Es gibt unterschiedliche fertigungsbezogene Fehlstellen in karbonfaserverstärkten Kunststoffen (CFK) und sie haben meist eines gemeinsam: Die Verminderung der mechanischen Festigkeit. Porosität hat in CFK-Werkstoffen einen wesentlichen Einfluss auf die Übertagung von Schubkräften. Die intralaminare Scherfestigkeit nimmt bis ca. 4 Vol.-% Porosität näherungsweise um ca. 7 % je Volumenprozent ab. Eine präzise Ermittlung des Porositätsgehalts kann daher entscheidend für das Versagen von industriellen Bauteilen sein. Gerade im Bereich der Luftfahrt kann das mit verehrenden Folgen verbunden sein. Großflächige Untersuchungen hinsichtlich der Porosität sind hier sehr wichtig.
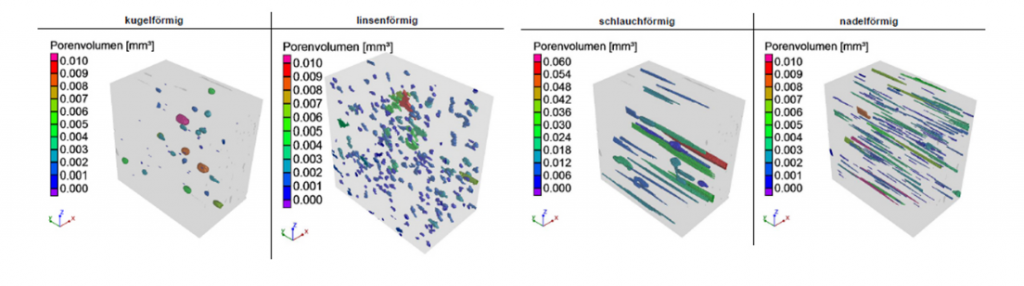
Abb.1: Verschiedene Porenformen in CFK-Werkstoffen
Die Entstehung von Porosität in CFK-Werkstoffen ist auf verschiedene Gründe in der Herstellung zurückzuführen. Sie entsteht häufig durch
- siedendes Harz aufgrund eines zu niedrigen und zu langen Unterdrucks,
- einen zu geringen Autoklaven- oder Pressendruck,
- Reaktionsgase,
- ein fehlerhaft evakuiertes Werkzeug,
- ein feuchtes Laminat.
Porosität kann in CFK verschiedene Formen annehmen (Abb. 1). Die geometrische Porenform ist vom Laminat aber auch der Position innerhalb des Laminats abhängig. Kugelförmige Poren entstehen meist an Kreuzungspunkten zweier Faserbündel in harzreichen Regionen. Linsenförmige Poren sind häufig zwischen zwei Laminatlagen von Prepreg-Gelegen zu finden. Hingegen folgen schlauch- und nadelförmige Poren den Faserbündeln. Letztere sind auch innerhalb einzelner Faserbündel zwischen Filamenten vorhanden. Die CFK-Porosität besteht allerdings aus einem Netzwerk unterschiedlicher Porenvorkommen und schwächt auch im Gesamten den Verbundwerkstoff.
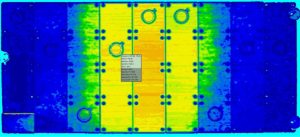
Abb. 2: C-Bild einer Ultraschallmessung einer CFK-Platte mit unterschiedlichen Porositätsstufen
Porosität wird in CFK-Werkstoffen üblicherweise großflächig zerstörungsfrei mit Ultraschalltechniken geprüft. Das hat sich seit Jahrzehnten bewährt. Man unterscheidet bei der Ultraschallprüfung zwei wesentliche Methoden: die Impuls-Echo- und die Transmissionsprüfung. Bei der Transmissionsprüfung wird die Schwächung des Ultraschallsignals durch die Streuung, Absorption oder Brechung beim Durchlaufen des Materials analysiert. Bei der Impuls-Echo-Prüfung wird das Echo des Impulses z. B. an der Bauteilrückwand analysiert. Poren Schwächen das Signal, welche als Rückwandechoverminderung in dB oder dB/mm angegeben wird. Man erhält ein zweidimensionales Bild (C-Bild, Abb. 2) über die Lage von Merkmalen (bzw. Poren) mit zugehöriger Signalschwächung.
