1. Einleitung
Die Anwendungsfelder von kunststoffgebundenen (ks.-geb.) Dauermagneten können aktuell primär den beiden Bereichen der Sensorik als Signalgeber und der Antriebstechnik zugeordnet werden. Im Bereich von Motorkonzepten kann unter anderem eine magnetische Anregung von Synchron- oder Gleichstrommaschinen durch den Einsatz von ks.-geb. Dauermagneten erfolgen, da mit Hilfe des Spritzgießprozesses eine hohe Geometriefreiheit ausgenutzt wird [1]. Hierdurch lassen sich bis zu 70 % der weltweiten Produktion von Elektromotoren mit Hilfe des neuen Antriebskonzeptes durch ks.-geb. Dauermagnete realisieren [2,3]. Die neuen Konzepte im Bereich von (A)synchronmaschinen ermöglichen durch die Ausnutzung der Geometriefreiheit eine Verbesserung der Leistung und des Wirkungsgrads, wodurch eine Miniaturisierung sowie eine deutliche Reduktion des Materialeinsatzes erfolgen kann. Aktuell kommen im Bereich von ks.-geb. Dauermagneten, die im Spritzguss gefertigt werden, vornehmlich Thermoplast basierte Matrixsysteme zum Einsatz. Durch den Einsatz von Duroplasten könnte die Medien- und Temperaturbeständigkeit deutlich erhöht werden, wodurch die Anwendungsbereiche von ks.-geb. Dauermagneten vor allem im Bereich der Antriebstechnik auch auf Pumpensysteme und die chemische Industrie erweitert werden könnte [4]. Die hohe Beständigkeit duroplastischer Werkstoffe beruht auf der Vernetzung der Molekularstruktur innerhalb des Duroplasten [5]. Zusätzlich weisen Duroplaste gerade im Bereich des Werkzeuges eine minimale Viskosität auf [6]. Dies kann für eine optimierte Orientierung von anisotropen Füllstoffen genutzt werden, um das magnetische Potential von hartmagnetischen Partikeln vollständig durch eine Ausrichtung zu nutzen und damit die magnetischen Eigenschaften im Bauteil zu erhöhen. Zusätzlich kann das geringe Kriech- und Setzverhalten von Duroplasten gegenüber Thermoplasten positiv bewertet werden [4].
Im Rahmen des Papers wird die Auslegung eines Spritzgießwerkzeuges zur Fertigung von ringförmigen Bauteilen aus einem ks.-geb. Dauermagneten auf Duroplast Basis vorgestellt. Hauptaugenmerk ist hierbei neben der Umsetzung der magnetischen Anforderungen an das Werkzeug durch eine Integration von Dauermagneten und eine entsprechende Werkstoffauslegung der einzelnen Werkzeugkomponenten, die fertigungstechnische Realisierung der Verarbeitung von Duroplast basierten hochgefüllten Compounds durch Auslegung des Angusssystems und der Temperaturführung im Werkzeug.
2. Stand der Technik
2.1. Ks.-geb. Dauermagneten
Ks.-geb. Dauermagnete sind Verbundmaterialien, die aus einer Kunststoffmatrix mit eingebetteten hartmagnetischen Füllstoffpartikeln bestehen. Hierbei können als Matrixmaterial generell Thermoplasten, Duroplasten und Elastomere zum Einsatz kommen [7]. Dabei definiert das Matrixmaterial vornehmlich das Fertigungsverfahren und damit auch die möglichen Anwendungsgebiete durch die zu erreichenden Eigenschaften. Prinzipiell können ks.