Einleitung
Die Isolierung von Schwingungen während der spanenden Bearbeitung ist ein wichtiger Faktor zur Ausführung eines stabilen Fertigungsprozesses und wirkt sich somit direkt auf das zu erzielende Ergebnis und die Lebensdauer von Werkzeugen aus. Dabei gilt besonders die Dämpfung von schneidnahen Schwingungen als hocheffektiv.
Schwingungskritische Bearbeitungssituationen können durch die strukturdynamischen Eigenschaften der Maschine bei fast allen Bearbeitungsprozessen entstehen, so dass Technologieparameter, die für eine wirtschaftliche Bearbeitung signifikant sind, nicht voll ausgenutzt werden können [1]. Gängige Lösungsansätze zur Minimierung dieser Probleme sind passive Zusatzsysteme wie Hilfsmassendämpfer oder Schwingungstilger oder aktive Zusatzsysteme bei denen Energie von außen zugeführt werden muss. Hierbei handelt es sich jedoch um kundenspezifische und damit aufwändige und kostenintensive Lösungen [2].
In dem aktuellen Forschungsvorhaben IGF 20957 N werden Formgedächtnislegierungen im pseudoelastischen Werkstoffzustand eingesetzt, um nicht gewollte Schwingungen am Schneidwerkzeug zu dämpfen. Dazu wird der Effekt der mechanisch induzierten Pseudoelastizität genutzt, der ein besonders hohes quasi-elastisches Verformungsvermögen aufweist. Das Vermögen zur elastischen Verformung liegt bei Formgedächtnislegierungen in einer kristallographisch reversiblen Martensit-Austenit-Phasenumwandlung begründet [3]. Während eines Be- und Entlastungszyklus (in Form der zu betrachtenden zyklischen Schwingungsbelastung) eines FG-Elements wird eine ausgeprägte Umwandlungshysterese (charakterisiert durch Stauchung des FG-Elements und korrelierender anliegender mechanischer Spannung) durchlaufen, worauf ihr Dämpfungspotential basiert [4]. Eine größere durchlaufene Hysterese (hinsichtlich eingeschlossener Fläche) entspricht dabei einem höheren Dämpfungsvermögen (dissipierte Energie). Der Zusammenhang ist in Abbildung 2 dargestellt.
Um die gewünschten Dämpfungseffekte zu realisieren, müssen die FG-Elemente in den Kraftfluss der schwingungskritischen Maschinenkomponenten integriert werden. Dadurch werden die Elemente in den meisten Anwendungsszenarien einer Druckbelastung ausgesetzt. Da der Fokus von bisherigen Untersuchungen zum Dämpfungsverhalten von FGL zumeist auf den typischerweise zugbelasteten Drähten lag, war es notwendig grundlegende Untersuchungen zum Verhalten von druckbelasteten FG-Elementen in verschiedenen Werkstoffzuständen durchzuführen, um so die generelle Eignung zu identifizieren. Dazu wurden in [5] Druckversuche unter geringen dynamischen Belastungen an zylindrischen FG-Probekörpern mit parallel geschliffenen Stirnflächen durchgeführt. In diesem Zusammenhang wurde das Spannungs-Stauchungs-Verhalten in Abhängigkeit von unterschiedlichen Wärmebehandlungszuständen der FG-Elemente untersucht. Um die so gewonnenen Erkenntnisse durch Auswirkungen weiterer Einflussfaktoren auf das Materialverhalten zu ergänzen und dadurch eine breitere Datenbasis für die nächsten Entwicklungsschritte zu schaffen, wurden die Untersuchungen um die Einflüsse unterschiedlicher Legierungszusammensetzungen auf die Spannungs-Stauchungs-Eigenschaften unter geringen dynamischen Lasten erweitert.
