Stahl bietet erhebliche, bislang nicht ausgeschöpfte Möglichkeiten, den Einsatz von Rohstoff und Energie zu verringern. Dabei kann die Qualität der Halb- und Endprodukte gesteigert werden, wie die Zuliefermesse Industrial Supply der Hannover Messe 2016 zeigt.
Faserverstärkte und Kombinationswerkstoffe sind in den Publikums- und Fachmedien präsent. Die Potenziale des klassischen Werkstoffs Stahl sind darüber etwas in den Hintergrund getreten. Dabei ist der Werkstoff Stahl aufgrund seines Herstellprozesses anderen Werkstoffen wie Aluminium oder Carbon überlegen.
„Betrachtet man den gesamten Produktlebenszyklus von Herstellung über die Nutzungsphase bis zum Recycling, so führt hochfester Stahl im Vergleich zu einem geringeren CO2-Ausstoß“, sagt Frank Heidelberger vom Stahlhersteller Salzgitter Flachstahl. Der Marketingleiter weiß das Stahlinstitut VDEh hinter sich. „Bei der Primärerzeugung von 1 t Stahl fallen rund 2 t CO2 an, bei Aluminium sind es rund 10 t und bei CFK sogar mehr als 20 t“, führt Institutsreferent Christoph Keul aus. „Bezieht man die Wiederverwertbarkeit in die Ökobilanz ein, wird bei der Erzeugung von 1 t Stahl, bezogen auf mehrere Recycling-Zyklen, sogar weniger als 1 t Kohlendioxid freigesetzt.“ Allerdings ruht auch die CFK-Branche nicht: Firmen wie CFK Valley Stade Recycling entwickeln mit Erfolg Verfahren zur Wiederverwertung. So könnten aus Alt-CFK hergestellte Fasermatten bald die Fenster des Airbus verkleiden.
1. Stahlveredelung:
Verzinkte Stähle werden leichter und haltbarer
Der vergleichsweise ressourcenschonende Herstellungsprozess von Stahl lässt sich gleichwohl weiter verbessern. Das betrifft natürlich auch die vor- und nachgelagerten Prozesse. Ein Beispiel sind verzinkte Stähle, wie sie im Automobil- und Bausektor zum Einsatz kommen.
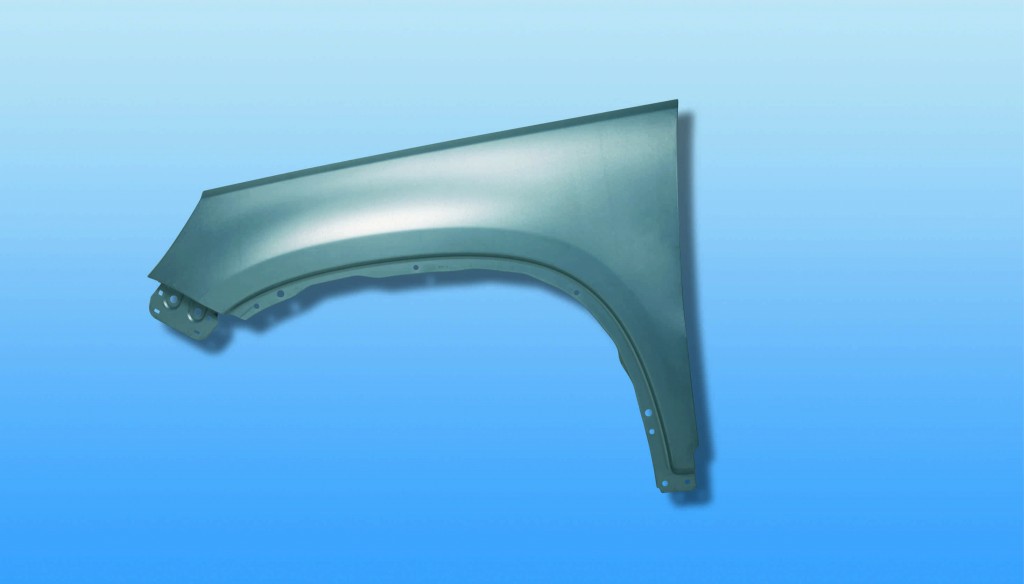
Kotflügel aus Stahl mit Zink-Magnesium-Schicht (StronSal). (Quelle: Salzgitter AG)
Um bei gleichbleibenden Korrosionsschutz-Eigenschaften die Dicke der Zinkschicht und damit den Zinkverbrauch pro Bauteil zu verringern, entwickelte der Stahlhersteller Salzgitter (Halle 6, Stand F02) eine Zink-Magnesium-Beschichtung. Sie verbessert bereits bei der Herstellung die CO2-Bilanz, da der Zinkbedarf um bis zu 50 Prozent reduziert werden kann.