-geb. Dauermagnete im Pressen und im Spritzguss verarbeitet werden, wobei gepresste Magnete vor allem einen hohen Füllstoffanteil und so höhere magnetische Eigenschaften aufweisen sowie auf einer Duroplast basierten Matrix beruhen [8]. Thermoplast basierte ks.-geb. Dauermagnete werden vor allem im Spritzguss hergestellt und sind durch die Fließfähigkeit in der Schmelze auf einen Füllstoffgehalt von 65 vol.-% begrenzt [9]. Die Herstellung von Duroplast basierten ks.-geb. Dauermagneten im Spritzgießverfahren konnte bereits erfolgreich umgesetzt werden, wie unter anderem in [10] an Hand von ungesättigtem Polyesterharz (UP) und Samarium-Eisen-Nickel (SmFeN) gezeigt wird. Die bisherigen Arbeiten beschränken sich auf Machbarkeitsstudien mit gegensätzlichem Fazit im Hinblick auf den Vergleich zu spritzgegossenen Dauermagneten auf Thermoplast Basis. Hierbei lässt auch die fehlende systematische Untersuchung der Wirkzusammenhänge keinen kommerziellen Einsatz zu. Zudem wurden die Untersuchungen bisher nur an einfachen Geometrien wie Platten durchgeführt [11]. Hinsichtlich des Anwendungsfeldes im Bereich von Sensoren und der Antriebtechnik sind jedoch komplexe Geometrien zentral. Als Füllstoffe werden hauptsächlich keramische Materialien wie z. B. Strontium- oder Bariumferrit (SrFeO, BaFeO) oder Selten-Erd-Werkstoffe wie z. B. Neodym-Eisen-Bor (NdFeB) und Samarium-Cobalt (SmCo) eingesetzt, die sich hinsichtlich der magnetischen Eigenschaften, wie Remanenz BR und Koerzitivfeldstärke HC sowie der möglichen Einsatztemperaturen und der Ausrichtbarkeit im Magnetrichtfeld stark unterscheiden [12]. Die Füllstoff- bzw. Partikelgröße ist grundsätzlich materialabhängig und beträgt bei ferritischen Füllstoffen in der Regel zwischen ca. 1-10 µm und bei NdFeB-Füllstoffe zwischen ca. 100-400 µm. Die Partikelform weist bei anisotropen SrFeO eine hexagonale Struktur und bei isotropen NdFeB eine sphärische Form auf. Anisotropes NdFeB zeigt keine definierte Form, sondern klar abgegrenzte Bruchstücke als Partikel.
Allgemein sind alle Füllstofftypen jeweils magnetisch isotrop und anisotrop erhältlich, wobei die Vorzugsorientierung bei anisotropen Pulvern die Ausrichtung der Partikel in einem Magnetfeld ermöglicht, sofern die Partikel noch beweglich sind und ein magnetisches Moment besitzen. Hierdurch können bis zu 50 % höher magnetische Eigenschaften verglichen zu isotropen Füllstoffpartikeln erreicht werden [14]. Die Partikelform hat unter anderem einen Einfluss auf das Fließ- und Orientierungsverhalten, da zum Beispiel plättchenförmige Partikel aneinander abgleiten können und sich damit in hohem Maße parallel und in Fließrichtung ausrichten [15]. Die Orientierung der Füllstoffpartikel wird demnach nicht nur durch das Fließverhalten des Compounds und hier insbesondere durch den Verlauf der Viskosität des Matrixmaterials über Temperatur und Zeit sowie der Füllstoffgeometrie beeinflusst, sondern auch durch eine mögliche Partikel-Partikel-Interaktion, die vor allem durch den Einsatz von Agglomerat bildenden Füllstoffen und einem hohem Füllstoffgehalt hervorgerufen werden kann. Hierbei neigen insbesondere Partikel mit einer geringen Größe zu einer Agglomeratbildung [16].
