Einsatz coextrudierter Profile
Elastomerprofile werden in vielen Anwendungsfeldern zur Mediendichtung oder Vibrations- und Stoßdämpfung eingesetzt. Um sie in ihrer Form zu stabilisieren und mit anderen Elementen zu verbinden, werden häufig hybride Profile mit harten und weichen Anteilen hergestellt. Durch Kombination der Werkstoffe in einem Produkt können ihre Stärken kombiniert und Schwächen kompensiert werden, z.B. durch Integration elastischer und starrer thermoplastischer Elemente. Bisher können solche Hybride nur in aufwendigen zweischrittigen Verfahren hergestellt werden, die meist auf die Verwendung von kostenintensiven Haftvermittlern angewiesen sind [1]. So werden bei Automobildichtungen z. B. Leisten aus Polyvinylchlorid (PVC) zur mechanischen Unterstützung der Dichtlippen an das Profil geklebt oder verstärkende Stahlbänder mit Kautschuk überzogen [2].
In einem Forschungsvorhaben des Instituts für Kunststoffverarbeitung (IKV) wird die Umsetzung eines Coextrusionsverfahrens untersucht, das eine Herstellung solcher Hybridprofile aus Elastomer und Thermoplast in einem Schritt ohne Haftvermittler ermöglicht. Dazu wird u. a. ein neuartiges Coextrusionswerkzeug entwickelt. Die Stoffströme werden im Werkzeug unter Druck zusammengeführt, so dass ein fester Verbund entsteht. Im Anschluss wird der Kautschuk durch Infrarotstrahlung vulkanisiert, wobei der Thermoplast abgeschirmt wird. In einem ersten Schritt wurden verschiedene Materialkombinationen aus Thermoplasten und Kautschuken hinsichtlich ihrer Verbundhaftung getestet, um deren prinzipielle Eignung für das geplante Vorgehen zu beurteilen.
Herstellung hybrider Profile – State of the Art
Für die Herstellung eines Hybridbauteils mit thermoplastischen und elastomeren Bestandteilen sind derzeit zwei Verfahren verfügbar: das Fügen zweier oder mehrerer Halbzeuge durch Verkleben und das Anfügen einer plastifizierten Komponente an einen bereits verfestigten Partner, z.B. durch Anextrudieren oder Überspritzen [3, 4]. Beim Klebeverfahren werden die Thermoplast- und Kautschukkomponenten zunächst in unabhängigen konventionellen Prozessen hergestellt und durch Abkühlen bzw. Vernetzen verfestigt. Dann werden sie gereinigt, die Fügeflächen vorbereitet und ein Haftstoff aufgetragen. Anschließend werden die Fügepartner unter Druck gefügt. Vorteilhaft daran ist, dass beide Komponenten unter den jeweils optimalen Bedingungen hergestellt werden und dass beim Fügen keine weiteren Temperaturlasten die Bauteilqualität beeinflussen. Nachteilig sind die höhere Durchlaufzeit, das größere Fehlerpotenzial sowie die Umweltbelastung und Zusatzkosten durch den Haftvermittler [1]. Bei dem zweiten Verfahren wird zunächst die Kautschukkomponente extrudiert und vernetzt. Anschließend wird diese einem zweiten Werkzeug zugeführt, in dem mit einem weiteren Extruder die thermoplastische Komponente an das Gummiprofil anextrudiert wird. Auch hier wird ein Haftvermittler benötigt. Des Weiteren kann es beim zweiten Extrusionsschritt zu Lufteinschlüssen kommen [1].
Identifikation von Materialpaarungen für die Coextrusion
Um einen einstufigen Prozess samt neuartigem Werkzeug zu entwickeln, sind zunächst geeignete Materialkombinationen aus Thermoplasten und Kautschuken zu identifizieren, zwischen denen ein wirksamer Haftverbund hergestellt werden kann. Es begünstigt die Haftung, wenn die Kontaktflächen der Fügepartner ähnliche Oberflächenenergien besitzen. Diese besteht aus einem polaren und einem dispersen Anteil. Je stärker die dispersen und polaren Anteile übereinstimmen, desto mehr Wechselwirkungsmöglichkeiten gibt es zwischen den beiden Stoffen, da nur gleiche Wechselwirkungskomponenten eine Verbindung miteinander eingehen [5]. Für die Untersuchungen wurden als Vertreter der Elastomere Ethylen-Propylen-Dien-Kautschuk (EPDM), Acrylnitril-Butadien-Kautschuk (NBR), Hydrierter NBR (HNBR), Liquid Silicone Rubber (LSR), Butadien-Kautschuk (BR), Chloropren-Kautschuk (CR), und Styrol-Butadien-Kautschuk (SBR) und als Vertreter der Thermoplaste Polyphthalamid (PPA), Polyamid 6 (PA6), PA612, Polybutylenterephthalat (PBT), Low-Density Polyethylen (LDPE), Polycarbonat (PC), und Polyphenylensulfid (PPS) ausgewählt, da diese den Großteil möglicher Anwendungsfälle abdecken. Jeder dieser Kunststoffe wurde erst zu einer Platte (85 x 85 x 2 mm³) verpresst und dann seine Oberflächenenergie mittels optischer Kontaktwinkelmessung bestimmt. Anschließend wurden je zwei Platten ausgewählter Materialpaarungen in einer Heizpresse aneinandergepresst. Die Verbundfestigkeit dieser plattenförmigen Materialverbunde aus Thermoplast und Kautschuk wurde am Ende im Zug-Schälversuch zerstörend bestimmt, um die am besten geeigneten Materialpaarungen für den weiteren Projektverlauf zu identifizieren.
