Einleitung
Keramische Faser-Verbundwerkstoffe (engl.: Ceramic Matrix Composites – CMC) bilden eine Werkstoffklasse, die die Vorzüge monolithischer Keramiken (z.B. Hochtemperaturstabilität, Oxidationsbeständigkeit, Korrosionsbeständigkeit) mit schadenstolerantem Versagensverhalten kombiniert. Dadurch ist es möglich CMC als Strukturbauteile einzusetzen, die nicht nur auf Druck (monolithische Keramik) sondern auch auf Zug oder Biegung belastet werden können und dabei gleichzeitig eine verbesserte Thermoschockbeständigkeit aufweisen. Allerdings ist die Verwendung keramischer Fasern sehr kostenintensiv, weshalb es die Vorzüge eines solchen Bauteils gegenüber der Fertigung aus monolithischen Keramiken oder Metallen für die meisten Anwender aus wirtschaftlicher Sicht nicht rechtfertigt. Im Rahmen des AiF-Projekts „ForWerk“ (Formstabile Werkzeugisolation im Kraftfluss mit verbesserten thermischen Kennwerten aufgrund eines hybriden Aufbaus; Vorhaben-Nr. 20646 N) soll nun die Entwicklung eines Hybridbauteils aus CMC und einer neuartigen, porösen Keramik erfolgen, um die Bauteilkosten zu senken und gleichzeitig die Vorteile der verwendeten Materialien für die Anwendung auszunutzen. Für die Herstellung der neuartigen Teilkomponente wird ein mit Keramikpartikeln hochgefülltes Papier verwendet, welches über konventionelle Papiermaschinen gefertigt und zu einer sogenannten papierabgeleiteten Keramik versintert werden kann (vgl. Einschub „Papierabgeleitete Keramik“).
Formstabile Wärmeisolation als mögliche Anwendung für ein Hybridbauteil
Die Blech- und Rohrwarmumformung spielt vor allem im modernen Automobilbau eine wichtige Rolle. Moderne Warmumformprozesse werden zunehmend so ausgelegt, dass sie Umformung und Wärmebehandlung überlagern (thermomechanische Behandlung). Der schematische Aufbau eines solchen Warmumformwerkzeugs ist in Abbildung 1 dargestellt. Die dafür erforderlichen Temperaturen unterscheiden sich je nach Verfahren und Werkstoff. Höchste Anforderungen stellt beispielsweise die superplastische Umformung von Titanwerkstoffen (z.B. Ti-6Al-4V) mit Temperaturen bis 900 °C [1]. Um isotherme Bedingungen bei der Umformung sicherzustellen, muss das Werkzeug konstant auf Umformtemperatur geheizt werden, wobei ein Wärmeabtransport aus dem Werkzeug in die Presse aus mehreren Gründen unbedingt zu verhindern ist. Zum einen können die erforderlichen Werkzeugtemperaturen ohne ein ausgereiftes Isolationskonzept nicht erreicht werden, zum anderen sind die verschiedenen Komponenten der Presse nicht für erhöhte Temperaturen ausgelegt, was insbesondere zu Überhitzungen und Schädigungen an hydraulischen und elektrischen Bestandteilen führen kann. Entsprechend wäre eine thermische Isolation im Kraftfluss zwischen Werkzeug und Aufnahme der Presse sinnvoll. Nach aktuellem Stand der Technik kommt nur ein OFC-Material infrage, um die hohen mechanischen und thermischen Eigenschaften zu erfüllen. Dieses ist jedoch als Vollmaterial sehr preisintensiv. Daher wird zum Schutz der Pressenkomponenten in der Regel aktiv mit Wasser gekühlt, wodurch ohne eine geeignete Isolation große Energieverluste zu verzeichnen sind und damit die Wirtschaftlichkeit stark beeinträchtigt wird.
