Günter Motz, Martin Günthner, Walter Krenkel
Für viele Entwicklungen im Anlagen- und Maschinenbau aber auch für den Alltag steigen die Anforderungen an die Werkstoffe, die sowohl hoheren Drücken und Temperaturen standhalten müssen als auch in chemisch aggressiven und abrasiven Medien eingesetzt werden. Einerseits lassen sich diese erhöhten Anforderungen an das Material durch den Einsatz besonders korrosionsfester und verschleißbeständiger Metalle und Legierungen realisieren, die aber meist sehr teuer sind. Andererseits werden besonders stabile Werkstoffe, wie die Keramiken eingesetzt, wobei aber nicht jedes Bauteil aus Metall durch Keramik ersetzbar ist. Für viele Anwendungen ist es jedoch oft ausreichend, wenn nur die Oberfläche eines metallischen Bauteils beschichtet wird.
Beschichtungen spielen sowohl im Alltag als auch in der Industrie eine große Rolle. In vielen Bereichen haben sich Hartstoffbeschichtungen wie Metallcarbide, -nitride, -boride oder -silizide, aber auch Diamant sehr gut bewährt. Nachteilig ist hierbei jedoch der hohe apparative Aufwand für die Verfahren (PVD, CVD, Ionenimplantation), mit denen diese Schichten aufgebracht werden sowie die daraus resultierenden hohen Kosten. Als kritisch erweist sich oft auch die Haftfestigkeit der dünnen Hartstoffschichten, insbesondere hervorgerufen durch unterschiedliche Wärmeausdehnungskoeffizienten zwischen Substrat und Schicht. Daher wird versucht, dieses Problem durch ausgleichende Zwischenschichten oder durch zusätzliche Haftvermittler zu minimieren.
Ein relativ neuer Ansatz zur Erzeugung keramischer Beschichtungen ist die Verwendung von Polymerkeramiken. Dabei handelt es sich um anorganische Materialien, die durch die thermische Behandlung meist auf Silizium basierender Polymere (Precursoren) hergestellt werden. Die auch als Precursortechnologie bezeichnete Variante der Keramikherstellung schlägt somit eine Brücke zwischen den Werkstoffklassen der Polymere und der Keramiken. Polymerkeramiken sind seit ca. 50 Jahren bekannt und stellen eine vielversprechende Alternative zu den konventionellen, auf Keramikpulvern basierenden Verfahren zur Herstellung von Keramiken dar. Der allgemeine Verfahrensweg zur Herstellung von Polymerkeramiken ist in Bild 1 schematisch dargestellt.

Bild 1: Schema zur Herstellung von Polymerkeramiken
Seit ungefähr zwanzig Jahren besteht ein besonderes Interesse an kommerziell erhältlichen Polymeren wie Polysiloxanen (Silikone), Polysilazanen, Polycarbosilanen oder Polycarbosilazanen, die als Precursoren für Keramiken in den Systemen SiOC, SiN, SiC und SiCN dienen. Die Eigenschaften dieser Polymere lassen sich nicht nur hinsichtlich ihrer chemischen Zusammensetzung sondern auch bezüglich ihrer Verarbeitbarkeit und des Grades der Keramisierung maßschneidern. Daraus ergibt sich eine Vielzahl von Anwendungsmöglichkeiten nicht nur in den für diese Stoffklasse klassischen Bereichen, wie der Herstellung von Keramikfasern und faserverstärkten, keramischen Verbundwerkstoffen, sondern beispielsweise auch als Anodenmaterial in Li-Batterien, MEMS (Micro-Electro-Mechanical System), Sensoren, Heizelementen, Glühkerzen für Dieselmotoren, Keramikschäumen oder als robuste Katalysatoren unter extremen Bedingungen.
Die Entwicklung der Polymerkeramiken wurde zunächst in den sechziger und siebziger Jahren des letzten Jahrhunderts vor allem durch die Suche nach höchsttemperaturstabilen Keramikfasern für den Einsatz in schadenstoleranten, faserverstärkten Keramiken vorangetrieben. Diese sind über die herkömmliche Pulvertechnologie nicht zugängig. Mittlerweile ist jedoch die Verwendung der Precursoren für polymere bzw. keramische Schichten mit strukturellen oder funktionellen Eigenschaften das sich am schnellsten entwickelnde Anwendungsgebiet.
