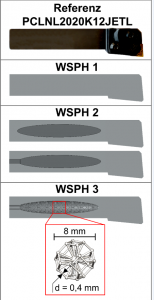
Abbildung 1: Übersicht der generierten Wende-schneidplattenhalter (WSPH
Dipl.-Ing. Florian Vogel, Sebastian Berger M.Sc., Dr.-Ing. Ekrem Özkaya, Prof. Dr.-Ing. Dirk Biermann
Einleitung
Resultierend aus der sich bei der Zerspanung von Titanwerkstoffen einstellenden, werkstoffspezifischen Segmentspanbildung können eingesetzte Werkzeuge je nach gegebenen Prozessbedingungen erheblich in Schwingung versetzt werden, sodass neben einem gesteigerten Werkzeugverschleiß die geforderten Bauteilqualitäten oftmals nicht erzielbar sind. Durch den Einsatz additiv gefertigter Wendeschneidplattenhalter (WSPH) für die Drehbearbeitung von TiAl6V4 erfolgt eine passive Dämpfung derartiger, spanbildungsinduzierter Werkzeugschwingungen. Ausschlaggebend hierfür ist die durch den additiven Herstellungsprozess ermöglichte Erzeugung speziell gestalteter Hohlelemente in den Schäften der WSPH. Einerseits bedingt durch eine daraus resultierende, schwingungsoptimierte Werkzeuggestaltung, andererseits aufgrund der inneren Reibung von zusätzlich in die Schäfte eingebrachten Füllwerkstoffen werden die Schwingungsamplituden des Werkzeugs signifikant reduziert.
Problemstellung
Primär aufgrund der geringen Dichte von ρ = 4,51 g/cm³ bei gleichzeitig hoher spezifischer Festigkeit und Zähigkeit wird Titan zunehmend insbesondere in den Bereichen Luft- und Raumfahrt, Medizintechnik, Motorenbau sowie Offshore-Industrie als Konstruktionswerkstoff eingesetzt. Von hoher Bedeutung für Anwendungen unter kritischen Umgebungsbedingungen sind zudem die äußerst gute Korrosionsbeständigkeit und geringe Wärmeleitfähigkeit des Leichtmetalls [1]. Jedoch ist letztere in Kombination mit der hohen Reaktionsaffinität des Werkstoffs für die bei der Titanzerspanung gesteigerten Anforderungen an Werkzeug und Maschine verantwortlich [1; 2; 3]. Des Weiteren ist die sich bei der spanenden Titanbearbeitung einstellende, werkstoffspezifische Segmentspanbildung mit
einer gravierenden Beeinträchtigung der Prozessstabilität verbunden [2; 3]. Untersuchungen haben gezeigt, dass bei Schnittgeschwindigkeiten von vc≥ 100 m/min, aber auch bei ungünstig gewählten Schnittparametern im Bereich kleiner Schnittgeschwindigkeiten, ausgeprägte Werkzeugschwingungen zu verzeichnen sind. Bedingt durch das sich periodisch wiederholende Aufstauchen und Abgleiten einzelner Spansegmente in dem Bereich der Wirkzone erfolgt eine dynamische Werkzeuganregung, die je nach Intensität einen von Oberflächenzerrüttung geprägten Werkzeugverschleiß zur Folge hat [4; 5]. Werkstückseitig resultieren entsprechend makroskopische und mikroskopische Inhomogenitäten der Oberfläche aus den teilweise hochfrequenten Schwingungen des Werkzeugs [5].
Während angepasste Schneidwerkstoffe bzw. Beschichtungen und Kühlschmierstoffkonzepte eine thermische sowie diffusionsbedinge Werkzeugbeeinträchtigung minimieren, ist eine Reduktion spanbildungsinduzierter Werkzeugschwingungen oftmals nur mit konstruktiven oder steuerungstechnischen Anstrengungen möglich [5; 6]. Dabei wird zwischen aktiven und passiven Methoden der Schwingungsdämpfung unterschieden. Namensgebend für die aktive Dämpfung ist der Einsatz von Peripheriesystemen, wie Aktoren und Sensoren, die eine aktive Einflussnahme auf den Prozess ermöglichen. Hierfür bedarf es jedoch i. d. R. komplexer Aufbauten und Steuerungen. Dahingegen sind für eine passive Dämpfung der Werkzeugschwingungen oftmals einfache, konstruktive Maßnahmen ausreichend. Beispielsweise können am Werkzeug applizierte Massen die Werkzeugeigenfrequenz verschieben, oder Zusatzelemente können die Schwingungsenergie dissipativ senken [4; 5; 7; 8].
