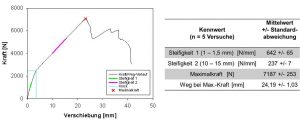
Abbildung 1: Typischer Kraft/Verschiebungs-Verlauf mit Auswertungskriterien (links) und ermittelte mechanische Kennwerte fehlerfreier Referenzproben (rechts)
Einleitung
Nachdem im ersten Teil dieser Artikelserie die Identifikation von typischen Fehlern in Klebverbindungen sowie die Klassierung und Abstraktion zu generischen Fehlerformen und deren Implementierung in Laborproben beschrieben wurde, soll in diesem zweiten Teil nun auf die Bewertung dieser Fehlerarten eingegangen werden. Diese Schadensbewertung geschieht vor dem Hintergrund, dass Fertigungsbetriebe und Betreiber von geklebten Strukturen in der Lage versetzt werden sollen die Gefährdung, die von fehler- und schadhaften Klebverbindungen ausgehen kann, im Rahmen eines Risikomanagements zu beurteilen. Im dritten und letzten Teil der Artikelserie werden dann zerstörungsfreie Prüfverfahren und Methoden vorgestellt, mit denen entsprechende Imperfektion in Klebverbindungen detektiert werden können.
Experimentelle Untersuchungen zur Schadensbewertung und Ermittlung des Schädigungspotenzials
Um die Auswirkungen von unterschiedlichen Fehlern und Imperfektionen auf das mechanische Verhalten von Klebverbindung zu untersuchen, werden vergleichende experimentelle Laborversuche an fehlerfreien und fehlerbehafteten Klebungen durchgeführt. Dies hat zum Ziel Abminderungsfaktoren und so das Schädigungspotenzial spezifischer Imperfektionen ableiten zu können.
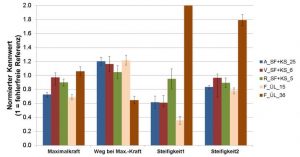
Abbildung 3: Normierte Kennwerte der Versuchsreihen (V=Volumen-, A=Adhäsions-,R=Rissfehler, F=Fehlbildung Klebschicht und Sichtfuge).
Hochelastischer Dickschichtklebstoff
Beispielhaft für die Klasse der hochelastischen Dickschichtklebstoffe wurde der Klebstoff Sikaflex 268 Powercure ausgewählt und untersucht. Für die Versuche wurde eine bauteilähnliche Probenform verwendet, die eine Scheibenklebung abbildet (s. Abbildung 3 des ersten Teils der Artikelserie). Die Probe besteht aus zwei gestuften Aluminium-Fügeteilen mit einer Breite von 50 mm. Die Klebschicht (rot) besitzt eine Dicke von 8 mm und eine Überlappungslänge von 30 mm. Die Sichtfuge (orange) weist eine Dicke von 10 mm und eine Höhe von 33,5 mm. Beide Fugen wurden mit dem o.g. Klebstoff ausgeführt. Zur Verbesserung der Haftung wurden die Klebflächen gestrahlt und mit dem Sika Schwarzprimer 207 vorbehandelt.
Die im ersten Teil vorgestellten Fehlertypen (Volumen-, Adhäsions- und Rissfehler) wurden jeweils in drei Größenausprägungen (klein, mittel, groß) sowohl nur in die Klebschicht und die Sichtfuge jeweils als auch gleichzeitig in beide Bereiche eingebracht. Adhäsionsfehler wurden auf dem Fügeteil ausgeführt, das die metallische Schiffsstruktur (Rahmen) darstellt. Bei der Untersuchung zur Fehlbildung von Klebschicht und Sichtfuge wurde eine Variation der Überlappungslänge der Klebschicht in vier Ausprägungen vorgenommen. Eine Vergrößerung der Überlappungslänge führt dabei zu einer entsprechenden Verringerung der Sichtfugenbreite und umgekehrt.
