Pulvermetallurgische Verarbeitung von Pulvermischungen
Pulvermischungen werden in der konventionellen Pulvermetallurgie (PM) beim Matrizenpressen von Formteilen standardmäßig eingesetzt. Beim herkömmlichen Pressen und Sintern von Eisen- und Stahlpulvern werden Legierungszuschläge mit einem gut pressbaren Grundpulver gemischt. Die Legierungszuschläge können als Elementarpulver oder sog. „Meisterlegierung“ zugesetzt werden. Meisterlegierungen enthalten die Legierungselemente in den gewünschten Verhältnissen und vermeiden so das Mischen von Vielkomponentenwerkstoffen. Die Partikelgröße der Zusätze ist abhängig von der Legierungsart. Nicht aufschmelzende Elemente werden in Form feiner Pulver zugemischt, um beim Sintern eine homogene Durchmischung mittels Festkörperdiffusion zu erreichen. Aufschmelzende Partikel können in gröberer Form zugemischt werden, da sich die Schmelze vor den Diffusionsprozessen gleichmäßig im Bauteil verteilt. Aus Pulvermischungen verschiedener Korngrößen und Dichten ergeben sich auch stets Entmischungsproblematiken. In der konventionellen Pulvermetallurgie wird daher zum Teil über ein vorgelagertes Diffusionsglühen feines Pulver an das Grundpulver angesintert oder es werden organische Bindemittel verwendet, um feines Pulver an das Grundpulver zu kleben. Organische Hilfsmittel werden nach dem Formgebungsprozess durch Sintern thermisch entfernt. [1]
Die konventionelle PM-Route greift neben dem klassischen Legieren eines Werkstoffs auch auf Kombination verschiedener Werkstoffe zurück. Das Schichtverbundpressen als Formgebungsverfahren für ein Bauteil aus mehreren Pulvern ist ein etabliertes Verfahren. So können durch die Formgebung von Pulverpartikeln Werkstoffverbunde erzeugt werden, die schmelzmetallurgisch aus physikalischen Gründen nicht realisierbar sind. [1]
Chancen additiver Fertigungstechnologien
Die additive Fertigung (engl. Additive Manufacturing (AM)) greift auf andere Formgebungs- und Konsolidierungsverfahren zurück als die konventionelle Press- und Sinterroute, sodass die Notwendigkeit der Verformbarkeit der Grundpulver wegfällt. Gleichzeitig wird die Flexibilität, welche die Pulvermischungen bieten, erhalten und kann auch für die AM-Verfahren genutzt werden. Zudem können die Erkenntnisse, die aus der Verarbeitung von Pulvermischungen aus der Press- und Sinterroute bereits bekannt sind, zielführend genutzt werden. So können die Methoden zur Vermeidung von Entmischungen nahezu direkt auf die AM-Prozesse übertragen werden. Weitere Potentiale der Pulvermischungen in der AM-Fertigung sind kostengünstiges Legieren oder die Fertigung von Spezialwerkstoffen. Komplex geformte, gradierte Schichtbauteile sind nur eins von vielen denkbaren Beispielen.
Die Forschung an Werkstoffen für die additive Fertigung steht noch am Anfang. Bisher werden weitgehend Werkstoffe verarbeitet, die von den AM-Anlagenherstellern für ihre Prozesse qualifiziert wurden, um die verschiedenen AM-Prozesse in der Industrie zu etablieren. Diese Werkstoffpalette ist recht überschaubar und hinsichtlich der Diversität der meist schmelzmetallurgisch hergestellten, konventionellen Werkstoffe nicht vergleichbar. Mit fortschreitender Entwicklung der AM-Verfahren, erlangt aber auch die Forderung nach Werkstoffen, die sowohl auf spezielle Anwendungen wie auch auf die AM-Prozesse maßgeschneidert sind, zunehmend an Bedeutung.
Pulvermischungen in der additiven Fertigung
Die Bauteilkonsolidierung beim Binder Jetting, vorgestellt in Teil 1, weist Ähnlichkeiten zum Press-& Sinterprozess auf. Auch hier wird die Festigkeit der Bauteile über Diffusionsvorgänge beim Sintern erreicht. Pulvermischungen werden beim Binder Jetting jedoch bisher wenig verarbeitet [2].