Eine weitere Möglichkeit der passiven Schwingungsdämpfung besteht in der Integration sogenannter Partikeldämpfer in das Werkzeugsystem, durch die eine direkte Dissipation der Schwingungsenergie möglich ist [9; 10]. Hierbei handelt es sich um ein festes, hohlförmiges Element (Primärsystem), welches mit einer beweglichen Pulvermasse (Sekundärsystem) gefüllt ist [9; 11; 12]. Einerseits reibungsbedingt, andererseits durch elastische Stöße lassen sich über einen großen Frequenzbereich hohe Dämpfungsraten erzielen. Unterschieden wird dabei zwischen einer Dissipation durch Kontakt der Füllpartikel mit dem Primärsystem und einer Dämpfung durch gegenseitigen Partikelkontakt [9; 10; 11; 12]. Dementsprechend hoch ist die Anzahl an Faktoren, die die Dämpfungseigenschaften partikelgefüllter Elemente beeinträchtigen. Neben des Einflusses der geometrischen Gestaltung der Hohlstruktur lassen sich u. a. die Partikelgröße und -dichte sowie die Schüttdichte der Partikelfüllung als Dissipationsfaktoren bestimmen [8; 9; 11; 13].
Während die Integration von Partikeldämpfern in Werkzeugsysteme bisher nur mit gesteigertem, konstruktions- und fertigungstechnischem Aufwand möglich war und sich darüber hinaus auf vergleichsweise simple Hohlelementgeometrien beschränkte, ermöglichen Verfahren der additiven Fertigung die einfache Generierung komplex strukturierter Dämpfungssysteme [4; 8; 9]. Dabei können zum einen geschlossene Geometrien erzeugt werden, sodass der beim Herstellungsprozess nicht aufgeschmolzene Pulverwerkstoff in der Hohlstruktur verbleibt und somit als Partikeldämpfer fungiert [4; 9]. Zum anderen ermöglicht eine Bauteilöffnung die flexible Befüllung des Hohlelements mit verschiedenen Füllwerkstoffen, wodurch die Dämpfungseigenschaften des Systems zusätzlich angepasst werden können [8; 14]. Durchgeführte Untersuchungen mit additiv hergestellten Wendeschneidplattenhaltern (WSPH), die zwei geschlossene, pulvergefüllte Hohlelemente aufwiesen, haben gezeigt, dass derartig konstruierte Werkzeuge ein großes Potential aufweisen, spanbildungsinduzierte Werkzeugschwingungen bei der Drehbearbeitung von Titan (Ti6Al2Sn4Zr6Mo) zu dämpfen. Allerdings wurde gleichermaßen festgestellt, dass weiterhin ein erheblicher Forschungsbedarf sowohl hinsichtlich der geometrischen Hohlelementgestaltung als auch bei der Auswahl eines geeigneten Füllwerkstoffs besteht [4].
In diesem Kontext werden im Rahmen eines aktuellen Forschungsprojekts am Institut für Spanende Fertigung (ISF) der TU Dortmund die Dämpfungseigenschaften verschieden innenstrukturierter WSPH untersucht. Fokussiert wird dabei zudem der Einfluss diverser Füllwerkstoffe auf das Schwingungsverhalten der mithilfe des Selective-Laser-Melting(SLM)-Verfahrens hergestellten Werkzeughalter. Die im Folgenden vorgestellten Ergebnisse ausgewählter Versuche ermöglichen einerseits einen Überblick über die Einflussfaktoren bei der Auslegung schwingungsgedämpfter WSPH. Andererseits wird das hohe Potential der passiven Dämpfung durch additiv strukturierte Hohlelemente auch über den betrachteten Anwendungsfall hinaus aufgezeigt.
