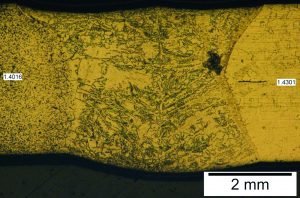
Abbildung 1: Querschliff einer lasergeschweißten Mischverbindung aus ferritischen und
austenitischen Edelstählen
Heutzutage haben korrosionsbeständige Stähle viele Anwendungsbereiche des täglichen Lebens erobert. So kommen diese in zahlreichen Bereichen zum Einsatz, in denen erhöhte Korrosionsgefahr durch aggressive Medien droht, aber auch für Aufgabenstellungen mit hohen hygienischen Anforderungen. Im Laufe der Zeit wurde eine Vielzahl an verschiedenen korrosionsbeständigen Stählen für spezifische Einsatzgebiete entwickelt, die sich in ihrer Legierungszusammensetzung und Gefügemorphologie teilweise deutlich voneinander unterscheiden. Dies wirkt sich auch auf die Schweißeignung der jeweiligen Werkstoffe aus, die immer dann eine Rolle spielt, wenn einzelne Bauteile im Produktionsprozess durch Schweißen zu einer Baugruppe gefügt werden sollen. Während zum Verbinden massiverer Bauteile meist das Wolfram- oder Metall-Inertgas-Schweißen sowie das Widerstandspunktschweißen Anwendung finden, wird im Bereich filigraner Produkte meist das Laserstrahlschweißen verwendet. Durch dessen konzentrierte Wärmeeinbringung bei gleichzeitig geringem Gesamtenergieeintrag können verzugsarme Schweißbaugruppen in sehr kurzen Taktzeiten hergestellt werden. Am Bayerischen Laserzentrum (blz) konnte darüber hinaus gezeigt werden, dass trotz der stark unterschiedlichen Wärmeausdehnung und Wärmeleitfähigkeit die Möglichkeit besteht, auch Mischverbindungen zwischen austenitischen und ferritischen korrosionsbeständigen Stählen herzustellen, ohne dabei die Duktilität und Festigkeit der Werkstoffe im Bereich der Schweißnaht signifikant zu verringern.
Eine Branche, die die Möglichkeiten des Laserstrahlschweißens für korrosionsbeständige Stähle bereits früh erkannt hat, ist die Medizintechnik, welche eine Vielzahl von Möglichkeiten für den Einsatz des Lasers als direktes bzw. indirektes Werkzeug bietet. Insbesondere bei der Herstellung von Medizintechnikprodukten hat der Laser in der Vergangenheit zunehmend an Bedeutung gewonnen. Hierbei kommt der Laser vor allem für Fügeoperationen im Bereich medizintechnischer Geräte sowie beim Schweißen von Produkten zur einmaligen Verwendung, wie beispielsweise Kanülen, zum Einsatz.
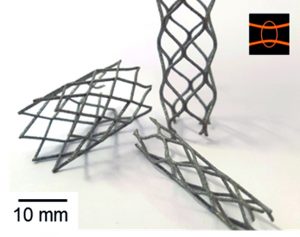
Abbildung 2: Additiv gefertigte Stent-ähnliche Strukturen aus einer Nickel-Titan-Formgedächtnislegierung
Neben medizintechnischen Geräten aus korrosionsbeständigen Stählen erfordert vor allem die Fertigung von patientenspezifischen Implantaten aus Titanlegierungen sowie die Herstellung von Bohrschablonen bzw. Hilfsmitteln für chirurgische Operationen den Einsatz neuer Fertigungstechnologien. Aufgrund der hohen Anforderungen an die Flexibilität wurden in diesem Zusammenhang additive Fertigungsverfahren wie die Stereolithographie (SLA), das Selektive Lasersintern (SLS) oder das Laserstrahlschmelzen von Metallen (LSS) als mögliche Fertigungsverfahren identifiziert und bei der Herstellung von Medizinprodukten erfolgreich etabliert. Additive Fertigungsverfahren bieten die Möglichkeit auf Basis von CAD-Modellen komplex geformte Bauteile zu generieren. Ausschlaggebend hierfür ist in erster Linie der schichtweise Aufbauprozess, der allen additiven Fertigungsverfahren gemein ist. So können durch den Einsatz von Bindern bzw. hochenergetischen Strahlwerkzeugen (Laserstrahl bzw. Elektronenstrahl) Polymerwerkstoffe und metallische Werkstoffe gefügt werden. Im Rahmen der Grundlagen- und anwendungsorientierten Forschung befasst sich der Lehrstuhl für Photonische Technologien (LPT) an der Friedrich-Alexander-Universität Erlangen-Nürnberg (FAU) mit der laserbasierten additiven Verarbeitung von Metallen mittels LSS und Laserpulverauftragschweißen (LPAS). Für die