Abstract
Die Entwicklung und Verfügbarkeit von Werkstoffen und den aus ihnen herstellbaren Werkzeugen und Produkten sind seit jeher die Basis für den technischen und sozialen Fortschritt. Nicht zuletzt für metallische Konstruktionswerkstoffe gilt jedoch, dass ihre Leistungsgrenzen in vielen Anwendungsgebieten bereits erreicht worden sind. Die zunehmenden Anforderungen an Eigenschaften und Qualität der Werkstoffe machen somit Innovationen in der Werkstoffentwicklung erforderlich. Mit der neuen Methode des Laser-Tieflegierens sollen die Grenzen der konventionellen Schmelzmetallurgie überwunden werden. Das Ziel dieser experimentellen Werkstoffentwicklung ist eine hochdurchsatzfähige und reproduzierbare Erzeugung von chemisch homogenen Legierungsvarianten. Die Beherrschung des Tieflegierprozesses hinsichtlich der Homogenität des Umschmelzbades ist hierfür ein wichtiger Schritt und soll mittels in-situ-Erfassung des Emissionsspektrums des prozessinduzierten Plasmas sichergestellt werden. In ersten Untersuchungen konnte gezeigt werden, dass der zeitliche Verlauf einer Chromlinie dafür geeignet ist, während des Umschmelzvorgangs die Veränderung des Elementgehaltes innerhalb des Umschmelzbades zu beobachten. So stellte sich beim Tieflegieren von einem Grundsubstrat aus unlegiertem Einsatzstahl 1.0401 mit einer vordeponierten Schicht aus einem pulverförmigen Edelstahl 1.4404 die Intensität der Chromlinie spätestens nach zwei Umschmelzvorgängen, was einer Dauer von 1,1 s entspricht, auf ein konstantes Niveau ein.
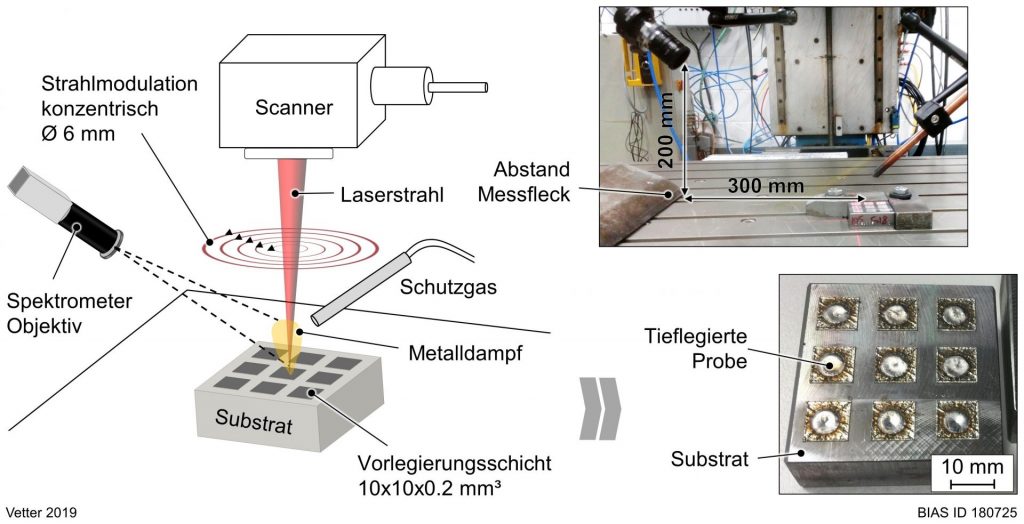
Bild 1: Laser-Tieflegieren mit Prozessüberwachung mittels Spektroskopie.
1. Einleitung
Insbesondere metallische Werkstoffe unterliegen aufgrund ihrer vielseitigen Einsatzmöglichkeiten einer großen Anzahl von Belastungen unterschiedlichster Stärke und Ausprägung. Mit zunehmenden Innovationsgrad in der Technologie steigen auch die Ansprüche an die Konstruktionswerkstoffe, die zur Umsetzung der Innovationen benötigt werden. Konsequenterweise bedarf es daher auch neuer, dynamischer Verfahren, die es ermöglichen, effizient und mit vertretbarem wirtschaftlichen Aufwand passgenaue Werkstoffe zu entwickeln, die den jeweiligen Anforderungen an diese gerecht werden. Ein vielversprechender Ansatz ist die hochdurchsatzbasierte experimentelle Werkstoffentwicklung. Dabei wird die Probengröße zunächst drastisch verringert und die Anzahl der zu untersuchenden Proben dagegen erhöht. Dies ermöglicht die Analyse einer Vielzahl unterschiedlichster Legierungszustände, deren Eigenschaften über eine heuristische Prädiktorfunktion hinsichtlich der makroskopischen Werkstoffeigenschaften des Anforderungsprofils ermittelt werden sollen [1].
