J. Tenkamp, S. Siddique, F. Walther
Fachgebiet Werkstoffprüftechnik (WPT), Technische Universität Dortmund, Baroper Str. 303, D-44227 Dortmund, www.wpt-info.de
Einleitung
Viele Bauteile des Maschinen- und Anlagenbaus werden im Betrieb schwingbeansprucht. Dabei müssen diese nicht selten 107 bis 109 oder gar 1010 Lastwechsel ertragen. War es früher Stand des Wissens, dass Werkstoffe nicht durch Ermüdung versagen, wenn die einwirkende Beanspruchung unterhalb der sog. „Dauerfestigkeit“ liegt, wurden mit neuen Methoden Ausfälle im Bereich sehr großer Lastspielzahlen (VHCF, Very High Cycle Fatigue) auch für Beanspruchungen unterhalb der „Dauerfestigkeit“ festgestellt. Dies führt zum Schluss, dass eine derartige „Grenze“ nicht existiert [1,2].
Für viele Legierungen der Gittertypen kubisch-raumzentriert (krz) und kubisch-flächenzentriert (kfz) wurde im VHCF-Bereich ein weiterer Abfall der Wöhlerkurve festgestellt. Zudem kann es zur Änderung des Rissinitiierungsorts von der Oberfläche ins Volumen kommen, sodass der Schädigungsmechanismus je nach Betriebsdauer wechselt [3]. Aufgrund dieser Erkenntnisse werden zuverlässige Auslegungskenngrößen für sicherheitsrelevante Bauteile immer wichtiger, z.B. für Motorenkomponenten (≥ 108), Wälzlager (≥ 109) und Gasturbinen (≥ 1010 Lastwechsel).
Während mit konventionellen servohydraulischen und elektromagnetischen Schwingprüfsystemen in der Regel Prüffrequenzen bis 300 Hz erreicht werden können, ermöglichen Ultraschallprüfsysteme (USF) eine Prüffrequenz von 20.000 Hz. Die Dauer von Schwingversuchen kann dadurch entscheidend reduziert werden. USF-Systeme ermöglichen eine zeiteffiziente Charakterisierung des Ermüdungsverhaltens bis 109 (< 1 Tag Versuchszeit) oder 1010 Lastwechsel (6 Tage Versuchszeit). Zum Vergleich würde ein Schwingversuch bis 109 Lastwechsel mit 300 Hz ca. 58 Tage dauern. Die hohe Prüffrequenz von 20.000 Hz wird mittels piezoelektrischer Aktuatoren erreicht [1], um eine zeit- und ressourceneffiziente Charakterisierung des Ermüdungsverhaltens bei sehr hohen Lastspielzahlen zu gewährleisten.
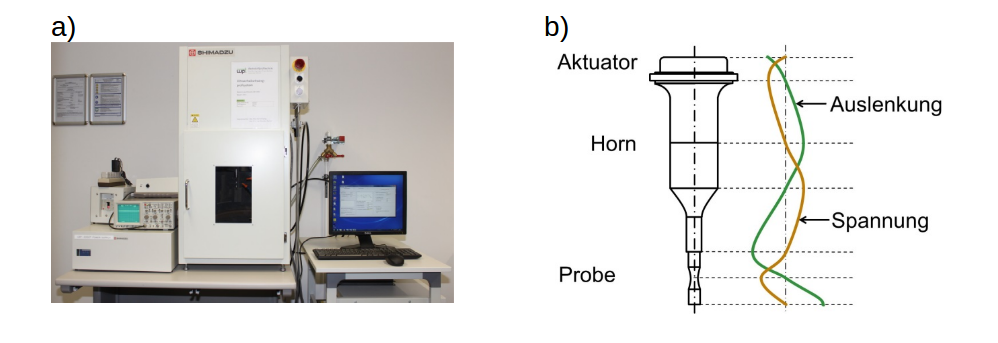
Abbildung 1: (a) Ultraschallschwingprüfsystem (Standard-Konfiguration) Shimadzu USF-2000, (b) Funktionsprinzip der Ultraschallermüdung
Experimentelle Vorgehensweise
Die experimentelle Vorgehensweise und das Leistungsvermögen der Versuchstechnik sollen anhand des Ultraschallschwingprüfsystems USF-2000 (Fa. Shimadzu, Duisburg) veranschaulicht werden. Abbildung 1a zeigt eine Übersichtsaufnahme des Prüfsystems und Abbildung 1b das Funktionsprinzip. Ein piezoelektrischer Kristall wird als Aktuator eingesetzt, der mit 20.000 Hz schwingt. Die Probengeometrie wird mittels analytischer und numerischer Berechnung so ausgelegt, dass die Maximalbeanspruchung in der Probenmitte auftritt und die maximale Auslenkung am freien Probenende. Die Probe wird einseitig mittels Gewinde in das Prüfsystem eingeschraubt (Abbildung 2a).