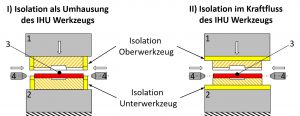
Abbildung 1: Schematischer Aufbau eines beheizten Presswerkzeugs zur Innenhochdruckumformung mit Wärmeisolation als Umhausung (links) bzw. im Kraftfluss (rechts); 1 – Pressenstößel, 2 – Pressentisch, 3 – Werkstück, 4 – Dichtstempel
Die Entwicklung einer solchen formstabilen Isolation ist Ziel des Forschungsprojekts „ForWerk“ und soll, wie eingangs beschrieben, als Hybrid-Bauteil bestehend aus oxidischem CMC (genauer: oxide fiber composite – kurz: OFC) und monolithischer, papierabgeleiteter Keramik realisiert werden. Hier können die Vorteile beider Komponenten insofern vorteilhaft miteinander kombiniert werden, als dass das OFC als tragende Rahmenstruktur die mechanische Belastung (Schließkraft der Presse) aufnimmt, während die papierabgeleitete Keramik als mechanisch entkoppelter Füllstoff hauptsächlich die Funktion der thermischen Isolation übernimmt und gleichzeitig die Kosten des Gesamtbauteils senkt. Da beide Materialien Oxide sind, sind sie trotz der hohen Werkzeugtemperaturen an Luftatmosphäre oxidationsstabil und damit sicher einsetzbar. Die Auslegung und Optimierung des Bauteils hinsichtlich dessen Höhe sowie des geometrischen Aufbaus der Rahmenstruktur erfolgt mittels einer Simulationssoftware (LS-DYNA). Eine mögliche Geometrie ist in Abbildung 2 dargestellt. Der OFC-Rahmen begrenzt dabei zwei rechteckige Inlays aus papierabgeleiteter Keramik.
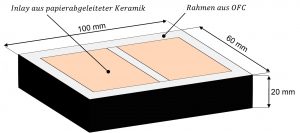
Abbildung 2: Skizze des Aufbaus einer Hybridisolation aus papierabgeleiteter Keramik (Inlays) und OFC-Keramik (Rahmen)
Materialentwicklung
Die zum Aufbau des Rahmens verwendeten OFC werden aus Nextel™720-Fasern (3M) und einer mullitbasierten Matrix hergestellt. Die Verwendung von Mullit als Faser- und Matrixmaterial ist für diese Anwendung dem mechanisch stabileren Aluminiumoxid (Al2O3) vorzuziehen, da die Wärmeleitfähigkeit mit 6 W/mK bei Raumtemperatur (bzw. 3,5 W/mK bei 1000 °C) im direkten Vergleich zu Al2O3 (20 – 30 W/mK) eine bessere thermische Gesamtperformance des Bauteils ermöglicht. Die mit der niedrigeren Festigkeit des Mullits einhergehenden Nachteile gegenüber Al2O3 können über konstruktive Maßnahmen (Verbreiterung der Stege) vergleichsweise einfach angepasst werden.
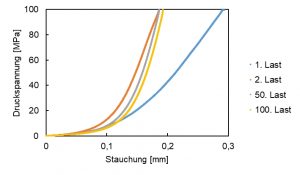
Abbildung 3: Mechanisches Verhalten des OFC im Druckversuch mit Mehrfachbelastung bis 100 MPa
Da die Anwendung in der Presse einer reinen Druckbelastung entspricht, wurden Druckversuche zur mechanischen Charakterisierung der hergestellten Probekörper durchgeführt. Hierfür wurde über die Werkzeuggeometrie, die Schließkraft der Presse und eine aus der Simulation abgeleitete Rahmenstruktur (Flächenanteil OFC 30 %) eine Druckbelastung von 70 MPa für das OFC in der Anwendung bestimmt. Als Grenzwert für die mechanische Untersuchung wurde ein entsprechend erhöhter Wert von 100 MPa gewählt, mit dem die Probekörper zyklisch belastet wurden, um das Auf- und Zufahren der Presse nachzustellen.
Die mechanische Untersuchung zeigte, dass die Bauteile nach den hier getesteten 100 Belastungszyklen immer noch beschädigungsfrei und ohne Setzungsverhalten waren. Zwischen der „Erstbelastung“ und den folgenden Zyklen konnte ein stark veränderter Verlauf der Druckspannung über der Stauchung beobachtet werden (siehe Abbildung 3). Zurückgeführt werden kann dies darauf, dass die hergestellte Probe (Dicke 6,19 mm) nicht exakt planparallel war und somit in den erhabenen Bereichen eine Überbelastung auftrat, die zum Versagen einzelner Matrixbereiche und damit zur planparallelen Ausrichtung der Probe führte. Die hohe Reproduzierbarkeit der dargestellten Kurven (Zyklus 2-100) lässt jedoch erwarten, dass sich dies auf die Erstbelastung beschränkte. Für die 3-Punkt-Biegefestigkeit (nach ISO 17138) konnte ein Wert von 87 +– 4 MPa (Faservolumengehalt 35,5 %) bestimmt werden. Zwar stellt die mechanische Belastbarkeit des OFC den Hauptaspekt für den Einsatz des Bauteils dar, dennoch leistet die Rahmenstruktur auch einen wichtigen Beitrag zur thermischen Isolationsleistung. Da sich die zuvor genannte Wärmeleitfähigkeit von Mullit auf dichte Probekörper bezieht, die Mullit-Matrix des OFC hingegen hochporös ist (> 50 Vol.%) und durch die eingelagerten Fasern vielfache Phasenübergänge (Matrix-Faser, Faser-Matrix) aufweist, wurden die Werte des OFC für die Simulation über Laser-Flash-Messungen bestimmt (vgl. Abbildung 4).