Nach festgelegten Grenzwerten wird entschieden, ob es sich um ein Gut- oder Ausschussbauteil handelt. So bleibt bei der Prüfung von CFK-Bauteilen der Luftfahrt kein Millimeter unerfasst. Die Ultraschallprüfung ist ein vergleichendes Verfahren, mit dem der Porositätsgehalt von Porenanhäufungen nur bedingt direkt bestimmt werden kann. Grenzwerte werden selten in der Einheit „Vol.-%“, sondern häufig als zulässige maximale Rückwandechoverminderung definiert. Eine direkte Ermittlung der Volumenporosität ist nicht möglich. Informationen über Porengeometrie, -größe und -verteilung können mit diesem Verfahren nicht gewonnen werden. Gerade bei kostspieligen Bauteilen, dessen Herstellung viel Rohmaterial und Arbeitsleistung erfordert, ist eine hohe Herstellprozessgüte ein wesentlicher Faktor für die Wirtschaftlichkeit des Produkts. Zur Optimierung und auch um bei grenzwertigen Porositätsanteilen eine tiefgehende Untersuchung durchführen zu können, wurden in den vergangenen Jahren neue Methoden zur Porositätscharakterisierung erforscht und entwickelt.
Die Computertomografie ist ein zerstörungsfreies Prüfverfahren welches Bauteilinformationen in dreidimensionaler Darstellung liefert. Bei klassischen industriellen Aufnahmeverfahren der Computertomografie wird das Bauteil um eine Rotationsachse mit 360° gedreht. Teilweise werden Röntgenprojektionen aus tausenden von Winkelpositionen aufgenommen, welche z. B. mit einem Feldkamp-Davis-Kress-Algorithmus zu einem dreidimensionalen Volumen rekonstruiert werden können. Die Voxel (Volumen-Pixel) erhalten – bezogen auf die zugehörige Röntgenstrahlschwächung des Materials – einen Grauwert. Die Schwächung von Röntgenstrahlung ist dichteabhängig. Eine hohe Materialdichte führt in CT-Daten zu einem hohen Grauwert. So können die einzelnen Bestandteile eines Bauteils oder Materials analysiert werden. In CFK-Werkstoffen können so die Poren vom Faser/Harz-System segmentiert werden.
Man gewinnt detaillierte Informationen zur Volumenporosität, der Porenverteilung und auch geometrische längenbezogene Größen in allen Raumrichtungen oder auch über Oberfläche und Volumen einzelner Poren. Porosität kann so dreidimensional untersucht und bewertet werden, was Bauteile vor dem Ausschuss retten und zur Wirtschaftlichkeit beitragen kann. Eine Einschränkung gibt es jedoch hinsichtlich der maximal zu untersuchenden Bauteilgröße und demzufolge der Datenmengen. Porositätsanalysen erfordern hochaufgelöste CT-Messungen. Ein Voxel ist für zuverlässige Porositätscharakterisierungen unter 20 µm zu wählen. Die Analyse von zwei Kubikzentimeter Werkstoff resultiert in einer Datenmenge von ca. 2 GByte. Es wird u. a. aus diesem Grund deutlich, dass es aktuell nicht praktikabel wäre, die CT-Prüfung von Kohlefaserverbundwerkstoffen auf große Komponenten auszudehnen. Sie kann jedoch als ideale Ergänzung zu den bekannten Ultraschallverfahren und als sogenannte Eskalationsmethode genutzt werden. Bauteilbereiche mit grenzwertig hoher Porosität können damit tiefergehend untersucht werden. Ebenso ist es möglich mit der CT unklare Anzeigen, also Merkmale mit nicht eindeutig zuzuordnenden Eigenschaften, aufzuklären und so die Ergebnisse anderer Prüfverfahren zu verifizieren.