2.2 Orientierung der hartmagnetischen Füllstoffe
Die Nutzung des maximalen Werkstoffpotentials magnetisch anisotroper Füllstoffe erfordert eine Ausrichtung der Partikel in der Kunststoffschmelze durch ein definiertes Magnetrichtfeld im Formgebungsverfahren, das durch Elektro- oder Dauermagneten erzeugt werden kann. Dabei kann abhängig von dem hartmagnetischen Füllstoff und der Stärke des Magnetfeldes neben der Ausrichtung auch eine Aufmagnetisierung der Partikel erfolgen. Spritzgießwerkzeuge mit integriertem Magnetrichtfeld müssen somit magnetisch ausgelegt werden. Eine erfolgreiche Integration des Magnetfeldes in ein Spritzgießwerkzeug kann erst durch die Zuordnung von Werkzeugstählen mit definierter Permeabilität für magnetisch leitfähige und isolierende Bereiche innerhalb des Werkzeuges unter Berücksichtigung für das Spritzgießen funktioneller Randbedingungen ermöglicht werden. Um die magnetische Leitfähigkeit für entsprechende Bereiche gezielt herabzusetzen, ist eine Legierung oder eine austenitische Härtung erforderlich. Die notwendige Magnetfeldstärke für eine optimale Ausrichtung der Füllstoffe im Werkzeug unterscheiden sich hinsichtlich des Füllstofftyps und betragen bei Thermoplasten bei SrFeO ca. 160 kA/m und bei SmCo ca. 800 kA/m [17]. Auf Grund des proportionalen Zusammenhangs zwischen der Magnetfeldstärke und der magnetischen Flussdichte ist in der Kavität des Werkzeuges eine Flussdichte von ca. 200 mT für eine Orientierung von SrFeO Partikeln erforderlich [1]. Wichtig ist hierbei, dass die Feldstärke für eine Füllstoffpartikelorientierung insbesondere bei Selten-Erd Füllstoffen deutlich von der Feldstärke zur Sättigungsmagnetisierung abweicht, sodass zusätzlich eine Sättigungsmagnetisierung des Bauteils bei Feldstärken >1600 kA/m notwendig ist [17]. Innerhalb des Orientierungsprozesses der Füllstoffpartikel treten gegenläufige Effekte hinsichtlich Verarbeitbarkeit und magnetischer Eigenschaften auf. Dabei verbessern sich die magnetischen Eigenschaften vollausgerichteter Magnete mit steigendem Füllstoffanteil, die Orientierbarkeit sinkt jedoch bei sehr hohen Füllstoffanteilen aufgrund von Partikel-Partikel-Interaktionen durch eine reduzierte Beweglichkeit der Füllstoffe.
Zur direkten Herstellung von multipolaren Dauermagneten im Spritzgießverfahren gibt es zwei generelle Vorgehensweisen. Zum einen können Magnete mit einer unidirektionaler Füllstofforientierung gefertigt und erst nach dem Spritzgießprozess entmagnetisiert und erneut mit einer multipolaren Magnetstruktur aufmagnetisiert werden. Zum anderen ist die direkte Herstellung von sogenannten polorientierten Magneten möglich, bei denen schon im Fertigungsverfahren eine multipolare Magnetstruktur eingebracht wird. Hierbei werden z. B. Richtmagnete mit wechselnder Polrichtung in das Werkzeug integriert, wodurch die Richtfelder bogenförmig zwischen zwei angrenzenden Magneten verlaufen. Dieses bogenförmige Feld muss dabei eine hohe Überdeckung der Kavität mit geringem Anteil am Streufeld aufweisen, wodurch die Magnete nah der Kavität angeordnet sein müssen. Dadurch können unterschiedliche multipolare und komplexe Polverläufe über die Polwechsel realisiert werden, die z. B. in der Sensorik und Aktuatorik gezielt eingesetzt werden [7]. Unter der Voraussetzung der Magnetisierung der Füllstoffpartikel durch das anliegende Magnetrichtfeld entfällt die Magnetisierung in einem zweiten Prozessschritt.
2.3 Spritzgießen von Duroplast basierten Formmassen
Beim Spritzgießen wird der Kunststoff innerhalb eines Zylinders plastifiziert, dosiert und nachfolgend in die Werkzeugkavität eingespritzt. Thermoplast basierte Matrixsysteme durchlaufen dabei nur eine Phasenänderung innerhalb des Prozesses, wobei das Material nach dem Aufschmelzen durch das kalte Werkzeug erstarrt. Im Gegensatz hierzu wird bei Duroplast basierten Matrixsystemen eine Vernetzung der Polymerketten, also eine zeitabhängige Änderung der chemischen Struktur, durch weitere Aufheizung im Werkzeug erzielt. Durch diese vernetzte Molekülstruktur ist nach dem Aushärten kein erneutes Aufschmelzen möglich [5]. Sowohl in der Aufbereitung als auch im Spritzgießaggregat müssen die Formmassen bei möglichst niedrigen Temperaturen plastifiziert werden und unter hohen Temperaturen im Werkzeug härten. Aufgrund der zunächst noch nicht vorhandenen Vernetzung der Polymere nimmt die Viskosität mit zunehmender Erwärmung ab, wobei gleichzeitig die Vernetzungsreaktion startet, sich aber erst bei hohen Temperaturen mit hoher Geschwindigkeit vollzieht [6]. Damit wird das Minimum der Viskosität im Werkzeug erreicht und kann hier für die Orientierung der Füllstoffe verwendet werden. Das Fließ-/ Härtungsverhalten der Duroplaste ist unter anderem abhängig von der Materialzusammensetzung, der Vorvernetzung, des Temperaturverlaufs und der Zeit. Insbesondere die Werkzeugtemperatur hat hierauf einen großen Einfluss. So kann es geschwindigkeitsbedingt bei höheren Werkzeugtemperaturen zu einer geringeren Viskosität kommen [6]. Das Fließverhalten beim Duroplastspritzgießen entspricht einer Block-Scherströmung, bei der die Fließfront durch einen generell hohen Füllstoffanteil zerklüftet und während der Füllphase unverdichtet vorliegt [6]. Erst nach der volumetrischen Füllung und dem anschließenden Druckaufbau in der Kavität wird das Material verdichtet. Eine dünne niedrigviskose Randschicht ermöglicht allerdings auch eine sehr genaue Abformung der Werkzeugoberfläche. Für die Spritzgießverarbeitung werden rieselförmige, duroplastische Formmassen benötigt, deren Herstellung vorwiegend bei relativ wenigen, chemischen Betrieben in großer Menge stattfindet [18].
