Verbundfestigkeit und Haftung der Lackfilme
Eine hohe Haftfestigkeit ist eine grundlegende Voraussetzung für die Funktion und Langlebigkeit von Beschichtungen. Die Haftfestigkeit von Lackfilmen auf Kunststoffbauteilen besteht in der Wirkung von Anziehungskräften zwischen verschiedenen Stoffen (Adhäsion). Diese Adhäsionskräfte sind abhängig von der Benetzung des Bauteils durch den flüssigen Lack, der Art der entstehenden Wechselwirkungen in der Grenzfläche und den daraus resultierenden, meist zwischenmolekularen Bindungen.
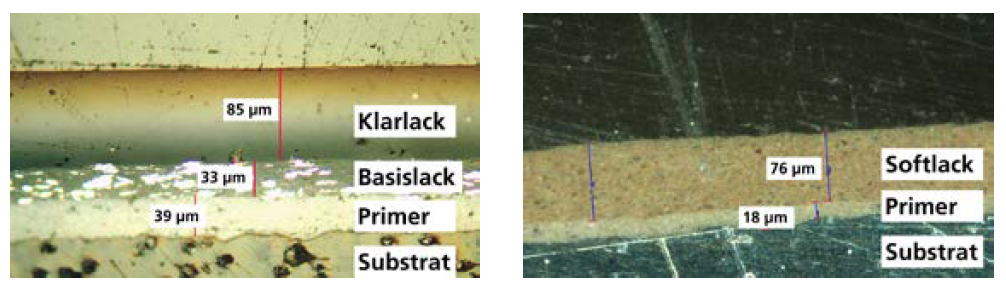
Abbildung 1: Aufnahmen mittels Lichtmikroskop – typischer Lackaufbau, links Exterieurbauteil, rechts Interieurbauteil, Bildquelle: Fraunhofer IPA
Es gibt einige Faktoren sowohl in der Entwicklungsphase als auch im späteren Fertigungsablauf, die Einfluss auf die Haftfestigkeit nehmen können. Bei der Materialauswahl ist darauf zu achten, dass das Kunststoffsubstrat und das Lacksystem aufeinander abgestimmt sind. Dies betrifft nicht nur die Benetzbarkeit im Lackierprozess, sondern auch die grundlegende Verträglichkeit der Materialien. Ein Kunststoffsubstrat kann ungeeignet für eine Lackierung sein, wenn es Additive wie Weichmacher oder innere Trennmittel enthält, die stark ausdiffundieren. Einige Kunststoffe reagieren empfindlich auf bestimmte Lösemittel, die im Lack enthalten sind. Die Lösemittelempfindlichkeit muss auch bei der Reinigung der Kunststoffteile vor dem Lackieren berücksichtigt werden. Die meisten Kunststoffe werden vor einer Lackierung aufgrund ihrer niedrigen Oberflächenenergie und/oder ihrer geringen Polarität einer Oberflächenaktivierung unterzogen. Gängige Verfahren sind z. B. das Beflammen, die Corona-Behandlung, die Plasmaaktivierung oder Fluorierung. Die optimalen Parameter müssen in Versuchen ermittelt werden. Nicht alle Vorbehandlungsmethoden sind langzeitstabil (z. B. Beflammen, Corona), d. h. der Lackierprozess sollte bei diesen Verfahren unmittelbar nach der Oberflächenaktivierung erfolgen. Die festgelegten Parameter bei der Lackapplikation müssen eingehalten werden. Beim Aushärten/Trocknen des Lacksystems (siehe Abbildung 1) ist die Temperaturempfindlichkeit des Kunststoffbauteils zu berücksichtigen. Wichtig in der gesamten Prozesskette sind die Lagerungsbedingungen, der Transport und das Handling der Rohteile, wie z. B. eine saubere Umgebung oder die Entnahme der Bauteile mit sauberen Handschuhen.
Aus einer Vielzahl von Haftfestigkeitsprüfungen (eine umfangreiche Zusammenstellung von Prüfungen gibt es z. B. im DIN-Taschenbuch 482 „Haftfestigkeit von Beschichtungen“) haben sich einige Prüfverfahren insbesondere im Automobilbereich stark etabliert. Nachfolgend werden die drei wichtigsten Haftfestigkeitsprüfungen, die Gitterschnittprüfung, der Dampfstrahltest und die Multisteinschlagprüfung detailliert vorgestellt.