Die Proben wurden in quasi-statischen Kurzeitversuchen bis zum vollständigen strukturellen Versagen der Klebschicht wegkontrolliert mit einer Traversengeschwindigkeit von 20 mm/min bei Raumtemperatur geprüft. In Abbildung 1 (links) sind am Beispiel eines typischen Kraft/Verschiebungs-Verlaufs verschiedene Kennwerte definiert, die im Weiteren als Auswertungskriterien und zum Vergleich verschiedener Kraft/Verschiebungs-Verläufe benutzt werden. Im Anfangsbereich ist nach etwa 3 mm Verschiebung ein deutlicher Steifigkeitsunterschied zu erkennen, der durch einen charakteristischen „Knick“ in der Kurve beschrieben wird. Die Ursachen dieses Steifigkeitsunterschieds, der ohne äußerliche Anrisse an Klebschicht und Sichtfuge auftritt, sind noch nicht abschließend geklärt. Es wird vermutet, dass es im Inneren der Probe am Übergang von der Klebschicht zur Sichtfuge zu diesem Zeitpunkt zu einer Kavitäts- und Rissbildung kommt, die durch den dort vorherrschenden hohen hydrostatischen Zugspannungszustand ausgelöst wird. Dadurch reduziert sich die bis dahin vorliegende Dehnungsbehinderung des Klebstoffs lokal und die Probe zeigt eine wesentlich größere Nachgiebigkeit, was sich in der reduzierten Steifigkeit ausdrückt. Insgesamt ist festzustellen, dass die Steifigkeit der Probe maßgeblich von der Sichtfuge bestimmt wird. Die Klebschicht leistet erst nach dem An- bzw. Abreißen der Sichtfuge einen nennenswerten Beitrag zum Tragverhalten der Klebverbindung. Die im Kraft/Verschiebungs-Verlauf farbig markierten Kennwerte sind für eine Versuchsreihe von fünf fehlerfreien Referenzproben in der Tabelle in Abbildung 1 dargestellt. Insgesamt ist eine sehr geringe Streuung der Kennwerte zu beobachten, was eine gute und reproduzierbare Fertigungsqualität der Proben belegt.
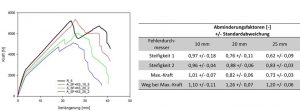
Abbildung 2: Typische Kraft/Verschiebungs-Verläufe von Proben mit unterschiedliche großen Adhäsionsfehlern in Klebschicht und Sichtfuge (rot: Drm. 10 mm, grün: Drm. 20 mm, blau: Drm. 25 mm) sowie schwarz dargestellt der repräsentative Verlauf einer fehlerfreien Referenzprobe (links) und ermittelte Abminderungsfaktoren mit Angabe des entsprechenden ursächlichen Fehlerdurchmessers (rechts)
Die Referenzwerte kRef werden im Folgenden benutzt, um die normierten maximalen Abweichungen A für Proben mit Imperfektionen zu ermitteln. In der Regel sind diese Abweichungen als Abminderungen Ai=ki ⁄kRef mit Ai<1 zu verstehen. Für das Beispiel einer Versuchsreihe mit verschieden großen Adhäsionsfehlern, die in Klebschicht und Sichtfuge vorliegen, sind in dem Graph in Abbildung 2, links entsprechende repräsentative Kraft/Verschiebungs-Verläufe dargestellt. Deutlich ist zu erkennen, wie die Kurven von Proben mit zunehmender Fehlergröße weitgehend unter der der fehlerfreien Referenzprobe verlaufen. Gegenüber den fehlerfreien Referenzproben ergeben sich auf Grundlage von Versuchsreihen mit jeweils drei Wiederholversuchen Abminderungen für die betrachteten Fehlerdurchmesser bezgl. der Anfangssteifigkeit (Steifigkeit 1) von bis zu 38% und bezüglich der Maximalkraft von bis zu 27% (Abbildung 2, rechts, Tabelle). Statt einer Abminderung erfährt die Verschiebung bei Maximalkraft stets eine Steigerung um bis zu ca. 26%, was auf ein stärkeres Mittragen der Klebschicht hinweist.
Die relativen Veränderungen der Kennwerte von Versuchsreihen mit Fehlern, die sich am stärksten hinsichtlich der definierten Kennwerte ausgewirkt haben, sind im Diagramm in Abbildung 3 dargestellt. Hierbei lagen die Fehler jeweils in der größten Ausprägung sowohl in der Klebschicht als auch in der Sichtfuge vor. Bei der Fehlbildung der Sichtfuge wurde neben einer 1,5-fach verbreiterten Sichtfuge (F_ÜL_15) auch das andere Extrem einer 60% dünneren Sichtfuge (F_ÜL_36) betrachtet.