Da die Proben infolge der Verformung bei hohen Frequenzen stark erwärmen können, sind Ultraschallprüfsysteme mit Systemen ausgerüstet, um die Temperaturerhöhung der Proben zu mindern bzw. vermeiden. Die Proben werden mit Druckluft gekühlt (Abbildung 2b, oben) und mit einem Impuls-Pause-Verhältnis geprüft, z.B. 50:50. Die Temperaturentwicklung wird mit Hilfe eines Pyrometers (Abbildung 2b, unten) kontrolliert. Der Schädigungsfortschritt und das Probenversagen werden anhand der Änderung der Resonanzfrequenz detektiert. Entsteht ein makroskopischer Anriss, führt die reduzierte Eigenfrequenz der Probe zum Abfall der Arbeitsfrequenz des Prüfsystems und der Test wird automatisiert beendet.
Die Probenprüfung wurde unter Einsatz des Systems USF-2000 (in Standard-Konfiguration) mittellastfrei vorgenommen. Viele Bauteile unterliegen im Betrieb aber einer überlagerten statischen Belastung, u.a. durch Eigengewicht oder prozessinduzierte Eigenspannungen. Diese überlagerten statischen Lasten beeinflussen die Schädigungsentwicklung und die Lebensdauer, Zugspannungen führen zur Verringerung der Lebensdauer während Druckspannungen diese verlängern [4]. Um diese betriebsrelevanten Belastungszustände auch im VHCF-Bereich abbilden zu können, kann das System in einen Lastrahmen integriert und um einen Aktuator erweitert werden, wodurch VHCF-Versuche mit überlagerter Mittellast möglich werden. Der Einbau der Probe erfolgt durch beidseitiges Einschrauben in den Ultraschallprüfstand USF-2000A (in Mittellast-Konfiguration) mit ebenfalls geringem Aufwand (Abbildung 2c, 2d).
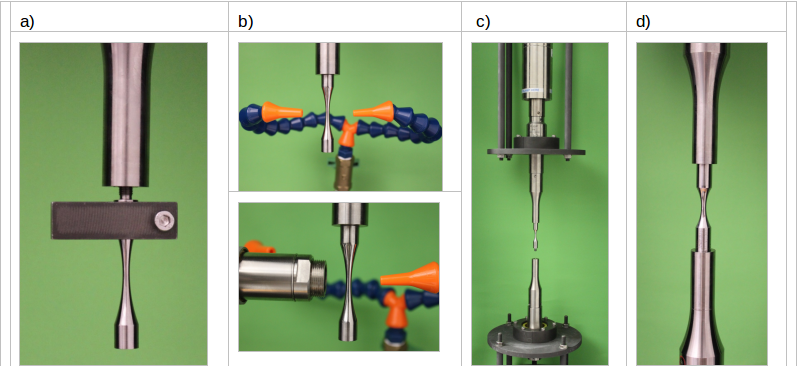
Abbildung 2: (a) Montage der Proben, (b) Druckluftkühlung (oben) und Detektion der Temperaturentwicklung mittels Pyrometer (unten), (c) + (d) beidseitige Montage der Proben im Ultraschallschwingprüfsystem (Mittellast-Konfiguration) Shimadzu USF-2000A
Praktische Anwendung
Die Nutzung der Prüfsysteme USF-2000 (ohne Mittellast) und USF-2000A (mit Mittellast) zur zeit- und ressourceneffizienten Bewertung der Leistungsfähigkeit und Zuverlässigkeit bei hohen und sehr hohen Lastspielzahlen soll anhand eines Beispiels aus dem Innovationsfeld „Additive Fertigung“ verdeutlicht werden. Die Proben wurden hierzu mittels selektivem Laserschmelzen (Selective Laser Melting, SLM) aus Pulver der Aluminiumlegierung AlSi12 hergestellt. Durch Anpassung der SLM-Prozessparameter wurden zwei Chargen I und II annähernd vergleichbarer quasistatischer Festigkeit, aber unterschiedlicher Porosität hergestellt.
Die quasistatische Festigkeit wurde im Zugversuch gemäß ISO 6892-1:2009 ermittelt. Charge I wies mit einer Zugfestigkeit Rm = 372,3 ± 27,2 MPa und Dehngrenze Rp0,2 = 218,0 ± 6,9 MPa eine höhere Festigkeit als Charge II mit Rm = 361,1 ± 4,5 MPa und Rp0,2 = 201,5 ± 3,7 MPa auf. Die relative Dichte der Charge II war allerdings höher. Insbesondere in Gefügeschliffen konnte die Reduktion großformatiger ermüdungskritischer Gasporen für Charge II belegt werden [5-6].
