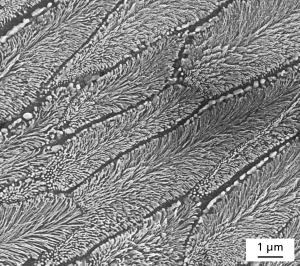
Bild 1: Feine Lamellenstruktur einer mit LMD hergestellten eutektischen Legierung auf Al-Basis
Andreas Weisheit, Fraunhofer-Institut für Lasertechnik
Unter dem Begriff der Additiven Fertigung, auch als 3D Druck bezeichnet, werden heute zahlreiche Verfahren subsummiert. Für metallische Werkstoffe sind die laserbasierten Verfahren im Pulverbett (Laser Powder Bed Fusion, LPBF) und mit Pulver- oder Drahtzufuhrdüse (Laser Metal Deposition, LMD) die wichtigsten, die auch als Laser Additive Manufacturing (LAM) zusammengefasst werden. In beiden Verfahren wird der Werkstoff vollständig aufgeschmolzen und Schicht für Schicht zu einem Bauteil aufgebaut. Die werkzeuglose Fertigung bietet ein hohes Maß an Individualisierung und (fast) unbegrenzte Design-Möglichkeiten. LAM hat in den letzten zwei Jahrzehnten eine rasante Entwicklung erfahren. Am Anfang waren es nur Prototypen, die mit diesem Fertigungsverfahren hergestellt wurden. Rasch kam dann die Herstellung von Unikaten (z. B. Implantate) und Einzelteilen (z. B. Werkzeugeinsätze) hinzu. Heute bewegt sich das Verfahren in Richtung einer Serienfertigung bis zu mehreren Zehntausend Teilen im Jahr. In Forschung und Industrie wird derzeit intensiv an hierfür notwendigen Voraussetzungen wie der Erhöhung der Produktivität, der Qualitätssicherung und der Integration in Prozessketten gearbeitet.
Während es für etablierte Fertigungsverfahren wie Gießen oder Schmieden eine große Palette von angepassten Legierungen gibt, ist die Auswahl für das LAM aber noch überschaubar und zudem fast ausschließlich beschränkt auf Legierungen, die für andere Fertigungsverfahren entwickelt wurden. Ein klassisches Beispiel ist die Gusslegierung AlSi10Mg, die sich mittels LAM hervorragend verarbeiten lässt und deren mechanische Eigenschaften die des Gusszustandes aufgrund des feinen Gefüges übertreffen [1]. Viele andere interessante Legierungen wie hochfeste Aluminium-Knetlegierungen sind jedoch aufgrund von Heißrissbildung nicht verarbeitbar. Defektfreie Volumenkörper über die Anpassung der Verfahrensparameter herzustellen, ist nur begrenzt möglich oder führt oft zu völlig unwirtschaftlichen Prozessbedingungen wie extrem kleiner Aufbaurate oder hoher Vorwärmung. Um das Potenzial des LAM in Zukunft optimal ausnutzen zu können, muss parallel zur Entwicklung der System- und Verfahrenstechnik auch eine Entwicklung maßgeschneiderter Legierungen erfolgen, die an die Bedingungen des Verfahrens angepasst sind und gleichzeitig die gewünschten Eigenschaften erreichen. Als Vorbild kann hier die spezifisch für das LAM entwickelte Legierung Scalmalloy® [2] dienen, eine Aluminium-Scandium-Legierung, die die extrem hohe Erstarrungsrate nutzt, um das Sc in Lösung zu halten, welches bei einer nachfolgenden Auslagerung in Form nanoskaliger intermetallischer Ausscheidungen zur Festigkeitssteigerung beiträgt. Gießtechnisch ist dieses Gefüge nicht zu erreichen, da die Ausscheidungen in grober Form schon bei der Erstarrung gebildet werden und mit einer wirtschaftlichen Wärmebehandlung nicht mehr aufgelöst werden können.
Für eine maßgeschneiderte Legierungsentwicklung müssen die für die Gefügeausbildung spezifischen Charakteristika des LAM näher betrachtet werden. Im Wesentlichen sind dies die hohe Erstarrungsrate und die hohe Abkühlrate im Festen (103 – 106 K/s), die damit einhergehende extrem gerichtete Wärmeabfuhr, die auf ein kleines Schmelzvolumen reduzierte Metallurgie und die zyklische Wiedererwärmung bereits aufgetragener Schichten.