Am Lehrstuhl Keramische Werkstoffe der Universität Bayreuth sind Beschichtungen auf Basis von SiCN Polymeren ein bedeutendes Arbeitsgebiet. Die Herstellung dieser Polymere erfolgt großtechnisch von der Firma MERCK KGaA, Darmstadt. In einem geeigneten Lösungsmittel gelöst, werden die SiCN Polymere mittels Tauchen, Sprühen, Pinseln oder Spin-Coating auf das entsprechende Substrat aufgebracht. Nach dem Trocknen härten die Schichten spontan durch die Reaktion mit Luftfeuchtigkeit unter Ausbildung einer hervorragend auf vielen Substraten haftenden SiOC bzw. SiOx-Schicht aus. Bild 2 zeigt die aus der Herstellungstemperatur resultierende Aufteilung in polymere und keramische Schichten, deren Eigenschaften sowie Anwendungen.

Bild 2: Herstellung und Anwendungen von Beschichtungen auf Polysilazanbasis
Eine typische Anwendung für die polymeren, transparenten Schichten ist der Kratzschutz von Kunststoffoberflächen. Eine chemische Modifizierung des Beschichtungssystems ermöglicht die Herstellung von hydrophilen (anti-fog) und hydrophoben (easy-to-clean) Oberflächen. Kommerziell werden bereits Anti-Graffiti-Beschichtungen auf Basis von Organopolysilazanen unter der Bezeichnung tutoPROM® bei Zügen der Deutschen Bahn AG und anderer Unternehmen eingesetzt (Bild 3). Anorganische Silazanpolymere (PHPS) unter dem Markennamen AZ Spinfil® dienen als Isolations- und Füllmaterialien in der Chipherstellung. Sowohl tutoPROM® als auch AZ Spinfil® sind Produkte der MERCK KGaA, Darmstadt.
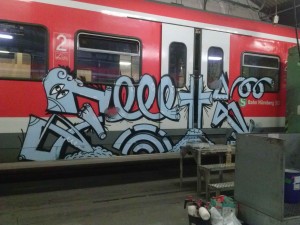
Mit tutoPROM® beschichtete Züge vor und nach der Entfernung der Graffities
Vor allem bei Bauteilen, die bei höheren Temperaturen und in aggressiven Umgebungen eingesetzt werden, sind dünne aber dichte Schichten aus präkeramischen Polymeren ein wirkungsvoller Schutz. Im polymeren Zustand sind diese Schichten bis zu Temperaturen von 500 °C einsetzbar, schützen vor Korrosion und Oxidation und sind stabil gegen Lösungsmittel. Bild 4a zeigt eine Silazanschutzschicht auf Kupfer nach der Oxidation bei 500 °C. Es ist deutlich zu sehen, dass sich die nur 1 µm dicke Beschichtung hervorragend eignet, um Bauteile aus Kupfer, beispielsweise für die Elektronik, vor Oxidation bzw. Korrosion zu schützen. Der sehr oxidationsstabile Edelstahl 1.4301 (V2A) bildet trotz seines relativ hohen Chromanteils eine dunkle Zunderschicht bei der Oxidation an Luft bei hohen Temperaturen. Durch die Aufbringung einer dünnen, keramisierbaren Silazanschutzschicht wird die Bildung der Oxidschicht sogar bis zu Anwendungstemperaturen über 1000 °C vermieden (Bild 4b).
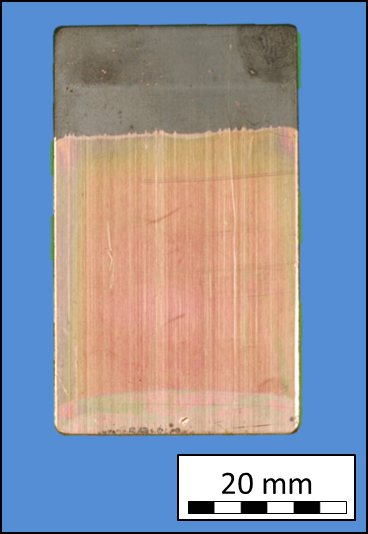
Bleche aus Kupfer (a) und V2A-Stahl (b) mit Polysilazan im unteren Bereich durch Tauchen beschichtet und bei 500 bzw. 1000 °C an Luft für jeweils eine Stunde ausgelagert.