schichtweise Fertigung von qualitativ hochwertigen Produkten, wie sie beispielsweise für die Medizintechnik oder die Luftfahrt erforderlich sind, ist ein stabiler und reproduzierbarer Schmelzprozess essentiell. So ist beim LSS sicherzustellen, dass bereits vor der Belichtung einer jeden Einzelschicht das metallische Pulver stets homogen aufgetragen wird. Die nachfolgende Belichtung ist stets in Abhängigkeit des Werkstoffs zu wählen. Sowohl in der Additiven Fertigung als auch beim Laserstrahlschweißen müssen unerwünschte Nebeneffekte aktiv durch die richtige Auswahl der Prozessparameter vermieden werden. Beispiele für solche Nebeneffekte stellen Anlauffarben oder Spritzer (siehe Abbildung 3), welche bei einer falsch gewählten Prozessstrategie durch eine hohe Schmelze- und Verdampfungsdynamik entstehen können, dar.
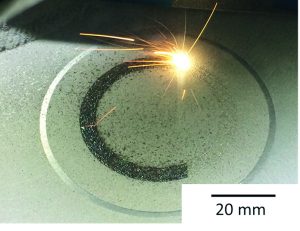
Abbildung 3: Spritzerbildung beim Laserstrahlschmelzen
Diese Prozessfehler führen meist zu Änderungen der chemischen Zusammensetzung der Bauteile und sind verantwortlich für abweichende Material- und Bauteileigenschaften. Auftretende Spritzer verringern im Fall von Stählen beispielsweise die Korrosionsbeständigkeit der Werkstoffe lokal und begünstigen somit die Entstehung von Korrosionsprodukten wie Rost. Werden Spritzer nicht durch einen effektiven Luftstrom aus der Prozesszone entfernt, können sich diese beim Laserstrahlschweißen auf dem Bauteil ablagern, wo sich in der späteren Verwendung Bakterien ansammeln und mögliche Infektionsherde bilden können. Daher sind Spritzer unter dem Gesichtspunkt der hygienekonformen Verwendung der späteren Produkte dringend zu vermeiden. Beim Laserstrahlschmelzen können sich Spritzer im noch nicht aufgeschmolzenen Pulverbett ablagern und den nachfolgenden Schmelzprozess negativ beeinflussen. Als direkte Folge können sich Poren und Anbindungsfehler einstellen.
Aus all diesen Gründen gewinnt das Prozessverständnis der Spritzerentstehung zunehmend an Bedeutung. Um dieses Verständnis zu erhalten und die beschriebenen Prozessinhomogenitäten vermeiden zu können, sind zum einen neuartige Prozessbeobachtungsansätze erforderlich, mithilfe derer die Entstehung von Spritzern erfasst und quantifiziert werden können. Darüber hinaus können Prozesssimulationen helfen, adäquate Prozessstrategien abzuleiten. Durch eine Kombination beider Ansätze wird am LPT die Spritzerbildung umfassend untersucht und analysiert. Bildgebende Verfahren sind mittlerweile gegenüber fotodiodenbasierten Sensoren die erste Wahl zur Erhöhung des Prozessverständnisses bei Lasermaterialbearbeitungsprozessen, da das Prozessverhalten in den Kameraaufnahmen direkt ersichtlich ist und nicht aufwändig und fehleranfällig aus den Signalen der Fotodioden interpretiert werden muss. Einer der großen Vorteile der Lasermaterialbearbeitung – die kleine Interaktionszone – erschwert jedoch die kamerabasierte Erfassung des Prozesses. Außerdem behindern die starken Prozessemissionen und die hohe Prozessdynamik die Erstellung auswertbarer Aufnahmen. Aus diesen Gründen werden für eine kamerabasierte Prozessanalyse sowohl eine hohe räumliche als auch zeitliche Auflösung der genutzten Kamerasysteme benötigt. Je nach beobachtetem Prozessphänomen erfordern die genannten Rahmenbedingungen darüber hinaus die Auswahl geeigneter Filter und zusätzlicher Beleuchtungseinrichtungen. Da die hohe zeitliche Auflösung zu einer hohen Zahl an Aufnahmen führt (bis zu 250.000 pro Sekunde), ist auch eine automatisierte Bildverarbeitung unerlässlich, um das volle Potential der Prozessbeobachtungshardware ausschöpfen zu können und der Entstehung von Spritzern auf den Grund zu gehen. Das für diese Arbeiten erforderliche Know-how konnte in den letzten Jahren am LPT erfolgreich aufgebaut und angewandt werden.