3. Anforderungen an das Spritzgießwerkzeug
Aufbauend auf dem Werkzeugkonzept zur Herstellung von multipolaren Ringen auf Thermoplast Basis [19], der Anlagentechnik im Bereich der Duroplastverarbeitung und Vorversuchen im Bereich des Spritzgießens von hochgefüllten hartmagnetischen Compounds auf Duroplast Basis wurden die Anforderungen an das Werkzeug zur Fertigung von multipolaren Ringen auf Duroplast Basis definiert. Es ist zu beachten, dass die Verarbeitung von Thermoplasten und Duroplasten auf einem vollständig anderen Wirkprinzip beruht und daher das bereits bestehende Werkzeug nur im Bereich der Magnetfeldintegration als Grundlage diente. Das multipolare Magnetfeld sollte durch Dauermagnete erzeugt werden und dabei hinsichtlich der Anordnung um die Kavität hauptsächlich den Füllstoff SrFeO bei einem Füllstoffgehalt von bis zu 65 vol.-% in einer Phenolharz- oder Epoxidharzformmasse orientieren. Demnach muss eine Magnetfeldstärke von mindestens 200 mT in der Kavität erreicht werden. Dabei wurde die Geometrie des ringförmigen Probekörpers mit einem Außendurchmesser von 50,6 mm und einem Innendurchmesser von 22,6 mm derart festgelegt, dass durch die Dauermagneten eine Abschwächung des Magnetfelds über den Durchmesser erfolgt und damit der Einfluss auf die Orientierung durch ein sich reduzierendes Magnetfeld über die Probenbreite betrachtet werden kann. Um eine Fertigung von Probekörpern zu gewährleisten, wurde neben der Temperierung der Kavität auf bis zu 200 °C auch eine separate Temperierung des Angusses gefordert. Die geometrische Gestaltung des Angusses wurde auf Basis von Voruntersuchungen derart definiert, dass der minimale Durchmesser des Angusskanals und -kegels 3 mm bei einer Schräge von mindestens 3° beträgt. Weiterhin wurde eine kurze Angusslänge im Bereich von 35 mm gefordert. Die Geometrie des Angusses sowie die separate Temperierung soll ein vollständiges Vernetzen und Entformen in der Fertigung gewährleiten. Um einen Austausch der Komponenten bei einer möglichen ungewollten Vernetzung zu gewährleisten, sollte das Werkzeug modular aufgebaut werden. Weiterhin sollte das Bauteil flächig ausgeworfen werden, um einen Bruch durch einzelne Auswerferstifte bedingt durch das spröde Materialverhalten zu verhindern. Für eine Prozessüberwachung sollten zudem Druck- und Temperatursensoren kavitätsnah integriert werden.