Abbildung 4: Wärmeleitfähigkeit des OFC bei verschiedenen Temperaturen bestimmt mittels Laser-Flash-Methode
Die Messergebnisse sind in guter Übereinstimmung mit publizierten Werten für hochporöse Mullit-Proben (offene Porosität 47 Vol.%) [2] und vergleichbaren OFC (WHIPOX) [3] und liegen mit 1,52 bis
1,23 W/mK im Vergleich zu monolithischem Mullit ungefähr um den Faktor 2 – 3 niedriger. Wenngleich sich die Laser-Flash-Methode als transientes Messverfahren nur bedingt für inhomogene, anisotrope Materialien eignet, gibt es keine geeignetere Alternative, um die Wärmeleitfähigkeit über den hier gezeigten Temperaturbereich zu bestimmen. Daher sollen Temperaturmessungen im Rahmen geplanter Belastungstests genaueren Aufschluss über die thermische Isolationsleistung geben.
Für die Hybridisolation werden Platten aus papierabgeleiteter Keramik in den OFC-Rahmen eingelegt. Die Herstellung der dafür benötigten Grünpapiere konnte bereits erfolgreich auf die Versuchspapiermaschine der PTS in den Technikumsmaßstab überführt werden, wodurch ein möglicher Scale-Up auf industrielle Maschinen bereits vorbereitet wurde. Die Herstellung von hochgefüllten Grünpapieren bis ca. 87 Gew.% Füllstoffanteil konnte in den Versuchen gezeigt werden. Selbst bei diesen extrem hohen Füllstoffanteilen wiesen die Papiere neben einer hohen Gleichmäßigkeit (z.B. Materialdicke, Füllstoffverteilung) brauchbare mechanische Eigenschaften wie beispielsweise einen Tear-Index von rund 1,5 bis 2,0 mN m²/g auf, wodurch die technische Umsetzbarkeit möglich ist.
Abbildung 5 zeigt die Herstellung eines Inlays aus hochgefülltem Grünpapier unter Last im Sinterofen sowie die gesinterte Keramik. Diese wird dafür aus Einzellagen mit einer Höhe von rund 0,5 mm aufgebaut und passgenau zugeschnitten. Die entwickelten hochporösen Keramiken (über 60 % offene Porosität) auf Aluminiumoxid/Zirkoniumoxid-Basis weisen sehr geringe Wärmeleitfähigkeiten von unter 0,3 W/mK bei 800 °C bis 1000 °C auf, wodurch sie die Isolationswirkung des Hybridbauteils deutlich erhöhen. Die Inlays werden mittels eines keramischen Klebers fest mit der OFC-Rahmenstruktur zum angestrebten hybriden Aufbau verbunden.
![Abbildung 5: Grünkörper (hochgefülltes Spezialpapier) im Sinterofen vor der Temperaturbehandlung unter Beschwerung [links], gesintertes Inlay aus papierabgeleiteter Keramik nach dem Sintern [rechts]](https://werkstoffzeitschrift.de/wp-content/uploads/2021/06/abb5-1-300x126.jpg)
Abbildung 5: Grünkörper (hochgefülltes Spezialpapier) im Sinterofen vor der
Temperaturbehandlung unter Beschwerung [links], gesintertes Inlay aus papierabgeleiteter Keramik nach dem Sintern [rechts]
Potentielle weitere Anwendungsgebiete
Neben dem Einsatz als Isolationswerkstoff können weitere Anwendungsfelder für die entwickelten Hybridkeramiken erschlossen werden, wobei die Aufteilung in tragende Rahmenstruktur und funktionellen Füllstoff beibehalten werden soll. Für die Formgebung des Füllstoffs könnten dabei auch Wellen- oder Faltenstrukturen realisiert werden.