Experimentelle Randbedingungen und Versuchsplanung
Der mithilfe des SLM-Verfahrens realisierte, additive Aufbau der WSPH erfolgte mit einem 1.2709-Pulverwerkstoff der Korngröße dK = 20 – 63 µm unter Verwendung einer Layerdicke von sL = 40 µm. In der Abbildung 1 ist eine Übersicht der generierten Halter dargestellt. Die Plattensitz- und Schaftgeometrien entsprechen dabei diesen des als Referenz eingesetzten konventionellen Hochdruckhalters (PCLNL2020K12JETL). Neben einem zusätzlichen, generativ hergestellten Referenzhalter ohne Hohlelement (WSPH 1) wurden zwei weitere Haltertypen mit ellipsoidem Hohlelement eingesetzt (WSPH 2 und WSPH 3). Während eine Variante des WSPH 2 über keine Bauteilöffnung verfügte, sodass der beim Herstellungsprozess nicht aufgeschmolzene SLM-Pulverwerkstoff im Werkzeugschaft verblieb, konnte dieser durch Öffnungen in den Schäften einer weiteren Version des WSPH 2 sowie des WSPH 3 ausgebracht und eine reversible Befüllung der Kavitäten mit verschiedenen Füllwerkstoffen ermöglicht werden. Zur Stabilitätssteigerung und Erhöhung der Kontakt- und somit Reibungsflächen zwischen den Füllpartikeln und dem Werkzeughalter wurde in dem Ellipsoiden des WSPH 3 eine Stützstruktur aus einer Vielzahl aneinandergereihter Elemente basierend auf einem sogenannten „Oktaederstumpf“ während des SLM-Prozesses generiert.

Tabelle 1: Übersicht der eingesetzten Füllwerkstoffe [15; 16; 17]
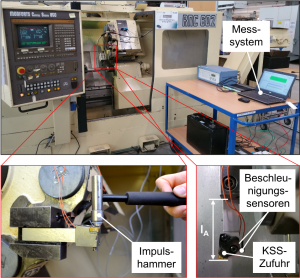
Abbildung 2: Versuchsaufbauten zur Bestim-mung der Nachgiebigkeitsfrequenzgänge und des Einsatzverhaltens der WSPH
Die Versuchsdurchführung erfolgte auf einer CNC-Drehmaschine der Firma Monforts (Typ „RNC 602“). Sowohl für die Versuche zur Bestimmung der Nachgiebigkeitsfrequenzgänge der WSPH, dargestellt in Abbildung 2 (unten links), als auch für die Drehversuche (Abbildung 2, unten rechts) wurden die Halter mit einer Ausspannlänge von lA = 75 mm in die sich im Maschinenrevolver befindliche VDI-40-Werkzeugaufnahme eingespannt. Die Drehbearbeitung des TiAl6V4-Werkstoffs erfolgte mit Wendeschneidplatten des Typs „CNNG120408-MF1“ der Seco Tools GmbH und einer direkten, wirkzonennahen Kühlschmierstoff-Zufuhr (p = 6 bar). Für die Aufnahme der Werkzeugschwingungen wurden auf den Plattensitzen der WSPH in Schnitt- und in Vorschubrichtung jeweils ein Beschleunigungssensor der Firma Brüel und Kjær geklebt und mit einem speziellen Mess- und Analysesystem verbunden.