Prüfstand und Versuchsmaterial
Es wurde das Spannungs-Stauchungs-Verhalten von drei binären NiTi-Legierungen eines Herstellers untereinander verglichen. Unter den bekannten FG-Legierungen verfügen NiTi-Basislegierungen über ausgeprägte pseudoelastische Eigenschaften sowie eine hohe Ermüdungs- und Korrosionsbeständigkeit. Allerdings bewirken bereits marginale Abweichungen in der anteiligen Zusammensetzung der Legierungselemente Nickel und Titan (<0,1 Gew.-%, die Zusammensetzung kann aus Datenblättern des Herstellers entnommen werden) erfahrungsgemäß starke Unterschiede in resultierenden Materialeigenschaften, insbesondere in den Phasenumwandlungstemperaturen. In Tabelle 1 sind die Materialparameter sowie die Abmessungen der erstellten Probekörper für die hier vorgestellten Druckversuche dargestellt.
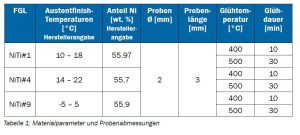
Tabelle 1: Materialparameter und Probenabmessungen
Die Parameter für die Wärmebehandlungen wurden auf Grundlage der in [5] erhaltenen Erkenntnisse ausgewählt. Bei diesen Kombinationen von Glühtemperatur und -dauer zeigten sich dort deutliche Unterschiede im Spannungs-Stauchungsverhalten und daher das Potenzial für ein breites Einsatzspektrum.
Zur Durchführung der Stauchversuche wurde an einer Zug-Druck-Prüfmaschine des Herstellers TIRA GmbH ein Versuchsaufbau mit Vorrichtungen zur Krafteinleitung, zur Führung des Probekörpers und zur externen Wegmessung eingerichtet. Der Aufbau ist in Abbildung 1 dargestellt.
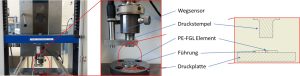
Abbildung 1: Zug-Druck-Prüfmaschine und Versuchsaufbau
Versuchsdurchführung
Die FG-Probekörper wurden mithilfe einer Führung auf der Druckplatte positioniert und eine Kraft über den Druckstempel auf die Stirnfläche der Proben bis zu einer Probenstauchung von 4 % der Ausgangslänge aufgebracht. Anschließend erfolgte die Rücknahme der Belastung bis zur vollständigen Entlastung der Probekörper. Die resultierenden Kraft-Weg Punkte wurden aufgezeichnet, in Spannungs-Stauchungs-Kurven umgewandelt und anschließend anhand festgelegter Auswertekriterien analysiert. Zu diesen Kriterien zählen die Hystereseenergie sowie die maximal erreichte mechanische Spannung. Weitere Versuchsparameter sind die Prüfgeschwindigkeit (0,005 mm/s) sowie die Umgebungstemperatur (20 °C).
Versuchsergebnisse
In Abb. 2 sind die resultierenden Spannungs-Stauchungs-Kurven der Druckversuche dargestellt.
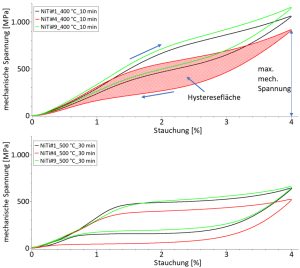
Abbildung 2: Resultierende Spannungs-Stauchungs-Kurven infolge einer Wärmebehandlung von 400 °C für 10 min (oben, mit Kennzeichnung der Hysteresefläche und der max. mech. Spannung) und 500 °C für 30 min (unten)
Zu Versuchsbeginn lagen die Materialien im austenitischen Zustand vor. Dies ist die Voraussetzung für das pseudoelastische Verhalten durch Bildung von spannungsinduziertem Martensit. Das resultierende Verhalten lässt sich nach einem zunächst annähernd linear-elastischen Anstieg bei sämtlichen Versuchskurven beobachten, allerdings verlaufen die Anstiege der Spannungsplateaus bei der höheren Glühtemperatur von 500 °C und längerer Wärmebehandlung wesentlich flacher. Es sind deutlich geringere mechanischen Spannungen notwendig, um gleiche Stauchungswerte zu erzeugen. Die Entlastung verbunden mit der Rückumwandlung in die austenitische Phase sowie der Wiedererlangung der ursprünglichen Probenform und -abmaße liegt insgesamt auf deutlich geringeren Spannungsniveaus. Es zeigt sich ein hysteresebehaftetes Verhalten. Eine tiefergehende Erläuterung der werkstofflichen Zusammenhänge lässt sich in [6] finden. Weitere relevante Unterschiede zwischen den untersuchten Materialzusammensetzungen in Verbindung mit der Wärmebehandlung wurden anhand der zuvor festgelegten Auswertekriterien deutlich gemacht (Abbildung 3).