Aufgrund der chemischen und thermischen Stabilität der Keramik und der potentiell auch als Gradient realisierbaren Porosität des Füllstoffs, wäre z.B. ein Einsatz im Bereich der Stofftrennung in aggressiven Medien (z.B. Rauchgasfiltration) oder als Porenbrenner denkbar. Ferner kann die poröse Struktur der papierabgeleiteten Keramik in Katalyseprozessen Verwendung finden, beispielsweise als Membranreaktor. Durch Aufbringen eines Katalysators in die Porenstruktur stellt die Keramik den Träger dar, der für eine große Oberfläche und gleichzeitig die nötige Wärmeabfuhr sorgt.
Zusammenfassung
Der Einsatz eines Hybridbauteils aus OFC und papierabgeleiteter Keramik als formstabile Werkzeugisolation im Kraftfluss einer Warmpresse wird im Rahmen des „ForWerk“-Projekts untersucht. Die mechanischen Eigenschaften des als Rahmenstruktur zum Einsatz kommenden OFC weisen bereits die erforderlichen Festigkeiten sowie die zyklische Belastbarkeit auf. Als Inlay für die Isolation wird eine papierabgeleitete Keramik aus einer Aluminiumoxid-Zirkoniumoxid-Mischung verwendet, deren Funktion die Reduktion der Wärmeleitfähigkeit sowie der Gesamtbauteilkosten ist. Aufgrund der hohen Porosität (über 60 %) erreicht diese eine Wärmeleitfähigkeit von unter 0,3 W/mK bei 1000 °C. Die Optimierung des Bauteils hinsichtlich dessen Performance erfolgt über die Simulationssoftware LS-DYNA. Belastungstests unter Realbedingungen sollen die Gesamtperformance der Hybrid-Lösung bestätigen.
Einschub Papierabgeleitete Keramik
Die papierabgeleitete Keramik wurde an der Papiertechnischen Stiftung im Rahmen von Forschungsprojekten seit 2003 entwickelt und optimiert. Durch den Einsatz etablierter Verfahren aus dem Bereich der Papierherstellung ist es möglich flächiges, präkeramisches Material kostengünstig und in großer Menge auf der Papiermaschine zu erzeugen. Die variable Einstellung der Mischungsverhältnisse von Zellulose und keramischem Füllstoff in den Grünkörpern ermöglicht eine variable Einstellung von Porosität und Festigkeit der Keramiken in einem weiten Bereich. Ein weiterer großer Vorteil ist die gute Formbarkeit der Grünkörperschichten. Durch Prozesse wie Rollen, Falten und Wellen sind die unterschiedlichsten Geometrien zugänglich, wodurch der Einsatz in einer Vielzahl technischer Anwendungen ermöglicht wird.
Literatur
[1] Alabort, E.; Putman, D.; Reed, R. C.: Superplasticity in Ti-6Al-4V: Characterisation, modelling and applications. In: Acta Materialia 95 (2015), S. 428 – 442.
[2] Barea, R.; Osendi, M. I.; Ferreira, J. M.F.; Miranzo, P.: Thermal conductivity of highly porous mullite material. In: Acta Materialia 53 (2005), S. 3313 – 3318.
[3] Schneider, H.; Komarneni, S.: Mullite. Weinheim, Chichester 2005, S. 435.
IGF Vorhaben Nr. 20646 BG
Formstabile Werkzeugisolation
im Kraftfluss mit verbesserten
thermischen Kennwerten aufgrund eines hybriden Aufbaus
(kurz: ForWerk)
Laufzeit:
01.04.2019 – 30.11.2021
Forschungsstellen:
Papiertechnische Stiftung (PTS), Heidenau
Universität Bayreuth, Lehrstuhl
Keramische Werkstoffe (CME)
Fraunhofer-Institut für Werkzeugmaschinen und Umformtechnik (IWU),
Chemnitz
PTS: Dr. Stefan Knohl, Dr. Cornell Wüstner
CME: Georg Puchas, Felix Lindner
IWU: Ricardo Trân, Elmar Galiev
Ansprechpartner für nähere Informationen:
Dr. Cornell Wüstner (PTS)
cornell.wuestner@ptspaper.de
Georg Puchas (CME)
georg.puchas@uni-bayreuth.de