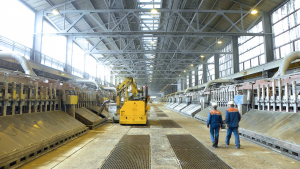
Abbildung 1: Eine von insgesamt drei Elektrolysehallen bei der TRIMET Aluminium SE in Essen. Jede Halle beheimatet insgesamt 120 Elektrolyseöfen (© TRIMET Aluminium SE)
Im Zuge der Energiewende werden konventionelle Energieerzeugungsquellen zunehmend durch Erzeugungsanlagen ersetzt, die auf erneuerbare Energien basieren. Der Großteil der erneuerbaren Energieerzeugung besitzt eine starke Wetterabhängigkeit, was zu einer erheblichen Fluktuation in der Stromerzeugung führt. Eine Lösung für diese Problematik ist die Flexibilisierung der industriellen Nachfrage nach Strom.
Zusammen mit den Lehrstühlen für Automatisierungstechnik/Informatik (LfA), Strömungsmechanik und Werkstofftechnik der Bergischen Universität Wuppertal arbeitet die TRIMET Aluminium SE in Essen an dem Projekt der Virtuellen Batterie. Dabei fungieren bei der TRIMET 120 Elektrolyseöfen als Testreihe, die eine Speicherkapazität von rund 1120 MWh bei einem Wirkungsgrad von bis 95% zur Verfügung stellen können. Damit eine solche Speicherkapazität erreicht werden kann, wird die Testreihe nicht mehr mit einer konstanten, sondern flexiblen Stromstärke betrieben. Mit einer solchen flexiblen Leistungsanpassung können zukünftige Schwankungen im Energienetz, die durch Angebotsengpässe oder -überschüsse entstehen, zusätzlich ausgeglichen werden.
Dieser Paradigmenwechsel bringt nicht nur neue Vorteile, sondern auch weitere Herausforderungen mit sich, die von der Neugestaltung der Prozessführung bis hin zur Umrüstung der einzelnen Öfen reichen.
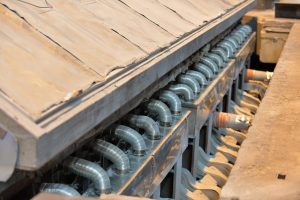
Abbildung 2: Mehrere Wärmetauscher, die an
der Seite eines Elektrolyseofens installiert sind (© TRIMET Aluminium SE)
Durch die Flexibilisierung der Ofenstromstärke ändern sich die thermischen Zustände innerhalb des Ofens, da eine Änderung der Stromstärke eine Änderung der Ofentemperatur nach sich zieht. Eine zu hohe Temperatur innerhalb des Ofen ist nicht wünschenswert und kann im schlimmsten Fall zu irreparablen Schäden am Ofen führen. Auf der anderen Seite können zu niedrige Ofentemperaturen zum Erstarren des Elektrolyten im Ofen führen. Um Schäden und Ausfälle zu vermeiden, werden die Öfen unter anderem mit Wärmetauschern ausgestattet. Diese sorgen dafür, dass der überschüssige Wärmestrom innerhalb des Ofens durch eine erhöhte Stromstärke abgeführt werden kann. Gleichzeitig dienen die Wärmetauscher auch als Wärmeisolierung, um bei einer geringen Stromstärke ein zu starkes Abkühlen der Öfen zu verhindern. Zusätzlich werden in den Luftabsaugungsrohren elektronische Klappen eingesetzt, um die Luftabsaugung der Wärmetauscher zu regulieren.
Hierzu entwickelt der LfA einen Algorithmus zur Regelung der elektronischen Klappen. Für die Ermittlung von sinnvollen Parametern und Prozessvariablen für die Klappenregelung werden zusammen mit der TRIMET Aluminium SE Strommodulationsexperimente, also eine Variation der Stromstärke, an mehreren Versuchsöfen durchgeführt und vom LfA ausgewertet. In Abbildung 2 sind mehrere Wärmetauscher abgebildet, die an der Seitenwand eines Aluminiumelektrolyseofens angebracht sind.
Damit die Aluminiumproduktion weiterhin effizient betrieben werden kann, werden darüber hinaus Methoden erforscht und entwickelt, die den Ofenprozess fortlaufend überwachen und auf zukünftige Ofenstörungen hinweisen.