Darüber hinaus erleichtert die Beschichtung die Weiterverarbeitung: Da im Umformprozess 70 Prozent weniger Zinkabrieb im Vergleich zur herkömmlichen feuerverzinkten Beschichtung anfällt, müssen die Werkzeuge seltener gereinigt werden.
2. Stahlerzeugung:
Konverterprozesse verbessern
Effizienzpotenziale bietet aber nicht allein die Legierung bzw. Veredelung von Stahl. Auch die eigentliche Stahlerzeugung aus Roheisen kann im Hinblick auf Ressourcennutzung und Kosten optimiert werden. Dafür entwickelte der Anlagenhersteller SMS group zusammen mit der TU Dortmund und einem europäischen Grobblech-Hersteller ein datengetriebenes Vorhersage- und Steuerungssystem für den Basic-Oxygen-Furnace-, den sogenannten BOF-Konverter, der 2015 etwa 60 Prozent zur Weltstahlproduktion von 1,6 Mrd. t beitrug.
Im Konverterprozess werden durch Aufblasen mit Sauerstoff störende Substanzen –je nach gewünschtem Endprodukt etwa Kohlenstoff oder Silizium – verbrannt. So wird innerhalb von knapp 15 Minuten aus einer Charge Roheisen hochwertiger Stahl.
Da im Prozess große Energiemengen freigesetzt werden, sind große Mengen Schrott zur Kühlung erforderlich. Darüber hinaus werden zusätzliche Heiz- und Kühlmittel eingesetzt oder es wird Sauerstoff nachgeblasen, um die Endtemperatur des Stahls möglichst genau einzustellen. Muss bei einem großen Konverter etwa die Stahltemperatur durch O2-Einsatz um 40 °C angehoben werden, geht knapp 1 t Roheisen verloren: Das Oxidationsprodukt wird zu Schlacke.
Das neue, datengetriebene System speist nun die zahlreich erhobenen Prozessdaten in Softwarealgorithmen ein. Sie ermöglichen, die Stahltemperatur genauer als bisher und in Echtzeit vorauszuberechnen und dadurch die Abläufe der Konverterkampagne besser zu steuern. „Dabei werden selbstständig auch Informationen aus unmittelbar vorangegangenen Chargen berücksichtigt: der Verschleiß der Ausmauerung, Prozessverluste und Schrottzusammenstellungen“, erklärt Norbert Uebber von der SMS-Forschungsabteilung. „So erhalten wir sehr genaue, sich selbst nachjustierende Vorhersagealgorithmen, die Rohstoffverluste verringern und die Energieeffizienz erhöhen.“
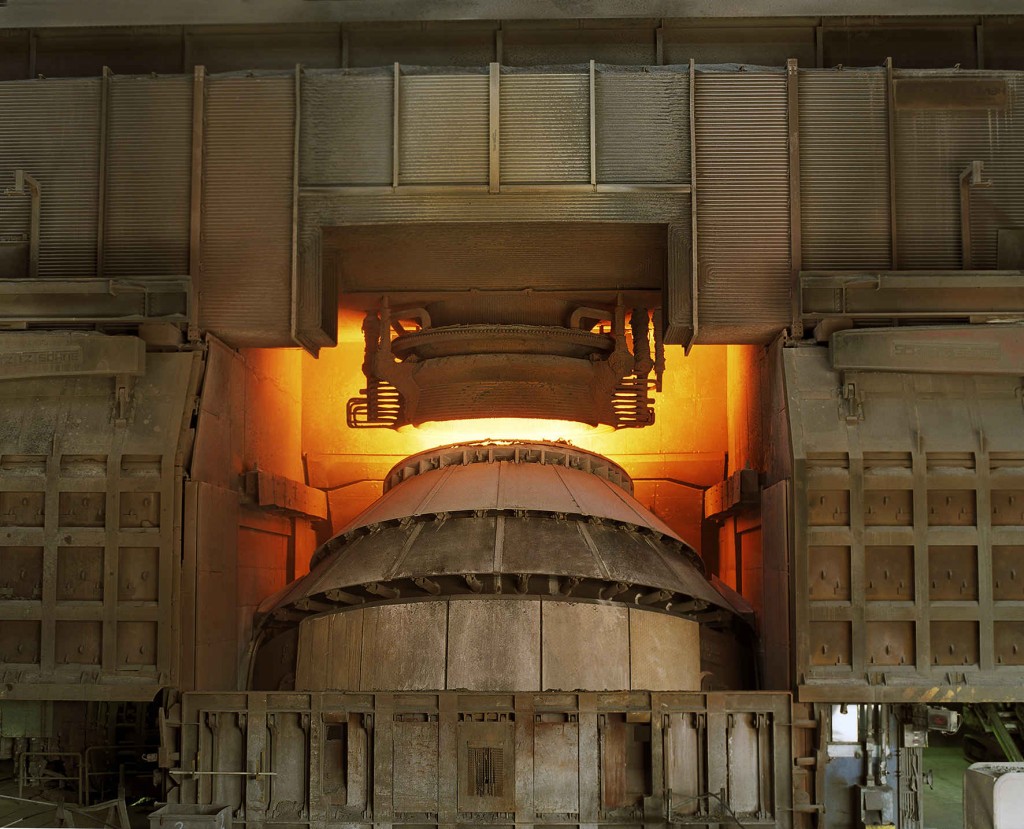
BOF-Stahlkonverter (Quelle: SMS group).