Zusammenfassend lässt sich feststellen, dass Fehlbildungen der Sichtfuge (verbreitert oder dünner) drastische Veränderungen insbesondere der Anfangssteifigkeit hervorrufen können. Diesbezüglich sind auch große Adhäsions- und Volumenfehler mit einer Steifigkeitsabnahme um bis zu -40% als kritisch zu bewerten. Abminderungen durch diese Fehler bezüglich der globalen Steifigkeit 2 sind dagegen deutlich geringer (bis -20%). Lediglich eine schmal ausgebildete Sichtfuge erhöht hier weiterhin die Steifigkeit deutlich. Die Tragfähigkeit der Klebverbindung wird am stärksten durch Adhäsionsfehler und breite Sichtfugen um bis zu ca. -30% reduziert. Volumen- und Rissfehler zeigen sich diesbezüglich nahezu unauffällig. Hingegen bewirken alle Fehler eine moderate Erhöhung der Verschiebung zum Zeitpunkt des Auftretens der Maximalkraft. Als Fazit lässt sich festhalten, dass Fehlbildungen der Klebfugengeometrie (insbesondere der Sichtfugenbreite) zu vermeiden sind. Ebenso sollten Volumen und Adhäsionsfehler vermieden werden. Als weniger kritisch haben sich Rissfehler herausgestellt.
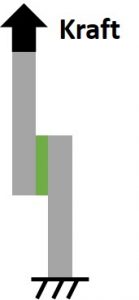
Abbildung 4:
Zugscherversuch
Hochfester Strukturklebstoff
Für die Klasse der Strukturklebstoffe wurde exemplarisch der Klebstoff Scotch-Weld 7271 B/A der Firma 3M untersucht. Als Probenform wurde in Anlehnung an DIN EN 1465:2009-07 eine einschnittig überlappte Zugscherprobe gewählt. Die Klebschichtbreite und Überlappungslänge betrugen jeweils 50 mm, die Klebschichtdicke 5 mm. Die Fügeteile bestehen aus einer 10 mm dicken Aluminiumlegierung, die vor dem Kleben mit Korund gestrahlt und mit Methylethylketon (MEK) gereinigt wurden. Die Prüfung der Proben erfolgte unter quasistatischer Zugscherbeanspruchung bis zum strukturellen Versagen der Proben (vgl. Abbildung 4). Für Probenserien ohne und mit Imperfektionen wurden Festigkeitswerte ermittelt. Wie im ersten Artikel beschrieben, sollen die Proben mit Fehlstellen: 1. Einschlüsse in der Klebschicht, 2. Adhäsionsverluste in der Grenzschicht der Klebung sowie 3. Einschnürungen im Randbereich der Klebverbindung simulieren. Die Imperfektionen werden dabei rasterförmig (Einschlüsse), zentral (Adhäsionsverluste) bzw. quer und längs zur Zugrichtung bei den zerstörenden Prüfungen (Einschnürungen) in verschiedenen Ausprägungen in die Klebung eingebracht. Zur Übersicht sind alle Probenserien in Tabelle 1 aufgeführt. Eine Probenserie besteht dabei aus sechs Proben. Aus den Ergebnissen der einzelnen Zugscherproben wird anschließend ein Mittelwert gebildet.
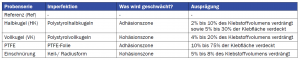
Tabelle 1: Probenserien für die zerstörenden Prüfungen
Während der zerstörenden Prüfung werden u.a. die Kraftmaxima aufgezeichnet. Diese Werte symbolisieren die Kräfte, die die verschiedenen Klebschichten maximal ertragen konnten, bis sie nachgeben und zerstört werden. Die maximalen Kräfte können anschließend untereinander zwischen den verschiedenen Probenserien verglichen werden, was Aufschluss über das Schädigungspotenzial der verschiedenen Fehlstellen gibt. Anschließend werden die Mittelwerte der Kraftmaxima einer Probenserie mit Fehlstellen in Relation zu der Referenzserie ohne Imperfektionen gesetzt, um einen Abminderungsfaktor berechnen und somit das Schädigungspotenzial dieser Fehlstelle einschätzen zu können.
Die Werte für die Imperfektionen, welche vorrangig die Adhäsionszone schwächen (Halbkugeln und PTFE), sind auf Abbildung 5 im Vergleich mit den Referenzwerten dargestellt.
