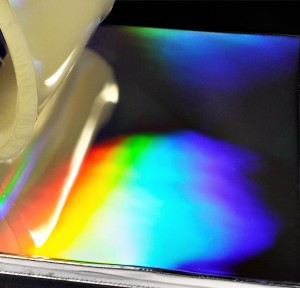
PUR wird von einer permanent beschichteten, nanostrukturierten Metalloberfläche sauber abgelöst. Durch die Nanostruktur kommt es im Bild zur Lichtbeugung und damit zur Farbgebung.
© Fraunhofer IFAM/Wolfgang Hielscher
Kunststoffteile werden täglich millionenfach in einer Werkzeugform hergestellt. Das Aufbringen eines Trennmittels verhindert bei diesem Fertigungsprozess ein Verkleben des Bauteils mit der Form – eine aufwendige und kostenintensive Methode. Eine sichere und vor allem trennmittelfreie Entformung ermöglichen Technologien aus dem Fraunhofer IFAM. Das sogenannte Release PLAS® -Trennschichtsystem wurde für die Kunststoffverarbeitung entwickelt und kann an ganz unterschiedliche Anforderungen der Materialien, Verarbeitungsmethoden und Bauteilgeometrien angepasst werden. Eine größere Herausforderung war bislang die trennmittelfreie Fertigung von Polyurethan-Kunststoffen – kurz PUR. In einem industriellen Gemeinschaftsprojekt konnten Wissenschaftler nun durch eine Anpassung der PUR-Rezeptur deutlich niedrigere Entformungskräfte erzielen und eine Produktion ohne Trennmittel ermöglichen.
Da ausreagierende Polyurethane eine hohe Haftungsneigung zu metallischen Oberflächen entwickeln, werden in der diskontinuierlichen Verarbeitung Trennmittel eingesetzt, um einen prozesssicheren Verfahrensablauf zu gewährleisten. In der industriellen Praxis werden dabei interne und externe Trennmittel verwendet, die
jedoch von einem Trennmittelübertrag auf die Werkzeug- bzw. Bauteiloberfläche begleitet werden. In der Folge entstehen zusätzliche Arbeitsschritte und Kosten. So müssen die PUR-Bauteile z. B. aufwendig von Trennmittelrückständen gereinigt werden, um ein anschließendes Lackieren oder Verkleben zu ermöglichen. Darüber hinaus reichern sich die Trennmittel im Laufe mehrerer Entformungszyklen auf der Werkzeugoberfläche an und bilden Ablagerungen, was zu einer schlechteren Abformgenauigkeit führt.
Industrie und Wissenschaft verfolgen deshalb konsequent das Ziel, eine dauerhafte und trennmittelfreie Fertigung – auch für Polyurethane – zu realisieren. Bei dem vom Fraunhofer-Institut für Fertigungstechnik und Angewandte Materialforschung IFAM in Bremen entwickelten Release PLAS® -Trennschichtsystem wird die Beschichtung direkt auf die Form aufgetragen. Sie bildet dabei Oberflächenstrukturen perfekt ab und kann in
ihrem Eigenschaftsprofil unterschiedlichen Anforderungen angepasst werden. Die stark hydrophob und abweisend wirkende plasmapolymere Schicht besteht aus einem siliziumorganischen Netzwerk und hat sich für viele Kunststoffarten und Fertigungstechniken bewährt.
Polyurethane reagieren anders
In der Polyurethan-Verarbeitung bieten permanente Trennschichten bisher nicht die gewünschten Vorteile gegenüber konventionellen Trennmitteln. In der Regel besteht keine ausreichende Langzeitstabilität der Trennwirkung, sodass auch hier kostenintensive Reinigungen und Wiederbeschichtungen notwendig sind. Zum
Trennverhalten reaktiver Polyurethane auf permanenten Trennschichten konnte bislang nachgewiesen werden, dass die Entformungseigenschaften in Abhängigkeit vom verwendeten PUR-System stark variieren. Das Versagen der Trennwirkung wird dabei durch Ablagerungen auf der Trennschichtoberfläche verursacht, die im Laufe weniger Entformungszyklen entstehen und zu einem Anstieg der Haftkräfte führen.
Durch aufwendige chemische und physikalische Analysen sowie oberflächentechnische Untersuchungen konnten die Fraunhofer IFAM-Forscher nun den Grund für das Versagen des Trennmechanismus herausfinden: Neben dem angestrebten Adhäsionsbruch zwischen Bauteil und Werkzeugoberfläche kommt es auch zu einem
Kohäsionsbruch in der oberflächennahen Grenzschicht des Bauteils (Interphase). Diese zum Zeitpunkt der Entformung nicht ausreichend stabile Interphase des PUR bewirkt, dass nanofeine Ablagerungen auf der Oberfläche des Werkzeugs verbleiben. Um derartige Materialübertragungsmechanismen zu unterbinden, und somit einen vollständigen Adhäsionsbruch zur Trennschicht zu erzeugen, wurden alle Parameter zur
Interphasenstabilität untersucht. Eine weitere Forschungsaufgabe war die Identifikation von Stabilisatoren – beispielsweise oberflächenaktive Additive.
Entwicklung trennfreundlicher PUR-Formulierungen mit stabiler Interphase
Um die Zusammenhänge bei der Interphasenbildung zu verstehen und diese gezielt zu beeinflussen wurden zwei verschiedene, sich ergänzende Lösungsstrategien verfolgt: Zum einen wurde der Einfluss der PUR-Rezeptur auf die Interphase analysiert, wobei systematisch verschiedene Inhaltsstoffe, wie Polyol, Isocyanat und der Katalysator verändert wurden. Zum anderen wurde die Interphase des sich bildenden PUR-Bauteils durch grenzflächenaktive Additive modifiziert und zusätzlich der Einfluss der Masse- und Formtemperatur auf die Fertigungsrandbedingungen untersucht.
Unter praxisnahen Verarbeitungsbedingungen konnten PUR-Modellrezepturen identifiziert werden, die bei der Entformung keine Ablagerungen auf der permanenten Trennschicht hinterlassen. Die Projektergebnisse zeigen, dass insbesondere das Polyol und der verwendete Katalysator einen deutlichen Einfluss auf das Entformungsverhalten haben. Darüber hinaus konnte ein Additiv identifiziert werden, welches die Entformbarkeit der getesteten PUR-Rezepturen in Kombination mit der Release PLAS® -Trennschicht für schlechter trennende Systeme deutlich verbessert. Es wirkt dabei nicht wie ein herkömmliches internes Trennmittel, da es nach aktuellem Kenntnisstand nicht aus dem Bauteil migriert. Das Additiv wird in die molekulare Struktur des PUR eingebunden, sodass bei einer Verwendung deutlich höhere Werkzeugstandzeiten erzielt werden können. Die Erkenntnis, dass ein geringer Unterschied der Formtemperatur bereits eine sprunghafte Reduktion der Trennkräfte bewirkt, muss ebenfalls in den Fertigungsprozess einfließen.
Weitere Informationen: http://www.ifam.fraunhofer.de