Das datengetriebene, sich selbst nachjustierende Steuerungssystem des BOF-Konverters ist ein Musterbeispiel für Industrie 4.0.
3. Stahlumformung:
Möglichkeiten massiven Leichtbaus
Welche Möglichkeiten bestehen, durch Optimierung geschmiedeter Bauteile Gewicht und Rohstoffeinsatz zu reduzieren, hat die „Initiative Massiver Leichtbau“ untersucht.
Der Zusammenschluss von Massivumformern und Stahlerzeugern erstellte dazu 2013–14 eine Pkw-Potenzialstudie, der eine Nfz-Studie folgte. Deren Ergebnisse und ihre aktuelle Umsetzung werden auf der Hannover Messe vorgestellt: auf dem Stand der Initiative (Halle 4, Stand E42) und am 26. April auf dem „Tag der Massivumformung“.
Ende 2014 bis Oktober 2015 analysierten die 28 beteiligten Unternehmen und Institute das Referenzfahrzeug: einen Transporter mit 3,5 t Gesamtgewicht, Nutzlast inklusive, mit einem 120 kW starken Antrieb, 2,1 Liter Hubraum und Turbo-Diesel-Direkteinspritzung, dazu einem manuellen Getriebe und Heckantrieb.
Fazit: Von untersuchten 2.394 kg Fahrzeuggewicht entfielen 845 kg auf massivumgeformte Bauteile: Sie bildeten das Optimierungspotenzial der Studie. Die anschließende Untersuchung ergab ein Einsparpotenzial von 99 kg. Dieses liegt, da in der Karosserie überwiegend Stahl- und Aluminium-Blechteile verwendet werden, besonders in Antriebsstrang und Fahrwerk: in Radnaben und Einspritzung, Kurbelwelle, Getriebe und anderen Bauteilen mehr.
„Das sind 99 kg, um bei gleichem Gesamtgewicht die Nutzlast zu erhöhen oder – bei gleicher Nutzlast – Gewicht und Verbrauch zu reduzieren“, skizziert Hans-Willi Raedt, die Möglichkeiten. Die Ergebnisse kommen für den Vizepräsidenten des Automobilzulieferers Hirschvogel und Sprechers der Leichtbau-Initiative nicht überraschend: „Anders als viele Karosseriebauteile erfuhren massivumgeformte Komponenten über Jahrzehnte zu wenig Aufmerksamkeit.“
Denn die Weiterentwicklung ist in der metallerzeugenden und -verarbeitenden Branche mit ihrer hohen Arbeitsteilung nicht einfach. „Ein Bauteil wie eine Kardangabel weiterzuentwickeln, bedeutet, alle Beteiligten in der Wertschöpfungskette ins Boot holen zu müssen: Stahlhersteller, Massivumformer, Zerspaner, Systemhersteller und Erstausrüster, also die Autohersteller selbst“, erklärt Raedt.
