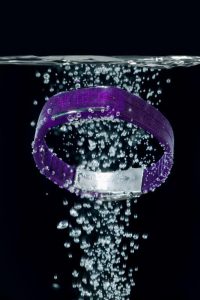
Bild 1: Korrosive Medien können im Laufe der Zeit über die Grenzfläche eines Hybrid-Bauteils eindringen und zu dessen Schädigung oder gar Delamination führen
Bild: Plasmatreat
Die Grenzfläche zwischen Kunststoff und Metall ist ein Risikofaktor, der Spritzgussherstellern bei der Produktion von Hybridbauteilen immer wieder Kopfzerbrechen bereitet. Insbesondere korrosive Medien können im Laufe der Zeit über
die Grenzfläche in das Bauteil eindringen und zu dessen Schädigung oder gar Delamination führen (Bild 1). Die Praxis
zeigt, dass auch ein ursprünglich dichter Verbundspritzguss nach einiger Zeit undicht werden kann und in Folge sein
Zusammenhalt und die Funktion der Bauteile nicht mehr gegeben sind. Das vorzeitige Haftungsversagen beruht in vielen
Fällen auf einer Feuchtigkeitsaufnahme in Kombination mit Sauerstoff, die eine Unterwanderung der Grenzfläche mit sich bringt.
Für dieses Problem eine sichere Industrielösung zu finden, war das Ziel der Systempartner Plasmatreat und Akro-Plastik. Dem Plasmaspezialisten und dem Kunststoffhersteller gelang es nach zweijähriger Forschungsarbeit, ein Verfahren mit dem Namen Plasma-SealTight zu entwickeln, bei dem die Zusammensetzung einer im Atmosphärendruck erzeugten plasmapolymeren anti-korrosiv wirkenden Schicht, die Rezeptur der Kunststoff-Compounds und die Prozessparameter so aufeinander abgestimmt wurden, dass ein langzeitstabiler mediendichter Verbund des Spritzgussbauteils entsteht.
Plasmabeschichtung ohne Vakuum
Die PlasmaPlus-Düsentechnologie, die als Basis für dieses neue Versiegelungsverfahren dient, wurde vor rund zehn Jahren von Plasmatreat und dem Fraunhofer-Institut für Fertigungstechnik und Angewandte Materialforschung IFAM, Bremen, entwickelt. Basierend auf der von dem Plasmaunternehmen bereits 1995 entwickelten Openair-Plasma-Düsentechnik zur Feinstreinigung und Aktivierung von Materialoberflächen, können mit ihr funktionale Dünnschichten anstatt im Niederdruck, d.h. in einer separaten und kostenaufwendigen Vakuumkammer, unter Atmosphärendruck und
damit unter ganz normalen Produktionsbedingungen inline oder extern erzeugt werden. Das Verfahren ist prozesssicher
und hundertprozentig reproduzierbar. Der trockene, umweltfreundliche Prozess ersetzt die bei der Hybrid- Spritzgießen
häufig angewandten Reinigungs- und Primerverfahren. Arbeitsschritte wie Zwischenlagerung oder Trocknungsprozesse
entfallen komplett, die Bauteile können sofort nach ihrer Beschichtung weiterverarbeitet werden.
Mehrfachfunktion
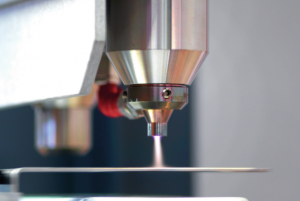
Bild 2: Mit dem chemisch-physikalischen Plasma-SealTight-Verfahren lassen sich in Millisekunden funktionelle Nanoschichten ortsselektiv abscheiden und in Folge stoffschlüssige Verbindungen unterschiedlicher Materialien erzeugen. Bild: Plasmatreat
Von den chemischen Eigenschaften einer Grenzflächenschicht zwischen zwei ungleichen Materialien wird verlangt, dass
sie eine simultane Verbindung zwischen den unterschiedlichen Stoffen herstellen. PlasmaPlus ist ein chemisch-physikalisches Verfahren, das durch Schichtabscheidung im Atmosphärendruck-Plasma die stoffschlüssige Verbindung der verschiedenen Materialien bewirkt. Die Schicht verbindet sich auf molekularer Ebene mit dem Metall und gewährleistet im Verbund mit den angepassten Kunststoffcompounds eine so hohe Haftung und Dichtigkeit, dass sie gleichzeitig die Funktion einer Antikorrosionsschicht übernimmt.
