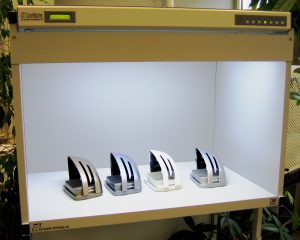
Abbildung 1: Lichtkabine für die visuelle Beurteilung von Proben, Bildquelle: Fraunhofer IPA
Visuelle und messtechnische Beurteilung des Erscheinungsbildes (Appearance) lackierter Bauteile
Unterschiedliche Farbtöne sowie Farb- und Glanzeffekte lösen in uns Stimmungen aus. Wir sprechen oftmals von einem Sonnengelb, Nachtblau, Schneeweiß oder einem edlen Schimmer auf der Oberfläche. Ganz automatisch bringen wir neue Farb- und Glanzeindrücke in Verbindung mit bestehenden Erfahrungen, die durchaus einen Kaufwunsch auslösen können.
Die enorme Empfindlichkeit des menschlichen Auges erlaubt es uns mehrere Millionen Farben wahrzunehmen. Kleinste Farb- und Glanzabweichungen oder Lackierfehler reichen aber auch aus, um dem Gesamtbild einen disharmonischen Eindruck zu verleihen. Kein Messgerät ist in der Lage, die Vielfalt an visuellen Eindrücken des menschlichen Auges in gleicher Weise zu erfassen. Rein physikalisch gesehen wird im Auge nur ein zweidimensionales Bild auf der Netzhaut (Retina) erzeugt und dabei verkleinert sowie umgekehrt (das Bild steht auf dem Kopf) abgebildet. Viele einzelne Eindrücke aus unterschiedlichen Winkeln in kürzester Zeit betrachtet (bedingt durch die Augenbewegungen) werden im Sehzentrum des Gehirns zu einem komplexen Gesamteindruck verarbeitet. Das dreidimensionale Bild entsteht erst im Gehirn. Das Sehen ist von Geburt an ein lebenslanger, individueller Lernprozess. Die visuelle Wahrnehmung ist daher eine subjektive Empfindung und zudem von der Tagesform abhängig.
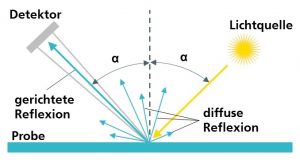
Abbildung 2: Schematische Darstellung zur Definition und messtechnischen Erfassung des Glanzes, Bildquelle: Fraunhofer IPA
Wie kann nun sichergestellt werden, dass alle Einzelkomponenten in einem Automobil aufeinander abgestimmt werden und eine gleichbleibende Qualität der optischen Lackfilmeigenschaften gewährleistet wird?
Die visuelle Beurteilung des Erscheinungsbildes in der Praxis benötigt gewisse Rahmenbedingungen, die erfüllt werden müssen, um reproduzierbare Ergebnisse zu erzielen. Diese Rahmenbedingungen können Vorgaben enthalten wie z. B. die Beleuchtung durch diffuses Licht aus nördlicher Richtung, den Abstand vom Fenster ca. 1,5 m, die Probe dem Fenster zugewandt und um 70° zur Horizontalen geneigt sowie den Betrachtungsabstand von ca. 0,6 m. Da die natürlichen Lichtverhältnisse nicht immer gleich sind, ist es sinnvoll, zusätzlich eine Lichtkabine mit neutralem Hintergrund einzusetzen, die mehrere genormte Lichtarten mit jeweils unterschiedlicher Zusammensetzung des Lichtspektrums wie z. B. künstliches Tageslicht, Glühlampenlicht und Kaufhauslicht simulieren kann (siehe Abbildung 1). Ein Stativ kann helfen, die Proben richtig zu positionieren.
Welche Qualitätskriterien sind ausschlaggebend bei der visuellen Wahrnehmung und sollten überprüft werden?