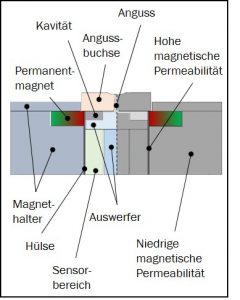
Abbildung 1: Grundlegender Aufbau des Werkzeuges mit Zuordnung der magnetischen Permeabilität der Bereiche als Grundlage für die Simulation
4. Auslegung des Spritzgießwerkzeuges
Die zentrale Anforderung an das Werkzeug war die Integration der Dauermagnete, die auch auf der entsprechenden Wahl der Werkstoffe der einzelnen Komponenten beruht, um einen ausreichend hohen magnetischen Fluss in der Kavität zu erreichen und eine Orientierung der Füllstoffe zu ermöglichen. Hierzu musste insbesondere die Halterung der Magnete und die kavitätsnahen Bereiche sowie das Angusssystem aus einem Werkstoff mit einer geringen magnetischen Permeabilität ausgelegt werden. Neben Ferro-Titanit-Cromoni, der eine aufwändige Verarbeitbarkeit aufweist, eignet sich dafür austenitisch gehärteter Stahl, der eine niedrige magnetische Permeabilität im Bereich von 2 bei 150 °C zusammen mit einer geringen Sättigungsflussdichte aufweist. Durch die Wahl der Stähle im Bereich um die Permanentmagnete und die Kavität wurde sichergestellt, dass das Magnetfeld auf Grund der geringen Permeabilität der Werkstoffe gezielt in die Kavität zur Orientierung der Füllstoffe eingeleitet werden kann. Das zu erreichende Magnetfeld in der Kavität kann zusätzlich durch eine Hülse beeinflusst werden, die den direkten Abschluss des äußeren Probendurchmessers und des inneren Durchmessers der Permanentmagnete bildet. Diese Hülse soll im Rahmen des Werkzeugkonzeptes modular aus drei verschiedenen Werkstoffen mit unterschiedlicher magnetischer Permeabilität gefertigt werden. Die Permanentmagnete des Typs VACODYM 677 HR (Fa. Vacuumschmelze GmbH & Co. KG, Hanau, Deutschland) weisen eine Remanenz von 0,9 T bei 210 °C bei einer Magnetfeldstärke bis 400 kA/m auf. Abbildung 1 zeigt zunächst den allgemeinen Aufbau im kavitätsnahen Bereich mit Zuweisung der Materialien relativ zu einer hohen und niedrigen magnetischen Permeabilität. Es werden dabei nur für den generellen Aufbau relevante Bereiche abgebildet. Das zu erreichende Magnetfeld wurde simulativ mit Hilfe der Software Comsol Multiphysics 5.6 (Fa. COMSOL Multiphysics GmbH, Göttingen, Deutschland) überprüft. Hierbei wurden die einzelnen Werkstoffe hinsichtlich ihrer magnetischen Permeabilität als Grundlage für die Simulation verwendet und ein Quadrant des Probekörpers zur Reduktion der Berechnungszeit ausgewertet. Der Kavität wird dabei das Material Luft zugewiesen, da hier zunächst auf Grund der fehlenden Orientierung eine geringe Permeabilität vorliegt. Die Hülse wird als ein Bereich mit einer hohen magnetischen Permeabilität in der Simulation angesetzt. Den Permanentmagneten wird in der Simulation entsprechend den Angaben des Herstellers eine magnetische Flussdichte zugewiesen. Abbildung 2 zeigt den Verlauf der Feldlinien und den Betrag der magnetischen Flussdichte im Bauteil in Abhängig der Permanentmagnete, die von außen radial um das Bauteil angeordnet wurden. Hierbei zeigt sich in den Randbereichen des Quadranten eine zu vernachlässigende Abweichung des Magnetfeldes bedingt durch die reduzierte Simulation. Die Feldlinien sind hierbei nicht in Abhängigkeit der Magnetfeldstärke, sondern gleichmäßig verteilt. Die magnetische Flussdichte kann der Skala entnommen werden. Die Feldlinien bilden zwischen den Permanentmagneten im Bauteil geschlossene bogenförmige Linien aus. Auf Grund der Polanordnung kommt es zudem zwischen den Magneten in der Halterung zu einem Feldlinienschluss. Abbildung 3 zeigt das magnetische Skalarprodukt ψ im Bauteil, wodurch die Polstruktur verdeutlicht werden kann.