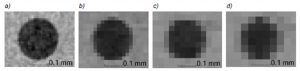
Abb. 3: Schnittbilder von CT-Aufnahmen zur Veranschaulichung des Partialvolumeneffekts anhand einer kugelförmigen Pore mit den Voxelgrößen a) 10 μm, b) 20 μm, c) 30 μm und d) 40 μm.
Bei der Auswertung der geometrischen Eigenschaften einzelner Poren oder der Volumenporosität müssen sie von dem umgebenden Material segmentert werden. Es gibt unterschiedliche Ansätze zur Segmentierung. Als einfachste Methode gilt, die Daten nach dem Grauwert zu unterscheiden. Da Poren aus Gaseinschlüssen bestehen und eine im Vergleich zum CFK-Material geringere Dichte aufweisen, können die niedrigen Grauwerte vom Material getrennt werden. Die Schwellwertbestimmung kann z. B. an einer bekannten und porenfreien Probe durchgeführt werden. Der Vorteil dieses Segmentierungsverfahrens ist die unkomplizierte, einfach anzuwendende und konservative Verwendung einer Vergleichsprobe. Nachteilig ist jedoch, dass inhomogene Grauwertverteilungen zu Fehlsegmentierungen führen können. Regionen mit inhomogenen Grauwerterteilungen finden sich in komplexen Proben- bzw. Bauteilgeometrien. Sie entstehen durch meist unvermeidbare Artefakte bei der CT-Messung. Um dennoch zuverlässige Analysen durchführen zu können, verwendet man lokaladaptive Segmentierungsverfahren. Hier werden Objektkanten mittels eines Algorithmus unabhängig von der globalen Grauwertverteilung und innerhalb eines Grauwertdifferenzbereichs lokal und adaptiv zum Grauwertlevel ermittelt. Man benötigt also keine porenfreie Referenzprobe und kann auch in Bereichen inhomogener Grauwertverteilungen Poren segmentieren. Diese Segmentierungsmethode findet heute schon in vielen Bereichen Anwendung. Nachteilig ist jedoch die Notwendigkeit für eine zum Vergleich mit der Referenzmethode eher hohe notwendige Auflösung der Computertomografiedaten.
Diese Auflösung ist ein entscheidender Parameter der Porensegmentierung. Sie setzt sich im Wesentlichen aus der Voxelgröße, geometrischen Unschärfe und der inneren Unschärfe des Detektors zusammen. Als Voxelgröße ist der Abstand zwischen zwei Punkten definiert, mit welchem ein Objekt abgetastet wird. Mit zunehmend größerer Abtastung nimmt die Detailerkennbarkeit eines Objekts ab und somit auch eine potentielle Fehlsegmentierung zu (Abb. 3).
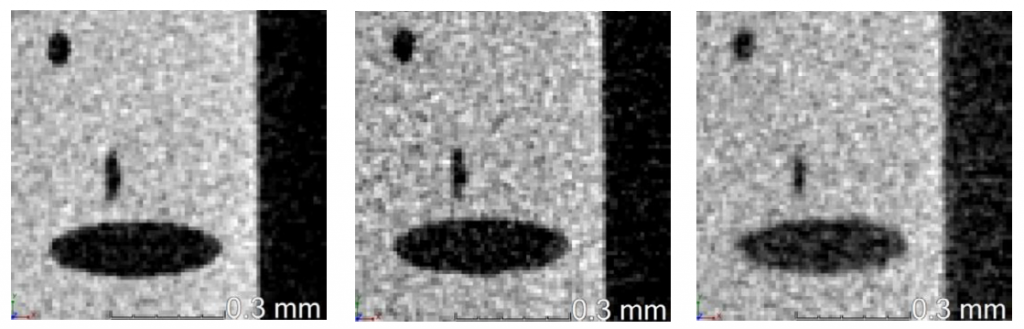
Abb. 4: Schnittbilder von CT-Aufnahmen mit den Fokusgrößen
a) 0 µm, b) 10 µm und c) 30 µm.