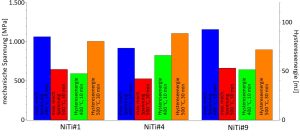
Abbildung 3: Vergleich der max. mechanischen Spannungen und Hystereseenergie
Im Vergleich der maximalen mechanischen Spannungen zeigen sich deutlich höhere Werte infolge der Wärmebehandlung mit der geringeren Glühtemperatur von 400 °C. Betrachtet man die Materialzusammensetzungen liegen die maximalen mechanischen Spannungen bei der Legierung NiTi#9 am höchsten, gefolgt von NiTi#1 und NiTi#4.
In Bezug auf die Hystereseenergie, also die Fläche, welche durch die Spannungs-Stauchung-Kurve eingeschlossen wird, resultiert die höhere Glühtemperatur von 500 °C in höheren Werten. Im Vergleich der verschiedenen Legierungen zeigt sich bei NiTi#4 der höchste Wert, gefolgt von NiTi#9 und NiTi#1.
Über die korrekte Wahl der Legierungszusammensetzung lässt sich somit bereits entscheidend Einfluss auf die Eigenschaften des Dämpfungselements nehmen. Es ist nicht ausreichend eine Legierung zu wählen, die im pseudoelastischen Werkstoffzustand vorliegt. Wie man den Ergebnissen entnehmen kann, weisen die untersuchten Legierungen, obwohl alle im pseudoelastischen Zustand vorliegen, deutlich unterschiedliche Dämpfungspotentiale auf.
- Mit steigender Differenz zwischen der Umwandlungstemperatur Af und der Einsatztemperatur (TUmgebung) korrelieren gleiche Stauchungswerte mit höheren mechanischen Spannungen sowie geringerer Hystereseenergie. Elemente aus diesen Legierungen können also als steifer betrachtet werden.
- Darüber hinaus lässt sich die Eignung einer gewählten Legierung zur Nutzung als Dämpfungselement anpassen, in dem man das Halbzeug einer Wärmebehandlung mit veränderten Parametern unterzieht. So kann man auch bei einer nicht optimal getroffenen Werkstoffauswahl das Dämpfungselement doch noch den geforderten Dämpfungseigenschaften annähern.
Unter dem vorliegenden Belastungsfall (vBelastung = 0,005 mm/s, TUmgebung = 20 °C) stellen Dämpfungselemente aus der Legierung NiTi#4 die geeignetste Wahl zur Schwingungsdämpfung unter Druckbelastung dar, wenn eine hohe Isolierung von auftretenden Schwingungen gewünscht wäre. Für beide Wärmebehandlungszustände weist diese Legierung die geringsten mechanischen Spannungen bei gleichzeitig maximaler Hystereseenergie auf. Durch Erhöhung der Wärmebehandlungstemperatur und Verlängerung der Wärmebehandlungsdauer lässt sich die Eignung von Elementen aus NiTi#4 weiter steigern. Für Systeme mit steiferen Anforderungen sollten hingegen Dämpfungselemente aus NiTi#9 gefertigt werden.
Zusammenfassung und Ausblick
Insgesamt wird anhand der gezeigten Versuchsergebnisse der hohe Einfluss der Materialzusammensetzung in Verbindung mit den Wärmebehandlungsparametern auf das Spannungs-Stauchungs-Verhalten deutlich. In Bezug auf die Wärmebehandlung ist es einerseits notwendig den Prozess mit hoher Präzision auszuführen, da die Eigenschaften sehr sensibel auf variierende Prozessparameter reagieren. Andererseits bieten sich Möglichkeiten zur Anpassung des Materialverhaltens an die individuellen Gegebenheiten des Anwendungsfalls.
Das Potenzial zur Realisierung von Dämpfungsfunktionen konnte bei sämtlichen FG-Probekörpern in Form der vorhanden Hystereseenergie nachgewiesen werden. Bei der Legierungsauswahl ist zusätzlich die Höhe der Phasenumwandlungstemperaturen ein wichtiges Kriterium. Diese stehen in einem engen Zusammenhang mit den resultierenden Niveauhöhen der mechanischen Spannungen in Abhängigkeit der Umgebungstemperatur.