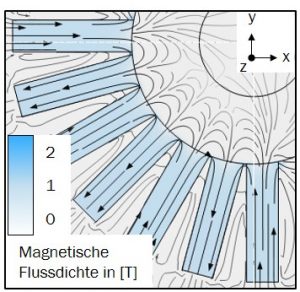
Abbildung 2: Verlauf der magnetischen Feldlinien und magnetische Flussdichte im Bauteil relativ zu Permanentmagneten
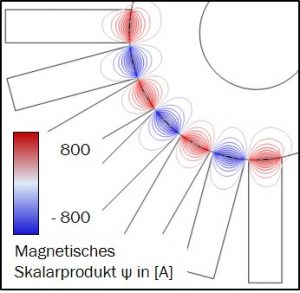
Abbildung 3: Polstruktur in einem Quadranten des Bauteils an Hand des magnetischen Skalarproduktes ψ
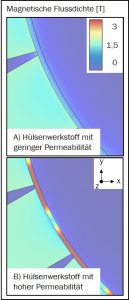
Abbildung 4: Einfluss des Hösenwerkstoffes mit einer niedrigen (A) und hohen (B) Permeabilität auf die magnetische Flussdichte
Um eine Abschätzung machen zu können, bis zu welchem Durchmesser die magnetische Richtfeldstärke im Bauteil ausreichend für eine Orientierung der Füllstoffe ist, wurden Isolinien der magnetischen Feldstärke über das Bauteil entlang des Durchmessers untersucht. Entsprechend zeigt sich, dass eine maximale Orientierung bis zu einem Durchmesser von 40,6 mm erreicht werden kann. Hierdurch konnte das Bauteil entsprechend der Anforderungen in Bereiche mit unterschiedlicher Orientierung unterteilt werden, wobei im Randbereich am Umfang eine maximale Richtfeldstärke von 500 mT bis zu einem Durchmesser von 48 mm erreicht wird. Der Einfluss des Werkstoffes der Hülse ist in Abbildung 4 für eine niedrigen (A) und hohen (B) Permeabilität in der Hülse aufgezeigt. Hierbei kommt es zu einer Erhöhung der magnetischen Flussdichte zwischen den Magneten in der Hülse bedingt durch eine hohe Permeabilität. Die Reduktion der magnetischen Flussdichte in der Hülse durch eine geringe Permeabilität ist deutlich zu verzeichnen. Um eine gezielte Vernetzung des Bauteils und des Angusses zu gewährleisten, werden im Bereich der Kavität vier Heizpatronen mit einer maximalen Manteltemperatur von 750 °C (Fa. Hotset GmbH (Lüdenscheid, Deutschland) verbaut. Diese werden in zwei Ebenen um die Kavität angeordnet, um den Temperatureinfluss auf die Permanentmagnete zu reduzieren und gleichzeitig eine homogene Temperierung der Kavität zu ermöglichen. Weiterhin wird im Bereich des Angusses eine zusätzliche Patrone ringförmig angeordnet, um die Vernetzung im Anguss steuern zu können. Dies gewährleistet eine sichere Entformung des Angusses zusammen mit dem Bauteil. Abbildung 5 zeigt hierbei die Anordnung der Heizpatronen im Bereich des Angusssystems und der Kavität. Zusätzlich sind in Abbildung 4 die beiden Temperatursensoren (Typ: 6192B, Fa. Kistler, Winterthur, Schweiz) abgebildet. Deren Anordnung erlaubt die Überwachung der Temperatur im Prozess radial im Bereich des Angusssystems und angussfern im Bereich der Kavität. Eine Anordnung der Sensoren radial mittig in der Kavität ist auf Grund der Position der Permanentmagneten nicht möglich.