So unterstützt der LfA die TRIMET Aluminium SE hinsichtlich der Auswertung der Ofenprozessdaten im Rahmen der Projekte Aluminiumelektrolyse 4.0 und Thermische Flexibilisierung der Aluminiumelek-trolyse. Ferner werden prädiktive Modelle unter dem Einsatz von Machine Learning und Deep Learning Ansätzen/Methoden entwickelt, um den aktuellen und zukünftigen Ofenzustand zu ermitteln sowie potenzielle Ofenstörungen zu identifizieren.
Individuelle Anodenstrommessung zur Erkennung von Störungen
Bei einem solch umfangreichen und komplexen Projekt, wie der Virtuellen Batterie, bedarf es weiterer Messtechnik, um auch bei Änderung der Stromstärke einen störungsfreien Betrieb der Elektrolyse zu gewährleisten. Bei einem Elektrolyseofen können während des Betriebs verschiedene Arten von Störungen auftreten. Beispielsweise können sich unter einer Anode sogenannte Spitzen bilden, die lokal zu Kurzschlüssen und damit zu einem ineffizienten Betrieb und einem höheren Wärmeeintrag führen können. Ohne eine Überwachung der insgesamt 26 Anoden pro Ofen, ist es schwierig festzustellen, welche Anode von der Störung betroffen ist. Mit einer kontinuierlichen Messung kann zudem laufend überprüft werden, ob eine Anode nach dem Wechsel korrekt eingesetzt wurde. Wird identifiziert, dass eine Anode zu tief oder zu hoch gesetzt ist, kann dieses Problem sofort behoben werden. Eine weitere Störung, die während des Betriebs auftreten kann, ist der sogenannte Anodeneffekt. Dieser resultiert aus einem zu geringen Aluminiumoxidgehalt unter einer Anode. Die Folge des Anodeneffektes ist, dass die Ofenspannung stark ansteigt, was zu einem hohen Wärmeeintrag führt. Eine Überwachung der Anodenstromverteilung bietet die Möglichkeit präventiv einzugreifen und somit einen Anodeneffekt zu verhindern.
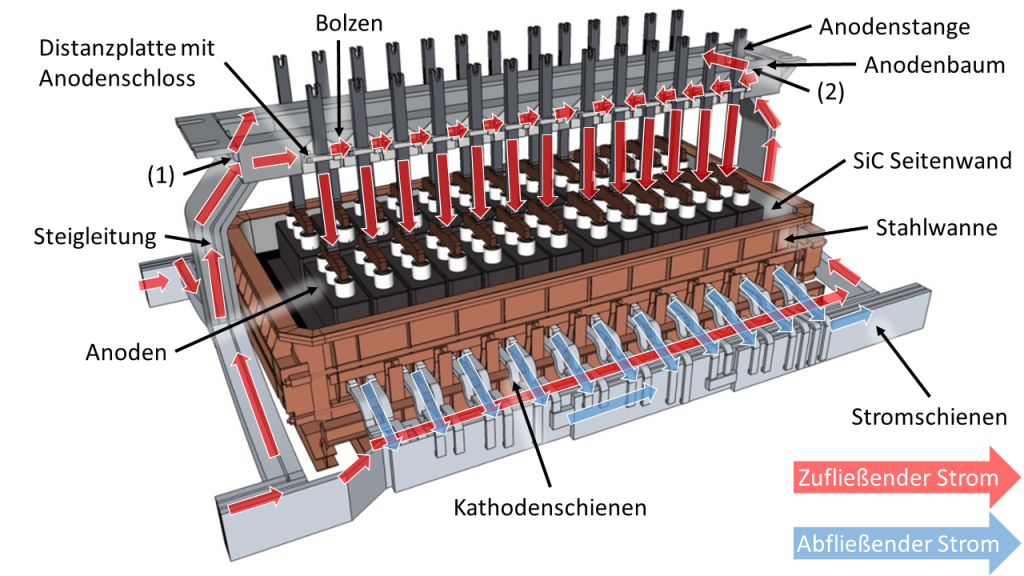
Abbildung 3: Modell eines Elektrolyseofens am TRIMET Standort Essen (© TRIMET Aluminium SE)
Doch wie funktioniert eine solche Strommessung in einem Umfeld, das von starken Magnetfeldern, mechanischen Einwirkungen und hohen Temperaturen geprägt ist? Hierzu hat der LfA verschiedene Messtechniken experimentell untersucht, darunter auch Hallsensoren und faseroptische Stromsensoren. Als ein robustes und kostengünstiges Verfahren hat sich die Anodenstrommessung mittels des Shunt-Verfahrens herausgestellt: Hierbei wird der Leiter selbst als Shunt betrachtet. Über die ermittelten Materialparameter sowie der kontinuierlich gemessenen Temperatur kann der Widerstand für einen bestimmten Streckenabschnitt berechnet werden. Unter Anwendung des Ohmschen Gesetzes erfolgt nach der Messung des