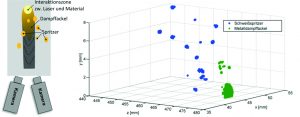
Abbildung 4: Kamerapositionierung und berechnete 3D-Rekonstruktion von Schweißspritzern (blau) und Teilen der Dampffackel (grün) beim Laserstrahlschweißen; Vorschub in z-Richtung.
Ein Beispiel für eine erfolgreiche Anwendung der genannten Expertise stellt die dreidimensionale Erfassung von Spritzer-Flugbahnen zur Quantifizierung des Prozessverhaltens dar. Im Gegensatz zur zweidimensionalen Prozessbeobachtung mit nur einer Kamera werden für die dreidimensionale Messung der Spritzerbahnen zwei synchronisierte Hochgeschwindigkeitskameras verwendet. Dadurch kann die reale Lage der Spritzer ohne Projektionsfehler mit hoher zeitlicher Auflösung erfasst werden. Da die Kameras den Prozess aus unterschiedlichen Raumwinkeln beobachten, müssen die Aufnahmen, zur Messung der dreidimensionalen Lage der Spritzer aus den beiden Kamerapositionen in ein gemeinsames Koordinatensystem transformiert werden. Die Berechnung der für diese sogenannte Rektifizierung benötigten Kalibriermatrix stellt, insbesondere aufgrund der kleinen Interaktionszone und des damit einhergehenden kleinen Bildbereichs der Kameras, bei Lasermaterialbearbeitungsprozessen eine besondere Herausforderung dar, welche jedoch am LPT durch eine selbst entwickelte Softwarelösung bewältigt werden konnte. Abbildung 4 zeigt das Ergebnis einer rekonstruierten Szene beim Laserstrahlschweißen.
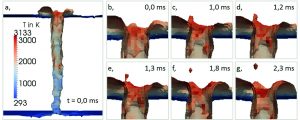
Abbildung 5: Mithilfe einer Simulation berechnete Spritzerablösung beim Schweißen von Stahl. Die Einzelbilder zeigen jeweils einen lateralen Schnitt durch die beim Schweißen aufgrund des Verdampfungsdrucks entstehende Dampfkapillare mit Blick in Schweißrichtung. Dabei wurde nicht das Material selbst, sondern die Phasengrenze zwischen Metall und Luft, also die Dampfkapillare und Blechober- und –unterseite in Falschfarben entsprechend der Temperatur visualisiert.
