Im Bereich der Fügetechnologien von Kunststoffen, bietet das Laserdurchstrahlschweißen im Vergleich zu anderen Verfahren eine einzigartige Vielfalt an Prozessüberwachungsmethoden zur Sicherstellung der Schweißnahtqualität. Vorteilhaft wirkt sich dabei aus, dass die Einflussgrößen aus Prozess und Maschine nur sehr kleinen Streuungen unterliegen und überwiegend erfasst und geregelt werden. Treten größere Schwankungen in der Qualität des Schweißergebnisses auf, können sie zumeist auf die Fügeteile selbst zurückgeführt werden. Die Prozesseinflussgrößen sind dort vielfältig, allen voran spielen die Bauteiltoleranzen sowie die optischen Eigenschaften des Materials eine bedeutende Rolle. Letztere – besonders die Lasertransmission des lasertransparenten Fügepartners – werden wiederum von zahlreichen Faktoren beeinflusst. Hier sind, neben der Art des Materials, insbesondere die Vorprozesse (z. B. der Spritzguss) oder enthaltene Additive – wie Farbmittel und Glasfasern – zu nennen.
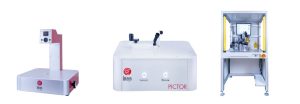
Bild 1: PICTOR Systeme zur Messung der Lasertransmission: links PICTOR Planar, Mitte PICTOR Radial, rechts PICTOR Radial als Integrationslösung (Quelle: Intego)
Die Möglichkeiten zur Kontrolle des Fügeprozesses beim Laserkunststoffschweißen sind breit gefächert. Stand der Technik sind dabei vor allem indirekte Methoden, die die Schweißnaht selbst nicht beurteilen, aber anhand verschiedener Überwachungsgrößen und -merkmale Rückschlüsse auf die zu erwartende Nahtqualität erlauben. Beim weit verbreiteten (Quasi-) Simultanschweißen ist eine etablierte Methode die sogenannte Fügewegüberwachung: dort wird die prinzipbedingte Relativbewegung der Fügepartner zueinander über die Prozesszeit als Kurve aufgenommen. Während der Fügeweg normalerweise auf ein bestimmtes Maß geregelt geschweißt wird, können charakteristische Kurvenpunkte, wie die notwendige Schweißzeit, die initiale Lage der Komponenten, aber auch der gesamte Fügewegverlauf überwacht und nach vorgegebenen Grenzen ausgewertet werden.
Wird als Verfahrensvariante das sogenannte Konturschweißen ohne Fügeweg gewählt (und steht dieser Parameter nicht zu Verfügung), kann als Prozessüberwachung die Pyrometrie, also die berührungslose Temperaturmessung zur Kontrolle und Prozessregelung eingesetzt werden. Dabei wird an der aktuellen Laserposition ein Teil der entstehenden Wärmestrahlung aus der Prozesswärme erfasst, um wiederum Rückschlüsse auf die Temperatur und den Energieeintrag durch den Laser zu ziehen. Faktoren, die zu Temperaturschwankungen führen können, sind (neben den Prozessparametern selbst) die Bauteilbeschaffenheit, vorrangig wieder die Lasertransmission, Ungleichmäßigkeiten in der Wärmeleitung – die durch Formfehler oder Nahtdefekte entstehen können – oder unerwünschte Verbrennungen an der Bauteiloberfläche.
Auch wenn diese beiden indirekten Überwachungsmethoden zu einer deutlich gesteigerten Prozesssicherheit führen, unterliegen sie bestimmten Grenzen, im Speziellen bzgl. der Größe detektierbarer Nahtfehler. So wird bei der Fügewegüberwachung die Bewegung der Fügeteile zueinander in der Regel als ein integraler Durchschnittswert über die gesamte Nahtkontur gemessen, wodurch lokal begrenzte Schweißnahtfehler unterhalb einer bestimmten Größe u. U. nicht detektiert werden können. Bei der Pyrometrie kommt die Dämpfung, Streuung und zeitliche Verzögerung der erfassten Wärmestrahlung beim Materialdurchgang aus der Fügezone nachteilig zum Tragen. Diese Faktoren sind stark material- und geometrieabhängig und können die Größe der erkennbaren Nahtdefekte ebenfalls einschränken.