Probenherstellung
Für die Kautschukmischungen wurde je eine sehr einfach gehaltene Rezeptur mit Ruß N990, Zinkoxid und einem Peroxid- oder Schwefelvernetzungssystem gewählt. Die Vernetzung der Kautschukplatten erfolgte erst in der Heizpresse beim paarweisen Verbinden der Kautschuk- und Thermoplastplatten. Die Plattenherstellung sowie das anschließende Verpressen zweier Platten erfolgte auf der Heizpresse KV247.01 (Abb. 1) der Rucks Maschinenbau GmbH, Glauchau. Das Silicon wurde mit dem UV-Belichtungsgerät BG 250 der Kent Stuttgart GmbH, Stuttgart-Wangen, vernetzt. Für das Verpressen der Platten aus Thermoplast und unvulkanisiertem Kautschuk zu einem Verbund wurde als Verarbeitungstemperatur die Schmelztemperatur des jeweiligen Thermoplasts gewählt und die Press- und damit Heizdauer so gewählt, dass von einer vollständigen Vernetzung des Kautschuks ausgegangen werden konnte (bis zu 16 min). Der Druck betrug stets 200 bar.
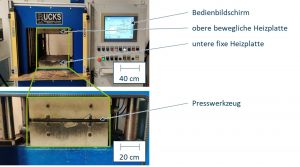
Abbildung 1: Heizpresse KV247.01
Kontaktwinkelmessungen
Mit dem Drop-Shape-Analyzer OCA der Dataphysics Instruments GmbH, Filderstadt, wurden die Oberflächenenergien bestimmt. Als Testflüssigkeiten bekannter Eigenschaften wurden dabei Diiodmethan und Wasser verwendet. Umso ähnlicher die Oberflächenenergien der Fügepartner, desto geringer ist ihre Grenzflächenspannung, was eine bessere Adhäsion erwarten lässt. Silicon zeigte die niedrigste und EPDM die höchste Oberflächenenergie unter den untersuchten Kautschuken (Abb. 2). LDPE wies unter den Thermoplasten die geringste Oberflächenenergie und PA6 die höchste auf. Nur bei wenigen Kunststoffen konnten polare Wechselwirkungen festgestellt werden. Die höchsten polaren Anteile finden sich bei PA6 und CR. Aufgrund ähnlicher Oberflächenenergien wird eine gute Haftung der Paarung LDPE/SBR erwartet.
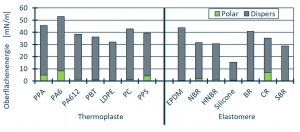
Abbildung 2: Oberflächenenergien aus Kontaktwinkelmessungen
Verbundfestigkeiten verschiedener Thermoplast-Kautschuk-Kombinationen
Mit einem 90°-Schälversuch, angelehnt an die DIN EN 28510-1:2014 DE [6], wurde die Schälfestigkeit der verschiedenen in der Heizpresse gefügten Platten an der Universalprüfmaschine der ZwickRoell GmbH & Co. KG, Ulm, gemessen (Abb. 3).