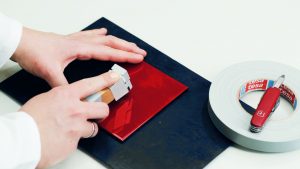
Abbildung 2: Durchführung der Gitterschnittprüfung Bildquelle: Fraunhofer IPA
Gitterschnittprüfung
Die Gitterschnittprüfung ist die am häufigsten eingesetzte Haftfestigkeitsprüfung in der Lackiertechnik. Vorteile, wie die einfache Handhabung, schnelle Durchführung, ein geringer apparativer Aufwand, niedrige Investitionskosten, ein breiter Einsatzbereich als Tascheninstrument und die hohe Akzeptanz sprechen für die Beliebtheit dieser Prüfmethode. Die Gitterschnittprüfung ist in der DIN EN ISO 2409 detailliert beschrieben. In die Beschichtung wird ein durchgehendes Gitter bis zum Substrat geschnitten (siehe Abbildung 2). Je nach Anwendungsbereich, Beschichtungseigenschaft und Substratmaterial werden in der Norm unterschiedliche Schneidwerkzeuge, Schnittanzahlen und -abstände empfohlen. In der Automobilindustrie werden nach Möglichkeit Mehrschneidengeräte mit 6 bzw. 11 Klingen verwendet. Zusätzlich wird ein Klebebandabriss, mit einem vorgegebenen Klebeband, in die jeweilige Richtung der Schnitte durchgeführt. Die Auswertung des erzeugten Gitterschnitts erfolgt visuell durch Vergleich mit Referenzbildern und wird in Form von Gitterschnitt-Kennwerten zwischen 0 und 5 angegeben (siehe Abbildung 3).
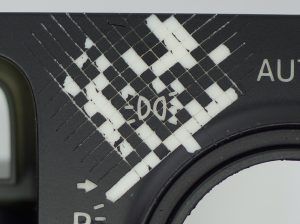
Abbildung 3: Gitterschnitt nach Klebebandabzug mit n.i.O.-Bewertung (Gt-Kennwert 4), Ablösung des Lackes vom Substrat, Bildquelle: Fraunhofer IPA
Was gibt es bei der Durchführung der Gitterschnittprüfung mit einem Mehrschneidengerät zu beachten? Zunächst einmal hat die Auswahl der Prüfstelle am Bauteil einen entscheidenden Einfluss auf das Ergebnis. Kenntnisse über die Rohteilherstellung bzw. -bearbeitung und den anschließenden Lackierprozess sind von Vorteil. Bei spritzgegossenen Kunststoffteilen liegen die Schwachstellen meist im Bereich der Angüsse und Kanten. Oftmals weist die gewünschte Prüfstelle oder das ganze Bauteil keine plane Oberfläche auf. Diese ist möglicherweise konvex gewölbt oder kleiner als in der Prüfvorschrift vorgegeben (z. B. Airbagabdeckungen, Türgriffe, Bedienknöpfe). Die Ausführung der Gitterschnittprüfung mit dem Mehrschneidenmesser auf solchen Bauteilen erfordert viel Übung und eine gewisse Geschicklichkeit, um reproduzierbare Gitterschnitte zu erhalten. Hier ist es kaum möglich, mit einem Schnittvorgang überall eine gleiche Schnitttiefe zu erzielen. Die Schnittlinien müssen vorsichtig nachgefahren werden, bis alle Schnitte gleich tief sind. Die Schnitttiefe kann wiederum einen Einfluss auf das Ergebnis haben. Optimalerweise durchdringt die Klinge beim Schneidvorgang die Lackschicht(en) ohne den Untergrund zu beschädigen, was sich bei der Vielzahl an unterschiedlich harten Kunststoffuntergründen und Lackmaterialien als äußerst schwierig erweist. Ein zu tiefes Eindringen der v-förmigen Klingen übt eine zusätzliche Belastung auf die Oberfläche aus, verdrängt das Substratmaterial nach oben und verfälscht somit das Ergebnis. Eine weitere Fehlerquelle liegt in der Durchführung des Klebebandabzugs. Das Abziehen des Klebebands übt eine Zugbelastung auf die Beschichtung aus, die von dem Abzugswinkel, der Abzugsgeschwindigkeit und dem vorangegangenen Anpressverfahren beeinflusst wird. Hinzu kommt, dass bei der Vielzahl an Lacksystemen trotz Reinigung der Oberfläche nicht immer die gewünschte Haftkraft des Klebebands auf dem Bauteil erreicht werden kann.
