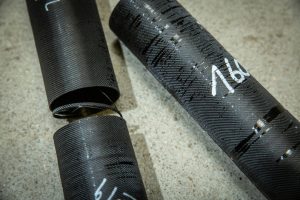
Zerstörte Probekörper nach einem Belastungstest im Hydropulser. (Bild: Heike Fischer / TH Köln)
Faserverbundmaterialien werden aufgrund ihres Gewichtsvorteils in immer mehr Branchen eingesetzt, etwa in der Automobilfertigung. Bislang gibt es aber noch keine zuverlässigen Prognoseverfahren für die Lebensdauer solcher Bauteile, so dass diese aus Sicherheitsgründen oftmals überdimensioniert werden.
In einem Forschungsprojekt haben die TH Köln und die Structural Engineering GmbH & Co. KG jetzt ein allgemeingültiges Berechnungsmodell entwickelt. Weiterlesen