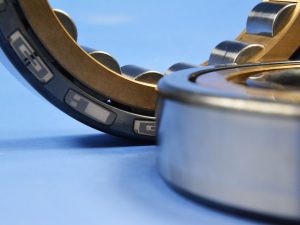
Wälzlager mit aufgedruckten und lasergesinterten Sensoren zur Dehnungs- und Körperschallmessung.
Keramische Werkstoffe erfüllen heute in den verschiedensten Anwendungen zuverlässig ihre Aufgaben. Ihr Eigenschaftspotenzial kommt vor allem bei komplexen Anforderungen zum Tragen, wo andere Werkstoffe deutliche Defizite aufweisen. So werden Hochleistungskeramiken u. a. in verschleiß- und temperaturkritischen Bereichen von Maschinen und Anlagen eingesetzt. Sie werden ständig weiter entwickelt und besitzen mittlerweile Eigenschaftsprofile, die vor wenigen Jahren noch undenkbar waren. Dazu tragen wesentlich die immer weiter spezialisierten Herstellungsverfahren und maßgeschneiderten Rohstoffe bei.
Keramische Pasten für lasergesinterte Sensoren auf Stahlbauteilen
Die keramische Dickschichttechnik wird typischerweise zum Aufbau funktioneller Schichten z. B. für keramische Schaltungsträger oder Sensoren verwendet. Die Technologie verarbeitet Pasten und basiert auf dem typischen Prozessablauf Siebdruck – Trocknung – Einbrand. Die Abscheidung der benötigten Funktionspasten ist bisher allerdings technologie- und anlagenbedingt auf kleinere Substratkörper beschränkt.
Den Fraunhofer-Instituten IKTS, ILT und IZM ist es nun erstmals gelungen, Sensorschichten direkt auf große 3D-Stahlbauteile aufzubringen. Dafür werden moderne 3D-Druckverfahren, wie Dispensen oder Aerosol-Jet-Druck, und statt der üblichen Ofenprozesse schnelle Laserprozesse genutzt, um die benötigten Funktionsschichten zu versintern. Damit lassen sich Isolations-, Leiterbahn-, Widerstands- und piezokeramische Schichten auf massiven Stahlbauteilen (1.4016, 1.3035) abscheiden und so Dehnungs-, Temperatur- und Körperschallsensoren realisieren. Im Mittelpunkt dabei stehen Pastensysteme, die hinsichtlich ihrer Absorptionseigenschaften und ihrer Schwindung sowie weiterer Schichteigenschaften aufeinander abgestimmt werden. Aufgrund der deutlich verkürzten Wechselwirkungszeiten bei der Laserbearbeitung zeigen besonders piezokeramische Pasten im Schichtaufbau mit Stahl sowie Isolations- und Elektrodenschichten deutlich verbesserte Materialeigenschaften gegenüber ofengesinterten Aufbauten.
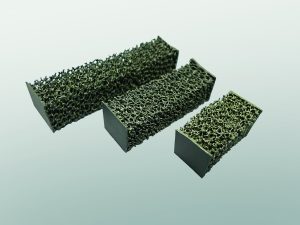
PTC-Heizer aus zellulärer Keramik in Sandwichbauweise zur einfachen Kontaktierung.
Zelluläre Keramiken für PTC-Heizer
Zelluläre Keramiken können gezielt mit einer großen Variabilität an Zellgröße und Zellform hergestellt werden. Aufgrund dieser besonderen Struktur lassen sie sich als Filter, Katalysatoren, Brenner oder auch Heizelemente einsetzen. Selbstregelnde PTC-Heizelemente (Positive Temperature Coefficient) finden beispielsweise in Automobil-Zuluftheizungen oder als Heizer für Haushaltsgeräte in großen Stückzahlen Anwendung. Aufgrund ihrer Bauweise – meist Stifte, Plättchen, Ringe oder Waben – ist allerdings nur ein geringer Wärmeübergang an das zu beheizende Medium möglich, was derzeit durch aufwändige Kombinationen mit metallischen Wärmetauschern kompensiert wird.
Am Fraunhofer IKTS wurden daher selbstregelnde Heizkomponenten aus zellulären Keramiken auf Basis von selbst synthetisierten bleihaltigen und bleifreien Bariumtitanat-Pulvern mit Sprungtemperaturen von 45 °C, 100 °C und 120 °C entwickelt. Ihre zelluläre Struktur ermöglicht große geometrische Oberflächen und somit einen hohen Wärmeübergang an zu beheizende Medien, wie Gase oder Flüssigkeiten. Diese Medien können die Heizerstruktur direkt und allseitig durchströmen, was eine schnelle und präzise Temperierung ermöglicht. Durch den direkten Kontakt kann auf zusätzliche Wärmetauscher weitgehend verzichtet werden, wodurch sich besonders kompakte Heizer bauen lassen. Der Aufbau der Heizer in Sandwichbauweise ermöglicht eine einfache elektrische Kontaktierung, die in der Herstellung leicht und flexibel anpassbar und dadurch auch in kleinen Serien rentabel ist. Weiterhin kann die Keramik mit Epoxidharz beschichtet werden. Dies gewährleistet eine Inertisierung des Materials gegenüber durchströmenden Medien und verhindert im Falle einer mechanischen Beschädigung den Eintrag von PTC-Material in das durchströmende Medium.