Um diesen Nachteilen beizukommen, gibt es für die Prozessüberwachung und Materialcharakterisierung weitere, direkte Methoden, welche auf optischen Verfahren beruhen und von der Fa. EVOSYS gemeinsam mit der Intego GmbH angeboten und kontinuierlich weiterentwickelt werden. So ist es bereits vor der Fügeoperation möglich, die Transmission des lasertransparenten Bauteils (als maßgebliche Prozesseinflussgröße) einfach und zuverlässig zu bestimmen. Dafür stehen die Transmissionsmessgeräte PICTOR Planar für flache Bauteile (wie Gehäusedeckel) sowie PICTOR Radial für radialsymmetrische Komponenten (z. B. Leitungskonnektoren) zur Verfügung. Diese Systeme können sowohl stand-alone für die begleitende Qualitätskontrolle entlang der Wertschöpfungskette eingesetzt werden (z. B. bei einer Wareneingangsprüfung) oder sind für eine Online-Überwachung vollständig in den Fertigungsablauf integrierbar. So ist es möglich, eine nicht spezifikationsgerechte Einzelkomponente noch vor der Fügeoperation auszuschleusen, anstatt die höherwertigere Gesamtbaugruppe nach dem Schweißvorgang verwerfen zu müssen. Daneben können die ermittelten Messwerte als Regelgröße für den nachfolgenden Schweißprozess verwendet werden, um beispielsweise den Eintrag der Laserenergie anzupassen. Das Messprinzip der Geräte beruht darauf, dass ein Messstrahl mit einem bestimmten Strahlungsfluss (Φ0) und einer Wellenlänge entsprechend des Arbeitslasers an der gewünschten Prüfstelle auf das Bauteil aufgebracht wird. Der transmittierte Strahlungsanteil (also der Teil der Strahlung, der das Bauteil durchdringt und nicht reflektiert oder absorbiert wird) wird nach dem Durchgang durch das Material sensorisch erfasst. Dieser verbleibende Strahlungsfluss (Φ T) wird als prozentualer Wert zum Referenzfluss Φ0 ins Verhältnis gesetzt. Die Messsysteme arbeiten u. a. mit der Lock-In Technologie, um Lichteinflüsse aus der Umgebung weitestgehend zu eliminieren und um präzise und wiederholgenaue Messergebnisse zu liefern. Daneben unterlaufen sie einem aufwändigen Kalibrierungsprozess, um eine hohe Vergleichbarkeit der Ergebnisse innerhalb verschiedener Geräte zu gewährleisten. Im Bild 1 sind die PICTOR Systeme als Stand-Alone Varianten (links und Mitte) sowie als ein beispielhaftes System für die Online-Integration dargestellt (rechts).
Während bzw. unmittelbar nach dem Schweißprozess, kann die Qualität der Schweißnaht anhand verschiedener Merkmale über bildgebende Verfahren bewertet werden, wofür die PICTOR Vision Geräte entwickelt wurden. Eine Variante sind Kamerasysteme zur optischen Infrarot (IR)-Inspektion, die sensitiv für einen Wellenlängenbereich von ca. 750 nm – 1500 nm sind. Dadurch ermöglichen sie eine zerstörungsfreie Sicht auf die Schweißnaht, selbst wenn der lasertransparente Fügepartner im sichtbaren Wellenlängenbereich opak ist. Dabei macht man sich – wie für den eigentlichen Laserschweißprozess auch – die Eigenschaft der meisten thermoplastischen Kunststoffe zu Nutze, dass sie im Infrarotbereich eine höhere Transparenz für das Licht aufweisen als für die kurzwelligere Strahlung des visuellen Spektrums. Für die Bildaufnahme wird die Baugruppe mit Infrarot-Lichtquellen be- oder durchstrahlt, wodurch die Schweißnaht visualisiert wird. Durch intelligente Softwarealgorithmen und Bildverarbeitung kann sie sehr schnell und automatisiert auf Fehler, wie geometrische Unregelmäßigkeiten, Unterbrechungen oder thermische Schädigungen überprüft werden. Bild 2 zeigt als Beispiel einen lasertransparent schwarz eingefärbten Leitungskonnektor, der mit laserabsorbierenden schwarzen Leitungsstücken verschweißt wurde. Links stellt sich der Konnektor unter Tageslicht im visuellen Spektrum schwarz dar, unter IR-Beleuchtung hingegen als transparent – die drei Schweißnähte werden sehr kontrastreich erkennbar. Rechts ist eine thermische Schädigung in der Schweißnaht dargestellt, die durch eine helle Spur in der Mitte der Naht charakterisiert ist und über die Bildverarbeitung automatisch detektiert werden kann. Analog zu den Systemen zur Messung der Lasertransmission, können die Geräte für eine Online-Prozesskontrolle integriert werden oder sind für eine produktionsbegleitende Qualitätskontrolle als einfach zu handhabende Stand-Alone Geräte verfügbar.