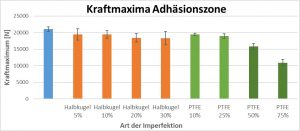
Abbildung 5: Vergleich der Kraftmaxima bei den Probenserien, die die Adhäsionszone schwächen
Das Diagramm zeigt, dass die Fehlstellen, welche primär die Adhäsionszone schwächen, generell eine negative Auswirkung auf die Festigkeit einer Klebung haben. Dieser schwächende Einfluss nimmt zu, je größer die Ausprägung der Imperfektionen in der Klebung wird. Bei den Halbkugeln als auch der PTFE-Folie bewegt sich die Festigkeitsabnahme im Vergleich zu einer intakten Klebung in einem Bereich von ca. 10%, sofern bis zu 30% der ursprünglichen Klebfläche verdeckt sind. Wird die Ausprägung der Fehlstellen größer (PTFE-Folie 50% und 75%), nimmt der negative Einfluss rapide zu. Dies spiegelt sich sowohl im Diagramm als auch in den Abminderungsfaktoren in Tabelle 2 wider.

Tabelle 2: Vergleich der Abminderungsfaktoren bei den Probenserien, die die Adhäsionszone schwächen
Die Werte, welche wesentlich die Kohäsionszone schwächen (Vollkugel und Einschnürung), sind auf Abbildung 6 im Vergleich mit den Referenzwerten dargestellt.
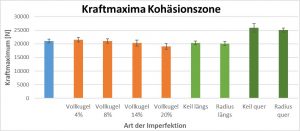
Abbildung 6: Vergleich der Kraftmaxima bei den Probenserien, die die Kohäsionszone schwächen
Im Diagramm ist ersichtlich, dass die Vollkugeln zunächst keine Schwächung der Klebfestigkeit herbeiführen. Erst mit steigender Ausprägung tritt der negative Einfluss auf und wird stärker, je mehr Polystyrolvollkugeln sich in der Klebschicht befinden. Auch die Einschnürungen längs zur Zugrichtung setzen das Kraftmaximum nur sehr wenig im Vergleich zur Referenzserie herab. Bei den Einschnürungen quer zur Zugrichtung werden die Kraftmaxima hingegen bis zu 23% erhöht (vgl. Tabelle 3), obwohl Klebstoffvolumen entfernt wurde.

Tabelle 3: Vergleich der Abminderungsfaktoren bei den Probenserien, die die Kohäsionszone schwächen
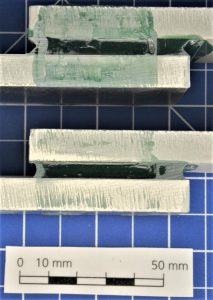
Abbildung 7: Einschnürungen im Randbereich der Klebung
Die Keil- bzw. Radiusformen im Randbereich der Klebschicht (vgl. Abbildung 7) wirken sich positiv aus, da sie Spannungsspitzen dort abbauen, wo der Riss beim Versagen der Klebung entsteht und diese somit mehr Kraft ertragen kann. Dies gilt jedoch nur für genau diesen Belastungsfall. Es zeigt jedoch, dass mit einer auf die Belastungen angepassten Klebschichtgeometrie zum einen Klebstoff gespart und zum anderen die Festigkeit erhöht werden kann.
Aus allen Ergebnissen wird ersichtlich, dass Fehlstellen in der Klebschicht einen negativen Einfluss auf die Festigkeit dieser haben. Die Schwächung wird umso größer, je größer die Ausprägung der Imperfektionen sind. Des Weiteren erweisen sich die Fehlstellen, die primär die Adhäsionszone schwächen, als schädigender gegenüber denen, welche im Wesentlichen die Kohäsionszone beeinträchtigen. Darüber hinaus können wider erwarten mit Einschnürungen in den Randbereichen der Klebung sogar positive Effekte erzielt werden, sofern diese entsprechend der Belastungsrichtung platziert werden.
Weiterführende Untersuchungen
Mit Hilfe der vorgestellten Untersuchungen konnte das Schädigungspotential der unterschiedlichen Fehlerausprägungen systematisch untersucht werden. Die Methoden und Möglichkeiten diese Fehlstellen zerstörungsfrei zu detektieren, werden in dem dritten und abschließenden Artikel „Inspektionsmethoden für die wiederkehrende Prüfung hochelastischer Dickschicht- und Strukturklebungen in Schiffbauanwendungen – Teil 3 (Fehlstellendetektion mit Hilfe von zerstörungsfreien Prüfverfahren)“ in der nächsten Ausgabe dargestellt.
Autoren:
Dr.-Ing. Oliver Klapp
E-Mail: oliver.klapp@ifam.fraunhofer.de
Tel.: +49 421 2246-479
Christopher Wald
E-Mail: christopher.wald@igp.fraunhofer.de
Tel.: +49 381 49682-564