Bei genauer Betrachtung der Oberflächenbeschaffenheit eines Lackfilms können unter anderem folgende Parameter ermittelt werden:
- Glanz
- Glanzschleier
- Lackfilmverlauf
- Abbildungsqualität
- Farbe
Der Glanz entsteht aus der gerichteten Reflexion des einfallenden Lichts (Einfallswinkel = Ausfallswinkel, siehe Abbildung 2). Ist eine Oberfläche sehr glatt, erscheint sie glänzend, ist die Oberfläche dagegen eher rau, kommt es zu einer diffusen Reflexion des Lichts in alle Richtungen, die Probe erscheint matt. Die visuell wahrgenommenen Glanzunterschiede lassen sich sehr gut mittels Reflektometer messtechnisch erfassen (DIN EN ISO 2812). Der Glanzgrad wird typischerweise bei 20° Neigung zur Senkrechten für hochglänzende, 60° für mittelglänzende oder 85° für mattglänzende Oberflächen ermittelt. Im gleichen Zug lässt sich der Parameter Glanzschleier der Oberfläche (auch Trübung, Haze-Wert, DIN EN ISO 13803) ermitteln. Eine hochglänzende Oberfläche kann durch Unebenheiten, schlechte Dispergierung des Lacks oder Applikationsfehler „milchig“-trüb aussehen. Die Bereiche in unmittelbarer Nähe der gerichteten Reflexion werden bei der Messung mittels Detektor erfasst. Es wird ein Messwinkel von 20° Neigung zur Senkrechten verwendet.
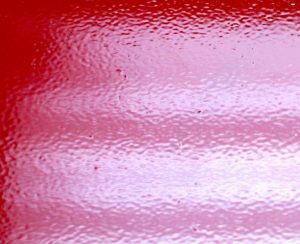
Abbildung 3: Beispiel einer Verlaufsstörung auf einer lackierten Oberfläche, Bildquelle: Fraunhofer IPA
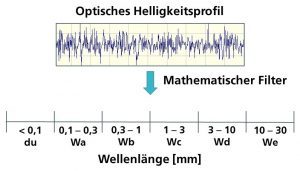
Abbildung 4: Schematische Darstellung der Messwerterfassung für die Beurteilung des Lackfilmverlaufs mittels Wave-Scan, Bildquelle: Fraunhofer IPA
Die Qualität des Lackfilmverlaufs (Orange Peel) wird durch die Zusammensetzung von welligen Strukturen auf der Oberfläche bestimmt. Eine Verlaufsstörung kann durch z. B. falsche Viskositätseinstellung des Lackmaterials, ein schlechtes Benetzungsverhalten des Lackfilms auf dem Untergrund und die falsche Wahl der Applikationsparameter beim Lackauftrag entstehen und wird durch ein welliges Muster heller und dunkler Felder auf einer hochglänzenden Oberfläche wahrgenommen (siehe Abbildung 3). Die Distanz zur Oberfläche spielt bei der Bewertung eine nicht unerhebliche Rolle. Kleine Strukturen sind aus der Nähe gut sichtbar, aus der Ferne dagegen schlecht erkennbar. Größere Wellen benötigen bei der Betrachtung eine gewisse Entfernung (z. B. 3 Meter). Messtechnisch kann die Welligkeit mittels Wave-scan bestimmt werden: Ein Laserstrahl „tastet“ die Oberfläche über eine definierte Strecke ab, indem das Messgerät über die Probenoberfläche bewegt wird. Dabei werden die reflektierten Laserstrahlen mittels Detektor in Form eines optischen Profils aufgenommen. Mittels mathematischer Filterung der Rohdaten werden die Strukturen in unterschiedliche Wellenlängenbereiche unterteilt (siehe Abbildung 4). Die typische Orangenhaut wird im langwelligen Bereich von 1,2 mm bis 30 mm wahrgenommen.
Der kurzwellige Bereich erstreckt sich über die Wellenlängen 0,3 mm bis 1,2 mm. Wenn die kurzwelligen Strukturen überwiegen, wird die Oberfläche als eher trüb wahrgenommen. Strukturen kleiner 0,1 mm erzeugen ein mattes Erscheinungsbild, daher wird in diesem Bereich zusätzlich der Wert Dullness (Mattigkeit) durch Erfassung des diffusen Streulichts ermittelt. Aus den Wellenlängenbereichen du, Wa und Wb lässt sich ein weiterer Parameter, die Abbildungsqualität (DOI – Distinctness of Image) bestimmen. Erscheint das Spiegelbild eines Gegenstands auf der lackierten Oberfläche kontrastreich, spricht man von einer guten Abbildungsqualität (siehe Abbildung 5).