Eine geeignete Methode zur Herstellung von Legierungen mit definierten chemischen Zusammensetzungen für Hochdurchsatzuntersuchungen ist die Laserstrahltechnologie. Der Laser bietet den entscheidenden Vorteil, dass er eine hohe Bearbeitungsgeschwindigkeit ermöglicht und zudem eine sehr hohe Präzision in Bezug auf den Energieeintrag aufweist [2]. Insbesondere beim Laserlegieren bietet dies die Möglichkeit, Legierungsgehalte über den Energieeintrag und das damit verbundene Legierungsvolumen variabel zu gestalten und somit potenziell neue Werkstoffeigenschaften zu generieren.
Für reproduzierbare Legierungszusammensetzungen wird an einem zweistufigen Laser-Tieflegierprozess geforscht. Dabei wird das Laserstrahlschmelzen (LBM) für die definierte Zugabe von Legierungselementen und anschließend ein Hochleistungslaser für den eigentlichen Tieflegierprozess verwendet [3]. Um Proben mit vergleichbaren Werkstoffeigenschaften zu erhalten, ist die Beherrschung des Tieflegierprozesses hinsichtlich der chemischen Homogenität des Umschmelzbades ein wichtiger Schritt im Herstellprozess. Diese soll mittels in-situ-Erfassung des Emissionsspektrums des prozessinduzierten Plasmas sichergestellt werden [3]. Dieser Vorgehensweise liegt die Hypothese zugrunde, dass sich die charakteristischen Linien des aufgezeichneten Spektrums in einem festgelegten Bereich nicht mehr oder nur noch geringfügig in ihrer Intensität verändern, sobald eine gleichmäßige Durchmischung des Umschmelzbades erreicht ist.
Jedes Element emittiert mit einer spezifischen Wellenlänge, wenn es durch den Laser angeregt und somit auf ein höheres Energieniveau gebracht wird. Aus der Intensitätsmessung über einen gewissen Wellenlängenbereich können somit aus den gemessenen Emissionen einzelne Elemente identifiziert und Legierungen oder andere Stoffzusammensetzungen abgeleitet werden [4]. Zur Identifizierung von Elektronenübergängen und damit der spektralen Peaks muss das aufgenommene Spektrum untersucht werden [5]. So liegen, gemäß der NIST Atomspektren-Datenbank, Emissionsspektren hoher Intensität von Eisen zwischen 340 nm und 880 nm und von Chrom bei 1010 nm. Ein entscheidendes Kriterium dafür, inwiefern die Spektroskopie zur Bewertung und Sicherstellung der Homogenität innerhalb der Legierung geeignet ist, ist die Korrelation von aufgezeichneten Metalldampfspektren und der tatsächlich vorliegenden chemischen Zusammensetzung der Probe.
2. Experimenteller Aufbau
2.1 Laser-Tieflegieren
Bild 1 zeigt den Versuchsaufbau für Untersuchungen der Homogenität mittels Spektroskopie. Für den Tieflegierprozess kam ein TruDisk12002 Scheibenlaser mit einer Wellenlänge von 1030 nm und maximaler Leistung von 12 kW zum Einsatz. Die Fokussierung erfolgte über eine PFO 3D-Scanneroptik mit Planfeldobjektiv (f-theta) und einer Brennweite von 450 mm. Der Spotdurchmesser betrug 650 µm während über eine im 45° Winkel angestellte Schutzgasdüse mit 13 mm Durchmesser kontinuierlich Argon mit 6 l/min in die Prozesszone eingebracht wurde (Bild 1). Als Vorlegierung wurde der pulverförmige Edelstahl 1.4404 mit 16,5 Gew.% Chrom als 0,2 mm dicke Schicht mittels Laserstrahlschmelzen auf dem Substrat vordeponiert. Das Substrat bestand aus einem Block des unlegierten Einsatzstahls 1.0401 mit den Abmaßen 150 mm x 150 mm x 18 mm.