Die Ergebnisse zeigen, dass die einzelnen Spritzer gut erkennbar und von der Dampffackel zu trennen sind. Durch die Auswertung mehrerer aufeinanderfolgender Aufnahmen können Geschwindigkeit und Richtung der Spritzerflugbahnen für verschiedene Prozessparameter gemessen werden, um das Prozessverhalten objektiv quantifizieren und zielgerichtet optimieren zu können. Auf Grundlage dieser Untersuchungen können darüber hinaus maßgeschneiderte Prozessbeobachtungssysteme mit der für eine Spritzerbeobachtung nötigen Verarbeitungsgeschwindigkeit ausgelegt werden, welche die Grundlage für eine echtzeitfähige Prozesskontrolle der Spritzerentstehung sowohl beim Laserstrahlschweißen als auch dem LSS-Prozess bilden. Die Ergebnisse der Prozessuntersuchungen bilden eine ideale Grundlage zum Abgleich mit der Simulation der Spritzerentstehung. Numerische Prozesssimulationen stellen ein immer wichtiger werdendes Werkzeug dar, um Prozesse zu untersuchen und so einerseits das Prozessverständnis zu erhöhen und andererseits Prozesse mit reduziertem experimentellen Aufwand auslegen, planen und optimieren zu können. Darüber hinaus ermöglichen Simulationen einen Blick in das Material, das heißt, mittels Simulationen ist es möglich Größen an experimentell unzugänglichen Stellen zu „messen“, wie bspw. Strömungen und Temperaturfelder im Innern des Schmelzbads. Zudem können Größen ausgewertet werden, die experimentell nicht oder nur unter erheblichem Aufwand bestimmt werden können, wie lokal aufgelöste Verdampfungsraten oder die ortsabhängige, absorbierte Laserleistung. Schließlich erlauben es Simulationen auch systemtechnisch (noch) nicht realisierbare Experimente bereits durchzuführen und so eine Aussage darüber zu treffen, ob die Entwicklung neuartiger Systemtechnik wie alternative Wellenlängen oder komplexere Bestrahlungsstrategien für den Prozess vorteilhaft ist.
Da die Spritzer in der Lasermaterialbearbeitung von einem komplexen Zusammenspiel verschiedener physikalischer Phänomene wie Absorption, Schmelzeströmung und schwankender Fluideigenschaften abhängen, muss ein Simulationsmodell zur Untersuchung der Spritzerentstehung eine Vielzahl an physikalischen Bausteinen enthalten. Ein solch multiphysikalisches Modell betrachtet daher zunächst die Strahl-Material-Wechselwirkung, das heißt Absorption und (Mehrfach-)Reflexion entlang der sich verändernden Werkstoffoberfläche. Zusätzlich muss das Prozessmodell die Thermodynamik des Prozesses, also die Erwärmung aufgrund des Energieeintrags durch den Laser, die daraus resultierenden Phasenwechsel, also Schmelzen, Verdampfen und Wiedererstarren, und die Fluidmechanik der Metallschmelze berechnen können. Um die notwendige Genauigkeit zur Darstellung von Spritzern zu erreichen, müssen schließlich die Kennwerte der Metallschmelze temperaturabhängig berücksichtigt werden, da die auftretenden Temperaturen prozessbedingt ortsabhängig zwischen Schmelz- und Verdampfungstemperatur variieren und für die Spritzerablösung entscheidende Kennwerte wie Viskosität und Oberflächenspannung daher lokal stark schwanken.
Ein solches fluiddynamisches Prozessmodell wurde am LPT entwickelt und bereits sehr erfolgreich zur Untersuchung vieler laserbasierter Prozesse wie Laserstrahlschweißen, -schneiden, -hartlöten, -bohren mit kurzen und ultrakurzen Pulsen und dem LSS-Prozess angewandt. Abbildung 5 zeigt eine solche Prozess-
simulation. Dabei lässt sich zunächst erkennen, wie eine anfänglich nur kleine Erhebung heißer Metallschmelze am Rande der Dampfkapillare aufgrund der vorherrschenden Prozessdynamik innerhalb kurzer Zeit weiter anwächst und sich schließlich innerhalb weniger als einer Millisekunde ein Spritzer ablöst. Die so gewonnenen Daten zu Spritzerposition und -bewegung können anschließend mit den experimentellen Daten abgeglichen werden und das Verständnis der Spritzerentstehung und -ablösung schließlich mit den durch die Simulation gewonnenen Erkenntnissen erweitert werden.
Mithilfe der Kombination der verschiedenartigen Systemtechniken, der bildgebenden Sensorik und des Simulationsmodells sind die Mitarbeiter an LPT und blz der Spritzerentstehung auf der Spur, um sowohl die Hygiene als auch die Korrosionsbeständigkeit medizintechnischer Produkte zu verbessern.
Autoren:
Stefanie Kohl, Lehrstuhl für Photonische Technologien, Friedrich-Alexander-Universität Erlangen-Nürnberg
Vincent Mann, Bayerisches Laserzentrum GmbH (blz), Erlangen
Christian Scheitler, Lehrstuhl für Photonische Technologien, Friedrich-Alexander-Universität Erlangen-Nürnberg Felix Tenner, Lehrstuhl für Photonische Technologien, Friedrich-Alexander-Universität Erlangen-Nürnberg