In der laserbasierten additiven Fertigung werden Pulvermischungen bereits verarbeitet. Zu nennen sind hier die Verarbeitung im Direct Energy Deposition (DED) Verfahren sowie beim Laser Powder Bed Fusion (LPBF) Verfahren. Der Fokus liegt hier aktuell vor allem auf der Legierungsentwicklung für die laserbasierten Prozesse. Beim DED Verfahren, wird das Pulver direkt am Laserstrahl auf das Bauteil aufgetragen, sodass es beim Pulverauftrag keine Entmischung gibt. Beide Prozesse (LPBF und DED) haben gemeinsam, dass das Pulver über die schmelzflüssige Phase lokal an das Bauteil gefügt wird. Anschließend sorgen hohe Temperaturgradienten für eine schnelle Erstarrung der Schmelze. Demnach sind diese Prozesse auf der Mikroskala mit Schweißprozessen vergleichbar. Die Werkstoffe, die für diese Prozesse entwickelt werden, nutzen die hohen Temperaturgradienten zur gezielten Eigenschaftseinstellung der Bauteile.
Gezielte Einstellung von Bauteileigenschaften aus dem LPBF Prozess am Beispiel von Pulvermischungen
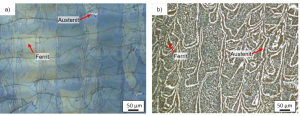
Abbildung 1: Gefüge des LPBF Duplexstahls im a) as-built Zustand und b) nach dem Lösungsglühen [3]
Durch die Legierungsmodifikation des Standard-Duplexstahls X2CrNiMoN22-5-3 konnte trotz der schnellen Abkühlung ein ferritisch-austenitisches Duplexstahlgefüge, ähnlich des lösungsgeglühten Stahls X2CrNiMoN22-5-3 direkt aus dem Prozess erzeugt werden, s. Abbildung 2 a) und b). Die Korrosionsbeständigkeit konnte, wie für Duplexstähle üblich, gegenüber dem reinen austenitischem Edelstahl AISI 316L gesteigert werden (Abbildung 2 c). Die Festigkeit dieses modifizierten Duplexstahls, aus den Mischungsverhältnissen abgeleitet M7-3 genannt, übertrifft die Festigkeit, die bisher im wärmebehandelten Zustand bei den Duplexstählen möglich war, bei gleichzeitig guter Duktilität (Abbildung 2 d). In der beschriebenen Studie sind durch die Ähnlichkeit der beiden verwendeten Pulver – vorlegierte, sphärische Pulver gleicher Partikelgrößenverteilungen – trotz des mechanischen Pulverauftrags keine Gefügeinhomogenitäten beobachtet worden. Aus diesem Grund erscheint auch eine standardmäßige Verarbeitung dieser Legierung als Pulvermischung vielversprechend. [4]
![Abbildung 2:a) Gefüge der Pulvermischung (M7-3) im LPBF as-built Zustand b) EBSD Phasenmapping von M7-3 EV=53 J/mm³, c) Stromdichtepotentialkurven von X2CrNiMo17-12-2, M7-3 EV=53 J/mm³ and EV=48 J/mm³ und X2CrNiMoN22-5-3, c) Kennwerte aus Zugversuchen von M7-3 im Vergleich zu X2CrNiMo17-12-2 und X2CrNiMoN22-5-3 [4]](https://werkstoffzeitschrift.de/wp-content/uploads/2021/06/Abbildungen-Paper2__Seite_2-208x300.jpg)
Abbildung 2:a) Gefüge der Pulvermischung (M7-3) im LPBF as-built Zustand b) EBSD Phasenmapping von M7-3 EV=53 J/mm³, c) Stromdichtepotentialkurven von X2CrNiMo17-12-2, M7-3 EV=53 J/mm³ and EV=48 J/mm³ und X2CrNiMoN22-5-3, d) Kennwerte aus Zugversuchen von M7-3 im Vergleich zu X2CrNiMo17-12-2 und X2CrNiMoN22-5-3 [4]