Zur Erzeugung einer Schicht wird dem Plasma ein Präkursor in Form einer siliziumorganischen Verbindung beigemischt.
Durch die hochenergetische Anregung im Plasma wird diese Verbindung fragmentiert und scheidet sich auf einer Oberfläche als glasartige Schicht ab. Die chemische Zusammensetzung kann je nach Anwendungsfall variiert werden, um
auf den unterschiedlichen Materialien die jeweils besten Funktionalisierungsresultate zu erzielen. Ein weiterer Vorteil
des Prozesses ist seine hohe Flexibilität. Insbesondere die Schichtstärke und die Prozessgeschwindigkeit können genau
auf eine bestimmte Korrosionsschutzwirkung abgestimmt werden. Gegenüber anderen Beschichtungstechniken liegt ein
ganz besondere Vorteil des Verfahrens zweifellos darin, dass die Schichtabscheidung aufgrund der Düsentechnik ortsselektiv, d.h. im Millimeterbereich und an genau definierter Stelle, erfolgen kann und das bei sehr hoher Geschwindigkeit (Bild 2). Während hier eine 100nm dünne Schichtdecke in Millisekunden abgeschieden wird, dauert es beispielsweise beim Niederdruckplasma (Vakuumkammer) etwa ein bis zwei Minuten und eine Ortsselektion ist nicht möglich. Durch die Entwicklung neuer Präkursoren und die umfangreiche Anpassung der Plasmaparameter gelang Plasmatreat beim Plasma-SealTight-Verfahren der gezielte Einbau von gleichzeitig mehreren Funktionen in einer Schicht. Zu diesen Funktionen gehören die gute Bindung an die Metalloberfläche, eine erhöhte Korrosionsbeständigkeit, die Wirkung als Medien- und Oxidationsbarriere sowie die haftvermittelnde Eigenschaften für Kunststoffe durch funktionelle chemische Gruppen. Während das in der Schicht enthaltene Silizium für die Haftung am Metall bzw. Metalloxid sorgt, ist Siliziumoxid für die Barrierewirkung und Mediendichtigkeit verantwortlich. Die organischen Anteile in der Schicht (funktionelle Gruppen) bewirken die Haftung an das Polymer.
Kunststoff-Rezepte
Bei der Rezeptur ihrer Kunststoffe haben die Hersteller viele vom Kunden verlangte Eigenschaften des späteren Produkts zu berücksichtigen – mechanische, elektrische, thermische und chemische, das Brandverhalten des Kunststoffs und seine allgemeinen Eigenschaften wie Dichte und Feuchtigkeitsaufnahme. Die jeweilige Modifizierung der Kunststoffmatrix erfolgt durch eine Additivierung sowie die Zugabe von Füll- und Verstärkungsstoffen. Erst diese Rezepturbestandteile machen aus dem Basiskunststoff einen anwendungsspezifischen Kunststoff-Compound. Die Sicherstellung einer konstanten Produktqualität und damit der Funktion der späteren Bauteile setzt beim Hersteller eine hohe Präzision und Reproduzierbarkeit des Compoundierprozesses voraus. Akro-Plastic, auf komplexe, individuelle
Anpassungen von Kunststoffeigenschaften spezialisiert und aufgrund einer im eigenen Hause entwickelten Compoundiertechnologie in der Lage, die vorgenannten Voraussetzungen in punkto Funktionserhaltung und Qualität
unabhängig vom Produktionsstandort international zu erfüllen, hatte im Projekt die Aufgabe übernommen, ein Compound mit gezielten Eigenschaften herzustellen. Die chemische Rezeptur musste bei dem neuen Verfahren vor allem zwei Aspekte berücksichtigen, den unterschiedlichen Längenausdehnungskoeffizienten von Kunststoff und Metall
auf der einen und den chemisch-physikalischen Haftverbund mit der plasmapolymeren Schicht auf der anderen Seite.
