Hintergrund
Die Blechumformung bietet eine Vielzahl von Möglichkeiten Bleche zu bearbeiten. Neben dem allgemein bekannten Tiefziehen und dem Innenhochdruckumformen gibt es eine Variante der Blechbearbeitung die weniger bekannt ist. Der vorliegende Artikel gibt einen kleinen Einblick in die inkrementelle Blechumformung (IBU).
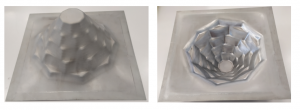
Abbildung 1: Tiefziehblech DC06 s0=0,8 mm; β=55°; Drücktiefe 100 mm
Verfahrensvarianten
Die IBU ist im Wesentlichen in vier Varianten unterteilt. IBU ohne Unterstützung, IBU mit Unterstützung (Vollpatrize), IBU mit partieller Unterstützung (Teilpatrize) und IBU mit zwei Umformwerkzeugen. Um die einfachste Variante der IBU durchführen zu können bedarf es einer 3-Achs CNC Fräsmaschine, eines Werkzeuges in Form eines Drückdorns und eines Werkstückhalters mit entsprechendem Freiraum um die gewünschte Drücktiefe zu erreichen. Dabei werden aus Blechen räumliche Körper erzeugt. Das Verfahren kann mit dem 3D-Druck verglichen werden, bei dem einzelne Schichten des Körpers parallel zur Z-Achse angeordnet sind und stufenweise bearbeitet werden. Nach der kompletten Bearbeitung einer Ebene bzw. dem Abfahren der ganzen Kontur einer Schicht, erfolgt die Zustellung in Z-Richtung, um die nächste Schicht zu bearbeiten. Durch das Abfahren der Höhenlinien ist die reine inkrementelle Blechumformung ein zeitintensives Verfahren. Für das in Abbildung 1 dargestellte Bauteil wurde bei einer Zustellung in Z-Richtung von 0,4 mm eine Bearbeitungszeit von 55 Minuten benötigt. Zur Vermeidung der Ausbildung von Zustellmarken an einer x-/y-Koordinate empfiehlt es sich eine spiralförmige Zustellung zu verwenden.
An dem Beispiel in Abbildung 1 ist, unter Verwendung der IBU ohne Unterstützung, ein 0,8 mm dickes Tiefziehblech (DC06) um einhundert Millimeter in die Tiefe umgeformt. Der Kegelwinkel beträgt 55°. Anders als beim klassischen Tiefziehen, bei dem die Wandstärke nicht verändert wird, erfährt das Blech beim IBU-Verfahren eine Materialabstreckung auf einen bestimmten Wert. Dieser kann mit dem vom Projizierdrücken bekannten Sinus-Gesetz berechnet werden.
s1= s0 * sin(90°- β)
Hierbei entspricht s0 der Ausgangsdicke des Materials und β dem Kegelwinkel. Der Kegelwinkel und die damit verbundene Materialabstreckung ist ein Grenzwert für die Umsetzung einer Bearbeitung im IBU- Verfahren ohne Unterstützung. Wenn der Kegelwinkel zu steil gewählt ist, kommt es zum Materialversagen in Form von Rissbildung. Für das oben genannte Bauteil berechnet sich eine Materialabstreckung auf s1 = 0,459 mm. In Abbildung 2 ist das Bauteil im Halbschnitt dargestellt und es sind fünf Messpunkte angegeben die die Materialabstreckung nach der Umformung anzeigen. Die gemessenen Werte ergeben eine annähernd gute Übereinstimmung mit den berechneten. Allerdings liegt die Maß- und Formgenauigkeit bei der IBU Variante ohne Unterstützung im Bereich von einigen Millimetern. In Abbildung 2 sind links im Bild die Geometrie und die Verfahrwege des Werkzeuges dargestellt. Das Fertigteil nach erfolgter Bearbeitung rechts im Bild weist an den Übergängen erhebliche Abweichungen auf. Diese können durch Unterstützung in Form einer Teil- oder Vollpatrize minimiert werden. Dennoch ist auch ohne Patrize eine Wiederholgenauigkeit gegeben, sodass die Formabweichungen reproduzierbar sind. Somit sind Maßnahmen zur Reduzierung der Formabweichung möglich.
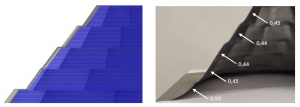
Abbildung 2: Blechteil DC06 im Halbschnitt. Links: Verfahrwege CAM. Rechts: fertig gedrücktes Blech
Anwendungsmöglichkeiten
Durch die erheblich reduzierten Werkzeugkosten gegenüber dem Tiefziehen ist das Verfahren für die Prototypenherstellung und Kleinserien besonders gut geeignet. Unter anderem zeigen die Herstellung von Unikaten für den medizinischen Bereich z. B. Blechmaske für die Anpassung von Schnarchmasken; individuelle Beinstützen oder Titanblech- Anwendungen in der Zahnmedizin interessante Einsatzgebiete für diese Technologie auf. So kann aus einem 3D-Scan des Kopfes eine Schädelplatte modelliert und gefertigt werden. Zur Veranschaulichung ist exemplarisch in Abbildung 3 dargestellt wie mit Hilfe der Fotogrammetrie aus mehreren Bildern ein 3-Dimensionaler Körper, anschließend ein Netzkörper und schließlich das fertige Werkstück erstellt wurde. Die Datenerfassung der Körper kann mittels 3D-Scannern, Fotogrammetrie oder über eine CAD Software erstellt werden. Die Verfahrwege sind mit einer geeigneten CAM-Software zu generieren.
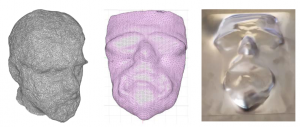
Abbildung 3: Von links nach rechts: Dreidimensionaler Körper nach Fotogrammetrie, bearbeiteter Netzkörper, fertig gedrücktes Werkstück (AlMg3) s0=2mm
Kombinationsmöglichkeiten mit anderen Verfahren
Das herkömmliche IBU-Verfahren lässt sich auch mit anderen Verfahren kombinieren. So kann z.B. eine Kombination aus IBU mit Patrize und gleichzeitigem Streckziehen erhebliche Vorteile bringen. Während beim inkrementellen Blechumformen die Grenzen durch den Kegelwinkel und der Materialabstreckung schnell erreicht sind, kann durch das eingebundene Streckziehen das Material vorgeformt und im Anschluss mit Vertiefungen und Hinterschneidungen mittels der richtigen Umformstrategie hergestellt werden. Ebenfalls lässt sich die Herstellungszeit erheblich minimieren. Eine weitere Kombinationsmöglichkeit ist die inkrementelle Blechumformung mit Additiven Verfahren. So kann nach erfolgter Umformung individuell und lokal eine Auftragsschweißung erfolgen um Nebenformelemente für eine optimierte Gestaltung zu erzeugen.
Referenz
[1] Dietrich, J. (2018). Praxis der Umformtechnik (Bd. 12. Auflage). Dresden: Springer. ISBN: 978-3-658-19530-4
Bilder: B.Eng. Pierre Rene Kurrat
Autoren:
Prof. Dr.-Ing. Bernd Hager,
B. Eng. Pierre Rene Kurrat
Labor für Umformtechnik
Hochschule Hannover