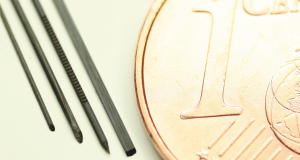
Abbildung 1 Z-Pins zur 3D-Verstärkung von Faser-Kunststoff-Verbunden: v.l.n.r. mit kreisförmigem Querschnitt mit einem Durchmesser von 0,28 mm und 0,5 mm sowie mit definierter Oberflächen-Mikrostrukturierung (umlaufende Kerben) und mit rechteckförmiger Querschnittsfläche.
Einleitung
Hochleistungs-Faserverbundwerkstoffe, wie sie heute verbreitet in Strukturkomponenten in der Luft- und Raumfahrt sowie zunehmend auch in Bereichen der Elektromobilität zum Einsatz kommen, bestehen typischerweise aus einer polymeren Matrix in Kombination mit verstärkenden Fasern. Speziell die kohlenstofffaserverstärkten Kunststoffe (CFK) mit Epoxidharzmatrix werden dort eingesetzt, wo ein hoher Leichtbaugrad zwingend erforderlich ist, um energie- und kosteneffiziente Systeme zu erreichen. Diese Werkstoffe besitzen, abhängig u.a. von der Kombination von Matrix und Faserverstärkung sowie der Anordnung und Ausrichtung der verstärkenden Fasern, hervorragende mechanische Eigenschaften kombiniert mit einem geringen Gewicht. Diese Eigenschaften zeigen sich in der Laminatebene, in der die lasttragenden Fasermaterialien ausgerichtet sind.
Nachteilige Eigenschaften faserverstärkter Kunststoffe und Strategien zu deren Reduzierung
Ihr schichtweiser Aufbau ruft aber auch weniger befriedigende Eigenschaften hervor. Dazu zählen bspw. geringe mechanische Eigenschaften, wie z.B. E-Modul und Festigkeit, in Dickenrichtung des Laminates sowie die geringen Delaminationsfestigkeiten. Durch stoß- und schlagartige Beanspruchungen, die auf Faser-Kunststoff-Verbund (FKV)-Strukturen wirken, können Ablösungen zwischen den Faserlagen entstehen. Sie rufen eine Reduzierung der Resttragfähigkeit hervor. Eine zerstörungsfreie Detektion derartiger Delaminationen ist nur unter großem Aufwand möglich. Äußerlich sind diese Schäden häufig kaum erkennbar. Sie können aber, unter dynamischen Beanspruchungen, zwischen den Laminatschichten wachsen und zu einer Schwächung sowie einem vorzeitigem Versagen der FKV-Strukturen führen.
Um diesen nachteiligen Eigenschaften zu begegnen, können z.B. thermoplastische oder Elastomerpartikel den vorrangig eingesetzten duroplastischen Matrices zugegeben werden. Sie rufen Mechanismen hervor, die zu einer Erhöhung der bruchmechanischen Eigenschaften des Matrixwerkstoffes und somit des Verbundes führen. Diesen Verbesserungen sind allerdings Grenzen gesetzt, so dass weitergehende Eigenschaftsverbesserungen vor allem durch die Anordnung von zusätzlichen Verstärkungsfasern in Dickenrichtung des Laminates erreicht werden können. Es existieren eine Vielzahl von Methoden, mit denen eine dreidimensionale (3D) Faseranordnung erzeugt werden kann, um mögliche Delaminationen zu verhindern, auftretendes Risswachstum zu verlangsamen oder sogar zu stoppen und dadurch schadenstolerante Strukturen zu erzeugen. Diese Verfahren, wie z.B. 3D-Web- und Flechtverfahren oder das Vernähen von Faserlagen, stammen aus der Textilindustrie und werden vorrangig an noch nicht mit Matrixmaterial imprägnierten Faserwerkstoffen angewendet.
3D-Verstärkung von Hochleistungs-Faserverbundwerkstoffen mittels z-Pins
Beim Einsatz vorimprägnierter Faserhalbzeuge (Prepreg), wie sie heute vorrangig in Strukturbauteilen in der Luft-und Raumfahrt verwendet werden, können diese Verfahren, aufgrund der vorliegenden Verarbeitungseigenschaften, nicht eingesetzt werden. Um eine 3D-Verstärkung dieser Werkstoffe zu erzeugen, wird das s.g. z-Pin Verfahren genutzt. Dabei werden dünne stabförmige Elemente (Pins), die aus hochfesten und hochsteifen Materialien, wie z.B. Stahl, Titan oder CFK mit unidirektionaler Faserverstärkung, bestehen, senkrecht zur Laminatebene in den FKV-Werkstoff eingebracht. In Abbildung 1 sind typische z-Pins aus CFK, die für den Einsatz zur 3D-Verstärkung von Prepreg-Materialien zum Einsatz kommen, im Größenvergleich zu einer 1 Eurocent Münze, dargestellt.