Ergebnisse und Diskussion
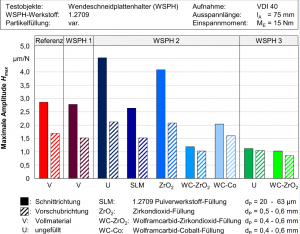
Abbildung 3: Maximale Amplituden der getesteten WSPH
Um vor der Drehbearbeitung des TiAl6V4-Werkstoffs die Partikelfüllung mit der höchsten dämpfungssteigernden Wirkung und somit eine Vorauswahl der in den Drehversuchen einzusetzenden WSPH-Füllvariante bestimmen zu können, erfolgte zunächst mithilfe der Impulshammermethode die Ermittlung der werkzeug- bzw. füllungsspezifischen Nachgiebigkeitsfrequenzgänge. Dazu wurden die WSPH am Plattensitz werkzeugnah in Schnitt- und Vorschubrichtung jeweils zehnmal unabhängig voneinander angeregt. Die Ergebnisse der Einzelmessungen je Anregungsrichtung konnten in einem speziellen Mess- und Analyseprogramm gemittelt und für die nachfolgende Auswertung herangezogen werden. Neben der Referenz und dem WSPH 1 wurden die WSPH 2 und 3 sowohl ungefüllt als auch partikelgefüllt getestet. Basierend auf den Resultaten der zunächst getesteten Füllvarianten des WSPH 2 erfolgte die Befüllung des WSPH 3 nachfolgend lediglich mit dem Partikelwerkstoff, der das größte Dämpfungssteigerungspotential aufgewiesen hat. In der Abbildung 3 sind die ermittelten Maximalwerte der Amplituden (Hmax) zusammengefasst. Bedingt durch die von Schnitt- zur Vorschubrichtung abweichende Abstützung der WSPH in der Werkzeugaufnahme resultieren generelle Unterschiede in den Amplitudenhöhen bei den jeweiligen Anregungsrichtungen.
Bei Vergleich der Referenz mit dem WSPH 1 zeigt sich, dass hinsichtlich der Nachgiebigkeit im Schwingungsfall keine grundlegenden Unterschiede zwischen dem konventionell und dem additiv hergestellten Halter bestehen. Sowohl in Schnitt- als auch in Vorschubrichtung sind annähernd gleich ausgeprägte Amplitudenmaxima und somit keine Beeinflussung des Dämpfungsvermögens der WSPH durch die verschiedenen Herstellungsmethoden erkennbar. Beobachtet werden kann dahingegen, dass im Werkzeugschaft befindliche Hohlstrukturen das Schwingungsverhalten der Halter erheblich beeinträchtigen. Während die Generierung eines einfachen, ungefüllten ellipsoiden Hohlelements zunächst mit verschlechterten Dämpfungseigenschaften einhergeht (WSPH 2), hat die in die Kavität zusätzlich eingebrachte Oktaederstumpfstruktur einen derart positiven Einfluss, dass die maximalen Amplituden des ungefüllten WSPH 3 diese der Referenz wesentlich unterschreiten. Zusätzlich dämpfungssteigernd wirkt sich eine Befüllung des Ellipsoiden (WSPH 2) mit geeigneten Partikelwerkstoffen aus. Der Verbleib des während des Herstellungsprozesses nicht aufgeschmolzenen Pulverwerkstoffs in der Kavität hat bereits eine deutliche Reduktion der Maxima zur Folge. Nochmals höher fällt die Schwingungsdämpfung durch die reversible WC-ZrO2-Befüllung des Hohlelements aus, mit der die geringsten Amplituden des WSPH 2 zwar erzielbar sind, diese des ungefüllten WSPH 3 jedoch nicht unterschritten werden. Losgelöst vom Vergleich der Halter untereinander zeigt sich bei den betrachteten Füllwerkstoffen die Tendenz, dass sich mit zunehmender Schüttdichte gleichermaßen das Dämpfungsvermögen erhöht und mit ρ = 5,90 g/cm3 (WC-ZrO2) einen Höchstwert erreicht. Da aus einer weiteren Steigerung der Schüttdichte durch die Befüllung des WSPH 2 mit WC-Co keine weitere Reduktion, sondern vielmehr eine Erhöhung der Nachgiebigkeit verglichen mit der WC-ZrO2-Füllung resultierte, fand beim WSPH 3 lediglich letztgenannte Anwendung. In Kombination mit der oktaederstumpfstrukturierten Kavität ist somit die höchste Schwingungsdämpfung feststellbar. Zur weiteren Analyse sind die Nachgiebigkeitsfrequenzgänge der Referenz und des WC-ZrO2-gefüllten WSPH 3 in Abbildung 4 gegenübergestellt.