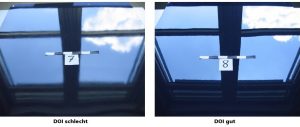
Abbildung 5: Gute und schlechte Abbildungsqualität im Vergleich, Bildquelle: Fraunhofer IPA
Die Wahrnehmung der Farbe ist von drei Faktoren abhängig. Erstens von der Zusammensetzung des sichtbaren Lichtspektrums der Lichtquelle bzw. Beleuchtung (ohne Licht keine Farbe). Zweitens von dem Objekt: Jedes Objekt bzw. jede Farbe hat eine individuelle Spektralkurve, je nachdem welche Anteile des einfallenden Lichtspektrums reflektiert und welche absorbiert werden. Schwarze Gegenstände absorbieren nahezu das gesamte Lichtspektrum, weiße Oberflächen reflektieren nahezu das gesamte einfallende Licht. Drittens von dem Beobachter: Das vom Objekt reflektierte Licht fällt in das menschliche Auge und wird als Farbe wahrgenommen. Hier besteht der Einfluss durch die Empfindlichkeit der Rezeptoren im Auge, die Größe der beobachteten Fläche sowie dem Abstand zum Auge. Die messtechnische Erfassung der Farbe mittels Spektralphotometer funktioniert nach dem gleichen Prinzip. Eine Normlichtart wird festgelegt (z. B. künstliches Tageslicht D65) und die Probe unter Ausschluss von Fremdlicht beleuchtet. Das reflektierte Licht wird detektiert und mittels der Spektralwertfunktionen eines festgelegten Normalbeobachters (z. B. 10°-Normalbeobachter) ausgewertet. Die gemessene Farbe wird in der Regel im dreidimensionalen CIELAB-Farbenraum (kartesisches Koordinatensystem) dargestellt und mit den berechneten Werten L* für Helligkeit, a* für Grün- und Rottöne sowie b* für Blau- und Gelbtöne beschrieben (DIN EN ISO 11664-4). Durch Messung einer Probe im Vergleich zu einer Referenz lassen sich die jeweiligen Farbabstände berechnen (ΔL*, Δa*, Δb*). Aus diesen Farbabständen kann wiederum ein Gesamtfarbabstand ΔE*ab berechnet werden. Dieser Wert entspricht einem kreisrunden Toleranzbereich im Farbraum und stimmt nicht immer mit der visuellen Akzeptanz überein. Wichtig jedoch bei der Festlegung von Toleranzen ist immer die Übereinstimmung mit der visuellen Bewertung. Bei einem knalligen Rot z. B. wird bei der visuellen Bewertung ein höherer Farbabstand akzeptiert als bei einem Pastellrosa. Grün lässt z. B. größere Toleranzen zu als Dunkelblau. Daher wurden weitere Gesamtfarbabstandsformeln mit entsprechenden Gewichtungs- und Korrekturfaktoren entwickelt, die der visuellen Wahrnehmung besser entsprechen, z. B. CMC-Formel (ΔECMC), CIE94-Formel (ΔE94) und CIEDE2000-Formel (ΔE00).