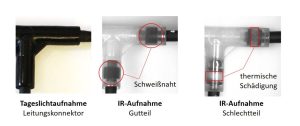
Bild 2: Optische IR-Inspektion der Schweißnaht mittels PICTOR Vision (Quelle: Evosys)
Eine weitere Variante der PICTOR Vision Inspektionssysteme sind thermografische Kameras, die die längerwellige IR-Wärmestrahlung aus der Baugruppe während des Schweißprozesses aufnehmen. Dies kann zum einen passiv erfolgen, wobei die Prozesswärme im Bereich der Schweißnaht erfasst wird, zum anderen aktiv über die Lock-in Methode, bei der das Bauteil nach dem Schweißprozess nochmals über Wärmestrahler aktiv angeregt wird. Dabei wird der Abfluss der eingebrachten Wärmeenergie vom einen in den anderen Fügepartner betrachtet, wobei die Schweißnaht die Schnittstelle bildet. Kommt es zu Störungen des Wärmeflusses, z. B. durch Schweißnahtunterbrechungen bzw. einem schlechten (thermischen) Kontakt, ändert sich die an der Bauteiloberfläche detektierte Wärmesignatur (Bild 3), welche wiederum als Überwachungsgröße und zur Bildverarbeitung genutzt wird. Im Gegensatz zur optischen IR-Inspektion, können hier – ähnlich der Pyrometrie – zusätzlich Rückschlüsse auf die Prozesstemperatur und eingebrachte Laserenergie gezogen werden.
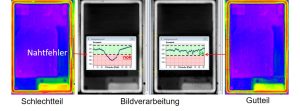
Bild 3: Wärmesignatur einer Laserschweißnaht (rot) aufgenommen mit PICTOR Vision (Thermografie) (Quelle: Evosys)
Da sich beim Laserkunststoffschweißen die Schweißnaht in aller Regel im Überlappstoß zwischen den beiden Fügepartnern und nicht an deren Oberfläche bildet, ist allen bildgebenden Inspektionsverfahren gemein, dass die aufgenommene Strahlung stets das lasertranstransparente Teil durchdringen muss. Da dieser Strahlungsanteil maßgeblich von den optischen Materialeigenschaften beeinflusst wird, ist die Güte der Bildinformation und die Größe der detektierbaren Fehler stark material- und geometrieabhängig. Das geeignete Überwachungsverfahren muss daher anwendungsspezifisch unter Berücksichtigung des Materials, der Füllstoffe und der geometrischen Komplexität ausgewählt werden.
Fazit
Zusammenfassend bieten die PICTOR Planar, PICTOR Radial und PICTOR Vision Systeme die umfassende Möglichkeit, das Material und die Ausbildung der Schweißnaht über optische und bildgebende Inspektionsverfahren direkt zu charakterisieren. Durch ihre vollautomatisierte Integrierbarkeit in eine Online-Prozesskontrolle stellen sie eine einzigartige Ergänzung zu den etablierten Überwachungsmethoden dar, um die Schweißnahtqualität zuverlässig zu bewerten und sicherzustellen.
Autoren
Dipl.-Ing. Frank Brunnecker,
Geschäftsführer & Gesellschafter,
Evosys Laser GmbH
Dipl.-Ing. Christian Ebenhöh,
Key Account Manager,
Evosys Laser GmbH