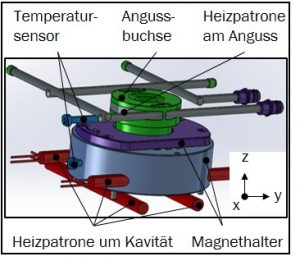
Abbildung 5: Anordnung der Heizpatronen Kavitätsnah und am Angusssystem sowie Position der Temperatursensoren
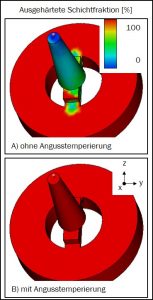
Abbildung 6: Vernetzung im Bauteil in Abhängigkeit der Temperierung des Angusses
Weiterhin werden angussfern drei Drucksensoren (Typ: 6178A, Fa. Kistler, Winterthur, Schweiz) integriert, die derart angeordnet sind, dass über den Umfang betrachtet, der Druck angussnah und angussfern sowie in der Bindenaht aufgenommen werden kann. Hierdurch
kann der Einfluss von Prozessparametern an verschiedenen charakteristischen Positionen im Bauteil ermittelt werden. Bedingt durch die Variation des Angusspunktes durch Wechseleinsätze kann zusätzlich der Druck in der Polteilung oder -mitte erfasst werden. Die Geometrie des Angusses wurde mit einem minimalen Kegeldurchmesser von 5 mm und einer Schräge von 5° definiert. Zusätzlich wurde die Angusslänge auf 34 mm limitiert. Damit werden die Anforderungen an das Angusssystem erfüllt. Ein flächiger Auswerfer wird entsprechend Abbildung 1 realisiert, in dem die Auswerferstifte nicht direkt Kontakt zum Bauteil haben, sondern eine entsprechende Platte bewegen.
Um die Fertigung der Bauteile mit Hilfe der im Werkzeug vorhandenen Temperierung und des Angusssystems sowie die Fließbedingungen zu überprüfen, wurde eine Füllstudie mit Hilfe der Software Moldflow (Fa. Autodesk, San Rafael, USA) durchgeführt. Hierbei wurde als Materialgrundlage das Viskositätsverhalten in Abhängigkeit der Zeit und der Temperatur auf Basis eines Epoxidharzes mit 60 vol.-% SrFeO Füllstoff hinterlegt. Die Prozessparameter innerhalb der Studie wurden mit einer Massetemperatur von 85 °C und einer Werkzeugtemperatur von 180 °C festgesetzt. Hierbei handelt es sich um Standardparameter für ein hochgefülltes hartmagnetisches Compound auf Duroplast Basis. Zunächst kann gezeigt werden, dass erst durch die separate Temperierung des Angusses dessen Vernetzung erfolgt. Abbildung 6 zeigt hierbei den Vernetzungsgrad im Bauteil ohne (Abbildung 6A) und mit (Abbildung 6B) Temperierung im Anguss.
Basierend auf der Simulation wird eine Füllzeit von 20 s und eine Heizzeit von 120 s erreicht. Hierbei kommt es bedingt durch den 2 Punktanguss entsprechend der Abbildung 7 zu einer symmetrischen Bauteilfüllung. Dabei erreicht die Temperatur an der Fließfront einen maximalen Wert von 160 °C im Einspritzprozess.
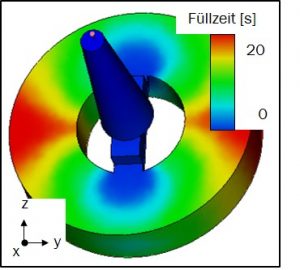
Abbildung 7: Füllstudie
5. Zusammenfassung und Ausblick
Es konnte ein Spritzgießwerkzeug zur Fertigung von multipolaren Ringen auf Duroplast Basis an Hand eines hochgefülltes Compounds ausgelegt werden. Basierend auf den Anforderungen hinsichtlich des Materials und der speziellen Verarbeitung von Duroplasten sowie den magnetischen Eigenschaften im Bauteil wurden die Anforderungen an die Werkstoffe zur Integration des Magnetfeldes und an die Temperierung sowie das Angusssystem definiert. Auf Basis einer magnetischen Simulation konnte die erfolgreiche Integration eines Magnetfeldes zur Orientierung der Füllstoffe an Hand von Permanentmagneten exemplarisch für SrFeO nachgewiesen werden. Mit Hilfe einer Füllstudie konnte weiterhin für 60 vol.-% SrFeO in einer Epoxidharzmatrix gezeigt werden, dass das Konzept der Temperierung und der Geometrie des Angusses eine erfolgreiche Herstellung des Bauteils erlaubt.
Nach Fertigung des Werkzeuges sollen erste Bauteile hinsichtlich der magnetischen Eigenschaften charakterisiert werden, um einen Abgleich zu der Simulation zu ermöglichen. Weiterhin soll eine Prozessparameteroptimierung erfolgen, um zum einen die Heizzeit durch Anpassung der Werkzeugtemperatur zu reduzieren und zum anderen die magnetischen Eigenschaften zu erhöhen.
Referenzen
[1] Drummer, D. Dissertation. Friedrich-Alexander-Universität, 2004.