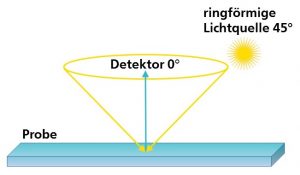
Abbildung 6: Farbmessgeometrie 45°/0°, Bildquelle: Fraunhofer IPA
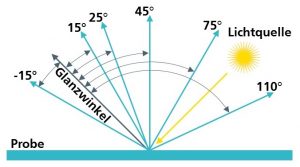
Abbildung 7: Beispiel für eine Mehrwinkelgeometrie für die farbmetrische Erfassung von Effektlacken, Bildquelle: Fraunhofer IPA
Je nach Lacksystem und Pigmentierung kann es notwendig sein bei der Farbmessung unterschiedliche Messgeometrien einzusetzen (umfassende Informationen zu den Messbedingungen sind in der DIN 5033-7 zu finden). Beispielhaft werden folgende Messgeometrien beschrieben:
- 45°/0° für Uni-Farbtöne
- Mehrwinkelgeometrie 15°, 25°,.45°, 75°, 110° für Metallic- und andere Effektlacke (Hell-Dunkel Flop)
- Mehrwinkelgeometrie 15°, 25°,.45°, 75°, 110° und zusätzlich -15° für Multicoloreffektlackierungen (Farbflop)
Bei Uni-Farbtönen wird in der Regel die 45°/0° Geometrie verwendet (siehe Abbildung 6). Das Objekt wird unter 45° ringsum beleuchtet und das reflektierte Licht unter 0° detektiert. Hierbei wird der Einfluss des Glanzes ausgeschlossen und somit eine gute Übereinstimmung mit der visuellen Bewertung der Farbe erzielt. Bei Metallic- und anderen Effektlacken führt die Variation des Beobachtungswinkels zu einer starken Helligkeitsänderung (Hell-Dunkel Flop). Dieser Effekt lässt die Konturen eines Bauteils besser zur Geltung kommen, benötigt allerdings mehr Messwinkel zur Erfassung der Farbe. Die Messung erfolgt mittels Mehrwinkelfarbmessgerät. Der Lichteinfall erfolgt gerichtet unter 45° zur Senkrechten, detektiert wird unter den Winkeln 15°, 25°, 45°, 75°, 110°, ausgehend vom Glanzwinkel (siehe Abbildung 7). Handelt es sich um farbfloppende Multicoloreffektlackierungen, wird zusätzlich der Messwinkel -15° (Messwinkel hinter dem Glanz) eingesetzt. Je nach Anwendung sind auf dem Markt weitere Farbmessgeräte mit weitaus mehr Messwinkeln verfügbar.
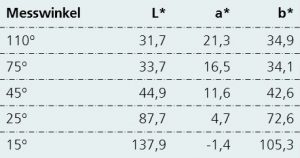
Tabelle 1: Messwerte zu den Betrachtungswinkeln in Abbildung 8. Die reflektierende Wirkung des goldenen Pearl-Pigments ist deutlich in der hohen Spannweite des Helligkeitswerts L* erkennbar. Der goldfarbene Schimmer dieser Pigmente nimmt ebenfalls stark ab, je weiter der Messwinkel sich vom Glanzwinkel entfernt. Siehe Messwerte b* für Blau- und Gelbtöne.
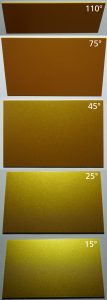
Abbildung 8: Beispiel für die visuelle Wirkung einer Lackierung mit goldfarbenen synthetischem Pearl Pigment bei unterschiedlichen Beobachtungswinkeln analog der Messgeometrien eines Mehrwinkelfarbmessgeräts, Bildquelle: Fraunhofer IPA
Abbildung 8 veranschaulicht als Beispiel die Wirkung einer Lackierung mit goldfarbenem synthetischem Pearl Pigment bei unterschiedlichen Betrachtungswinkeln analog der Messgeometrien eines Mehrwinkelfarbmessgeräts. Die dazugehörigen Messwerte sind in Tabelle 1 aufgeführt. Ziel der Messtechnik im Bereich Appearance ist immer die Übereinstimmung mit der menschlichen Wahrnehmung. Die Messtechnik hat eine sehr hohe Bedeutung in der Qualitätssicherung, bei der Entwicklungsarbeit hat jedoch die visuelle Wahrnehmung einen höheren Stellenwert.
Kontakt:
Fraunhofer-Institut für Produktionstechnik und Automatisierung IPA
Nobelstraße 12, 70569 Stuttgart
www.ipa.fraunhofer.de
Autoren: Dipl.-Ing. (FH) Marina Schäfer, Dipl.-Ing. (FH) Manh Hung Tran