Starke Haftung
Für das Basis-Compound in der Testphase konzentrierte man sich auf einen glasfaserverstärkten Kunststoff des
Typs PA6 GF30, der entsprechend dem Testverlauf modifiziert wurde. Getestet wurden bislang rund 3500 Prüfkörper
mit verschiedenen Metallen und modifizierten Kunststoff-Compounds, wobei die Plasmaschicht ständig – sowohl in Hin-
blick auf Haftung wie gleichzeitig auch auf den Schutz vor korrosiven Medien – optimiert wurde. Zum gewünschten kohäsiven Bruch des Kunststoffs kam es bei den Metallen Stahl, Edelstahl, poliertem Edelstahl und poliertem Kupfer. Die erreichten Zugscherfestigkeiten lagen hier in einem hohen Bereich (Bild 3). Bei Aluminium und galvanisiertem Stahl
erfolgte ein Mischbruch. Ein kohäsiver Bruch im Kunststoff wurde auch bei anderen Kombinationen, wie Stahl und
Edelstahl, jeweils angespritzt mit den Thermoplasten PA66 GF30, PA6 GF50, PA66+PA6 GF30 und PBT GF 30, erreicht.
Durchgeführte Auslagerungstests zeigten ebenfalls gute Festigkeiten.
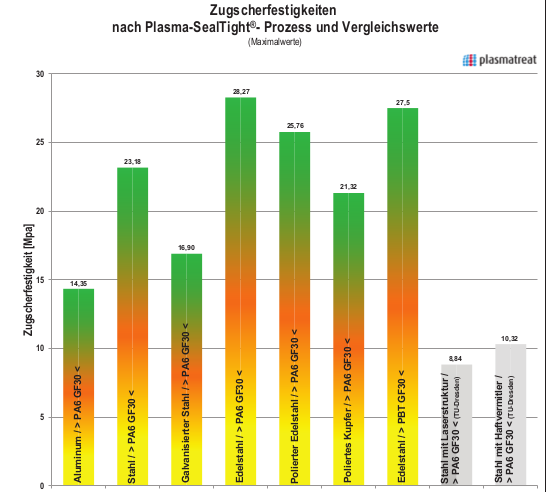
Bild 3: Im Vergleich: Die erreichten maximalen Zugscherfestigkeiten der Plasma-SealTight-Verbunde liegen weit über den Höchstwerten der mit einem Haftvermittler beschichten bzw. laserstrukturierten Prüfkörper. Bild: Plasmatreat
Mediendicht
Werden Materialien nicht stoffgebunden gefügt, so kann Wasser leicht in die Grenzfläche eindringen und sich auf der Materialoberfläche ausdehnen. Die Plasma-Versiegelung verhindert diesen Effekt, indem die Schicht mikroskopisch
kleine Hohlräume fein wie ein Nebel ausfüllt und sich korrosionsschützend mit der Metalloberfläche verbindet (Bild 4).
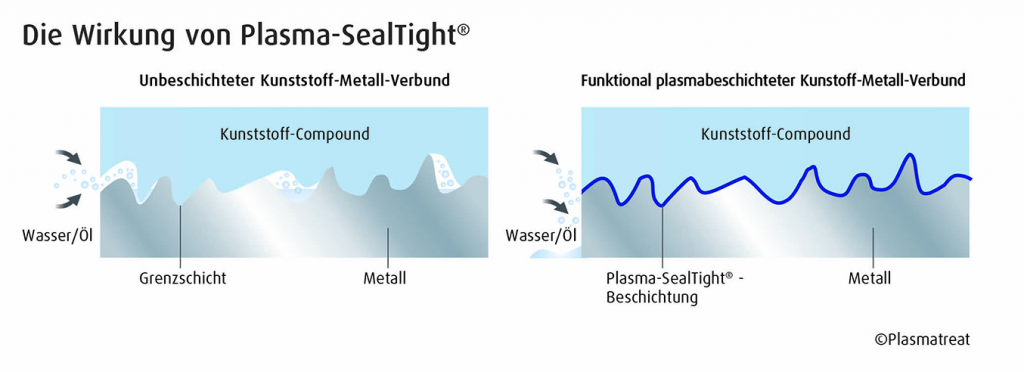
Bild 4: Dringt Wasser in die Grenzfläche des Kunststoff-Metall-Verbunds, kann es zu Korrosion, zum Versagen der Bauteilfunktion oder gar zu einer Delamination kommen (links). Die plasmapolymere Schicht (rechts) füllt dagegen alle Hohlräume und bietet dem Wasser keine Möglichkeit, in die Grenz- fläche vorzudringen. Die stoffschlüssige Verbindung wirkt somit korrosionsschützend.Bild: Plasmatreat
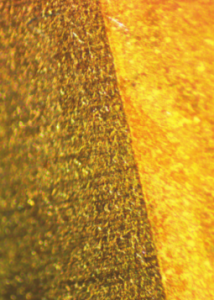
Bild 5: Die mikroskopische Aufnahme zeigt eine
deutliche Trennlinie zwischen der plasmabe-
schichteten, korrosionsfreien Metallfläche (links)
und dem unbeschichteten, korrodierten Bereich
(rechts) Bild: Plasmatreat
Ziel der bislang durchgeführten Versuche zur Mediendichtigkeit und Korrosionswiderstandsfähigkeit war zu erfahren,
inwieweit die erlangte Verbundfestigkeit durch Auslagerungstests geschwächt wird. Bei den plasmabeschichteten Metallen konnte nachgewiesen werden, dass die Schicht eine Barriere gegen Wasser, Salzlösungen und Gase bildet
und keine Unterwanderung durch diese Medien stattfindet. Ein Beispiel: Ein Edelstahlprüfkörper wurde zur Hälfte