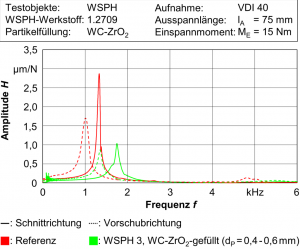
Abbildung 4: Nachgiebigkeitsfrequenzgänge der Referenz und des WC-ZrO2-gefüllten WSPH 3
Bei Betrachtung der Frequenzgänge (Abb. 4) ist zu erkennen, dass durch den additiven, WC-ZrO2-gefüllten Werkzeugaufbau nicht nur die Amplitudenmaxima der Referenz signifikant um ca. 64 % in Schnitt- und ca. 50 % in Vorschubrichtung reduziert wurden, sondern ebenfalls die Eigenfrequenzen deutlich verschoben sind. Insbesondere bei Drehprozessen, bei denen Werkzeuganregungen in den Eigenfrequenzbereichen der Referenz erfolgen, können ausgeprägte Werkzeugschwingungen bereits durch die verschobenen Stabilitätsgrenzen verhindert werden. Des Weiteren ist feststellbar, dass im Gegensatz zur Referenz die maximalen Auslenkungen des gefüllten WSPH 3 in beiden Anregungsrichtungen von fast gleicher Höhe sind. Einerseits lässt dies auf ein annähernd isotropes Dämpfungsvermögen schließen, andererseits wird der eingangs beschriebene Einfluss der von der Schnitt- zur Vorschubrichtung abweichenden Einspannsituation der Halter in der Werkzeugaufnahme weitestgehend kompensiert.
Bei der Überprüfung des Einsatzverhaltens der additiv gefertigten Halter bei der Drehbearbeitung des TiAl6V4-Werkstoffs wurde sich auf die Verwendung der WC-ZrO2 gefüllten WSPH 2 und 3, die bei den vorangegangenen Untersuchungen zur Bestimmung der Nachgiebigkeit die geringsten Auslenkungen aufgewiesen haben, beschränkt. Dabei erfolgte mit der Schnittgeschwindigkeit vc = 40 m/min, dem Vorschub f = 0,2 mm/U und der Schnitttiefe von aP = 1,5 mm die Betrachtung einer kritischen Parameterkombination. Während der Versuchsdurchführung wurden die Beschleunigungssignale stetig detektiert und für die nachfolgende Auswertung durch Anwendung einer analyseprogrammgestützten, einfachen Fourier-Transformation als Beschleunigungsamplituden ausgegeben. In der Abbildung 5 sind die Maximalwerte der Beschleunigungsamplituden der partikelgefüllten WSPH diesen der Referenz gegenübergestellt.
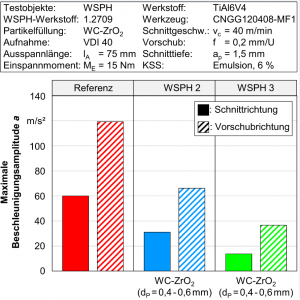
Abbildung 5: Maximale Beschleunigungsamplituden der in den Drehversuchen eingesetzten WSPH
Bei Vergleich der maximalen Beschleunigungsamplituden der Schnitt- mit diesen der Vorschubrichtung (Abb. 5) zeigt sich bei allen drei eingesetzten WSPH tendenziell ein ähnliches Schwingungsverhalten. Die Maxima in Vorschub- sind etwa doppelt so hoch wie diese in Schnittrichtung, was auf eine prozessbedingt, richtungsabhängig starke Werkzeuganregung in der Wirkzone schließen lässt. Wiedererkennbar sind weiterhin die in den Voruntersuchungen ermittelten, unterschiedlichen Nachgiebigkeiten der Halter. Auch hier ist festzustellen, dass der WC-ZrO2-gefüllte WSPH 2 die Werkzeugschwingungen verglichen mit der Referenz bereits deutlich reduziert, die Schwingungsdämpfung bedingt durch die sich zusätzlich im Ellipsoiden des partikelgefüllten WSPH 3 befindliche Oktaederstumpfstruktur jedoch signifikanter ausfällt. Dies resultiert offenbar einerseits aus dem schwingungsoptimierten Schaftaufbau, andererseits aus den strukturbedingt gesteigerten Kontaktflächen zwischen Füllpartikeln und Halter, womit im Schwingungsfall gleichermaßen eine gesteigerte, reibungsbedingte Dissipation einhergeht. Nachfolgend wird das Einsatzverhalten der Referenz und des WC-ZrO2-gefüllten WSPH 3 mithilfe der Abbildung 6 detaillierter analysiert.