Insgesamt ermittelte die Initiative 535 Vorschläge, die in der Mehrzahl den konstruktiven Leichtbau betreffen, gefolgt von fertigungsbasierten Lösungen und stofflichem Leichtbau. Das ist für Raedt kein Zufall: „Massivumformer beherrschen konstruktive Methoden am Besten.“
3.1. Werkstofflicher Leichtbau:
Beispiel Schwenklager
Werkstoffliche Verbesserungen sind vergleichsweise langwierig umzusetzen. Neue Materialien erfordern umfangreiche Tests durch den Hersteller. Dazu kommen die Freigabeprozesse bei Systemherstellern und Erstrausrüstern.
Angesichts des Aufwands gibt es auf allen Seiten eine gewisse Zurückhaltung, neue Legierungen einzusetzen. Das gilt umso mehr, als weltweit operierende Zulieferer und Autohersteller immer auch die Logistik im Blick haben. „Das Material muss unter Umständen in Werken auf verschiedenen Kontinenten jederzeit und in ausreichender Menge zur Verfügung stehen“, sagt Raedt.
Gleichwohl lotete die Initiative auch die Möglichkeiten stofflicher Verbesserungen aus. Beim Getriebe ließen sich durch Einsatz höherwertigen, festeren Stahls (20NiMoCr6-5 statt 20MoCr4) knapp 2,5 kg von 63 kg einsparen. Die Modellrechnung ergab dabei eine Kostensteigerung von nicht einmal 1 Euro/kg eingesparten Gewichts.
„Noch festere Stähle könnten weitere Gewichtseinsparungen ermöglichen“, sagt Raedt. Bleibt das Problem: Die Einkäufer müssen mitspielen. Schließlich sehen viele Einkäufer erst auf den Einkaufspreis, dann auf den Nutzen durch sinkende Gesamtfertigungskosten.
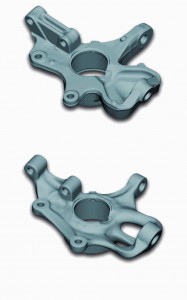
Schwenklager im Vorher-Nachher-Vergleich (Quelle: Leiber Group)
Neben höherfestem Stahl kann im werkstofflichen Leichtbau auch Aluminium zum Einsatz kommen. Beim Schwenklager der Vorderachse etwa wurde gegossenes Eisen durch geschmiedetes Aluminium ersetzt. Daraus resultierte ein Einspareffekt von rund 4.400 g. Das zum Vergleich herangezogene Serienbauteil ist 161 Prozent schwerer als der Leichtbauvorschlag: Denn Gusseisen hat eine dreimal höhere Dichte als ein Alu-Schmiedebauteil.
So einfach allerdings lässt sich nach Ansicht von Christoph Keul vom Stahlinstitut Stahl nicht durch Aluminium ersetzen. „Abgesehen von der notwendigen Werkstoffqualifizierung liegen die Kosten für Alu-Schmiedeteilen um etwa 25 Prozent über denen von Schmiedebauteilen aus Stahl.“
Es geht aber noch einfacher: Würden die 24 Radschrauben der Nfz-Studie mittels Einnapfung optimiert, ergäbe das bei 12 g pro Stück eine Gesamtgewichtsreduktion von 412 g.
3.2. Fertigungsbasierter Leichtbau:
Beispiel Hinterachse
Rund 2,5 kg Gewicht ließen sich durch eine optimierte Hinterachse einsparen, deren Beispiel zeigt: Werkstoffliche, konstruktive und fertigungsbasierte Verbesserungen sind nicht scharf von einander zu trennen. So stand am Anfang die Einsicht, dass durch Einsatz höherfesten Stahls eine Gewichtsverringerung erreicht werden könnte: durch das Material selbst, aber auch konstruktiv durch die Möglichkeit, ein Rohr mit konstanter Wanddicke durch eines ungleichmäßiger Stärke zu ersetzen. So wiegt das herkömmliche Bauteil, das beiderseits des Differentialgehäuses verbaut wird, 44 Prozent mehr. Der Einsatz des belastungsoptimierten Bauteils aber erfordert, im dritten Schritt, die Anpassung des Fertigungsablaufs durch Einsatz eines Rundknetprozesses.