Der Laserstrahl wurde über die Scanneroptik kreisförmig moduliert. Für einen Umschmelzvorgang wurde eine Modulationsfigur, bestehend aus fünf konzentrischen Kreisen von innen nach außen nacheinander abgescannt. Der Modulationsweg solch einer Modulationsfigur lag insgesamt bei 46 mm mit einer Bearbeitungsdauer von 572 ms. Der Durchmesser der Figur und somit die resultierende Probengröße betrug 6 mm. Bei allen Versuchen betrug die Laserleistung 3,5 kW und die Scangeschwindigkeit 5 m/min. Für die Aufzeichnung der Metalldampfspektren kam das TELLUS EMI-1020 mit einem Spektralbereich von 190 nm bis 1000 nm zum Einsatz. Die Messsonde wurde über einen Lichtleiterkoppler mit einem Objektiv verbunden und unter einem Winkel von 45° im Abstand von 360 mm zur Prozesszone ausgerichtet. Bild 1 zeigt die tieflegierten Proben auf dem Substrat nach dem Tieflegierprozess.
2.2 Identifizierung von Spektrallinien
Um die Integrationszeit so weit zu erhöhen, dass die verfügbare Aufnahmefrequenz des Spektroskops bestmöglich ausgenutzt wird, kam ein Abschwächer-Modul zwischen Spektroskop und Objektiv zum Einsatz (Bild 2). Zusätzlich ermöglicht der Abschwächer eine Rückbeleuchtung mittels Helium-Neon-Laser für eine optimale Anpassung des Spektrometer-Messflecks an die Größe der Prozesszone. Je größer die Integrationszeit, desto genauer entspricht das gemessene Spektrum dem tatsächlich Vorhandenen, da es weniger von zufälligen Intensitätsschwankungen beeinflusst wird. Gleichzeitig darf die Integrationszeit nicht zu groß sein, damit die Verläufe der Intensitäten zeitlich möglichst gut aufgelöst werden. Ein zwischen Objektiv und Spektroskop verbauter variabler Abschwächer sorgt für eine an den Sensor angepasste Flussregelung. Damit verhindert er eine Übersättigung des Sensors und ermöglicht eine Anpassung der Integrationszeit an die Periodendauer. Bild 2 zeigt auf der linken Seite ein Metalldampfspektrum, welches ohne Abschwächer aufgezeichnet wurde. Die nutzbare Integrationszeit ist auf 0,45 ms beschränkt, bevor es zu einer Übersättigung des Sensors kommt. Der Abschwächer ermöglicht es, die Integrationszeit auf 3 ms zu erhöhen und dadurch die Qualität der Spektren, wie im rechten Bildteil zu sehen, durch ein verringertes Rauschen deutlich zu steigern.

Bild 2: Der variable Abschwächer sorgt für eine Erhöhung der Integrationszeit und verhindert eine Übersättigung.
Um aus den aufgezeichneten Spektren Rückschlüsse auf die chemische Homogenität der Legierung ziehen zu können, sind gut identifizierbare Elementlinien im Gesamtspektrum erforderlich. Bild 3 zeigt ein, vom NIST-Atomic-Spectra-Database-Interface für das LIBS-Verfahren (laser induced breakdown spektroskopy) generiertes, synthetisches LTE-Spektrum (local thermal equilibrium) mit Dopplerverbreiterung. Unter Angabe der Plasmaparameter des Lasersprozesses für den Werkstoff der vordeponierten Schicht werden die Ionenpopulationen gemäß den Saha-Gleichungen und die Energieniveaupopulationen gemäß der Boltzmanstatistik berechnet. Elektronendichte und -temperatur betragen bei einem Laserschweißprozess typischerweise 1016 cm-3 und 0,75 eV [5]. Die NIST-Datenbank stellt die Summe der Emissionen aller im Werkstoff enthaltener Elemente sowie die Anteile von Chrom und Eisen dar. Dies ermöglicht es, einzelne Peaks bestimmten Elementen zuzuordnen. Laut NIST ASD treten im Bereich von 521 nm mehrere Chromlinien mit hohen relativen Intensitäten auf [6]. Im Diagramm ist deutlich zu erkennen, dass die hohe Intensitätsspitze an dieser Stelle fast ausschließlich von Chromlinien hervorgerufen wird (Bild 3). Allerdings bestehen zwischen den Metalldampfspektren beim Laser-Tieflegieren und typischen LIBS-Spektren bzw. den synthetischen Spektren der NIST ASD große Unterschiede. Dies liegt unter anderem an der starken Prozessstrahlung, der Wärmestrahlung des Schmelzbads, der undefinierten Anregung beim Laserprozess und des nicht Vorhandenseins eines lokalen thermischen Gleichgewichts. Dennoch kann die Analyse der Metalldampfspektren Aufschlüsse über die chemische Zusammensetzung der Schmelze liefern. Für die Spektralanalyse der Chromanteile in den Legierungen wurde die Chromlinie bei einer Wellenlänge von 520,84 nm gewählt, da diese der maximalen Empfindlichkeit des Spektroskops an nächsten kommt.