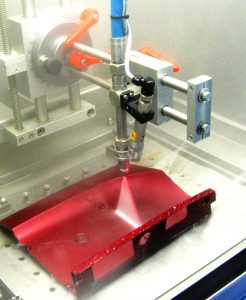
Abbildung 4: Dampfstrahltest zur Bestimmung der Haftfestigkeit von Beschichtungen, Bildquelle: Fraunhofer IPA
Dampfstrahltest
Ein sehr realitätsnahes Prüfverfahren im Exterieur-Bereich stellt der Dampfstrahltest dar (siehe Abbildung 4). Bei dem Test wird das Reinigen eines Automobils mit einem Dampfstrahlreiniger simuliert. Das Prüfverfahren basiert auf der DIN EN ISO 16925 und ist fester Bestandteil von Prüfvorschriften der OEM’s (Original Equipment Manufacturer) bei der Bemusterung von Exterieur-Anbauteilen. Die Oberfläche einer beschichteten Probe wird durch Einritzen eines Andreaskreuzes bis zum Substrat verletzt und anschließend mit einem definierten Druckwasserstrahl auf ihre Haftfestigkeit geprüft. Die Auswertung erfolgt anhand eines visuellen Vergleichs mit Bildern, wobei den abgelösten Flächen Kennwerte zwischen 0 und 5 zugeordnet werden (siehe Abbildung 5). Wesentlichen Einfluss auf das Ergebnis haben die Parameter Volumenstrom, Druck, Temperatur und Sprühzeit. Das Dampfstrahlgerät muss in der Lage sein, diese Parameter während der Prüfdauer in den jeweiligen Toleranzbereichen aufrechtzuerhalten. Das Herzstück des Prüfgeräts stellt jedoch die Düse dar. Das gleichmäßige Strahlbild und die Druckverteilung des Wasserstrahls auf der Prüffläche hängen stark von der Geometrie und Verarbeitungsqualität der Düse ab. Im Rahmen der Kalibrierung des Dampfstrahlgerätes und zur Ermittlung möglicher Verschleißschäden wird deshalb die Strahlbildanalyse mittels Kraftmessdose durchgeführt. Hierbei wird die Druckkraft der gesamten Wasserstrahlfläche gemessen, als 3D-Bild dargestellt und bewertet (siehe Abbildung 6). Werden mehrere Dampfstrahlprüfgeräte in einem Prüflabor gleichermaßen für Prüfungen verwendet, muss eine gewisse Vergleichbarkeit der Geräte untereinander sichergestellt sein. Neueste Untersuchungen in der Gruppe Lackierprozessentwicklung am Fraunhofer IPA bezüglich der zwei dort verwendeten Dampfstrahlgeräte mittels definierten Prüfplatten zeigen, dass sich die Geräte nicht signifikant voneinander unterscheiden. Der größere Einfluss ist durch die teilnehmenden Prüfer bedingt.
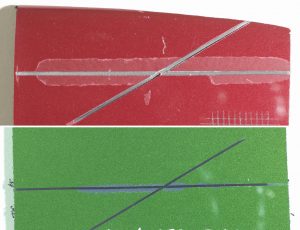
Abbildung 5: Schadensbild der Dampfstrahlprüfung, oben Ablösung des Klarlacks vom Basislack (Kennwert 5), unten Ablösung des Basislacks vom Primer (Kennwert 2), Bildquelle: Fraunhofer IPA
Die Fehlermöglichkeiten bei der Durchführung des Dampfstrahltests liegen neben der Einhaltung des Abstands der Düse zur Probe, der exakten Positionierung zur Wasserstrahlfläche und dem Auftreffwinkel des Wasserstrahls vor allem auch in der Handhabung der Schneide- oder Ritzwerkzeuge durch den Prüfer. In den meisten Prüfvorschriften sind entweder ein Cuttermesser oder ein Ritzstichel nach Sikkens zu verwenden. Die Ritzqualität wird durch konstante Geschwindigkeit und Druckausübung des Ritzwerkzeugs auf die Probe sichergestellt. Weitere Einflüsse sind die Ritztiefe und der Winkel, vor allem bei dem Ritzstichel nach Sikkens. Dieser erzeugt durch die 1 mm breite Schneide eine flächige Abtragung der Beschichtung, die je nach Handhabung und Prüfteilgeometrie einseitig tiefer ausfallen kann. Abstellhilfen bei der Positionierung der Probe im Dampfstrahlgerät bieten z. B. eingezeichnete Markierungen im Positionierbereich oder ein Laser, der die Mitte des Wasserstrahls markiert. Mittels Distanzblock lässt sich der Abstand der Düse leicht kontrollieren. Das Ritzen und die visuelle Auswertung können nur durch entsprechende Erfahrung der Prüfer reproduzierbar durchgeführt werden.