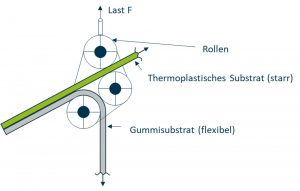
Abbildung 3: Messaufbau des Schälversuchs
In Abbildung 4 ist ein Auszug aus den Messergebnissen dargestellt. Einige Materialpaarungen, wie die mit LSR (Silicon), zeigten gar keine Haftung und ließen keine Messung der Verbundfestigkeit zu. Die Kombination LDPE/ EPDM erreichte die höchste Festigkeit von ca. 17 MPa. Der Wert liegt damit schon in einem vergleichbaren Bereich wie die Festigkeiten bei Metallklebungen, bei denen z. T. noch höhere Werte (> 20 MPa) erreicht werden [7]. Das Ergebnis entspricht nicht der Erwartung basierend auf der Betrachtung der Oberflächenenergien. Während EPDM eine der höchstens Oberflächenenergien besitzt, zeigt LDPE eine der geringsten. Eine gute Haftung der Paarung LDPE/SBR wiederrum wurde als Ergebnis die Kontaktwinkelmessungen prognostiziert. Das Phänomen der Haftung ist sehr komplex und meist nicht durch einen einzelnen Mechanismus definiert. Insbesondere die parallel ablaufende Vernetzungsreaktion des Kautschuks kann einen signifikanten Einfluss auf die Verbindung der Kontaktflächen haben. Ebenso ist eine Reversion des Kautschuks bei langen Heizzeiten nicht auszuschließen. Auch die parallel ablaufende Kristallisationsreaktion kann die Haftung der Fügepartner beeinflussen [5]. Die alleinige Betrachtung der Oberflächenenergien zur Vorhersage des Verbundverhaltens verschiedener Materialpaarungen ist somit unzureichend. Basierend auf den Ergebnissen der Schälversuche lassen sich dennoch die Werkstoffkombinationen LDPE/EPDM und LDPE/SBR als geeignet zur Substitution von Klebeverbindungen ansehen.
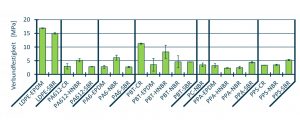
Abbildung 4: Verbundfestigkeiten verschiedener Materialkombinationen
Einfluss der Prozessbedingungen auf die Verbundfestikeit
Für den weiteren Projektverlauf wird zuerst die Kombination LDPE/EPDM genauer untersucht. Mit EPDM- und LDPE Platten wurden zudem der Einfluss von Temperatur (100, 120 °C), Zeit (15, 20, 25 s) und Druck (50, 150, 200 bar) auf den Haftverbund systematisch untersucht. Dabei wurden Druck und Temperatur möglichst den erwarteten Bedingungen im späteren Werkzeug angenähert. Grundsätzlich steigt die Festigkeit mit der Presszeit, -temperatur (vgl. Abb. 5) und dem Pressdruck an (vgl. Abb. 6). Bei
15 s Presszeit und einer Temperatur von 100 °C war die Haftung für das Durchführen eines Schältests zu gering. Der Wert im Diagramm ist daher 0 MPa. Diesen Parametern sind im realen Prozess allerdings Grenzen gesetzt. So führt bspw. eine zu hohe Massetemperatur oder Verweilzeit bis zum Werkzeugaustritt zum Anvernetzen des Kautschuks. Das Druck-Durchsatzverhalten der Extruder sowie die maximal zulässigen Drücke in der Extrusionsanlage limitieren u. a. den Druck im Werkzeug. Während ein Druck von 200 bar sowie eine Massetemperatur von 120 °C in der Fügezone des Coextrusionswerkzeugs realisiert werden können, wird die Zeit nur wenige Sekunden betragen. Daher wird erwartet, dass die Verbundfestigkeit zwar höchstens ca. 10 MPa erreicht, aber die Haftung für einen erfolgreichen Verbund ausreicht.
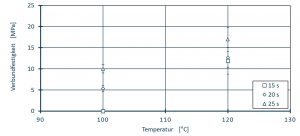
Abbildung 5: Einfluss von Fügetemperatur und -dauer auf die Verbundfestigkeit (200 bar)
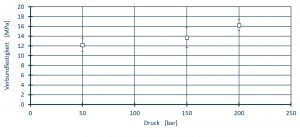
Abbildung 6: Einfluss des Fügedrucks auf die Verbundfestigkeit (25 s; 120 °C)
Vulkanisationsversuche mit Hybridplatten
Mit EPDM-LDPE-Platten wurden abschließend Vulkanisationsversuche im HeatStraD, einem diskontinuierlichen Ofen der Gerlach Maschinenbau GmbH, Nettetal, durchgeführt. Hierbei wurde überprüft, ob die LDPE-Komponente bis zum Ende der Heizzeit des EPDM eine ausreichende Formstabilität behält. Aufgrund der Schmelztemperatur von LDPE (110 °C) ist das Heizen mit Heißluft ausgeschlossen, die mit einem Brenner erzeugt wird und so niedrige Temperaturen nicht erreichen kann. Mit Infrarotstrahlung ließ sich der Kautschuk jedoch vulkanisieren, ohne dass der Thermoplast seine Formstabilität verlor. Dabei wurde die Strahlungsleistung so gewählt, dass der Kautschuk nach wenigen Sekunden 200 °C erreicht und anschließend für zwei Minuten hält. Der Vernetzungszustand wurde jeweils mit der Shore-A-Härte bewertet, die mit dem HPE2 Härtemessgerät der Bareiss Prüfgerätebau GmbH, Oberdischingen, gemessen wurde. Da der in den Plattenpressversuchen ermittelte maximale Wert von 45 Shore-A auch hier erreicht wurde, ist ein vollständiges Vernetzen des EPDM mithilfe von IR-Strahlung demnach möglich.