Um weitere Erkenntnisse zum Dämpfungsverhalten der Materialien zu erhalten, werden in den nächsten Arbeitsschritten weitere Einflussfaktoren in die Versuche einbezogen. Hierzu zählen die Zyklenbeständigkeit des Materialverhaltens, der Einfluss der Umgebungstemperatur und das Nachgiebigkeitsverhalten von eingebauten Dämpfungselementen. Im Anschluss daran erfolgt die Übertragung auf Dämpfungselemente für einen beispielhaften Use-Case, der auf der Grundlage der Versuchsergebnisse ausgewählt wird sowie die Untersuchung der Dämpfungseigenschaften im anwendungsnahen Zustand.
Das IGF-Vorhaben 20957 N „Einsatz von Formgedächtnislegierungen zur Bedämpfung von Werkzeugschwingungen im Fräsprozess“ der Forschungsvereinigung Forschungsgemeinschaft Werkzeuge und Werkstoffe e.V. (FGW), Papenberger Straße 49, 42859 Remscheid, wird über die AiF im Rahmen des Programms zur Förderung der industriellen Gemeinschaftsforschung (IGF) vom Bundesministerium für Wirtschaft und Klimaschutz aufgrund eines Beschlusses des Deutschen Bundestages gefördert.
Literaturverzeichnis
[1] Weck, M.: Brecher, C.: Werkzeugmaschinen Fertigungssysteme 1, Springer Verlag, Berlin, 9. Auflage, 2019
[2] Schmidt, S.: Verteilte Mehrmassendämpfer für Werkzeugmaschinen, Apprimus Verlag, Aachen, 2019
[3] Czechowicz, A., Langbein, S.: Konstruktionspraxis Formgedächtnistechnik, Springer Vieweg Verlag, Wiesbaden, 2013
[4] Schröder, B.: Dämpfungseigenschaften von Formgedächtnislegierungen, Dissertation am Institut für Statik und Dynamik der Luft- und Raumfahrtkonstruktionen der Universität Stuttgart, Stuttgart, 2001
[5] Brecher, C., Neus, S., Klumpen, N., Dültgen, P., Theiß, R., Krieg, R., Hoffmann, F.: Investigation of transformation behaviour of pseudoelastic NiTi shape memory alloys under compressive loading to asses the potential use in vibration damping in milling operations, Proceedings of the ASME 2021 Conference on Smart Materials, Adaptive Structures, and Intelligent Systems SMASIS, 2021
[6] Gümpel, P.: Formgedächtnislegierungen: Einsatzmöglichkeiten in Maschinenbau, Medizintechnik und Aktuatorik, Renningen: Expert Verlag, 2004
Infos zu den Autoren
Autoren: Christian Brecher, Stephan Neus, Niclas Klumpen, Peter Dültgen, Ralf Theiß, Romina Krieg, Simon Horn, Fabian Hoffmann
Prof. Dr.-Ing. Christian Brecher ist Professor und Inhaber des Lehrstuhls für Werkzeugmaschinen, Niclas Klumpen M. Sc. ist wissenschaftlicher Mitarbeiter in der Gruppe Maschinenuntersuchung & -beurteilung und Dipl.-Ing. Stephan Neus ist Oberingenieur und Leiter der Abteilung Maschinentechnik, alle am Werkzeugmaschinenlabor WZL der RWTH Aachen, Lehrstuhl für Werkzeugmaschinen. Dr.-Ing. Dipl.-Wirt.-Ing. Peter Dültgen ist Geschäftsführer der Forschungsgemeinschaft Werkzeuge und Werkstoffe e.V., Dr.-Ing. Ralf Theiß ist dort Wissenschaftlicher Direktor, Dr. rer. nat. Romina Krieg ist dort Bereichsleiterin für Werkstoffe, Fabian Hoffmann, M. Eng. und Simon Horn, B. Eng., sind dort wissenschaftliche Mitarbeiter.
Kontakt:
Tel. +49 2191-5921-143
hoffmann@fgw.de