[2] Buchert, M., Manhart, A. & Suttler, J. Untersuchung zu Seltenen Erden. Permanentmagnete im industriellen Einsatz in Baden-Württemberg. Öko-Institut eV (2014).
[3] Jens Kleinholz. Der Drehstrom-Asynchronmotor. Der am häufigsten gebaute Elektromotor der Welt. Available at https://www.elektro-motoren.org/drehstrom-asynchronmotor/ (2010).
[4] Baur, E., Brinkmann, S., Osswald, T., Rudoplh, N. & Schmachtenberg, E. Saechtling Kunststoff Taschenbuch. 31st ed. (Carl Hanser Verlag, 2013).
[5] Stitz, S. Spritzgießtechnik. Verarbeitung, Maschine, Peripherie. 2nd ed. (Hanser, 2004).
[6] Hoven-Nievelstein, W. Wir bewegen uns in Richtung Spezialitäten. Kunststoffe – Werkstoffe, Verarbeitung, Anwendung 6, 24–29 (2008).
[7] Grönefeld, M. in Magnetwerkstoffe für technische Anwendungen (Haus der Technik e.V., 2014).
[8] Michalowsky, L. & Schneider, J. Magnettechnik. Grundlagen, Werkstoffe, Anwendungen. 3rd ed. (Vulkan Verlag, 2006).
[9] Ehrenstein, G. W. & Drummer, D. (eds.). Kunststoffgebundene Dauermagnete. Werkstoffe, Fertigungsverfahren und Eigenschaften (Springer VDI Verlag, 2004).
[10] Ohmori, K., Hayashi, S. & Yoshizawa, S. Injection-molded Sm-Fe-N anisotropic magnets using unsaturated polyester resin. Journal of Alloys and Conpounds 408, 1359–1362 (2006).
[11] Maenz, T. Dissertation. Technische Universität Chemnitz, 2018.
[12] Brandstetter, F. Kunststoffe – ein reifes Arbeitsgebiet? Kunststoffe – Werkstoffe, Verarbeitung, Anwendung 8, 20–23 (2004).
[13] Schliesch, T. Sensormagnete: Vielfältig gestaltbare Spritzgussteile. Magnete mit virtuoser Polverteilung. Industrieanzeiger, 20 (2010).
[14] Hering, E., Martin, R. & Stohrer, M. Physik für Ingenieure. 12th ed. (Springer Vieweg, 2016).
[15] Otaigbe, J. U., Kim, H. S. & Xiao, J. Effect of Coupling Agent and Filler Particle size on melt rheology of polxmer-bonded Nd-Fe-B Magnets. Polymer composites 20, 607–704 (1999).
[16] Oniku, O. D., Arnold & D.P. High-Energy-Density Permanent Micromagnets Formed from Heterogeneous Magnetic Powder Mixtures. 25th International Conference on Micro Electro Machanical Systems (MEMS).IEEE (2012).
[17] Schliesch, T. in Hochgefüllte Kunststoffe mit definierten magnetischen, thermischen und elektrischen Eigenschaften, edited by G. W. Ehrenstein & D. Drummer (Springer VDI Verlag, 2002), pp. 179–210.
[18] Bonnet, M. Füllstoffe – klein, aber oho! Kunststoffe – Werkstoffe, Verarbeitung, Anwendung 9, 106–111 (2009).
[19] Kurth, K. Dissertation. FAU, 06/2019.
Danksagung
Besonderer Dank der Autoren für die finanzielle Förderung der Arbeiten gilt der Deutschen Forschungsgemeinschaft (DFG) als Fördergeber im Rahmen des Projektes des DFG DR 421/36-1 “Duroplastgebundene spritzgegossene Dauermagneten mit definierter Magnetisierungsstruktur“.
Förderung
Diese Forschung wurde im Rahmen des Projektes “Duroplastgebundene spritzgegossene Dauermagneten mit definierter Magnetisierungsstruktur“ mit dem Förderkennzeichen DFG DR 421/36-1 von der deutschen Forschungsgemeinschaft (DFG) gefördert.
Autoren
Uta Rösel, M.Sc.
E-Mail: uta.ur.roesel@fau.de,
Telefon: 09131/85 71071
Prof. Dietmar Drummer
E-Mail: dietmar.drummer@fau.de