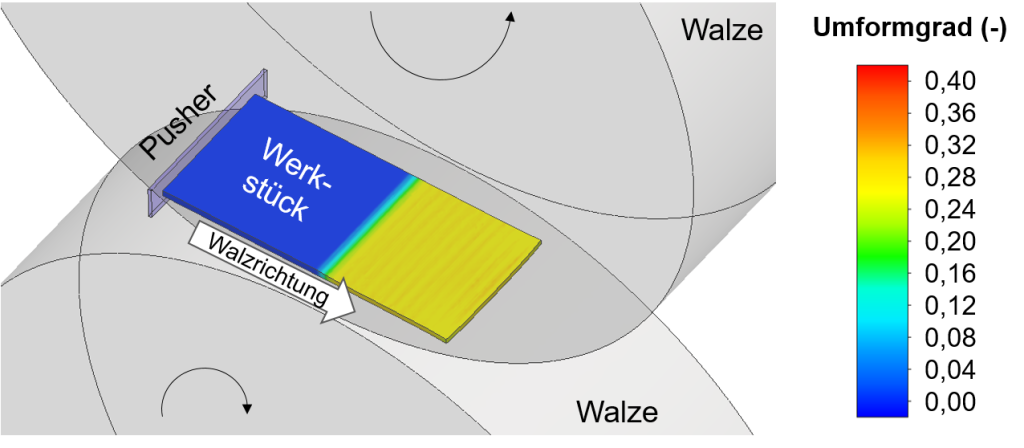
Abbildung 1: Verfahrensprinzip des Kaltwalzens und Modellaufbau in Simufact Forming V2024
Um die Lebensdauer der nicht beschichteten, metallischen Bipolarplatten von Brennstoffzellen zu erhöhen, sollte die Korrosion an kritischen Stellen möglichst langsam ablaufen. Anhand von kaltgewalzten 316L-Edelstahlproben wurden mikrostrukturelle Veränderungen der Oberflächen analysiert und durch multiple Regressionsanalysen Modellgleichungen zur Vorhersage der Korrosionsrate erstellt, die in FEM-Simulationen integrierbar sind. Diese Simulationen ermöglichen es, die Korrosionsanfälligkeit von Bauteilen vorherzusagen und gefährdete Bereiche anzupassen.
Korrosionsbeständigkeit von Bipolarplatten
Angesichts aktueller Herausforderungen in den Bereichen der Ressourceneffizienz und des Umweltschutzes rücken alternative Energieerzeugungsmethoden zunehmend in den Fokus. Eine vielversprechende Technologie in diesem Kontext ist die wasserstoffbasierte Energieversorgung durch Brennstoffzellen. Brennstoffzellen bieten ein großes Verbesserungspotenzial in Bezug auf Kosteneffizienz, Lebensdauer und Nachhaltigkeit [1]. Ein zentrales Bauteil in Brennstoffzellen ist die Bipolarplatte, von der etwa 400 Stück in einer Brennstoffzelle für einen durchschnittlichen PKW verbaut werden. Metallische Bipolarplatten sind aufgrund ihrer begrenzten Korrosionsbeständigkeit auf Beschichtungen angewiesen, die einen zusätzlichen Kostenfaktor darstellen und sich mit der Zeit abnutzen oder beschädigt werden können, was die Funktion der Brennstoffzelle beeinträchtigt [2].
Ziel der Forschung ist es, die Korrosion am Grundwerkstoff der Bipolarplatten zu verlangsamen, um einen direkten Zellausfall oder starken Leistungsverlust zu verhindern. Die durch die Korrosion in den Elektrolyten herausgelösten Metallionen adsorbieren teilweise an der Polymermembran und verringern dadurch deren Wasserstoffionenleitfähigkeit, sodass wiederum die Lebensdauer der Polymerelektrolyt-Brennstoffzelle sinkt. Aus der Literatur geht hervor, dass ein Zusammenhang zwischen Umformprozess und resultierender Korrosionsbeständigkeit besteht [3, 4]. Allerdings vernachlässigen diese Veröffentlichungen in der Regel die durch den Umformprozess verursachten lokalen mikrostrukturellen Veränderungen in den Bauteilen oder betrachten nur qualitativ die Veränderung eines ausgewählten Mikrostrukturparameters. Stattdessen wird nur das bauteilübergreifende Korrosionsverhalten untersucht und potenziell kritische Stellen, die eine besonders hohe Korrosion aufweisen, werden nicht hinreichend erfasst.