Im weiteren Verlauf des Forschungsprojekts liegt der Fokus auf der Entwicklung eines Co-Extrusionswerkzeug, in dem LDPE und EPDM zu einem Hybridprofil ausgeformt werden. Dabei ist neben der rheologischen Auslegung insbesondere die thermische Trennung im Werkzeug entscheidend. Als Abschluss des Projekts sind Extrusionsversuche mit dem neuen Werkzeug vorgesehen. Dabei werden die Einflüsse der verschiedenen Prozessparameter von Extrusion und Vulkanisation auf die Extrudateigenschaften wie Verbundfestigkeit und Oberflächenqualität systematisch untersucht. Auf Basis dieses Prozesswissens ist dann eine wirtschaftliche einstufige Fertigung von Thermoplast-Elastomer-Hybridprofile möglich.
Referenz
[1] Vroomen, G.; Köster, L.: Hybrid-Profile aus EPDM und TPV – Herstellung mittels Ein-Schritt-Technologie. Kunststoffe 90 (2000) 8, S. 110-114
[2] N.N.: DE 102007019478 A1: Dichtungsstrang, insbesondere zur Abdichtung von Klappen und Türen an Fahrzeugkarosserien. Offenlegungsschrift, Deutsches Patent- und Markenamt, 06.11.2008
[3] N.N.: DE 197 44 515 A1: Verfahren zur Herstellung eines endlos extrudierten Profilstranges durch Coextrusion unterschiedlicher Materialien und Extrusionsvorrichtung. Offenlegungsschrift, Deutsches Patent- und Markenamt, 15.04.1999
[4] Thust, T.: Rezeptur- und Prozesseinflüsse auf das Haftverhalten beim Mehrkomponentenspritzgießen von Thermoplast-Elastomer-Verbundbauteilen am Beispiel PA6.6 – HNBR. Martin-Luther-Universität Halle-Wittenberg, Dissertation, 2014
[5] Da Silva, L.F.M.; Öchsner, A.; Adams, R.D.: Handbook of Adhesion Technology – Volume 2. Heidelberg: Springer-Verlag Berlin Heidelberg, 2011
[6] N.N.: DIN EN 28510-1:2014-07: Klebstoffe – Schälprüfung für flexibel/starr geklebte Proben – Teil 1: 90°-Schälversuch. Berlin: Beuth Verlag, 2014
[7] Habenicht, G.: Kleben – Grundlagen, Technologien, Anwendungen. Berlin, Heidelberg: Springer-Verlag, 2009
Dank
Das IGF-Forschungsvorhaben 21126 N „Entwicklung eines einstufigen Coextrusionsverfahren zur Herstellung von Hybridprofilen aus einer thermoplastischen und einer elastomeren Komponente“ der Forschungsvereinigung Kunststoffverarbeitung wird über die AiF im Rahmen des Programms zur Förderung der Industriellen Gemeinschaftsforschung und entwicklung (IGF) vom Bundesministerium für Wirtschaft und Klimaschutz aufgrund eines Beschlusses des Deutschen Bundestages gefördert. Allen Institutionen gilt unser Dank.
Autoren
Univ.-Prof. Dr.-Ing. Christian Hopmann ist seit 2011 Inhaber des Lehrstuhls für Kunststoffverarbeitung und Leiter des Instituts für Kunststoffverarbeitung (IKV) in Industrie und Handwerk an der RWTH Aachen.
Fabian Fey, M.Sc. beschäftigt sich mit der Kautschukextrusion am IKV.
Mail: fabian.fey@ikv.rwth-aachen.de
Tel.: 0241 80-28355
Univ.-Prof. Dr.-Ing. Andreas Limper ist als Dozent und seit 2019 zudem als Senior Scientific Adviser Kautschuktechnologie am IKV tätig.
Malte Schön, M.Sc. ist seit 2021 Leiter der Abteilung Extrusion und Kautschuktechnologie am IKV.