Die Untersuchungen zum LPBF Duplexstahl haben gezeigt, dass Pulvermischungen im LPBF Verfahren zu homogenen Bauteilen verarbeitet werden können. In einem gemeinsamen Forschungsprojekt mit dem Fraunhofer IFAM in Bremen werden weitere Untersuchung zur Verarbeitung von LPBF Pulvermischungen durchgeführt, um über den kostengünstigen Einsatz von Pulvermischungen die Palette der verfügbaren Werkstoffe zu erweitern. Dabei wird, ähnlich zur klassischen Pulvermetallurgie, ein Basispulver durch verschiedene Zusätze modifiziert. Anders als im Sinterprozess, werden alle Pulverpartikel lokal aufgeschmolzen, sodass bei dem Mischungskonzept unter anderem die Schmelzpunkte bzw. Schmelzintervalle in Zusammenhang mit der Partikelgröße berücksichtigt werden müssen. Hochschmelzende Molybdän- oder Niobpartikel, beispielsweise, verbleiben ansonsten als festigkeitsreduzierende, unvollständig aufgeschmolzene Partikel im Gefüge [5,6]. Durch gezielte Zugabe von Chrom oder Chromkarbiden hingegen, kann potentiell die Korrosionsbeständigkeit oder die Verschleißbeständigkeit einer Legierung gesteigert werden. Bei starken Unterschieden zwischen den verschiedenen Pulverpartikeln hinsichtlich der Partikelgröße kann es zur Entmischung des Pulvers kommen. Diese Problematik wird durch den mechanischen Vorgang des Pulverauftrags durch eine Rakeleinheit möglichweise noch verstärkt. Gezeigt in Abbildung 3 sind das Pulverbett und eine Würfelbauplatte eines Warmarbeitsstahls X40CrMoV5-1 (AISI H13) mit 10 % Cr3C2-Karbidpulver. Die feinen Cr3C2-Karbide (D90=11 µm) entmischen im Pulverbett. Eine Abweichung der Zusammensetzung zwischen Würfel 1 und 11 ist auf eine ungleiche Verteilung der Karbidpartikel zurückzuführen. Durch Rückrechnung der chemischen Zusammensetzung wird die Bestimmung der Karbidadditionen in den jeweiligen Würfeln möglich. Während Würfel 1 4,6 % Cr3C2-Karbide enthält, sind in Würfel 11 6,2 % Cr3C2-Karbide enthalten. Im Mittel bedeutet dies einen Verlust von 48 % der Chromkarbidpartikel beim Aufschmelzen durch den Laser. Weiterführende Untersuchungen zur Verminderung der Entmischung und des Abdampfens sind Bestandteil laufender Untersuchungen im Projekt.
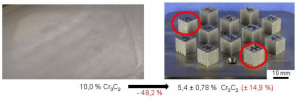
Abbildung 3: Pulverbett und mittels LPBF gebaute Würfel eines Baujobs aus X40CrMoV5-1 mit 10% Cr3C2-Karbiden; Verlust von Cr3C2-Karbiden durch Abbrand: 48%; Ungleichverteilung der Karbidpartikel zwischen Würfel 1 und 11: 14,9%
Eigenschaften vs. Verarbeitbarkeit
Die Verarbeitbarkeit harter Werkstoffe im LPBF Verfahren ist stark eingeschränkt. Werkstoffe, die zunächst als Würfelproben verarbeitbar scheinen, weisen beim Übertragen auf komplexere Strukturen oftmals Risse auf. Durch gezielte Legierungsmodifikation durch beigemischtes Pulver können die Grenzen der Verarbeitbarkeit kosteneffizient ausgelotet werden. Am IWM wurden Pulvermischungen aus den Schnellarbeitsstählen HS 6-5-3-8 und HS 7-7-7-11 verarbeitet und die Gefüge hinsichtlich kritischer Legierungsbestandteile untersucht. Durch die Verarbeitung der Mischungen wurde gezielt die Karbidmenge und das theoretische Karbidverhältnis MC/M6C, ermittelt durch thermodynamische Berechnung, variiert. Mit steigendem Anteil an HS 7-7-7-11 wurde eine steigende Rissneigung der Werkstoffe festgestellt und diese auf einen höheren Anteil von MC Karbiden zurückgeführt. Die Ergebnisse sind in Abbildung 4 zusammengefasst. Ausgehend von diesen Erkenntnissen konnten optimierte Legierungen sonderverdüst werden, die trotz hoher Legierungsgehalte verarbeitbar waren und Forschungsgegenstand eines kürzlich gestarteten IGF-AiF-Projekts mit dem Fraunhofer ILT in Aachen sind (IGF-Vorhaben-Nr. 21393 N). In diesem Beispiel dienten die Pulvermischungen somit dem Zweck, in der Werkstoffentwicklung kostenintensive, iterative Verdüsungsprozesse zu vermeiden.
