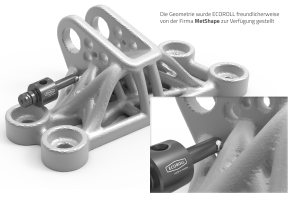
Bild 1: Nacharbeitung eines additiv gefertigten Strukturbauteils durch Festwalzen
Im Trendradar scheint sich der Hype um die additive Fertigung aktuell etwas abzuschwächen, und es kristallisieren sich immer mehr die wirklichen Use-cases heraus. Eine wesentliche Herausforderung besteht allerdings noch immer in der optimierten Konstruktion von Bauteilen. Denn natürlich ist die additive Fertigung aktuell den klassischen Fertigungsprozessen hinsichtlich der Effizienz unterlegen. Die Materialeigenschaft ist hier eine entscheidende Größe und heute noch nicht vollständig überprüfbar. Die Frage ist, wie groß ist die Festigkeit eines additiv gefertigten Bauteils im Vergleich zum herkömmlichen Werkstoff?
Für die additive Fertigung (AM) ergibt sich dabei eine sehr konkrete Aufgabe: Die Prozessparameter müssen so ausgewählt werden, dass das Gefüge möglichst vergleichbar ist und keine Schwachstellen oder belastungsabhängige Vorzugsorientierungen hat.
Im Bereich der additiven Fertigung im Pulverbettverfahren ist vor allem die relative Dichte des Werkstoffs ein wichtiger Faktor, der insbesondere die dynamische Festigkeit beeinflusst. Poren und Fehlstellen entstehen durch Unregelmäßigkeiten im Prozess und sind gerade in den hochbeanspruchten Randbereichen des Bauteils zu vermeiden.
In der Prozessauslegung ist nun der Anwendungstechniker gefragt, Parameter so lange zu verändern, bis eine möglichst hohe Dichte erreicht wird. Diese Suche nach der optimalen Konfiguration gestaltet sich in der Praxis allerdings als eher langwieriger Prozess.
In der klassischen Fertigung hingegen sind die Verfahren der mechanischen Oberflächenbearbeitung bekannt. Hierzu zählen das Kugelstrahlen oder das Festwalzen. Das Ziel dieser Verfahren ist es, die Oberflächen- und Randzoneneigenschaften des Werkstoffs so anzupassen, dass die Performance des Bauteils deutlich gesteigert werden kann.
Beim Festwalzen wird ein Walzkörper mit einer definierten Walzkraft in die Oberfläche gepresst, auf der er abrollt. Durch eine kleine Kontaktfläche zwischen Walzkörper und Oberfläche wird mit moderaten Walzkräften auf herkömmlichen CNC-Maschinen eine lokale Umformung des Werkstoffs erreicht. Dabei entstehen starke Druckeigenspannungen und Kaltverfestigungen, wodurch die Härte und dynamische Festigkeit des Bauteils gesteigert werden.
Insbesondere das Einbringen von Druckeigenspannungen führt bei einer dynamischen Belastung dazu, dass die Lebensdauer eines Bauteils steigt. Dieser Effekt ist besonders im Bereich der Dauerfestigkeit zu beobachten.
Ob und wie stark dieser Effekt auch bei der additiven Fertigung eintritt, ist aktuell Teil unterschiedlicher Forschungsprojekte, an denen sich die ECOROLL AG Werkzeugtechnik beteiligt. So wurde beispielsweise im Projekt „Antriebsstrang 2025“, gefördert durch das Bundesministerium für Wirtschaft und Klimaschutz (BMWK), der Effekt des Festwalzens auf die Biegeumlaufbelastung von additiven Bauteilen untersucht. Hierbei stand der Wire-Arc Additive Manufacturing Process (WAAM) im Fokus der Untersuchungen. Die additiv gefertigten Proben aus AlSi10Mg konnten hier durch eine Wärmebehandlung und anschließende Festwalzbearbeitung gegenüber der rein wärmebehandelten Probe um den Faktor 4 länger belastet werden.
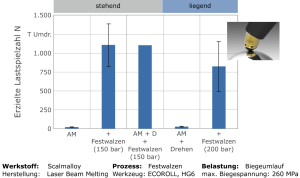
Bild 2: Lebensdauersteigerung durch Festwalzen bei additiv gefertigten Werkstoffen.
Im Bereich des selektiven Laserschmelzens wurden bei der ECOROLL AG vor einiger Zeit bereits Untersuchungen an dem aus der Luftfahrt stammenden Werkstoff Scalmaloy durchgeführt. Hier wurden ebenfalls Biegeumlaufproben additiv hergestellt und anschließend spanend nachbearbeitet. Ohne eine mechanische Nachbearbeitung konnte in diesem Fall lediglich eine sehr geringe Lebensdauer von ca. 25.000 Lastzyklen erreicht werden. Eine nachträgliche Festwalzbearbeitung mit einem hydrostatischen Festwalzwerkzeug hat zu einer signifikanten Steigerung auf über 1 Mio. Lastwechsel geführt. Das bedeutet einen Anstieg um den Faktor 40.
Die Analyse der Bauteile zeigt, dass der AM-Prozess nicht optimal war. Die sehr geringe Festigkeit ist auf eine große Porenanzahl zurückzuführen. Die nachträgliche Festwalzbearbeitung kann die Poren zwar nicht schließen. Allerdings werden sie im hochbelasteten Randbereich in ihrer Ausdehnung verkleinert und unterschreiten eine kritische Größe. Die zusätzlich eingebrachten Druckeigenspannungen sorgen außerdem für ein langsameres Risswachstum.
Daraus ergibt sich die Hypothese, dass das Festwalzen die Produktivität des AM-Prozesses steigern kann, da schlicht die Prozessparameter maximiert werden können. Der AM-Prozess kann also „schlecht“ sein, und trotzdem wird eine ausreichende Betriebsfestigkeit erreicht. Um genau diese Frage zu klären, beteiligt sich ECOROLL aktuell an unterschiedlichen Projekten zur mechanischen Nachbearbeitung von AM-Bauteilen, z. B. mit dem Fraunhofer IWM in Freiburg, wo es auch um die Möglichkeiten und Grenzen der Zugänglichkeit geht; was offensichtlich nicht trivial ist, wie man in Bild 1 erkennen kann.
Weitere Informationen: