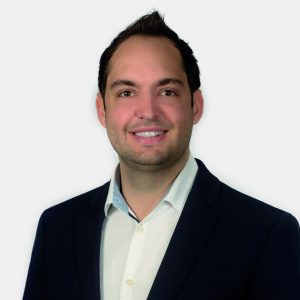
Dr. Sebastian Kirmse, Dr.-Ing. in Systems Engineering, Senior Consultant im Bereich R&D Transformation
bei MHP (Quelle: MHP)
Z-Threaded Carbon Fiber Reinforced Polymer (ZT-CFRP)
Leichtere, leistungsfähigere und multifunktionale Werkstoffe sind mittlerweile in allen Branchen gefragt. Der innovative Verbundwerkstoff ZT-CFRP, der von einer Forschungsgruppe der University of South Alabama entwickelt wurde, kann die Nachteile herkömmlicher kohlenstofffaserverstärkte Polymere (CFRP) überwinden und neue Möglichkeiten in der Produktion bieten. Mithilfe von MHP soll ZT-CFRP nun marktfähig gemacht werden.
Es ist nichts Neues, dass Automobil- und Flugzeughersteller schon seit vielen Jahren den Leichtbau forcieren, um kraftstoffsparende Vehikel auf den Markt zu bringen. Dabei sollen Materialien zum Einsatz kommen, die nicht nur leicht, sondern zugleich robust sind und den Insassen damit Sicherheit bieten. Wenn sich die Materialien dann noch sehr effizient herstellen lassen ist das der Idealfall.
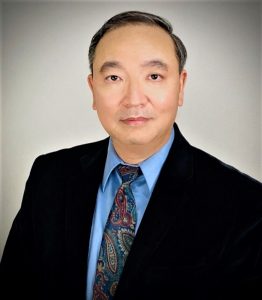
Prof. Kuang-Ting Hsiao, Ph.D. in Mechanical Engineering, Professor & Graduate Coordinator an der
University of South Alabama (Quelle: University of South Alabama)
Wie dringend hier neue Lösungen gesucht werden, zeigt eine Berechnung der Deutschen Rohstoffagentur, dem Fraunhofer-Institut für System- und Innovationsforschung ISI und dem Fraunhofer-Institut für Zuverlässigkeit und Mikrointegration IZM: Die Autoren rechnen für das Jahr 2040 mit einer jährlichen Lieferung von circa 440 Großraumflugzeugen, deren Airframes (Rumpf, Tragflächen und Triebwerksgondeln) mit einem durchschnittliche Leergewicht von 110 t ungefähr zur Hälfte aus Verbundwerkstoffe bestehen dürften. Sie gehen auch davon aus, dass in Großraumflugzeugen wie dem Airbus 350 oder der Boeing 787 Dreamliner die Verbundwerkstoffe, allen voran CFK, ihre bereits heute dominierende Rolle mit Gewichtsanteilen von circa 50 Prozent festigen wird. Zum künftigen Bedarf an Kohlenstofffaserverstärkte Kunststoff (CFK) und anderen Verbundwerkstoffen für den Bau von Flugzeugrümpfen machen die Autoren jedoch keine konkreten Angaben. Fakt ist, dass der Bedarf nach CFK und alternativen Verbundwerkstoffen steigt, der auch im Fahrzeugbau zum Einsatz kommt. CFK hat viele Vorteile, aber auch einige Nachteile: Beispielsweise ist der Kunststoff anfällig gegen mechanische Kräfte wie Stoßschäden, und hat eine geringe elektrische und thermische Leitfähigkeit über die gesamte Dicke. Alternative Materialien werden gesucht, die die Nachteile verringern. Eine Forschungsgruppe an der University of South Alabama, unter der Leitung von Prof. Kuang-Ting Hsiao, hat deshalb das Nanokomposit ZT-CFRP (Nanofiber Z-Threaded Carbon Fiber Reinforced Polymer), was ursprünglich von der NASA unterstützt wurde, entwickelt. Um ZT-CFRP schnell auf den Markt zu bringen, hat die Universität eine Forschungspartnerschaft gegründet, die von der National Science Foundation (NSF) der USA finanziert wird. Neben der University of South Alabama sind fünf Unternehmen aus verschiedenen Sektoren an der Partnerschaft beteiligt, die verschiedene Kompetenzen mitbringen: MHP, Porsche Motorsports, UST Mamiya, Hexcel Corporation und Toray Composite Materials America. MHP, eine Management- und IT-Beratung, fällt bei dieser Kooperation eine Schlüsselrolle zu. Das Unternehmen wird in enger Zusammenarbeit mit der Hochschule dabei unterstützen, einen Roll-to-Roll-Fertigungsprozess für ZT-CFRP zu gestalten, der die Produktion großer Mengen zu niedrigen Kosten ermöglicht.