Typischerweise besitzen die z-Pins einen kreisrunden Querschnitt mit einem Durchmesser zwischen 0,1 bis 1 mm. In der Abbildung 1 sind beispielhaft z-Pins mit 0,28 mm und 0,5 mm Durchmesser (erster und zweiter Pin von links) dargestellt. Neueste wissenschaftliche Untersuchungen nutzen auch kreisrunde z-Pins mit einer definierten Oberflächen-Mikrostrukturierung durch umlaufende Rillen sowie z-Pins mit rechteckförmigem Querschnitt (dritter und vierter Pin von links), um deren Auszugseigenschaften und damit die Effektivität der 3D-Verstärkung zu erhöhen. Aufgrund der geringen Dichte, werden heute vornehmlich CFK-z-Pins eingesetzt, die aus hochfesten Kohlenstofffasern in unidirektionaler (UD) Ausrichtung in Kombination mit einer temperaturstabilen BMI (Bismaleimide)-Matrix bestehen.
Es existieren unterschiedliche Verfahren, wie die z-Pins in das noch unausgehärtete Prepeg-Laminat eingebracht werden können, doch wird vorrangig das Ultraschall-unterstütze z-Pin Verfahren eingesetzt. Die Fertigung verpinnter Laminate mit dem s.g. UAZ-Verfahren (ultrasonically assisted z-fiber process) lässt sich schematisch mit der Abbildung 2 erklären.
![Abbildung 2 Darstellung der Fertigungsschritte zur Einbringung einer z-Pin Verstärkung in ein Prepreg-Laminat mittels des ultraschallunterstütztem (UAZ)-Verfahrens [1]](https://werkstoffzeitschrift.de/wp-content/uploads/2021/05/Fertigung-300x139.png)
Abbildung 2 Darstellung der Fertigungsschritte zur Einbringung einer z-Pin Verstärkung in ein Prepreg-Laminat mittels des ultraschallunterstütztem (UAZ)-Verfahrens [1]
Resultierende Eigenschaften z-Pin verstärkter Faserverbundkunststoffe
Die Einbringung einer z-Pin-Verstärkung besitzt wesentlichen Einfluss auf die resultierenden mechanischen Eigenschaften des verpinnten Laminates. In der Tabelle 1 sind, am Beispiel einer z-Pin Verstärkung mit z-Pins mit 0,5 mm Durchmesser bei 2% Pin-Dichte, die Auswirkungen auf ausgewählte Kennwerte eines verpinnten Laminates, im Vergleich zum unverpinnten Laminat, zusammengefasst.
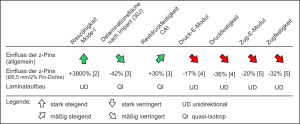
Tabelle 1 Änderung der mechanischen Kennwerte eines z-Pin-verstärkten Laminates im Vergleich zum unverpinnten Laminat bei gleichem Laminataufbau
Eigene Materialuntersuchungen zeigen wesentliche Verbesserungen der Delaminationsfestigkeiten sowie Impakt- und Schadenstoleranzeigenschaften. Es können Steigerungen der kritischen Energiefreisetzungsrate GIC unter Mode-I-Beanspruchung, bei einem Laminat mit UD-Faserausrichtung, von bis zu 3800% erreicht werden [2]. Unter Impaktbeanspruchung zeigen verpinnte Laminate ebenfalls deutliche Verringerungen der auftretenden Delaminationsflächen. Wie am Beispiel eines Schlagschadensereignisses auf ein Laminat mit quasi-isotropem (QI) Laminataufbau mit einer Energie von 30 J gezeigt werden konnte, werden Reduzierungen von 42% erreicht. Das hat wesentlichen Einfluss auf die Restfestigkeitseigenschaften, die um bis zu 30% gesteigert werden können [3].
Diese Eigenschaften können maßgeblich mit den Überbrückungseffekten, die die z-Pins zwischen den Faserlagen des Laminates hervorrufen, beschrieben werden. Treten an einer Fehlstelle oder einer Delamination im verpinnten Laminat Rissöffnungsbeanspruchungen auf, dann werden die z-Pins axial beansprucht und wirken einer Rissöffnung entgegen. Dabei kann ein Riss nur wachsen, wenn die Pins vom Laminat gelöst und unter Reibung ausgezogen werden. Die auftretenden energiedissipativen Prozesse haben eine Reduzierung der Energie an der Rissspitze zur Folge, so dass ein Risswachstum damit verlangsamt und sogar gänzlich gestoppt werden kann. Diese Brückenbildungsmechanismen sind im Wesentlichen abhängig von der Anbindung der z-Pins zum umgebenden Laminat. Eine Verbesserung der Bindungseigenschaften zwischen z-Pins und Laminat, wie z.B. durch eine Mikrostrukturierung oder plasmainduzierte Aktivierung der z-Pin Oberflächen, können weitergehende Erhöhungen dieser Eigenschaften hervorrufen. Wie in der Tabelle 1 dargestellt ist, rufen die z-Pins gleichermaßen Reduzierungen der mechanischen Eigenschaften des verpinnten Laminates, wie E-Modul und Festigkeit, die sich in der Laminatebene zeigen, hervor. Es zeigen sich bei Laminaten mit UD-Faserausrichtung Reduzierungen der Zug- und Druckfestigkeiten von 32% und 36%. Die Verringerungen der Elastizitätsmoduln fallen mit 20% beim Zug-E-Modul und 17% beim Druck-E-Modul geringer aus. Die Reduzierungen sind u.a. abhängig vom Durchmesser der z-Pins, so dass der Einsatz von Pins mit möglichst geringem Durchmesser zu bevorzugen ist [1,4,5]. Durch das derzeit eingesetzte Insertionsverfahren sind hier aber Grenzen gesetzt, um die strukturelle Integrität der Pins während der Insertionsphase zu gewährleisten.