Die geometrische Unschärfe kann ebenfalls einen negativen Einfluss auf die Auflösung haben. Röntgenstrahlen werden an einem sog. Fokuspunkt emittiert und durchdringen das Objekt bis sie am Detektor auftreffen, wo dessen Intensität in ein elektrisches Signal gewandelt wird. Da der Fokuspunkt auch aus Gründen der Wärmeabfuhr nicht beliebig klein ausgelegt werden kann, geht aus ihm zusammen mit der zu erzielenden geometrischen Vergrößerung des Objekts auf dem Detektor auch eine geometrische Unschärfe einher. Die Wahl der Fokusgröße muss daher kleiner als die Voxelgröße gewählt werden. Abweichungen hierzu führen zu unscharfen Aufnahmen mit Fehlern in der Segmentierung (Abb. 4).
Neben den bislang genannten Einflussgrößen gibt es eine Reihe weitere Parameter, die für eine zuverlässige Porositätscharakterisierung zu beachten sind. Die explizite Untersuchung zur Qualifizierung eines neuen Charakterisierungsprozesses kann mit experimentellen Ansätzen aufwändig und teuer sein. Man verwendet deswegen – analog zur Finite-Elemente-Simulation in der Werkstoffprüfung – numerische Simulationen von zerstörungsfreien Prüfmethoden. Eine gängige Simulationsmethode für die Röntgen-CT-Prüfung ist das Ray-Tracing-Verfahren. Ausgehend vom Fokuspunkt werden sämtliche Intensitätsschwächungen einem Röntgenstrahl auf einen Detektorpixel folgend numerisch oder analytisch berücksichtigt. Das wird Pixel für Pixel durchgeführt, wodurch simulierte Röntgenaufnahmen entstehen. Verschiedene Röntgenspektren, die Detektorsensitivität, innere Unschärfe des Detektors, gemoetrische Unschärfe und viele weitere Einflussgrößen können mit modernen Simulationstools berücksichtigt werden. Der Zufallsprozess der Erzeugung, Schwächung und Detektion von Röntgenstrahlen kann über Monte-Carlo-Simulationen angenähert oder über ein synthetisches Rauschen hinzugefügt werden. So entstehen realitätsgetreue Simulationen, die auf beliebige Bauteilgeometrien angewendet werden können. So kann beispielsweise in der Designphase eines Bauteils geprüft werden, ob eine Pore bestimmter Größe in einer bestimmten Region gefunden werden kann oder nicht. Mit dieser wertvollen Erkenntniss kann entweder das Bauteildesign überarbeitet oder die Methode für die zerstörungsfreie Bauteilprüfung angepasst werden.
Bei industriellen Röntgen-CT-Verfahren wird atuell meist eine kleine Probe eines Bauteils unersucht. Die Probe kann z. B. durch hohllochgebohrten Nietbohrungen gewonnen werden. Zerstörungsfreie Prüfungen an einem schwer zugänglichen Bauteilbereich oder die CT-Prüfung an großen Komponenten wie z. B. einer Tragfläche oder einem Rumpfsegment können damit nicht durchgeführt werden. Derzeit werden für solche Applikationen komplexere Systeme entwickelt. Mithilfe von Robotern, welche zum einen die Röntgenröhre und zum anderen den Detektor bewegen, können aufwändige Trajektorien gefahren werden, die eine Volumenrekonstruktion ermöglichen. Im Vergleich zur klassischen CT erfolgt keine 360°-Rotation um das Objekt, sondern es werden Aufnahmen aus vielen verschiedenen Blickwinkeln aufgenommen. Hieraus lässt sich ähnlich wie mit der konventionellen CT eine räumliche Auflösung von Materialmerkmalen erzielen. Besonders vorteilhaft kann das für Luftfahrtbauteile in der Fertigung oder auch für die Service-Inspektion sein, eine ganze Reihe von weiteren Anwendungen beispielsweise im Automobilbau ist aber ebenfalls möglich. Gelingt es die großen Datenmengen („Big Data“) automatisiert zu verarbeiten, wird dies den Anwendungsbereich der CT-Prüftechnik deutlich erweitern.
Autoren:
Dr.-Ing. Denis Kiefel, TESTIA GmbH
Prof. Dr.-Ing. habil. Dipl.-Geophys. Christian Grosse, TU München
TESTIA GmbH
Airbus Allee 1, 28199 Bremen