Spannungsabfalls über denselben Streckenabschnitt die Berechnung des Stroms. In Abbildung 3 ist der Stromverlauf eines Elektrolyseofens dargestellt. Der Strom fließt über die Stromschienen und dann entlang der Steigleitungen zum Anodenbaum, an dem die Anodenstangen aufgehängt sind. An den markierten Punkten (1) und (2) teilt sich der Strom dann nahezu symmetrisch auf die beiden Seiten des Anodenbaums auf. Wird beispielsweise ein Hallenstrom von 175 kA angenommen, so fließen allerdings aufgrund der Geometrie bei Punkt (1) ungefähr 2/3 des Gesamtstroms, d.h. 117 kA und bei Punkt (2) 1/3 des Gesamtstroms, also 58 kA hinein. Wie viel Strom nun über die Anodenstange in die Anode abfließt, hängt von vielen Einflussgrößen des Prozesses ab, im Mittel sind es 6–9 kA. Nachdem der Strom seinen Weg durch den Elektrolyten und das flüssige Aluminium genommen hat, fließt er über die Kathode und die angeschlossenen Kathodenschienen weiter zum nächsten Ofen.
Die Herausforderung besteht nun darin, dass die Anoden in einem Ofen aufgrund ihres Verbrauchs ungefähr alle 30 Tage gewechselt werden müssen. Aus diesem Grund, vor allem um mechanische Schäden und elektrische Kontaktschwierigkeiten vorzubeugen, galt es ein Messverfahren zu finden, das ohne jegliche für den Anodenwechsel hinderliche Sensorik an der Anodenstange funktioniert. Hierzu wurden Bolzenpaare in einem definierten Abstand in den Anodenbaum gesetzt, sodass das Shunt-Verfahren angewendet werden kann. Ist die Stromverteilung auf dem Anodenbaum bekannt, so können über die Differenzbildung die individuellen Anodenströme ermittelt werden.
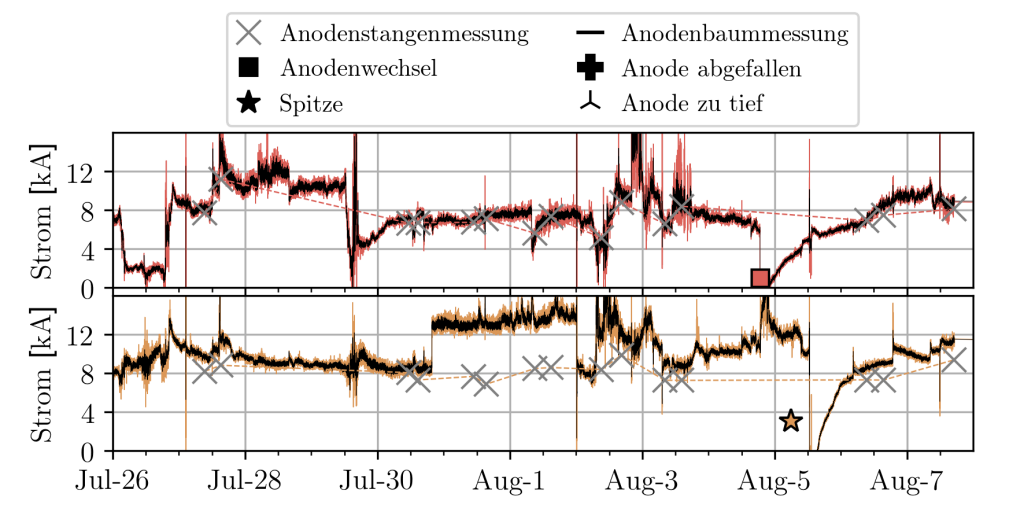
Abbildung 4: Anodenstrom, Anodenwechsel und
manuell detektierte Störungen bei zwei Anoden im Jahr 2018
In Abbildung 4 sind für zwei Anoden exemplarisch die Messergebnisse im zeitlichen Verlauf dargestellt. Zu Vergleichszwecken wurden in dem betrachteten Zeitraum neben der kontinuierlichen Messung auf dem Anodenbaum manuelle Messungen an der Anodenstange nach dem Shunt-Verfahren durchgeführt. Aufgrund von Vergleichsmessungen mit anderen Messverfahren und der einfacheren Geometrie werden die direkten Messungen an der Anodenstange als Grundwahrheit betrachtet (englisch: ground truth). Die Störungen Anode abgefallen und Anode zu tief sind in dem betrachteten Zeitraum nicht aufgetreten. Für die obere Anode ist zu erkennen, dass die Anodenstangenmessung und die Anodenbaummessung gut übereinstimmen. Ein durchgeführter Anodenwechsel ist anhand des Sprungs im Signalverlauf und einem anschließenden Stromanstieg wiederzuerkennen. Wird die Messung der unteren Anode