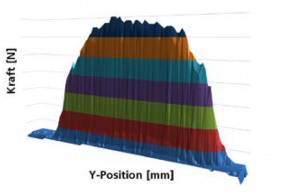
Abbildung 6: Strahlbild bei der Analyse mittels Kraftmessdose, Bildquelle: Fraunhofer IPA
Multisteinschlagprüfung
Ein weiteres Maß für die Haftfestigkeit von Lackierungen ist die Steinschlagfestigkeit. Basierend auf realen Belastungsfällen wurde die Multisteinschlagprüfung entwickelt (siehe Abbildung 7). Die DIN EN ISO 20567-1 beschreibt drei Varianten des Prüfverfahrens, die in den Hausnormen der OEM’s leicht abgewandelt wiederzufinden sind. Die Steinschlageinwirkung erfolgt durch viele kleine Schlagkörper (Hartgussgranulat), die mittels Druckluft auf den Probekörper geschossen werden. Bei einer schlechten Haftfestigkeit kommt es beim Aufprall der Schlagkörper zum Abplatzen von Lackmaterial. Das Ausmaß der Lackschädigung wird in der Regel visuell mittels Vergleichsbildern und der Zuweisung von Kennwerten bewertet (siehe Abbildung 8). Einige Prüfvorschriften verlangen vor der Bewertung einen zusätzlichen Klebebandabriss, der lose anhaftendes Beschichtungsmaterial entfernen soll. Das Prüfergebnis ist abhängig vom Arbeitsdruck, von der Masse des verwendeten Beschussmaterials, der Beschusszeit, dem Auftreffwinkel und dem Abstand der Probe zum Beschleunigungsrohr. Einen weiteren Einfluss hat die Korngrößenverteilung des Beschussmaterials, die von dem jeweiligen Lieferanten überprüft werden muss. Vor dem Start einer Prüfserie muss das Multisteinschlaggerät genauestens kalibriert werden. Hierbei wird die Förderzeit eingestellt, der Arbeitsdruck überprüft sowie ein Beschussbild zur Beurteilung der Gleichmäßigkeit des auftreffenden Granulats erstellt (siehe Abbildung 9). Um weitere Fehler zu vermeiden, ist der Gebrauch des Hartgussgranulats zu dokumentieren und dieses im vorgegebenen Intervall zu ersetzen. Der Prüfer muss zu jeder Zeit nachvollziehen können, inwieweit das Beschussmaterial bereits verbraucht ist.
Die Haftfestigkeit insgesamt ist eine wichtige Kenngröße für die Auswertung vieler weiterer Prüfverfahren wie z. B. der Ofenalterung, dem Klimawechseltest und der Belastung im Kondenswasserkonstantklima. Die Veränderung der Haftfestigkeit nach den klimatischen Belastungen wird im Vergleich mit der durchgeführten Haftfestigkeitsprüfung im Ausgangszustand ermittelt. Um die Prüfabläufe bei den subjektiv bewerteten Haftfestigkeitsprüfungen zu optimieren, ist eine intensive Einarbeitung und eine gewisse Erfahrung der Prüfer zwingend notwendig. Die Prüfgeräte müssen regelmäßig überprüft/kalibriert werden. Die Teilnahme an Ringversuchen zu den jeweiligen Prüfungen ist notwendig, um die Kompetenz des Prüflabors für dieses Prüfverfahren zu bestätigen. Bei der Gitterschnittprüfung besteht aktuell noch Bedarf, eine passende Referenzprobe mit definierter Haftung für einen Ringversuch zu finden. Untersuchungen zu diesem Thema werden am Fraunhofer IPA weiterverfolgt.
Autoren:
Dipl.-Ing. (FH) Marina Schäfer
Dipl.-Ing. (FH) Manh Hung Tran
Fraunhofer-Institut für Produktionstechnik und Automatisierung IPA
Nobelstraße 12, 70569 Stuttgart
www.ipa.fraunhofer.de