Aufbau und Eigenschaften des Nanokomposits ZT-CFRP
Der mit Nano-Partikeln angereicherte und mit Kohlenstofffasern verstärkte Kunststoffverbund ZT-CFRP unterscheidet sich in einer Reihe von Eigenschaften von anderen Verbundwerkstoffen seiner Gruppe: Lange, ultradünne Kohlenstoff-Nanofasern (CNF) fädeln sich durch ein Bett aus herkömmlichen, dickeren Kohlenstofffasern, die alle von einem Epoxidharz umgeben sind. Ein z-gerichtetes Fädeln durch das Kohlenstofffaserbett ist so möglich, ohne die Dicke und das Volumen des CFRPs zu erhöhen. Dabei werden dickere Kohlenstofffasern durch die Nanofasern fest miteinander verbunden und gestützt. Aufgrund des Zick-Zack-Fadenlaufs verzahnen sich die Nanofasern mit den Kohlenstofffasern. Weil die CNF lang genug sind, um 10 bis 50 Kohlenstofffasern miteinander zu verbinden, entsteht außerdem ein neuartiger 3D-Mikrostruktur-Verbundwerkstoff, der viel stärker ist als Epoxidharz allein oder herkömmliche Kohlenstofffaser-Verbundwerkstoffe. Das Netzwerk aus ineinandergreifenden Kohlenstoff-Nanofasern und Kohlenstofffasern verbessert die Fähigkeit des Verbundwerkstoffs, mechanische, elektrische und thermische Energie durch alle Teile des Materialsystems in alle Richtungen zu leiten. Dadurch erhöhen sich die Festigkeit und die Leitung von Wärme und Elektrizität massiv (vor allem orthogonal zur Faserrichtung).
Leichter als Aluminium und widerstandsfähiger als Stahl
Damit ist ZT-CFRP nicht nur leichter als Aluminium und widerstandsfähiger als Stahl, das Komposit ist auch deutlich weniger anfällig gegen mechanische Kräfte als bislang übliche mit Kohlenstofffasern verstärkte Kunststoffe. Darüber hinaus verringert die große elektrochemische Potenzialkompatibilität zwischen Kohlenstofffasern und Kohlenstoffnanofasern mögliche Korrosionsprobleme. Im Vergleich dazu weisen herkömmliche CFK, die in der Regel in Form von Laminaten hergestellt werden, keine z-förmigen Nanofasern auf und haben in der Dickenrichtung deutlich schlechtere Eigenschaften. CFK-Produkte, die mit herkömmlichen CFK-Prepregs hergestellt werden, sind weniger robust und haben eine höhere Schadensanfälligkeit als CFK-Produkte, die mit Prepregs auf Basis der ZT-CFRP-Technologie produziert werden können. Außerdem fehlen ihnen elektrische und thermische Leitfähigkeiten, wodurch viele Herausforderungen in der Entwicklung und Herstellung der Produkte für verschiedene Verbundwerkstoffmärkte, Anwender und Designer entstehen. Mithilfe von ZT-CFRP lassen sich die bestehenden Probleme lösen und neue Möglichkeiten entstehen, die die Fähigkeiten von CFK-Verbundwerkstoffen sowohl für die akademische Forschung als auch für die kommerzielle Nutzung verbessern.
Prepreg-Herstellungsprozess ohne weitere Anpassungen
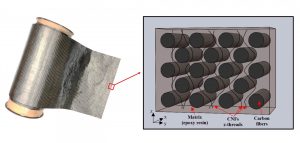
Eine illustrative Ansicht der ZT-CFRP-Nanokompositstruktur. ZT-CFRP wird sowohl als Prepreg-Rolle als auch als dünner Harzfilm zur Optimierung herkömmlicher Prepreg-Materialien oder zur klebenden Verbindung zweier Materialien mit verbesserter mechanischer, thermischer und elektrischer Verbindung und Haltbarkeit erhältlich sein. (Quelle: University of South Alabama)
Das ZT-CFRP-Prepreg kann mit einem proprietären modifizierten Rolle-zu-Rolle-Heißschweißverfahren („hot-melt process“) in drei Stufen hergestellt werden.
- Zunächst wird der Harzfilm erzeugt, der Kohlenstoff-Nanofasern enthält, die in Richtung der Dicke (d. h. in
z-Richtung) ausgerichtet sind. Dies geschieht mit einer von Prof. Kuang-Ting Hsiao Forschungsgruppe entwickelten automatisierten Harzfilm-Produktionsmaschine. Ein dünner Harzfilm, der nicht ausgerichtete CNF enthält, durchläuft ein elektrisches Feld, wodurch die CNF schnell in z-Richtung des Harzfilms ausgerichtet werden. - Dieser Harzfilm wird nun in einer modifizierten Heißschweiß-Prepreg-Produktionsmaschine mit speziellen Heiz- und Kühlelementen verwendet, um einen speziellen Fließübertragungsprozess zu erzeugen, der das Harz und die Nanofasern in ein trockenes Faserbett überträgt, wodurch schließlich das ZT-CFRP-Prepreg entsteht. Während des Fließübertragungsprozesses fädeln die z-ausgerichteten Nanofasern im Zick-Zack durch die Kohlenstofffasern. Dies wird auch als „z-Fädeln“ bezeichnet.