betrachtet, zeigen sich insbesondere Ende Juli/Anfang August starke Abweichungen. Der Trend eines starken Stromanstiegs bei der Anodenbaummessung kurz vor dem 5. August in Folge einer Spitze wird dennoch wiedergegeben. Da die aufgenommenen Messdaten allerdings im späteren Verlauf des Projektes zur automatischen Detektion der Störungen mittels Machine Learning genutzt werden sollen, müssen noch weitere Optimierungen am Messverfahren vorgenommen werden. Denn ohne saubere Eingangsdaten kann es dazu kommen, dass selbst ein sehr gutes Machine Learning Modell fehlerhafte Vorhersagen trifft.
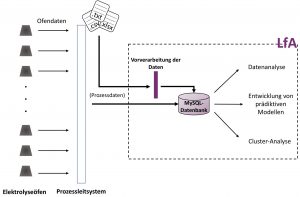
Abbildung 5: Verarbeitung der Ofenprozessdaten am Lehrstuhl für Automati-
sierungstechnik/Informatik (LfA)
Machine Learning in der Aluminiumelektrolyse
Start eines jeden neuen Machine Learning Projekts ist zunächst ein umfassendes Verständnis über das entsprechende Einsatzgebiet, in dem die späteren prädiktiven Modelllösungen eingesetzt werden. So ist es zunächst empfehlenswert, Rücksprachen mit den zuständigen Prozessingenieuren zu halten, um die Ziele klar zu definieren. Solche Gespräche haben den Vorteil, dass das Know-how aus vergangenen Projekten mit in das aktuelle Projektgeschehen einfließen kann.
Sobald die ersten Gespräche den Einsatz von prädiktiven Modellen rechtfertigen, müssen im weiteren Projektverlauf die entsprechenden Datenquellen identifiziert werden. Es kommt selten vor, dass alle Daten an einem Ort abgelegt werden, sondern zunächst aus verschiedenen Quellen zusammengetragen werden müssen. Dazu hat der LfA eine interne Vorverarbeitungs-Pipeline eingerichtet, um den Datenfluss zu vereinheitlichen und die verschiedenen Datenquellen miteinander zu verknüpfen. Am Ende des Vorganges werden alle Daten zentral in eine Datenbank abgelegt, mit der weitere Datenanalysen möglich sind. Die Abbildung 5 zeigt diesen Vorgang.
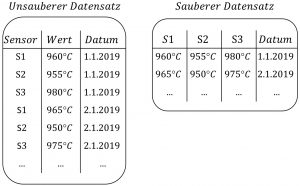
Abbildung 6: Unterschied zwischen einem unsauberen und sauberen Datensatz
Jeder, der bereits mit einer größeren Datenmenge gearbeitet hat, wird bestätigen, dass diese überwiegend unvollständig ist oder in einer Struktur vorliegt, die für das Anlernen von prädiktiven Modellen nicht geeignet ist. So werden z.B. Temperaturwerte von jedem Sensor mit dem dazugehörigen Zeitstempel in eine eigene Zeile abgespeichert. Dies widerspricht dem Gedanken von einem sauberen Datensatz, da jede Prozessvariable jeweils in eine eigene Spalte abgespeichert werden sollte (Abbildung 6). Dieses Konzept ist unter anderem in der frei zugänglichen Softwareumgebung R für statistische Berechnungen gängige Praxis.