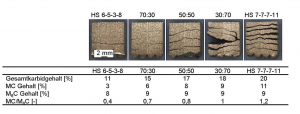
Abbildung 4: Rissneigung in Abhängigkeit der Legierungszusammensetzung und theoretischer Einflussfaktoren am Beispiel von Pulvermischungen aus HS 6 5 3 8 und HS 7 7 7 11
Herausforderung: Pulverrecycling
Zur wirtschaftlichen Verwendung von AM-Prozessen muss stets auch das Recycling der Pulver berücksichtigt werden. Das Pulver aus dem Pulverbett muss üblicherweise vor erneuter Verwendung gesiebt werden. Durch die Aufbereitung des Pulvers in einem Siebschritt, kann die Zusammensetzung des Pulvers (ungewollt) verändert werden. Das Recycling von Pulvermischungen als Feedstock für pulverbettbasierte Verfahren ist bisher wenig erforscht. Für einen kosteneffizienten Einsatz von Pulvermischungen in der Industrie muss diese Fragestellung zukünftig geklärt werden. Beim DED Verfahren, bei dem das Pulver unmittelbar am Laserstrahl auf die Probe aufgebracht wird, existiert dieses Problem nicht. Jedoch wird das nicht aufgeschmolzene Pulver auch bei diesem Verfahren entsorgt [7]. Die Pulverausnutzung des Verfahrens kann beispielsweise durch spezielle Düsenanpassungen erhöht werden, liegt jedoch weiterhin unterhalb von 75 % [8].
Förderung
Die vorgestellten Arbeiten wurden im IGF-Vorhaben 20933 N der Forschungsgesellschaft Stahlverformung e.V. über die AiF im Rahmen des Programms zur Förderung der industriellen Gemeinschaftsforschung (IGF) vom Bundesministerium für Wirtschaft und Energie aufgrund eines Beschlusses des Deutschen Bundestages sowie vom Europäischen Fonds für regionale Entwicklung (EFRE) unter der Fördernummer EFRE-0800666 gefördert.
References
[1] P. Beiss, Pulvermetallurgische Fertigungstechnik, Springer Berlin Heidelberg, Berlin, Heidelberg, 2013.
[2] Ming Li, Wenchao Du, Alaa Elwany, Zhijian Pei, Chao Ma, Metal Binder Jetting Additive Manufacturing: A Literature Review.
[3] J. Kunz, A. Boontanom, S. Herzog, A. Kaletsch, C. Broeckmann, Influence of hot isostatic pressing post-treatment on the microstructure and mechanical behavior of standard and super duplex stainless steel produced by laser powder bed fusion, Materials Science and Engineering: A (2020) 139806.
[4] M.L. Koehler, J. Kunz, S. Herzog, A. Kaletsch, C. Broeckmann, Microstructure analysis of novel LPBF-processed duplex stainless steels correlated to their mechanical and corrosion properties, Materials Science and Engineering: A (2020) 140432.
[5] I. Polozov, V. Sufiiarov, A. Popovich, D. Masaylo, A. Grigoriev, Synthesis of Ti-5Al, Ti-6Al-7Nb, and Ti-22Al-25Nb alloys from elemental powders using powder-bed fusion additive manufacturing, Journal of Alloys and Compounds 763 (2018) 436–445.
[6] I. Yadroitsev, P. Krakhmalev, I. Yadroitsava, Titanium Alloys Manufactured by In Situ Alloying During Laser Powder Bed Fusion, JOM 69 (2017) 2725–2730.
[7] M. Zenou, L. Grainger, Additive manufacturing of metallic materials, in: Additive Manufacturing, Elsevier, 2018, pp. 53–103.
[8] R. Koike, S. Takemura, Y. Kakinuma, M. Kondo, Enhancement of powder supply efficiency in directed energy deposition based on gas-solid multiphase-flow simulation, Procedia CIRP 78 (2018) 133–137.
Autor:innen
Marie Luise Köhler (m.koehler@iwm.rwth-aachen.de),
Johannes Kunz,
Simone Herzog,
Anke Kaletsch,
Christoph Broeckmann