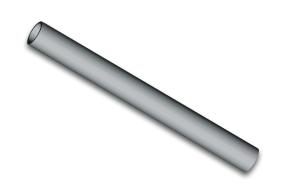
Hinterachse vor und nach der Optimierung (Quelle: voestalpine Metal Engineering)
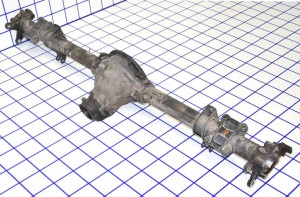
Hinterachse vor und nach der Optimierung (Quelle: voestalpine Metal Engineering)
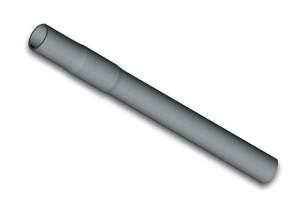
Hinterachse vor und nach der Optimierung (Quelle: voestalpine Metal Engineering)
3.3. Konstruktiver Leichtbau:
Beispiel Einspritzleiste
Die Einspritzleiste (Common Rail) wurde gleich mehrfach verändert. Man setzte höherfesten bainitischen Stahl ein und änderte den Durchmesser der im Prinzip rohrförmigen Einspritzleiste in Abhängigkeit von der Belastung. So wurde er mal dicker, mal dünner. So ergab sich für das neue Bauteil ein Einspareffekt von 293 g. Das zum Vergleich herangezogene Serienbauteil ist 28 Prozent schwerer.
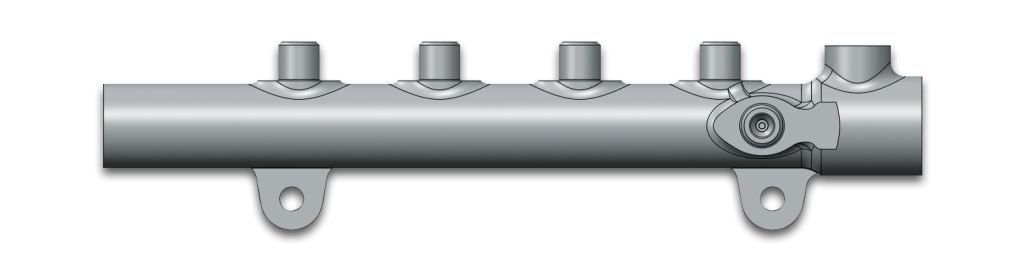
Die neu konstruierte Einspritzleiste (Quelle: Hirschvogel Automotive Group)
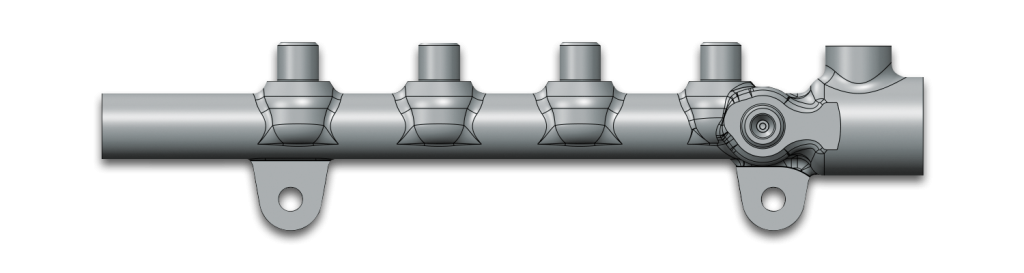
Die neu konstruierte Einspritzleiste (Quelle: Hirschvogel Automotive Group)
Für Raedt ist die Komponente ein Beispiel für die Vorteile der Massivumformung im Vergleich zur Zerspanung, mit deren Hilfe das Bauteil für gewöhnlich (und nicht nur im hier zugrunde gelegten Modell-Nfz) gefertigt wird. „Der Massivumformer denkt in freien Flächen“, sagt Raedt.
Soll heißen: Massivumformung bringt mehr Freiheit bei der Bauteilgeometrie, die hier deutlich komplizierter ist. Teurer aber käme das Bauteil im Falle des Modell-Kfz aber laut Raedt nicht. Die höheren Kosten für Material und Fertigung würden aufgewogen: durch verringerten Materialeinsatz und letztlich einfachere Prozesse. Denn die von der Leiste abgehenden Kraftstoffabgänge können zusammen mit der Leiste selbst geschmiedet werden. Beim zerspanten Bauteil müssen sie hingegen aufgeschweißt werden.