Sobald die Daten in einer sauberen und vollständigen Struktur vorliegen, kann anschließend die Modellbildung durchgeführt werden. In diesem Prozess sollten mehrere Modelle antrainiert und anschließend im Validierungsvorgang anhand einer Performanz-Metrik verglichen werden. Das Modell mit einer guten Performanz entscheidet diesen Prozess für sich und wird abschließend einem letzten Test unterzogen. Sobald dieser Test auch hier eine wünschenswerte Modell-Performanz liefert, kann dieses letztendlich im Produktivbetrieb eingesetzt werden. Es ist zu erkennen, dass mehrere Schritte für die Entwicklung eines prädiktiven Modells notwendig sind. Oftmals werden die Schritte iterativ durchgeführt, um die Modell-Performanz weiter zu verbessern.
Lernen mit Transparenz
Neben der Modell-Performanz spielt auch die Interpretierbarkeit der Modelle eine wichtige Rolle und sollte bei der Modellfindung nicht vernachlässigt werden. Auch in der Aluminiumindustrie sollte ersichtlich sein, welche Prozessvariablen einen maßgeblichen Einfluss auf die Vorhersage haben. Aus diesem Grund wurde in den ersten Versuchen ein Random Forest Modell verwendet, dessen Basis aus mehreren Entscheidungsbäumen besteht. Entscheidungsbäume tätigen ihre Vorhersage anhand von regelbasierten Entscheidungen, die zunächst über Trainingsdaten angelernt werden. Grundlegend besteht ein Entscheidungsbaum aus dem Wurzelknoten und den Blattknoten. Zwischen dem Wurzelknoten und den Blattknoten liegen die inneren Knoten. Alle Knoten sind dabei über Äste miteinander verbunden [1]. Ein beispielhafter Aufbau eines binären Entscheidungsbaums ist in Abbildung 7 zu sehen.
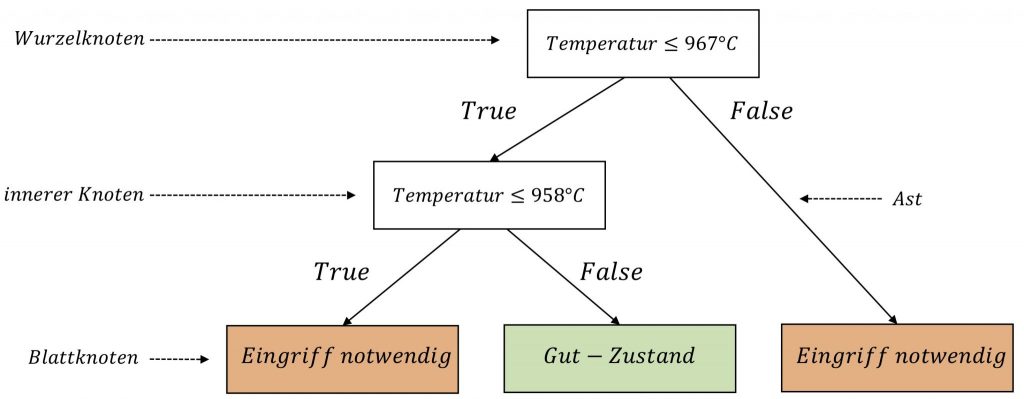
Abbildung 7: Beispielhafter Aufbau eines binä-
ren Entscheidungsbaums mit exemplarischen
Entscheidungsregeln
Bis auf die Blattknoten enthält jeder Knoten eine Entscheidungsregel. Die erste Entscheidungsregel befindet sich im Wurzelknoten. Anhand dieser wird entschieden, welcher Ast als nächstes gewählt wird, um zum nächsten Knoten zu gelangen. Dieser Entscheidungsprozess wird so lange durchgeführt, bis der Blattknoten erreicht wird, der keine Entscheidungsregel, sondern eine entsprechende Vorhersage über die zuvor definierte Zielvariable enthält.
Aus Abbildung 7 geht hervor, dass ein Eingriff notwendig ist, wenn die Temperatur größer als 967°C ist. Ist die Temperatur kleiner oder gleich 967°C, so wird im inneren Knoten ein weiteres Mal die Temperatur abgefragt. Liegt die Temperatur bei dieser Abfrage über 958°C, so befindet sich der Ofen im Gut-Zustand. Andernfalls ist ein Eingriff notwendig, um eine Temperaturänderung hervorzurufen, die den Ofen wieder in den Gut-Zustand überführen soll.
