Kragenziehprozesse und Kragengeometrien ausgelegt. Der Ziehspalt, der sich zwischen Stempel und Matrize befindet, beträgt 80 Prozent der Blechdicke. Auf diese Weise wird das Blech zusätzlich zum Kragenziehen abgestreckt und der Kragen erhält einen größeren zylindrischen Anteil. Des Weiteren wurde der Durchmesser des äußeren Kragens variiert, um eine Fügelänge von etwa 1,76 mm zu erreichen. Die Fügelänge wurde anhand einer den einzelnen Kragenziehprozessen nachgelagerten Simulation des mechanischen Fügevorgangs ermittelt. Der innere Kragen ist hierbei fixiert. Der zweite äußere Kragen wird auf den inneren Kragen axial aufgeschoben. Als Zielgrößen wurden der Deckschichtabstand und die Fügekraft untersucht. Durch die Abbildung des Fügevorgangs konnte der resultierende Lötspalt ausgewertet werden (Abbildung 1 c).
Bei dem Einsatz von Flussmittel muss das Lot das Flussmittel aus dem Lötspalt verdrängen. Um dies zu unterstützen, wird zwischen innerem und äußerem Kragen ein punktueller Pressverband erzeugt. Dieser Pressverband fixiert das obere und untere Deckblech zueinander und gibt für das Flussmittel über dem Umfang Spalte in dem Bereich, in dem der äußere auf dem inneren Kragen sitzt, frei. Auf diese Weise kann durch die Vorfixierung der Struktur das Flussmittel aus dem Spalt verdrängt werden und zusätzlich eine verbesserte Handhabung der Struktur, durch eine für diesen Zweck ausreichende Stabilität, gewährleistet werden (Abbildung 1 d).
Zum Löten der kragengezogenen Verbindungselemente kommt unter anderem das Induktionslöten zum Einsatz. Zu diesem Zweck wird ein Induktor im Inneren der Verbindung positioniert. Der Induktor erwärmt durch ein alternierendes magnetisches Außenfeld die Fügestelle und erstellt die Lötverbindung. Durch den Einsatz eines Induktors kommt es im Vergleich zum Ofenlöten zu einer lokalen Erwärmung der Sandwichstruktur. Demzufolge liegt eine geringe Wärmebeeinflussung des Gefüges der zu fügenden Kragen vor.
Fazit und Ausblick
Durch eine FE unterstützte Auslegung der Verbindungsstelle, kann eine dem Lötprozess gerechte Auslegung des Kragenziehprozesses durchgeführt werden. Die Kragenziehprozesse erzeugen Kragen mit Formen, die mit Hilfe von Lotformlingen verlötet werden können. Die Übereinstimmung der Auslegung gegenüber der Auswertung der Schliffbilder, sind in Abbildung 1 c und d dargestellt. In der 3-Punkt-Biegeprüfung konnte der Nachweis für die gewünschte Festigkeit erbracht werden.
Bei der 3-Punkt-Biegeprüfung kommt es zu einem strukturellen Versagen der Sandwichstruktur, wobei die Lötverbindungen trotz Ovalisierung keine augenscheinliche Schädigung aufweisen. Die Ovalisierung ist eine Folge der Biegebeanspruchung. Die Biegebeanspruchung führt zu einer einseitigen Längung der Sandwichstruktur zwischen den Auflagern. Die Kragenverbindungen stellen hoch steife Bereiche der Sandwichstruktur dar und eignen sich besonders für die Krafteinleitung. Im Gegensatz hierzu stehen die Zwischenbereiche zwischen den Kragenverbindungen. Bei der geprüften Biegebeanspruchung stellt sich in diesen Bereichen die größte Verformung ein. Die Kragenverbindung ermöglicht eine punktuelle Verbindung der beiden Deckschichten. Die Anordnung der Kragenverbindungen ermöglicht eine auf den Belastungsfall optimierte Struktur.
Im Vergleich zu der Biegeprüfung zweier fest verbundener Deckschichten kann die Steifigkeit um den Faktor 4,4 sowie die ertragbare Maximalkraft verdoppelt werden. Als weitere Fügemöglichkeit wird die Herstellung eines Pressverbands zwischen den einzelnen Kragen einer Verbindung als Alternative zur Lötverbindung untersucht. Diese Möglichkeit bietet eine vielversprechende Alternative aufgrund des geringeren Vor- und Nachbereitungsaufwands.
Danksagung
Das IGF-Vorhaben 17933N der Forschungsvereinigung Europäischen Forschungsgesellschaft für Blechverarbeitung e.V. wurde über die AiF im Rahmen des Programms zur Förderung der Industriellen Gemeinschaftsforschung (IGF) vom Bundesministerium für Wirtschaft und Energie aufgrund eines Beschlusses des Deutschen Bundestages gefördert.
Für die Unterstützung im Rahmen des Projektes dankt das PtU der Arbeitsgemeinschaft industrieller Forschungsvereinigungen „Otto von Guericke“ e.V. (AiF), der Europäischen Forschungsgesellschaft für Blechverarbeitung e.V. und den nachstehenden Projektpartnern: Graepel Seehausen GmbH und Co. KG, Haulick & Roos GmbH, Innobraze GmbH, KGW GmbH & Co. KG, Simufact Engineering GmbH und TOX PRESSOTECHNIK GmbH & Co. KG.
Technische Universität Darmstadt
Institut für Produktionstechnik und Umformmaschinen (PtU)
Otto-Berndt-Straße 2, 64287 Darmstadt
Tel. +49 6151-16-3056
Fax +49 6151-16-3021
E-Mail: mann@ptu.tu-darmstadt.de
Internet: http://www.ptu.tu-darmstadt.de
Fachartikel zum Thema Verbindungstechnik aus Werkstoffe in der Fertigung 5/2015
Literatur
[1] VDI, VDI-Richtlinie -VDI3359 – Kragenziehen, Blechdurchzüge.
[2] H.-J. Peter, Induktionslöten: Grundlagen, Anlagentechnik, Induktoraufbau, effektive Löttechnologien ; mit 11 Tabellen. Renningen: expert, 2011.