3.4. Ausblick: Wie Ideen Wirklichkeit werden
Aufschlussreich ist die Frage nach der Umsetzbarkeit der Leichtbauideen. Immerhin 45 Ideen mit einem Sparpotenzial von 23 kg (von 99 kg insgesamt), darunter die Einspritzleiste, wären innerhalb von zwei, drei Jahren vergleichsweise schnell umsetzbar (Gruppe A).
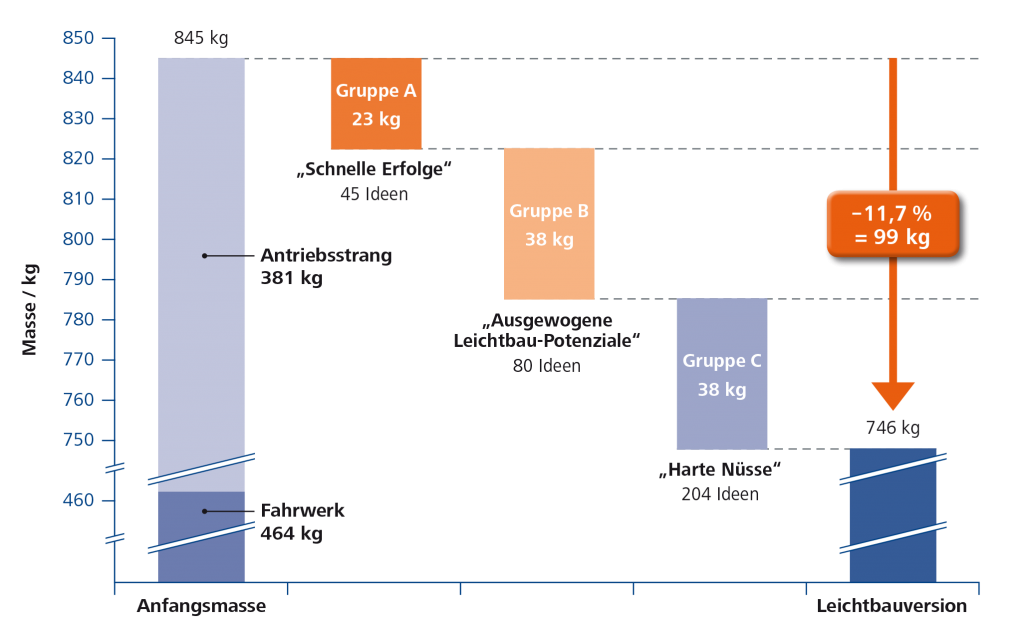
Leichtbauideen und ihre Umsetzungsmöglichkeiten (Quelle: Initiative Massiver Leichtbau)
Weitere 80 Ideen ermöglichten eine Gewichtsreduktion um 38 kg innerhalb von drei bis fünf Jahren. Allerdings beruhen das Schwenklager und viele andere Ideen dieser Gruppe B auf werkstofflichen Verbesserungen, die Komponenten eventuell auch verteuern und damit die Umsetzung erschweren.
Noch einmal 38 kg erwartet die Initiative durch die 204 Ideen der Gruppe C. Sie könnten, so Raedts Schätzung, innerhalb vier bis acht Jahren umgesetzt werden, wenn überhaupt. Nicht nur dass die Ideen meist eine nur geringe Gewichtsreduktion ermöglichen und die Produktionskosten erhöhen. Auch würde ihre Umsetzung einen vergleichsweise hohen entwicklungstechnischen und organisatorischen Aufwand nach sich ziehen.
Ein Beispiel ist die Verbindung von Kardanwelle zum Getriebe: Hier lassen sich zwar einige Hundert Gramm Gewicht einsparen, doch sind in diesem Fall gleich zwei Bauteile betroffen. „Entsprechend müssen mehr Personen und Abteilungen einbezogen werden. Und das bedeutet leider erheblich komplizierte Abläufe“, sagt Raedt.
Fachartikel zum Thema Ressourceneffizienz aus Werkstoffe in der Fertigung 2/2016