Entscheidungsbäume sind in der Regel komplexer aufgebaut als der in Abbildung 7 exemplarisch dargestellte Baum. Weiterhin muss vorab eine bestimmte Zielvariable festgelegt werden, damit überhaupt ein Lernvorgang stattfinden kann. Meistens ist für eine geeignete Festlegung der Zielvariable zusätzliches Expertenwissen notwendig. Die in Abbildung 7 gewählte Zielvariable besteht lediglich aus zwei Klassen – Gut-Zustand oder Eingriff notwendig.
Durch die grafische Visualisierung der Baumstruktur ist es möglich die Entscheidungsfindung und somit die internen Zusammenhänge des Modells zu verstehen. So können unter anderem die Prozessvariablen identifiziert werden, die einen hohen Einfluss auf die jeweiligen Vorhersagen der Zielvariable besitzen. Durch die Einblicke in die Baumstruktur können neue Erkenntnisse über die vorliegende Vorhersageproblematik gewonnen und mit den jeweiligen Ingenieuren geteilt werden. Entscheidungsbäume eignen sich deshalb nicht nur für die Vorhersage von Zielvariablen, sondern können auch dazu verwendet werden, um neues Wissen anhand der gesammelten Daten zu generieren.
Eine erweiterte Modellform stellt das Random Forest Modell dar, das grundsätzlich aus mehreren Entscheidungsbäumen besteht. Nach dem Trainingsvorgang führt jeder einzelne Entscheidungsbaum anhand von neuen Daten eine Vorhersage über die Zielvariable durch, die am Ende zu einer einzigen Entscheidung bzw. Vorhersage zusammengefasst werden. Durch die Verwendung des Random Forests erhöht sich die Komplexität des Modells, die aber zu einer besseren Modell-Performanz führen kann. Der LfA nutzt diesen Modelltypen, um entsprechende Prozessvariablen innerhalb der Aluminiumelektrolyse vorherzusagen. Mit diesen Vorhersagen soll anschließend eine Optimierung der Prozessführung in der Aluminiumelektrolyse erreicht werden.
Fazit
Zusammen mit der TRIMET Aluminium SE erforscht und entwickelt der Lehrstuhl für Automatisierung/Informatik der Bergischen Universität Wuppertal Lösungen für die intelligente und flexible Energienutzung innerhalb der Aluminiumelektrolyse. Die ersten Forschungsergebnisse zeigen das Potenzial von moderner Messtechnik und Machine Learning für die Erkennung von Ofenstörungen und die Optimierung der Prozessführung. So können mittels einer kontinuierlichen Anodenstrommessung Anodeneffekte und Anodenspitzen präventiv erkannt und die Effizienz des Prozesses erhöht werden. Vor allem der Einsatz von prädiktiven Modellen, die den Ofenbetrieb fortlaufend überwachen und zusätzliche Informationen liefern, können für den Prozessingenieur bei bestimmten Entscheidungen behilflich sein. Hierzu stellen Entscheidungsbäume einen vielversprechenden Ansatz dar, deren Einsatz in der Aluminiumelektrolyse durch den LfA intensiv untersucht wird. Dabei zeichnen sich Entscheidungsbäume durch ihre transparente Modellstruktur aus. Weiterführende Arbeiten liegen vor allem in der Vorverarbeitung der Daten, der Datenanalyse sowie der Verwendung von weiteren Modelltypen, die sich sinnvoll in der Aluminiumelektrolyse einsetzen lassen.
Danksagung
Diese Forschungsarbeiten werden von der Europäischen Union und dem Europäischen Fonds für regionale Entwicklung (EFRE) finanziell gefördert. Die Autoren bedanken sich für die Unterstützung.
Literatur
[1] Kelleher, John D. and Namee, Brian Mac and D’Arcy, Aoife: Fundamentals of Machine Learning for Predictive Data Analytics: Algorithms, Worked Examples, and Case Studies. The MIT Press, 2015
Autoren
¹M.Sc. Ron Kremser
¹M.Sc. Niclas Grabowski
Co-Autoren
¹Prof. Dr.-Ing. Dietmar Tutsch
² M.Sc. Thomas Pursche
³Dr.-Ing. Roman Düssel
³Dipl.-Inf. (FH) Kay Kessel
¹Lehrstuhl für Automatisierungstechnik/Informatik
²Lehrstuhl für Automatisierungstechnik/Regelungstechnik
Bergische Universität Wuppertal
Campus Freudenberg
Rainer-Gruenter-Straße 21
42119 Wuppertal
³TRIMET Aluminium SE
Aluminiumallee 1
45356 Essen