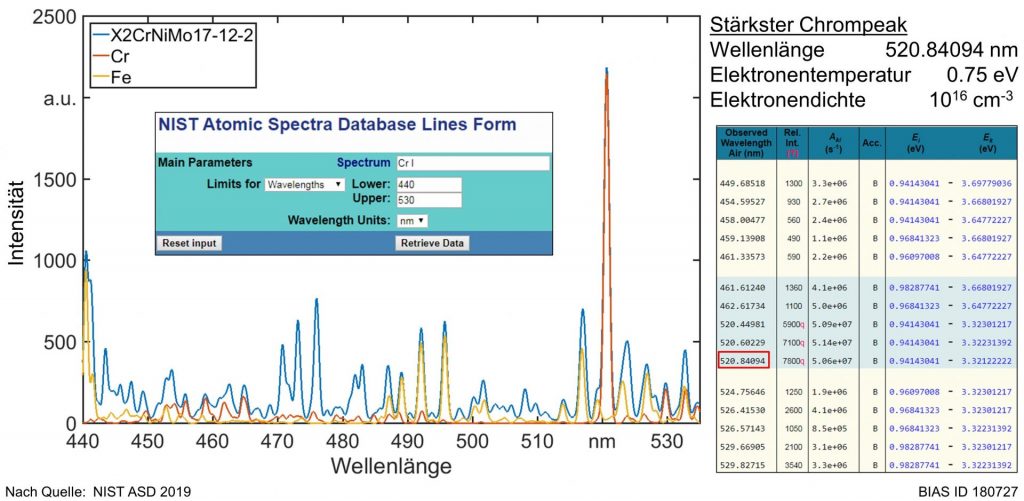
Bild 3: LTE-Spektrum von 1.4404 (X2CrNiMo17-12-2) sowie durch Eisen und Chrom entstehende Emissionsanteile
3. Ergebnisse
3.1 Einstellung der Elementkonzentration über das Umschmelzvolumen
Für die Untersuchung des Einflusses der Umschmelzdauer auf die Homogenisierung der Legierungen wurden Proben mit einem, zwei, drei und vier Umschmelzvorgängen erzeugt. Bild 4 zeigt die jeweiligen Proben im metallografischen Querschliff und den Einfluss der Anzahl an Umschmelzvorgängen, respektive der Umschmelzdauer, auf das Umschmelzvolumen und die Chromkonzentration der Legierungen. Die Schliffbilder der Proben weisen Risse und einige Poren hauptsächlich im unteren Bereich der Proben auf. Diese wirken sich jedoch nicht signifikant auf die betrachteten Homogenitätsuntersuchungen aus. Das Diagramm zeigt einen annähernd linearen Anstieg der Umschmelzfläche mit fortschreitender Umschmelzdauer. Aufgrund der rotationssymetrischen Form der Strahlmodulation kann von der umgeschmolzenen Fläche auf einen entsprechenden Anstieg des umgeschmolzenen Volumens geschlossen werden. Die Chromkonzentration der Proben wurde mittels wellenlängendispersiver Röntgenspektroskopie (WDX) bestimmt. Das Messfeld liegt mittig in der Probe und umfasst 32.500 Messpunkte bei einer Schrittweite in x und y von 10 µm. Die Chromkonzentration verringert sich bei vier Umschmelzvorgängen hintereinander mit zunehmendem Umschmelzvolumen von 2,48 Gew.% auf 1,19 Gew.%.