In Abbildung 3 sind Wöhlerkurven für beide AlSi12-Chargen im Bereich hoher bis sehr hoher Lastspielzahlen gezeigt. Die Versuche verdeutlichen, dass Ermüdungsbrüche auch jenseits des HCF-Bereichs (≥ 107 Lastwechsel) auftreten und dass die Ermüdungsfestigkeit von Proben der Charge II um ca. 45 % über der von Charge I liegt.
Diese großen Unterschiede in der Leistungsfähigkeit konnten mittels quasistatischer Versuche nicht bestimmt werden. Charge II würde auf Grundlage der Zugversuche sogar eine niedrigere Leistungsfähigkeit zugeordnet. Lediglich die VHCF-Kennwerte eignen sich als sensitive und zuverlässige Bewertungsgröße für schwingbeanspruchte Werkstoffe und Bauteile. Durch die zeit- und ressourceneffiziente Prüfung wurde dabei zudem eine abgesicherte Ermüdungsfestigkeit für 109 Lastwechsel für Charge I von 60,5 ± 4,7 MPa und für Charge II von 88,7 ± 3,3 MPa ermittelt werden [7].
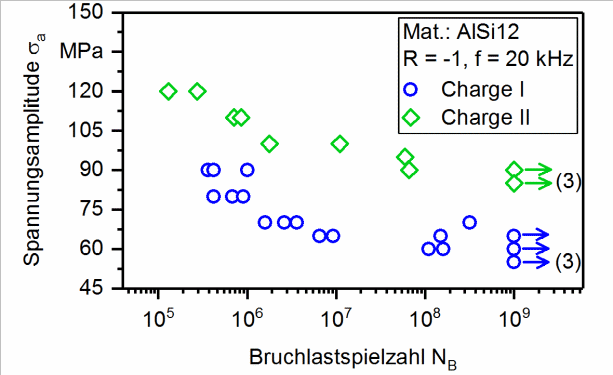
Abbildung 3: Wöhlerkurven für AlSi12-Proben der Chargen I und II [7]
Die Weiterentwicklungen im Bereich der Schwingprüfsysteme ermöglichen heute die detaillierte Untersuchung zyklisch beanspruchter Werkstoffe unter betriebsrelevanten Bedingungen vor dem Hintergrund von Sicherheit und Wirtschaftlichkeit. Durch die Kombination der technischen Möglichkeiten mit Effizienz und Nutzerfreundlichkeit haben Anwender heute neue, sehr leistungsfähige Werkzeuge, um u.a. die Auswirkung unterschiedlicher Wärmebehandlungen, chemischer Zusammensetzungen, Fertigungsparameter und Gefügedefekte und -parameter auf die mechanische Leistungsfähigkeit unter Schwingbeanspruchung in einem breiten Spektrum zuverlässig zu ermitteln.
Referenzen
[1] Pyttel, B.; Schwerdt, D.; Berger, C.: Very high cycle fatigue – Is there a fatigue limit? International Journal of Fatigue
33 (2011) 49-58.
[2] Benedetti, M.; Fontanari, V., Bandini, M.: Very high cycle fatigue resistance of shot-peened high strength aluminium alloys. Experimental and Applied Mechanics 4 (2013) 203-211.
[3] Morrissey, R.J.; Nicholas, T.: Fatigue strength of Ti-6Al-4V at very long lives. International Journal of Fatigue 27 (2005) 1608-1612.
[4] Wycisk, E.; Siddique, S.; Herzog, D.; Walther, F.; Emmelmann, C.: Fatigue performance of laser additively manufactured Ti-6Al-4V in very high cycle fatigue regime up to 109 cycles. Frontiers in Materials 2:72 (2015) 1-8.
[5] Siddique, S.; Imran, M.; Wycisk, E.; Emmelmann, C.; Walther, F.: Influence of process-induced microstructure and imperfections on mechanical properties of AlSi12 processed by selective laser melting. Journal of Materials Processing Technology 221 (2015) 205-213.
[6] Siddique, S.; Imran, M.; Rauer, M.; Kaloudis, M.; Wycisk, E.; Emmelmann, C.; Walther, F.: Computed tomography for characterization of fatigue performance of selective laser melted parts. Materials and Design 83 (2015) 661-669.
[7] Siddique, S., Imran, M., Walther, F.: Very high cycle fatigue and fatigue crack propagation behavior of selective laser melted AlSi12 alloy. International Journal of Fatigue 94, 2 (2017) 246-254.
Kurzangaben zu den Autoren
M.Sc. Jochen Tenkamp, 20.11.1988, wissenschaftlicher Mitarbeiter
M.Sc. Shafaqat Siddique, 22.12.1982, wissenschaftlicher Mitarbeiter
Prof. Dr.-Ing. Frank Walther, 29.08.1970, Institutsleiter
Kontaktperson
M.Sc. Jochen Tenkamp, Tel: (0231) 755 8425, E-Mail: jochen.tenkamp@tu-dortmund.de