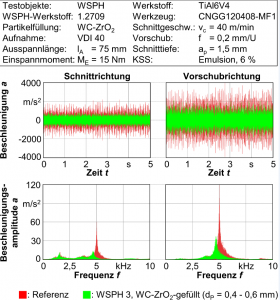
Abbildung 6: Einsatzverhalten der Referenz und des WC-ZrO2-gefüllten WSPH 3
Anhand der oben in Abbildung 6 dargestellten Beschleunigungssignale für ein repräsentatives Zeitintervall von t = 5 s ist bereits deutlich das schwingungsdämpfende Verhalten des gefüllten WSPH 3 erkennbar. Während die Referenz in Schnitt-, aber insbesondere auch in Vorschubrichtung ausgeprägte Beschleunigungsspitzen aufweist, zeigen sich bei dem innenstrukturierten Halter wesentlich verringerte Beschleunigungswerte und lediglich in Vorschubrichtung stellenweise leicht erhöhte Peaks, was sich in den, verglichen mit der Referenz, signifikant reduzierten Beschleunigungsamplituden widerspiegelt (Abbildung 6, unten). Diese entsprechen lediglich im Eigenfrequenzbereich bei etwa f = 5 kHz in Schnittrichtung ca. 23 % und in Vorschubrichtung ca. 31 % der Amplitudenhöhen des konventionellen WSPH. Darüber hinaus ist festzustellen, dass sich die Eigenfrequenzen durch den additiven, partikelgefüllten Werkzeugaufbau sichtlich verschoben haben. Auffällig sind zudem die nahezu deckungsgleichen Peaks der Referenz und des WSPH 3 in Schnittrichtung im Frequenzbereich um ca. 1,5 kHz. Es lässt sich vermuten, dass es sich hierbei um einen vernachlässigbaren, maschinen- bzw. werkzeugaufnahmeseitigen Einfluss handelt.
Resümee und Ausblick
Anhand der durchgeführten Untersuchungen konnte gezeigt werden, dass durch einen angepassten, additiv innenstrukturierten Werkzeugaufbau in Verbindung mit einer geeigneten Partikelfüllung des Hohlelements eine signifikante Dämpfung spanbildungsinduzierter Werkzeugschwingungen erzielbar ist. Im Speziellen hat sich sowohl bei den Versuchen zur Bestimmung der Nachgiebigkeitsfrequenzgänge als auch bei der Drehbearbeitung des TiAl6V4-Werkstoffs herausgestellt, dass die Generierung einer zusätzlichen Stützstruktur aus einer Vielzahl von Oktaederstumpfelementen innerhalb der ellipsoiden Kavität mit einer erheblichen Steigerung der Dämpfungseigenschaften des additiv hergestellten WSPH einhergeht. Als wesentlich dämpfungssteigernd hat sich mit WC-ZrO2 die zusätzliche Verwendung eines Füllwerkstoffs mit einer Schüttdichte von ρ = 5,90 g/cm3 erwiesen.
In nachfolgenden Untersuchungen wird nun der Einfluss der Partikelgröße der Füllwerkstoffe sowie des Füllvolumens auf das Schwingungsverhalten der WSPH detailliert betrachtet. Fokussiert wird dabei zudem die Verwendung ausgewählter Mischfüllungen. Einerseits mit variierender Partikelgröße gleichen Werkstoffs, andererseits finden Partikelmischungen verschiedenen Materials Einsatz. Weitere Untersuchungen zielen darauf ab, die erlangten Erkenntnisse auf die hybrid additive Fertigung von HSK63-Werkzeugaufnahmen für die Fräsbearbeitung zu übertragen. Denkbar wäre des Weiteren der Einsatz generativ innenstrukturierter, partikelgefüllter Elemente im Bereich von Spannelementen, um prozessbedingte Bauteilschwingungen zu reduzieren.