Experimentelle Untersuchung und Modellierung der Korrosionsrate
Zur Untersuchung der Korrosionsbeständigkeit wurden 2 mm dicke, kaltgewalzte Bleche (80 mm × 40 mm) des Werkstoffs 316L (EN 1.4404 – Massenanteile bestimmt durch optische Glimmentladungsspektroskopie: 0,03 % C; 17,31 % Cr; 10,55 % Ni; 2,38 % Mo; 1,14 % Mn;
0,3 % Si; 0,02 % P; <0,01 % S; 0,46 % Cu;
0,22 % Co; 0,06 % V; 0,01 % Nb; Rest Fe) unter Anwendung verschiedener Stichkombinationen in einem Duo-Reversier-Walzwerk mit einem Walzendurchmesser von 236 mm gewalzt. Im Anschluss erfolgte eine experimentelle Charakterisierung der unterschiedlichen Oberflächenzustände, um den Einfluss verschiedener mikrostruktureller Faktoren auf die Flächenkorrosion zu analysieren. Detaillierte Informationen hierzu sind bei Dittes et al. [5] zu finden. Die Charakterisierung umfasste röntgenografische Messungen der Eigenspannungen, Mikroverzerrung (als Maß für die Defektdichte) und Phasenzusammensetzung.
Für die Korrosionsversuche wurden durch Wasserstrahlschneiden kleinere Probekörper (30 mm × 20 mm) aus der Mitte der Walzprobe geschnitten, um einen nahezu homogenen Mikrostrukturzustand hinsichtlich Mikroverzerrung, Eigenspannungen und Phasenzusammensetzung zu gewährleisten. Der Zeitverlauf der Korrosionsrate wurde durch Tauchversuche in 0,5 molarer Schwefelsäure bei 30 °C über 20 Tage hinweg bestimmt.
Mithilfe der experimentellen Daten aus elf Probenzuständen konnten verschiedene Modellgleichungen zur Vorhersage der Flächenkorrosionsrate Kor∞ (für Zeit t Æ ∞) an der Oberfläche des Werkstoffs durch multiple Regressionsanalyse erstellt werden. Drei zusätzliche Probenzustände dienten der Validierung. Da bei der vorliegenden Zusammensetzung des Werkstoffs bei der Umformung Martensit gebildet wird, gilt das Modell für teilmartensitische Werkstoffzustände.
Für eine Einbindung in ein Simulationsmodell sind möglichst einfache Zusammenhänge zwischen Umformprozess, Mikrostruktur und Korrosionsrate wünschenswert. Wenn nur der Umformgrad berücksichtigt wird, weichen die Modellwerte stark von den experimentellen Werten ab (R² = 0,690). Sehr gute Übereinstimmung liefert die Einbindung der zusätzlichen Faktoren Martensitanteil (MA), Hauptspannung (σ2) der Austenitphase und Mikroverzerrung (MV) der Austenitphase. Die Vorgehensweise zur Implementierung in die FEM-Simulation wird unter Nutzung der Modellgleichung
Kor∞ = 0,0987 + 0,2916 ∙ MV – 0,0009 ∙ σ2 ∙ MV – 0,0006
∙ MA2 (1)
mit R² = 0,966 nachfolgend beschrieben[5].
