Die additive Fertigung hat sich in den vergangenen Jahren rasant entwickelt als innovatives Verfahren, oft bionisch inspirierte Bauteile werkzeuglos zu fertigen.
Besonders weit verbreitet haben sich die Laser-Pulverbettverfahren (LPBF – Laser Powder Bed Fusion; oft auch Selective Laser Melting oder Laser Cusing® genannt), bei denen wiederkehrend dünne Pulverschichten lokal mit einem Laser aufgeschmolzen werden und so Schicht für Schicht, dem dreidimensionalen CAD-Design und geeigneter Anlagensteuerung folgend, Komponenten erzeugt werden (Abb. 1). Die qualitätsbestimmenden Parameter des Bauprozesses wurden eingehend untersucht und auch die mikrostrukturellen Eigenschaften sowie die makroskopischen Geometriegrößen, hier besonders der Verzug, umfangreich untersucht.
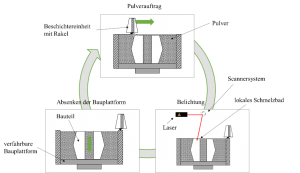
Abb. 1: Verfahrensschema des Laser Powder Bed Fusion Prozesses (LPBF)
Bei den metallischen Werkstoffen, die mittels LPBF verarbeitet werden, dominiert der nichtrostende Edelstahl AISI 316 L (1.4404 – X2CrNiMo17-12-2), der aufgrund seiner metallurgischen Kenngrößen besonders gut für diesen Prozess geeignet ist. Mit ihm lassen sich Porositäten im Zustand „as built“ sowie Verzug und Eigenspannungen im Bauteil recht gut beherrschen. Zwar stellen sich durch die raschen Aufheiz-/Aufschmelzzyklen der Pulverkörner mit rascher Wiedererstarrung sehr feinkörnige Gefüge mit gegenüber schmelzmetallurgisch erzeugtem Stahl höheren statischen und dynamischen Festigkeiten ein, das Niveau bleibt jedoch auf demjenigen der nicht härtbaren austenitischen Edelstähle.
Die hohen geometrischen Freiheitsgrade des 3D-Drucks erlauben es, Funktionsflächen unmittelbar in die Bauteile zu integrieren. Oft werden Funktionsflächen in Bauteilen adhäsiv oder abrasiv tribologisch beansprucht, teils erleiden sie auch durch strömende flüssige Medien erosiven Verschleiß.
Allgemein gelten austenitische nichtrostende Stähle als nicht härtbar, da sie keine Gefügeumwandlung von Austenit zu Martensit zeigen. Austenitische Werkstoffe können jedoch über den bei der Härterei Gerster entwickelten Niedertemperatur-Nitrocarburierprozess HARD-INOX-S®, bei dem Stickstoff und Kohlenstoff in die Bauteiloberfläche eindiffundieren, eine beträchtliche Härtesteigerung auf über 1.000 HV erreichen. Die sich einstellende homogene Randschicht wurde früher als „S-Phase“ bezeichnet, sie erreicht aufgrund der tiefen Temperaturen Eindringtiefen für N und C von 20 bis 30 µm. Die Korrosionsbeständigkeit verschlechtert sich gegenüber dem austenitischen Ausgangszustand nicht, ferner bleiben die Bauteile unmagnetisch.
Der Prozess ist daher prädestiniert, additiv gefertigte Bauteile aus 316 L in der Randschicht zu härten und sie so vor Verschleiß zu schützen. Eine partielle Behandlung ist ebenso möglich, sollte bei scharf gekerbten Bauteilen die Gefahr der Anrissbildung bei zu hoher Beanspruchung bestehen.
In einem Stichversuch wurde die Machbarkeit geprüft. Abb. 2 zeigt die Oberfläche von Probeplättchen aus dem Stahl 316 L im Zustand „as built“ sowie nach einem Schleifabtrag.