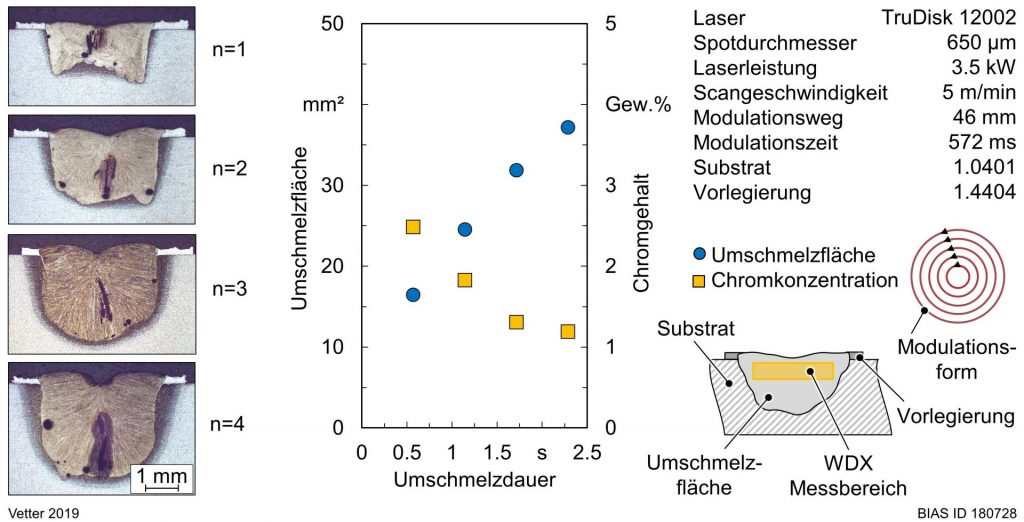
Bild 4: Einfluss der Anzahl an Umschmelzvorgängen auf das Umschmelzvolumen und die Chromkonzentration der Legierung.
3.2 Spektralanalyse
Aufgrund ungleichmäßig ausströmender Mengen angeregten Metalldampfes, wechselndem Kapillardurchmesser und unterschiedlich intensiver Prozessstrahlung können die Intensitätswerte einer Elementlinie von Spektrum zu Spektrum stark variieren [7]. Um dennoch Rückschlüsse auf die Elementanteile im Schmelzbad ziehen zu können, ist eine Normalisierung der Spektren erforderlich. Mit der Gesamtlichtnormalisierung wurde das Verhältnis der Intensität der beobachteten Linie zu jedem Zeitpunkt zur Summe aller erfassten Intensitäten dargestellt [8]. Bild 5 zeigt den Intensitätsverlauf des stärksten Chrompeaks über vier Umschmelzvorgänge hinweg. Die durchgezogenen Linien markieren jeweils das Ende eines Umschmelzvorgangs, die gestrichelten Linien das Ende eines Kreises der Modulationsfigur. Der Intensitätsverlauf des jeweils ersten Umschmelzvorganges unterscheidet sich deutlich von den folgenden drei Umschmelzvorgängen. Während der ersten Modulationsfigur erreicht die Intensität zu Beginn eines jeden Kreises der Modulationsfigur durch das Aufschmelzen der vordeponierten Elementschicht einen maximalen Chromanteil mit Werten von ca. 5,5 a.u. und fällt dann innerhalb einiger Millisekunden auf ca. 3 a.u. ab. Danach sinkt die Intensität innerhalb der nächsten 100 ms aufgrund der Vermengung mit aufgeschmolzenem Grundwerkstoff weiter auf 2 a.u. und bleibt annähernd konstant, bis der Laserstrahl zum nächstgrößeren Kreis der Modulationsfigur wechselt.