Implementierung und Kalibrierung der Korrosionsmodelle in FEM-Simulationen
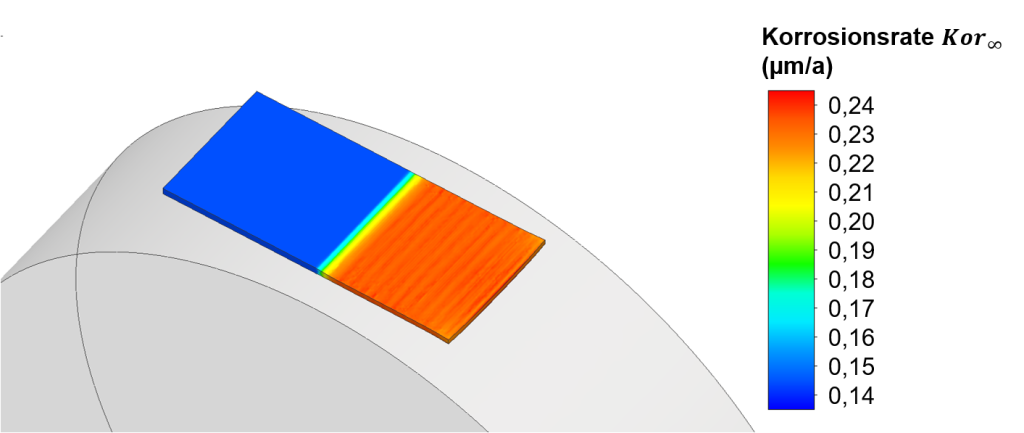
Abbildung 2: Resultierende Korrosionsrate während des Walzstiches von 2,0 mm auf 1,5 mm
Der generelle Modellaufbau zum Walzprozess mit den einzelnen Werkzeugen und der dazugehörigen Kinematik ist in Abbildung 1 dargestellt. Die entwickelten Modellgleichungen wurden in das FEM-System Simufact Forming V2024 integriert. Für eine realitätsnahe numerische Abbildung des Kaltwalzens wurden umformspezifische Fließkurven in Flachstauchversuchen ermittelt und mit dem Hockett-Sherby-Ansatz modelliert. Die Kalibrierung der Simulation erfolgte anhand der Probengeometrie, der Walzkraft, der Probentemperatur (gemessen durch Thermokamera und Thermoelemente) sowie optischer Formänderungsanalyse (ARGUS GOM). Diese detaillierte Kalibrierung ermöglichte eine gute Abbildung des realen Umformprozesses.
Die Implementierung der Korrosionsrate in die Simulation erforderte die Verknüpfung der Simulationsergebnisse (Umformgrad φ) mit den nachfolgend angegebenen mikrostrukturellen Größen. Da der Werkstoff unter Werkzeugkontakt Martensit bildet und in dieser Simulation die Phasenumwandlung nicht berücksichtigt wird, ist eine Ersatzgröße für die Eigenspannungen in der Phase Austenit erforderlich (Gl. (4)).
MV = 0,08°∙ln(φ+1,13) (2)
MA = 30,22 %∙φ–12,16 %∙φ2 (3)
σ2 = –141,38 MPa – 13,26 ∙MA (4)
Die Übereinstimmung der aus der Umformsimulation berechneten Korrosionsrate im Vergleich zu den experimentellen Daten sowie die Übertragbarkeit der Modellgleichungen auf andere Umformprozesse hängen maßgeblich von der Genauigkeit der Regressionsgleichung der Korrosionsrate (Gl. (1)) ab.
Über benutzerdefinierte Ergebnisgrößen konnten die Modellgleichungen in die Simulation integriert werden (siehe Abbildung 2). Dies ermöglichte die Berechnung der Korrosionsrate für das gesamte Bauteil auf die Korrosionsbeständigkeit.