(a)
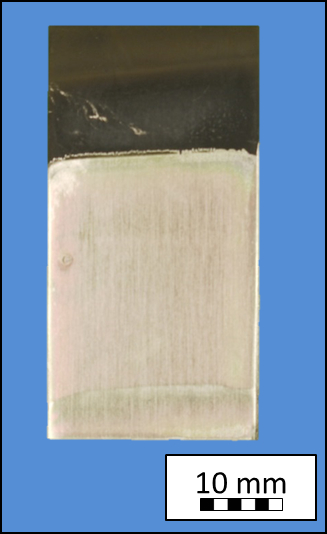
Bleche aus Kupfer (a) und V2A-Stahl (b) mit Polysilazan im unteren Bereich durch Tauchen beschichtet und bei 500 bzw. 1000 °C an Luft für jeweils eine Stunde ausgelagert. (b)
Eine besondere Herausforderung stellt ein kombinierter Korrosions- und Verschleißschutz von unedlen Stählen in extrem aggressiven Atmosphären, wie beispielsweise in Müllverbrennungsanlagen, dar. Hier reichen dünne Keramikschichten nicht mehr aus, um die Stähle zu schützen. Eine Möglichkeit, dickere und verschleißbeständige Schichten zu realisieren, ist das Einbringen von harten keramischen Füllstoffen in die Polymerkeramik, wodurch sowohl die Schichtdicke als auch die Härte erhöht werden können. Das am Lehrstuhl Keramische Werkstoffe hierfür entwickelte Beschichtungssystem besteht aus einem Organopolysilazan, Zirkonoxid als harter, nanokeramischer Füllstoff und Glaspulver zur Abdichtung der teilweise porösen Schichten während der Herstellung (Bild 5). Nach der Applikation und Pyrolyse des Mehrkomponenten-Schichtsystems bildet sich eine harte und bis zu 100 µm dicke Schicht, die sehr diffusionsstabil ist und sich somit auch unter extremen Bedingungen wie im Kraftwerksbereich einsetzen lässt. Die in Bild 5 erkennbare Porosität ist geschlossen und wirkt sich daher nicht negativ auf die Schutzfunktion aus.
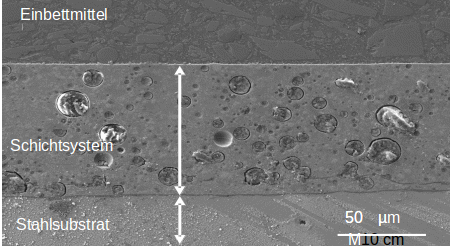
Mehrkomponentenbeschichtung auf Precursorbasis hergestellt bei 700 °C
Eine Möglichkeit zur Reduktion der Korrosion und damit von Instandhaltungskosten, z.B. in Müllverbrennungsanalgen, ist der Einsatz von geeigneten Schutzsystemen. Daher wurde das in den Bildern 5 und 6 abgebildete Schichtsystem bei 530 °C in einer für Müllverbrennungsanlagen typischen Salzschmelzemischung für eine Woche ausgelagert. Hierbei konnte weder eine Korrosion der Schutzschicht noch eine Diffusion korrosiver Spezies durch die Beschichtung zum Stahlsubstrat beobachtet werden. Da korrosiv hoch belastete Bauteile in Kraftwerken bei regelmäßigen Revisionen begutachtet und gegebenenfalls im Zuge von Instandhaltungsmaßnahmen ausgetauscht werden müssen, kann die neuartige Mehrkomponentenbeschichtung einen wesentlichen Beitrag zur Reduzierung der Instandhaltungsaufwendungen leisten.
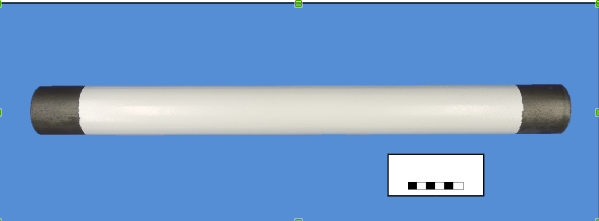
Stahlrohr aus 13CrMo4 mit keramischer Schutzschicht auf Precursorbasis
Die ausgewählten Beispiele zeigen die vielfältigen Anwendungsmöglichkeiten und das Potenzial der Polymerkeramikschichten auf. Einerseits lassen sich die Schichten mit gewöhnlichen Lackierverfahren aufbringen. Andererseits können die Schichteigenschaften in einem weiten Bereich vom Kunststoff bis hin zur Keramik eingestellt und an die jeweiligen Anforderungen angepasst werden.
Fachartikel zum Thema Polmerkeramikschichten aus Werkstoffe in der Fertigung 6/2015