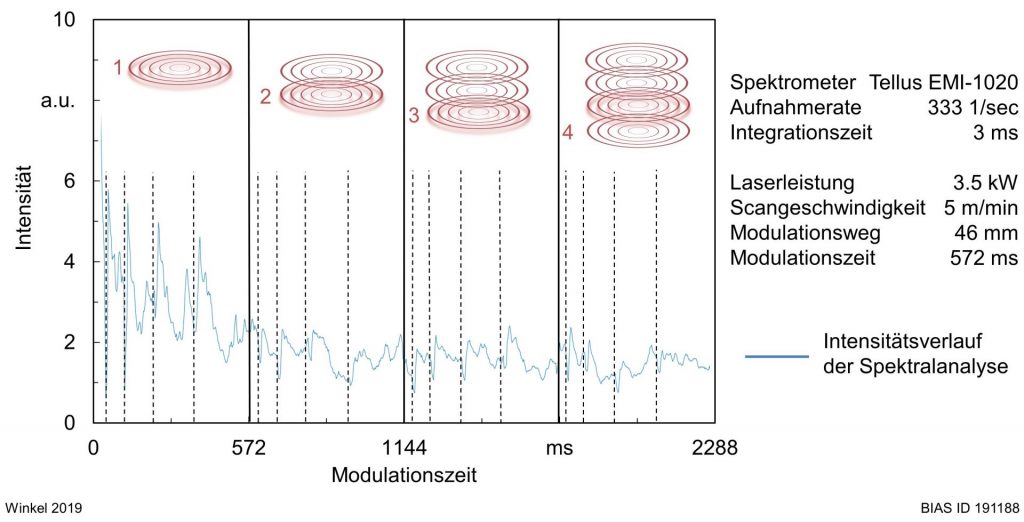
Bild 5: Intensitätsverlauf der Spektralanalyse bei viermaligem Umschmelzen und einer gesamten Prozessdauer von 2288 ms.
Bei den folgenden drei Umschmelzvorgängen bleibt die Intensität in etwa konstant zwischen 1,5 a.u. und 2,5 a.u. Größere Schwankungen treten dann nur noch vereinzelt auf. Der sinkende Intensitätsverlauf der Chrompeaks korreliert mit der abnehmenden Chromkonzentration bei steigender Modulationszeit und größer werdendem Umschmelzvolumen (Bild 4). Das Ziel der Spektralanalyse ist eine Bewertung der Gleichmäßigkeit der Elementverteilung bezogen auf die stoffliche Konzentration in jedem Volumenelement. Es wird vermutet, dass die Intensitätswerte der charakteristischen Linien des Metalldampfspektren ähnlich der Konzentration eines Legierungselementes in verschiedenen Teilvolumen schwanken. Je gleichmäßiger also die Elementverteilung im Schmelzbad ist, desto geringer fällt die Standardabweichung der Linienintensitäten aus.
3.3 Vergleich zwischen Spektralanalyse und chemischer Elementanalyse
In Bild 6 sind die Ergebnisse einer WDX-Analyse der Laser-tieflegierten Proben dargestellt. Die am linken Bildrand befindliche Skala gibt dabei den Massenanteil von Chrom in der tieflegierten Probe wieder. Nach einem Umschmelzvorgang (n=1) sind im eingefärbten metallografischen Schliffbild deutliche Konzentrationsunterschiede innerhalb der Legierung zu erkennen. Der unter dem Schliffbild befindliche Ausschnitt der WDX-Analyse zeigt den Unterschied ebenfalls. Stellenweise dunkle Bereiche, die für das chromfreie Substratmaterial stehen, treten zwischen grünlich-blau dargestellten, durchmischtem Gefüge auf. Der Verlauf der Chromkonzentration über den ausgewählten Messbereich (Bild 6) zeigt ebenfalls lokale Schwankungen bei einer sonst relativ gleichmäßigen Chromverteilung in Höhe von 2,48 Gew.%. Die Analyseergebnisse der Proben nach zwei bis vier Umschmelzvorgängen zeigen qualitativ keine erkennbaren Konzentrationsunterschiede über den Probenquerschnitt mehr.