Danksagung
Das Projekt „Schwingungsreduzierung bei der Dreh- und Fräsbearbeitung von Leichtbaumaterialien durch den Einsatz strahlgeschmolzener Werkzeugaufnahmen“ wurde gefördert durch die Deutsche Forschungsgemeinschaft (DFG) – Projektnummer 315697914. Hierfür gilt ein besonderer Dank.
Literatur
[1] Peters, M.; Leyens, C.: Titan und Titanlegierungen. WILEY-VCH Verlag GmbH & Co. KGaA; Weinheim (2002).
[2] Arrazola, P.-J.; Garay, A.; Iriarte, L.-M.; Armendia, M.; Marya, S.; Le Maître, F.: Machinability of titanium alloys (Ti6Al4V and Ti555.3). Journal of Materials Processing Technology; Volume 209 (2009); S. 2223 – 2230.
[3] Cotterell, M.; Byrne, G.: Dynamics of chip formation during orthogonal cutting of titanium alloy Ti-6Al-4V. CIRP Annals – Manufacturing Technology; Volume 57 (2008); S. 93 – 96.
[4] Biermann, D.; Meier, H.; Haberland, C.; Abrahams, H.; Metzger, M.; Steiner, M.: Einsatz additiv gefertigter Werkzeughalter. wt Werkstattstechnik online; Jahrgang 103 (2013); S. 481 – 484.
[5] Machai, C.: Grundlagenuntersuchung zur Zerspanung von β-Titanlegierungen unterschiedlicher Mikrostruktur. Dissertation; Institut für Spanende Fertigung; Technische Universität Dortmund (2012).
[6] Dearnley, P. A.; Grearson, A. N.: Evaluation of principal wear mechanism of cemented carbides and ceramics used for machining titanium alloy IMI 318. Materials Science and Technology 2 (1986); Nr. 1; S. 47 – 58.
[7] Siddhpura, M.; Paurobally, R.: A review of chatter vibration research in turning. International Journal of Machine Tools & Manufacture 61 (2012); S. 27 – 47.
[8] Vogel, F.; Özkaya, E.; Biermann, D.: Additiver Werkzeugaufbau zur Dämpfung von Prozessschwingungen. VDI-Z Integrierte Produktion 160 (2018); Nr. 1/2; S. 42 – 45.
[9] Künneke, T.; Zimmer, D.: Funktionsintegration additiv gefertigter Dämpfungsstrukturen bei Biegeschwingungen. Erschienen in: Additive Fertigung von Bauteilen und Strukturen; Richard, H. A.; Schramm, B.; Zipsner, T. (Hrsg.); Springer Vieweg; Wiesbaden (2017); S. 61 – 74.
[10] Friend, R. D.; Kinra, V. K.: Particle Impact Damping. Journal of Sound and Vibration 233 (1) (2000); S. 93 – 118.
[11] Marhadi, K. S.; Kinra, V. K.: Particle impact damping: Effect of mass ratio, material, and shape. Journal of Sound and Vibration 283 (1-2) (2005); S. 433 – 448.
[12] Sánchez, M.; Pugnaloni, L. A.: Effective mass overshoot in single degree of freedom mechanical systems with a particle damper. Journal of Sound and Vibration 330 (24) (2011); S. 5812 – 5819.
[13] Chockalingam, S; Natarajan, U.; George Cyril, A.: Damping investigation in boring bar using hybrid copper-zinc particles. Journal of Vibration and Control; Volume 23; Issue 13 (2015); S. 2128 – 2134.
[14] Yanagida, T.; Matchett, A. J.; Coulthard, J. M.: Damping and elastic properties of binary powder mixtures. Powder Technology 127 (2002); S. 107 – 115.
[15] Oerlikon AM Europe GmbH: Produktinformationen Pulverwerkstoff 1.2709. Barleben (2017)
[16] Sigmund Lindner GmbH: Produktdatenblatt SiLibeads Keramikkugeln Typ ZY-E. Warmensteinach (2019)
[17] Sigmund Lindner GmbH: Produktinformationen SiLibeads Kugelwerkstoffe Typ WC-ZY und Typ WC-Co. Warmensteinach (2019)