Der Grund für diese Reduzierungen liegt in der resultierenden Mikrostruktur des Laminates, die durch die Einbringung der z-Pins hervorgerufen wird. In der Abbildung 3 kann, anhand eines Horizontalschliffes eines z-Pin verstärkten Laminates, beispielhaft der Einfluss der z-Pins auf die Mikrostruktur des verpinnten Laminates verdeutlicht werden.

Abbildung 3 Horizontalschliff eines z-Pin verstärkten Laminates mit 0,5 mm z-Pins
Das Schliffbild zeigt, dass die eingebrachten Pins Verlagerungen der Laminatfasern in der direkten Umgebung der Pins verursachen, die eine erhöhte Faserwelligkeit sowie harzreiche Zonen hervorrufen. Ebenfalls entstehen Mikrobrüche am z-Pin/Laminat-Interface während der Aushärtung, aufgrund der unterschiedlichen Wärmeausdehnungskoeffizienten von Pins und Laminat in Dickenrichtung. Zusätzlich dazu existieren weitere Veränderungen der Mikrostruktur, wie z.B. das Durchtrennen und Ablenken von Laminatfasern in Dickenrichtung sowie die Verringerung des Faservolumengehaltes, dadurch dass die Pins gegen die Kompaktierung während der Aushärtung wirken.
Bestehende Hürden für den Einsatz der z-Pin-Technologie
Aufgrund der höheren Kosten beim Einsatz von z-Pins für eine 3D-Verstärkung, die sich aus den Pins und Fertigungshilfsstoffen ergeben, gepaart mit dem derzeit noch großen zeitlichen Aufwand und den zusätzlichen Fertigungsschritten im Laminatherstellungsprozess, ist ihr Einsatz momentan noch auf wenige Anwendungen beschränkt. Sie werden daher momentan ausschließlich in Spezialanwendungen eingesetzt, wie z.B. im Motorsportbereich zur Verbesserung des Crashverhaltens der Monocoque-Strukturen von Formel 1 Rennwagen [1]. Um die positiven Eigenschaften der z-Pin Technologie ebenfalls für kommerzielle Anwendungen im Automobil- und Luftfahrtbereich nutzbar zu machen, ist daher speziell die Weiterentwicklung des derzeitigen Fertigungsverfahrens zur Erzeugung einer 3D-Laminatstruktur, hin zu einem schnellen und kostengünstigen Verfahren, notwendig.
Referenzen
[1] Mouritz, Adrian P. Review of z-pinned laminates and sandwich composites. Composites Part A: Applied Science and Manufacturing, Volume 139, December 2020, 106128.
[2] Hoffmann, J.; Scharr, G.: Mode I delamination fatigue resistance of unidirectional and quasi-isotropic composite laminates reinforced with rectangular z-pins. Composites Part A: Applied Science and Manufacturing (2018), 115, pp. 228-235.
[3] Knaupp, M.; Scharr, G.: Einsatz von z-Pins zur Modifikation der Festigkeit schlag- und stoßbelasteter Verbundstrukturen. Konstruktion 64 (2012), Nr. 4, S. 77-82.
[4] Knopp, A.; Scharr, G.: Compression properties of z-pinned carbon-fibre/epoxy laminates reinforced with circumferentially notched z-pins. Composite Science and Technology (2021), 201, 108486; DOI: 10.1016/j.compscitech.2020.108486.
[5] Knopp, A.; Scharr, G.: Tensile Properties of Z-Pin Reinforced Laminates with Circumferentially Notched Z-Pins. Journal of Composite Science (2020), 4(2), 78; DOI: 10.3390/jcs4020078.
Autoren:
Dr. André Knopp, Prof. Dr. Gerhard Scharr, Andreas Holtz
Lehrstuhl für Konstruktionstechnik/Leichtbau
Fakultät für Maschinenbau und Schiffstechnik
Universität Rostock
Albert-Einstein-Str. 2, 18059 Rostock