In Bezug auf die rasche Erstarrung sind z. B. eutektische Legierungen interessant. Die Erstarrung dieser Legierungen ist durch die gleichzeitige Ausscheidung zweier fester Phasen aus der Schmelze – häufig in Form von Lamellen – gekennzeichnet. Das Potenzial liegt insbesondere darin, dass Eutektika oft aus einer duktilen Michkristallphase und einer harten intermetallischen Phase bestehen und somit einen guten Kompromiss zwischen Festigkeit und Duktilität in den Eigenschaften bieten. Beim LAM kommt hinzu, das die rasche Erstarrung zu einem kleinen Abstand der Lamellen (Bild 1) bis hin zu nanoskaligen Strukturen führt. Bei derartig feinen Gefügen ist nachgewiesen, dass eine hohe Festigkeit bei noch guter Duktilität erreicht werden kann [3]. Ein erweitertes Eigenschaftsspektrum kann zudem erreicht werden, wenn die Zusammensetzung unter- oder übereutektisch eingestellt wird. Im ersten Fall wird die Legierung durch primäre Ausscheidung des Mischkristalls duktiler, im zweiten Fall härter durch primäre Ausscheidung der intermetallischen Phase. Durch Zugabe weiterer Elemente, die aufgrund der hohen Abkühlrate im Festen in Lösung bleiben, kann die Festigkeit durch Ausscheidungshärtung weiter gesteigert werden. Die Ausscheidung kann dabei auch intrinsisch erfolgen, indem die zyklische Wiedererwärmung bereits aufgetragener Schichten genutzt wird. Hierzu ist aber eine ausreichend hohe Ausscheidungskinetik erforderlich.
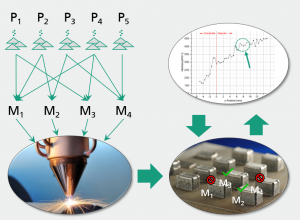
Bild 2: Rapid Alloy Development mittels LMD; Herstellung von Volumenkörpern aus Pulvermischungen (M1 = P1 + P2, …), Charakterisierung und Auswahl
Durch die lokale Metallurgie ist auch sichergestellt, dass die Feinheit des Gefüges unabhängig von Geometrie und Volumen des Bauteils ist, da ein immer gleich großes Volumen des Werkstoffes im Fertigungsprozess flüssig ist und die lokalen Abkühlbedingungen daher weitgehend konstant sind. Eine eutektische Erstarrung verhindert auch weitgehend das gerichtete Wachstum von Körnern wie es für einphasig erstarrende Legierungen typisch ist und häufig zu unerwünschten anisotropen Eigenschaften führt. In einem gerade gestarteten Verbundprojekt der Fraunhofer-Institute ILT, IWM und IGCV werden eutektische Aluminiumlegierungen u. a. für das LAM entwickelt, die sich diese Effekte zu Nutze machen und die die Eigenschaften der klassischen Al-Si-Legierungen deutlich übertreffen sollen.
Die Entwicklung einer neuen Legierung bis hin zur Qualifizierung für eine Anwendung ist in der Regel ein langwieriger Prozess von vielen Jahren. Wenn die Zertifizierung sicherheitsrelevanter Bauteile mit eingeschlossen ist, sind 10 Jahre und mehr keine Seltenheit. Dies ist häufig ein Grund für die Industrie, sich neuen Werkstoffen nicht selbst zu widmen und dies zunächst Wissenschaftseinrichtungen zu überlassen. Ein beschleunigtes Verfahren kann die Hemmschwelle herabsetzen. Auch hier ist das LAM eine Methode die eingesetzt werden kann als ein Verfahren des Rapid Alloy Development (RAD). Das LMD bietet dafür ideale Möglichkeiten [4]. Für ein erstes Screening von Legierungen bedarf es dabei nicht dem Vorliegen von entsprechenden Legierungspulvern, sondern es können Elementpulver in der gewünschten Zusammensetzung eingesetzt werden. Die Legierung entsteht dann erst im Schmelz- und Erstarrungsprozess. Da im Prinzip die Zusammensetzung durch Einstellung der Zufuhrparameter oder Verwendung anderer Mischungen in jeder aufgetragenen Lage geändert werden kann, sind gradierte Volumenkörper herstellbar, so dass in einer einzigen Probe schon verschiedene Legierungen hinsichtlich des Gefüges charakterisiert werden können. Das LMD ermöglicht zudem die rasche Herstellung unterschiedlichster Prüfkörper, die zur Bestimmung relevanter Gebrauchseigenschaften wie Festigkeit, Verschleißwiderstand oder Korrosionsbeständigkeit genutzt werden können. In Kombination mit modernen Methoden der digitalen Werkstoffentwicklung, die Vorhersagen von Phasenzusammensetzungen und Eigenschaften erlauben, kann so die Auswahl potentiell interessanter Werkstoffe rasch eingegrenzt werden. Nur noch eine kleine Auswahl von Zusammensetzungen muss dann als Legierungspulver hergestellt werden. Auch diese methodische Vorgehensweise soll in dem oben genannten Verbundprojekt erarbeitet und validiert werden.
Die Entwicklung von maßgeschneiderten Legierungen ist ein wichtiger Technologietreiber für die industrielle Umsetzung der Additiven Fertigung insbesondere für die Serienfertigung. Nur wenn hier eine ausreichend große Vielfalt gegeben ist, kann das Verfahren viele Anwendungsbereiche durchdringen.
Literatur
[1] Buchbinder, D.: Dissertation, RWTH Aachen, 2013, ISBN: 978-3-8440-2439-5
[2] Schmidtke, K., et al.: Phys. Procedia 12, 2011
[3] Suwanpreecha, C., et al.: Materials Science and Engineering A, Vol. 709, 2018
[4] Knoll, H., et al.: steel research int. 87, 2017, No. 9999