Die entwickelten Bauteile zeigten bei der Normprüfung nach DIN EN 60738-1 (06/2010) keine signifikanten Änderungen im Widerstandsverhalten nach 1000 bzw. 50 000 Schaltzyklen in kalter Umgebung und bei Raumtemperatur sowie im Dauerbetrieb (1000 h) bei höchster Betriebstemperatur (70 °C) und höchster Betriebsspannung (30 V).
Keramische Suspensionen für Abrasions- und Korrosionsschutzschichten
Keramische Beschichtungen können die Oberflächenbeständigkeit und -güte von Maschinenkomponenten entscheidend verbessern, beispielsweise hinsichtlich Verschleißschutz, Antihaftwirkung oder Isolationsverhalten. So dienen Al2O3-Schichten der Verbesserung der elektrischen Isolation, während Cr2O3-Schichten Metallbauteile wirksam gegen Korrosion schützen und Hartmetallschichten für den Verschleißschutz unabdingbar sind.
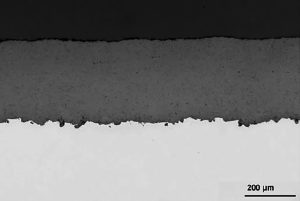
REM-Aufnahme einer Al2O3-Schicht auf Stahlsubstrat, hergestellt durch thermisches Spritzen einer Suspension (Quelle: Fraunhofer IWS).
Insbesondere thermische Beschichtungsverfahren, wie das Atmosphärische Plasmaspritzen (APS) oder Hochgeschwindigkeitsflammspritzen (HVOF), kommen hier bislang zum Einsatz. Auf Basis von keramischen oder metallischen Pulvern können Schichten zwischen 100 und 500 μm appliziert werden. Die verwendeten Pulverpartikel sind zwar fein und die Schicht dünn – trotzdem weist eine solche Oberfläche eine hohe Rauheit auf. Um eine gezielte Oberflächengüte zu erreichen, müssen die beschichteten Bauteile daher oftmals aufwendig mechanisch nachbearbeitet oder versiegelt werden. Um dies zu vermeiden, haben die Fraunhofer-Institute IKTS und IWS gemeinsam ein thermisches Beschichtungsverfahren weiterentwickelt: An Stelle des Pulvers wird eine Suspension verspritzt, die deutlich feinere Partikel als die üblichen Spritzpulver enthält. Dies bietet entscheidende Vorteile, da sich so dünne (< 100 μm) und dichte Schichten mit sehr glatten Oberflächen herstellen und zusätzlich noch Rohstoffe einsparen lassen. Die Schichteigenschaften werden zum einen von den Prozessparametern beim thermischen Spritzen und zum anderen von den Eigenschaften der Suspension bestimmt. Um die Effizienz des Spritzprozesses zu gewährleisten, muss die Feststoffkonzentration der Suspension mindestens 25 Ma.-% betragen. Gleichzeitig sollte die Suspension für einen stabilen Spritzprozess homogen sein und eine geringe Viskosität besitzen, um eine gute Förderfähigkeit zu garantieren. Demnach liegt die Voraussetzung für die Entwicklung einer solchen hochwertigen Spritzsuspension in der Auswahl geeigneter Rohstoffe sowie in der Einstellung der Suspensionseigenschaften. Materialien mit homogenen Partikelgrößenverteilungen und hoher Reinheit sind besonders geeignet, um daraus Suspensionen für Schutzschichten herzustellen. Die Suspensionseigenschaften lassen sich unter Verwendung von elektroakustischer, rheologischer und Sedimentations-Messtechnik hinsichtlich Feststoffgehalt, Korngrößenverteilung und Viskosität für jede Anwendung individuell einstellen und optimieren. Neben den unterschiedlichen keramischen Werkstoffen wie Chrom-, Aluminium- oder Zirkonoxid können erstmals auch Hartmetalle defektfrei thermisch gespritzt werden. Außerdem erlaubt die Technik gradierte Schichtsysteme, mit denen zum Beispiel thermische und mechanische Eigenschaften kombiniert werden können.
Fraunhofer-Institut für Keramische Technologien und Systeme IKTS
Susanne Freund
Winterbergstraße 28
01277 Dresden
Telefon +49 351 2553-7504
Fax +49 351 2554-334
susanne.freund@ikts.fraunhofer.de
www.ikts.fraunhofer.de