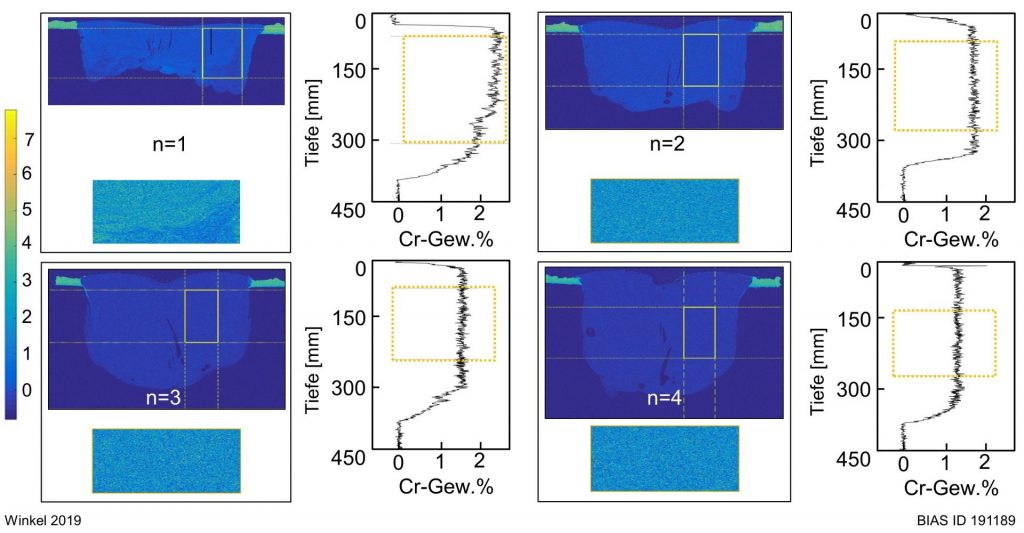
Bild 6: Chemische Analyse der Chromkonzentration (WDX) von Proben nach insgesamt einem, zwei, drei und vier Umschmelzvorgängen. Das Messfeld wird durch den gelben Auswahlkasten dargestellt.
Für die Bewertung der Eignung der Spektralanalyse zur Qualitätssicherung der homogenen Durchmischung von Legierungselementen, wurde die auf Basis der Intensitätsschwankungen und die nachträglich mittels WDX-Analyse ermittelte Homogenität miteinander verglichen. Dabei dient die Standardabweichung als Maß für die Homogenität. Bild 7 zeigt den Verlauf der Standardabweichung bei einem bis vier Umschmelzvorgängen sowohl bei der Messmethode nach WDX als auch nach der Spektrometer-Messmethode. Die Standardabweichung des Massenanteils von Chrom liegt bei einer Umschmelzdauer von 572 ms bei einem Wert von 1,2 Gew.%. Nach dem viermaligen Abscannen der Figur ist die Standardabweichung des Massengehaltes von Chrom auf einen Wert von 0,9 Gew.% gesunken. Bei den Standardabweichungen aus der Spektrometer-Messung verhält es sich ähnlich. Hier liegt der Wert nach den ersten 572 ms bei 1,25 a.u. und sinkt in den folgenden 1,72 s auf eine Standardabweichung von 0,52 a.u.
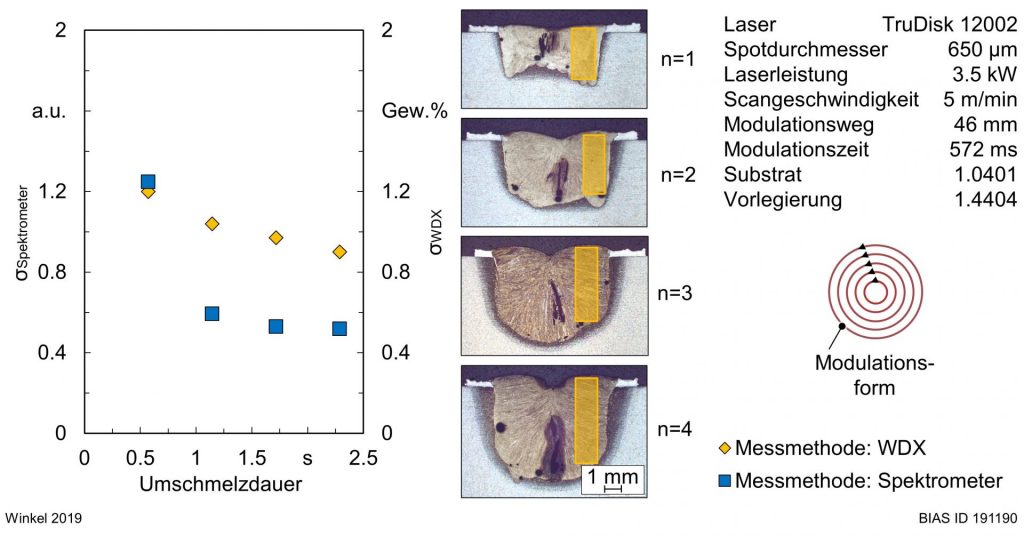
Bild 7: Vergleich der Homogenität der Chromkonzentration auf Basis der Standardabweichung von Messpunkten der WDX-Analyse und der Spektralanalyse.