Übertragung auf komplexe Prozesse
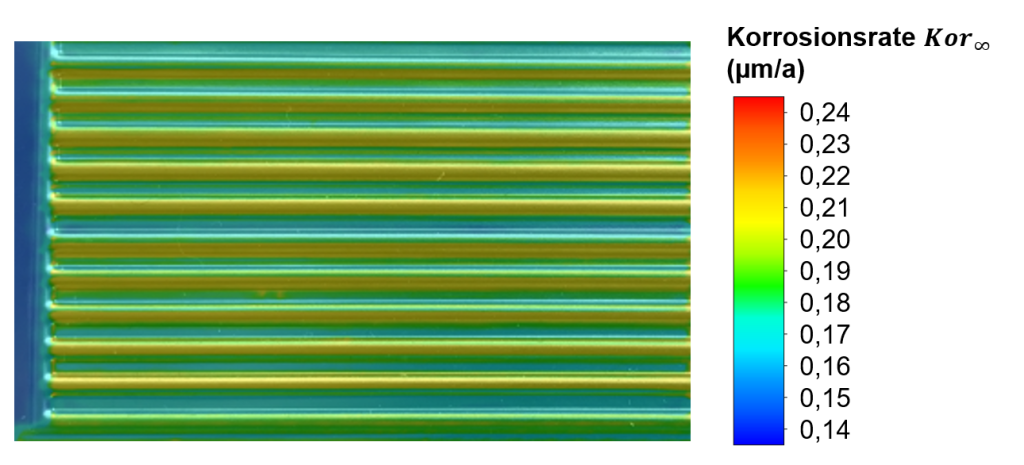
Abbildung 3: Anwendung auf komplexe Prozesse wie z. B. das Prägen des Flussfeldes einer Bipolarplatte während der Umformung (Darstellung als Ausschnitt)
Aktuelle Arbeiten befassen sich mit der Übertragung der Vorgehensweise auf komplexere Umformprozesse. Diese umfassen beispielsweise das Prägen, das bei der Herstellung des Flussfeldes einer Bipolarplatte Anwendung findet. Hierbei können korrosionsanfällige Bereiche identifiziert und visualisiert werden (siehe Abbildung 3).
Das entwickelte Modell beschreibt die Wechselwirkungen zwischen Umformprozess, Mikrostruktur und der resultierenden Flächenkorrosionsrate des Werkstoffs 316L, insbesondere unter Berücksichtigung der möglichen Martensitbildung durch Werkzeugkontakt während der Umformung. Die erfolgreiche Implementierung der experimentell ermittelten Korrosionsmodellgleichungen ermöglicht eine gute lokale Vorhersage der Korrosionsraten in den FEM-Simulationen. Diese numerische Simulation unterstützt die Optimierung von Werkstückdesigns und Umformprozessrouten, indem sie potenziell korrosionsanfällige Bereiche frühzeitig identifiziert und es erlaubt, durch gezielte Umformprozesse die Korrosionsbeständigkeit zu erhöhen. Dadurch wird die Entwicklung eigenschaftsoptimierter Umformprozesse gefördert, die sowohl die Lebensdauer als auch die Performance der umgeformten Bauteile verbessern. Die Methodik lässt sich zudem auf weitere Werkstoffe und Umformprozesse übertragen, was einen wichtigen Beitrag zur ressourceneffizienten Produktion leistet.
Quellen
[1]
R. A. Antunes, M. C. L. Oliveira, G. Ett und V. Ett, „Corrosion of metal bipolar plates for PEM fuel cells: A review,“ International Journal of hydrogen energy, pp. 3632-3647, 2010, doi:10.1016/j.ijhydene.2010.01.059.
[2]
H. Tawfik, Y. Hung und D. Mahajan, „Metal bipolar plates for PEM fuel cell—A review,“ Journal of Power Sources, pp. 755-767, 2007, doi:10.1016/j.jpowsour.2006.09.088.
[3]
F. Dundar, E. Dur, S. Mahabunphachai und M. Koc, „Corrosion resistance characteristics of stamped and hydroformed proton exchange membrane fuel cell metallic bipolar plates,“ Journal of Power Sources, pp. 2546-3552, 2010, https://doi.org/10.1016/j.jpowsour.2009.12.040.
[4]
M. F. Peker und Ö. N. K. M. Cora, „Surface Topography Evolution During Long-Run Micro-Stamping of Bipolar Plates (BPPs) and Effects on Corrosion and Contact Resistance Characteristics,“ in ASME 2012 International Mechanical Engineering Congress and Exposition, Houston, Texas, USA, pp. 3035-3039, 2012, https://doi.org/10.1115/IMECE2012-854612012.
[5]
A. Dittes, T. Mehner, S. Friedrich, B. Awiszus und T. Lampke, „Quantitative Model for the Prediction of the Corrosion Rate of Cold-Rolled 316L STEEL,“ Material Science 59, pp. 213-222, 2023, https://doi.org/10.1007/s11003-024-00765-y.
Weitere Informationen
Autoren: Sandra Friedrich1, Axel Dittes2, Thomas Mehner2, Carolin Binotsch1, Till Clausmeyer1, Thomas Lampke2, Birgit Awiszus1