atmosphärisch plasmabeschichtet, komplett mit PA6 GF30 übergespritzt und anschließend für mehrere Wochen in ein korrosives Medium gelegt. Nach Herausnahme wurde der Kunststoff mechanisch entfernt und das Metall geprüft. Zu erkennen war eine scharfe Trennung zwischen dem unbeschichteten, nun stark korrodierten Bereich und der plasmabeschichteten korrosionsfreien Metallfläche (Bild 5). Die Forschungen zur Öldichtigkeit und zu weiteren Medien sind derzeit noch im Gange, jedoch haben Vorversuche bereits gute Ergebnisse gezeigt.
Maschinelle Umsetzung
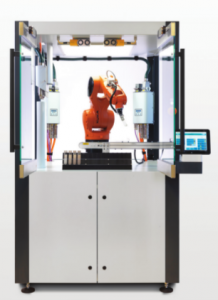
Bild 6: Die schlüsselfertige, vollautomatische Plasmazelle PTU1200 beinhaltet alles, was der Plasmaprozess verlangt und kann an jede han- delsübliche Spritzgussmaschine angeschlossen werden. Bild: Plasmatreat
Bei der maschinellen Umsetzung des Beschichtungsverfahrens standen für das Plasmaunternehmen die Kompaktheit
des Multi-Komponenten-Vorbehandlungssystems und seine einfache Integration in eine kontinuierliche Fertigungslinie an erster Stelle. Mit der Entwicklung der schlüsselfertigen, vollautomatischen Plasmazelle PTU1200 (Bild 6), die erstmals bei der K 2016 vorgestellt wurde, hat das Unternehmen sein Ziel erreicht. Die Zelle kann an jede handelsübliche Spritzguss maschine angepasst werden. Mit ihr wird nicht nur ein besonders schneller, sondern auch kontinuierlicher Fertigungsprozess für die Serienproduktion von Kunststoff-Metall-Bauteilen möglich. Die
Zelle beinhaltet vom Generator und Roboter, der Steuerungstechnik, einer PCU Plasma Control Unit und den Plasmajets
bis hin zu Kabeln und Verbrauchsmaterial alles, was der Prozess verlangt. Das Plasma-System selbst besteht aus zwei
getrennten Plasmadüsen. Ein Roboter – oder bei zwei kleineren Varianten ein XY-Achssystem – führt den Metalleinleger
zunächst unter die Openair-Plasmadüse, wo seine Oberfläche auf molekularer Ebene von jeglichen Kontaminationen gereinigt und damit seine ursprüngliche Fähigkeit für eine gute Benetzbarkeit wieder hergestellt wird. Im direkten Anschluss erfolgt die funktionale Beschichtung aus der zweiten Plasmadüse.
Fazit
Mit dem innovativen Beschichtungsprozess wurde eine zukunftsweisende Lösung zur Verbesserung von Kunststoff-Metall-Verbunden in der Spritzgussindustrie geschaffen. Die Systempartnerschaft der beiden Spezialisten bietet Anwendern ein besonders hohes Maß an Sicherheit bei der Erfüllung individueller Kundenanforderungen. Eine höhere Produktqualität kann lt. Angaben der Hersteller durch das neue Verfahren ebenso gewährleistet werden, wie ein sicherer, reproduzierbarer und wirtschaftlich effizienter Produktionsprozess – und dies bei völliger Verträglichkeit mit der Umwelt.
Autor:
Inès A. Melamies, facts4you.de
Kontakt:
Plasmatreat GmbH
Queller Str. 76-80
33803 Steinhagen
www.plasmatreat.de
AKRO-PLASTIC GmbH
Industriegebiet Brohltal-Ost
Im Stiefelfeld 1
56651 Niederzissen
www.akro-plastic.com