Zusammenfassung
Erste Untersuchungen zur Qualitätssicherung mittels Spektroskopie bei der laserbasierten experimentellen Werkstoffentwicklung haben gezeigt, dass zumindest für das Element Chrom die Homogenität über die Auswertung der Streuung eines Spektroskopiesignals bereits während des Prozesses bewertet werden kann, was die Möglichkeit für eine Regelung des Prozesses auf möglichst kurze Prozesszeiten bei dennoch guter Homogenität des Gefüges eröffnet. Die mit zunehmender Umschmelzdauer sinkende Standardabweichung in der WDX-Messung zeigt eine gleichmäßigere Verteilung der Legierungselemente im Grundsubstrat. Sowohl bei den in-situ Messungen als auch bei den nachträglichen Analysen an den tieflegierten Proben mittels WDX wurde deutlich, dass spätestens nach zwei Umschmelzvorgängen, was einer Umschmelzdauer von 1,1 s entspricht, eine weitestgehend gleichmäßige Durchmischung vorliegt. Mit zunehmender Umschmelzdauer steigt die Homogenität innerhalb der Legierung nur noch geringfügig an.
Danksagung
Gefördert durch die Deutsche Forschungsgemeinschaft (DFG) – Projektnummer 276397488 – SFB 1232. Für die finanzielle Unterstützung des Teilprojekts U02 „Laser-Tieflegieren zur Einstellung fein abgestufter Legierungszustände” wird gedankt.
Autor*innen
Konstantin Vetter (1),
Nils Murken (1),
Thorsten Winkel (1),
Hannes Freiße (1),
Annika Bohlen (1),
Frank Vollertsen (1), (2)
(1)BIAS Bremer Institut für angewandte Strahltechnik,
Klagenfurter Str. 5,
28359 Bremen, Germany
(2)Universität Bremen,
Bibliothekstr. 1,
28359 Bremen, Germany
Kontakt
M.Sc. Annika Bohlen
Gruppenleitung Additive Verfahren
BIAS – Bremer Institut für angewandte Strahltechnik GmbH
Klagenfurter Straße 5, 28359 Bremen
bohlen@bias.de, www.bias.de
Literatur
[1] Mädler, L.: Is High-throughput screening for structural material/metals possible? Proceedings of the 4th International Conference on Nanomanufacturing – nanoMan (2014) Bremen, Deutschland
[2] Vollertsen, F.; Partes, K.; Habedank, G.; Seefeld, T.: Deep penetration dispersing of aluminum with TiB2 using a single mode fiber laser. Production Engineering – Research and Development 1, 2 (2008) 27-32
[3] Vetter, K.; Freiße, H.; Vollertsen, F.: High-throughput material development using selective laser melting and high power laser. Proceedings of the 7th WGP-Jahreskongress (2017) Aachen, Deutschland, 511–518
[4] Huber, S.: In-situ-Legierungsbestimmung beim Laserstrahlschweißen. Forschungsberichte IWB 286 (2014) München, Deutschland
[5] Zaeh, M.-F.; Huber, S.: Characteristic line emissions of the metal vapour during laser beam welding. Production Engineering – Research and Development 5, 6 (2011) 667-678
[6] Kramida, A.; Ralchenko, Y.; Reader, J.; NIST ASD Team (2018): NIST Atomic Spectra Database (version 5.6.1), National Institute of Standards and Technology, Gaithersburg, https://physics.nist.gov/asd, zugegriffen am 12.03.2019
[7] Fabbro, R.; Slimani, S.; Coste, F.; Briand, F.: Analysis of the various melt pool hydrodynamic regimes observed during CW-Nd:Yag deep penetration laser welding. 26th International Congress on Applications of Lasers & Electro-Optics – Kongressberichte (2007)
[8] Karki, V.; Sarkar, A.; Singh, M.; Singh Maurya, G.; Kumar, R.; Kumar Rai, A.; Kummar Aggarwal, S.: Comparison of spectrum normalization techniques for univariate analysis of stainless steel by laser-induced breakdown spectroscopy. Pramana – Journal of physics 86, 6 (2016) 1313-1327