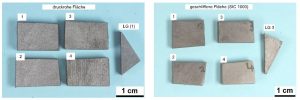
Abb. 2: Additiv gefertigte Proben aus Stahl 316 L (links: Oberfläche nur gedruckt (as built); rechts: Oberfläche nach 0,3 mm Schleifabtrag und Feinschleifen mit SiC 1.000)
Das Gefüge zeigt die typische Erstarrungsstruktur nach dem Laserschmelzprozess (Abb. 3, rechts).
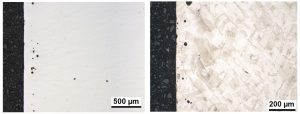
Abb. 3: Querschliff durch additiv gefertigten Stahl 316 L (links: ungeätzt, mit geringer Restporosität; rechts: Mikrostruktur nach Ätzung Adler, 10 s bei RT)
Nach dem von der Härterei Gerster entwickelten HARD-INOX-S ®-Nitrocarburierprozess stellt sich nach 420°C / 24 Std. in einer Stickstoff- und Kohlenstoff abgebenden Atmosphäre eine ca. 20 mm dicke Diffusionszone ein, die eine Härte von 1.000 – 1.300 HV 0,1 aufweist (Abb. 4).
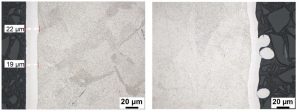
Abb. 4: Querschliff durch additiv gefertigten Stahl 316 L nach Hard Inox S®-Behandlung (links: Diffusionszone ca. 20 µm auf zuvor geschliffener Oberfläche; rechts: Diffusionszone auf einer Oberfläche „as built“ mit anhaftenden durchgehärteten Pulverpartikeln nach Ätzung Adler, 10 s bei RT)
Wie in den Gefügeaufnahmen erkennbar, bildet sich auf den additiv gefertigten Proben die erwartete gleichmäßige Diffusionszone hoher Härte aus (Abb. 5). Allerdings ist zuvor die Bauteiloberfläche nach dem 3D-Druck zu schleifen. Die rauere „as built“-Oberflächentopografie bleibt nach der Wärmebehandlung erhalten und führte z. B. zu geringeren Traganteilen bei tribologischer Beanspruchung mit gleichzeitig extremer Härte der Rauheitsgipfel. Ebenso wird deutlich, dass evtl. anhaftende Pulverpartikel aus dem Bauprozess bei der Wärmebehandlung „durchhärten“, welches für eine spätere Anwendung ebenfalls sehr negativ wäre. Wie in Abb. 4 zu sehen, kann es sich dabei um lose Pulverpartikel, aber auch um fester anhaftende Partikel handeln. Es empfiehlt sich daher, einen wirkungsvollen Reinigungsprozess vorzuschalten (Strahlen, Laserpolieren), der bei höher beanspruchten Bauteilen zur Reduzierung der Kerbwirkung einer rauen Oberfläche grundsätzlich angeraten ist.
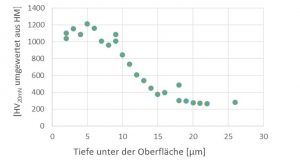
Abb. 5: Härteverlauf nach einer Hard-Inox-S®-Behandlung (420 °C / 24 Std.; Stahl 316 L)
Wie dieser Tastversuch gezeigt hat, lassen sich 3D-gedruckte Bauteile aus austenitischen nichtrostenden Stählen wie 316 L problemlos dem Wärmebehandlungsprozess HARD-INOX-S® unterziehen. Die Verschleißeigenschaften der Bauteile verbessern sich dadurch signifikant. HARD-INOX-S® kann als Schüttgutprozess realisiert werden und besitzt ein großes Potenzial für Anwendungen 3D-gedruckter Bauteile, auch bei anderen metallischen Werkstoffen.
Seit mehr als 70 Jahren bietet die Härterei Gerster AG Wärmebehandlungen an. HARD-INOX-S® ist ein von Gerster entwickeltes Verfahren und wird für das Härten von nichtrostenden Stählen eingesetzt, jetzt auch in Nordrhein-Westfalen.
Kontakt Deutschland
Peter Haase
Geschäftsführer
Gerster Deutschland GmbH
peter.haase@gerster.ch
Telefon +49 179 949 80 89