- In der letzten Stufe wird ZT-CFRP-Prepreg wie ein herkömmliches Prepreg auf einer kontinuierlichen Rolle aufgewickelt.
Die Art und Weise wie ZT-CFRP hergestellt werden kann, ermöglicht ein wettbewerbsfähiges Produktionsverfahren. Das bedeutet, die ZT-CFRP-Prepregs sind mit den Preisen für herkömmliche Prepregs vergleichbar. Hersteller von Verbundwerkstoffprodukten können das ZT-CFRP-Prepreg verwenden, ohne dabei ihr bestehendes Herstellungsverfahren oder ihre Produktionslinien zu ändern. Auch sind keine zusätzlichen Produktionsschritte erforderlich – Hersteller können das Verfahren ohne weitere Anpassungen in die bestehende CFK-Teileproduktion einfach übernehmen. Dadurch entstehen erhebliche Wettbewerbsvorteile für den Hersteller und Kosten können eingespart werden, da die ZT-CFRP-Technologie einfach und unkompliziert übernommen werden kann. Außerdem lässt sich das Produktionsvolumen aufgrund des Heißschweißverfahrens flexibel skalieren.
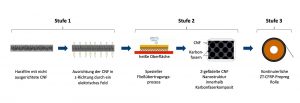
ZT-CFRP Prepreg-Herstellungsverfahren. Das ZT-CFRP-Prepreg kann mit einem proprietären modifizierten Rolle-zu-Rolle-Heißschweißverfahren („hot-melt process“) hergestellt werden. Hersteller von Verbundwerkstoffprodukten können ZT-CFRP ohne Änderung der bestehenden Produktionsverfahren verwenden. (Quelle: Dr. Sebastian Kirmse)
Verschiedene Einsatzmöglichkeiten des Nano-Prepreg
All das eröffnet ein breites Spektrum von lohnenden Einsatzmöglichkeiten in unterschiedlichen Bereichen – vom Golf-Sport über die Automotive-Branche bis zur Luft- und Raumfahrt. Um ein Beispiel weiter auszuführen: In der Automobilindustrie steigt die Nachfrage nach Leichtbauwerkstoffen. Das hat zwei Gründe. Zum einen soll die Fahrzeugmasse durch den Einbau schwerer Batterien für den Elektroantrieb besser ausgeglichen werden. Zum anderen sind Umweltauflagen, beispielsweise eine bessere Kraftstoffeffizienz, zu erfüllen. Mithilfe des Verbundwerkstoffs können Fahrzeuge hergestellt werden, die eine hohe Sicherheit für die Insassen garantieren und gleichzeitig leichter sind, wodurch der Energieverbrauch sinkt. Konkret könnte ZT-CFRP das heute für das Chassis übliche Aluminium ersetzen. Mit herkömmlichen Kohlenstofffaserverstärkter Kunststoff war das nicht immer möglich – vor allem für Teile, die erhöhten Wärmebelastungen ausgesetzt sind. Darüber hinaus könnte der Nanoverbundstoff die derzeitigen Konstruktionsbeschränkungen aufgrund der erhöhten Haltbarkeit, Scherfestigkeit und elektrischen und thermischen Leitfähigkeit verringern.
ZT-CFRP bei Flugzeugen: 100-mal bessere Leitfähigkeit als herkömmliches CFK
Wie bei Automobilen könnte der neue Verbundwerkstoff auch bei Flug- und Raumfahrzeugen in ähnlicher Weise zum Einsatz kommen. Die Luft- und Raumfahrtindustrie könnte besonders von der erhöhten thermischen und elektrischen Leitfähigkeit der Nanomaterialien profitieren: Moderne Luft- und Raumfahrzeuge sind mit kilometerlangen Kabeln und vielen elektronischen Geräten ausgestattet. Der Schutz vor Blitzschlag und die Abschirmung elektromagnetischer Wellen sind entscheidend für die Sicherheit der Flugzeugzellen und der Passagiere. Bei Flugzeugen aus CFK, zum Beispiel dem Airbus 350WXB und der Boeing 787, wird die CFK-Haut mit einem dünnen Metallgewebe umwickelt und verklebt, um den Schutz vor Blitzschlag und EM-Abschirmung zu gewährleisten. Das Metallgeflecht ist umständlich in der Herstellung, Montage und Reparatur, nicht besonders haltbar und reduziert die Vorteile von CFK in Bezug auf Gewicht und Korrosionsbeständigkeit. CFK mit höherer elektrischer Leitfähigkeit würde eine effektivere Ableitung der elektrischen Energie ermöglichen und die durch einen Blitzeinschlag verursachten lokalen Schäden verringern oder beseitigen. Eine elektrische Leitfähigkeit in z-Richtung von mehr als 10 S/m kann bereits ein zufriedenstellender EM-Abschirmungsschutz erreichen. ZT-CFRP-Laminat kann bereits eine Leitfähigkeit von 16 S/m erreichen, also 100-mal mehr als herkömmliches CFK. Die entsprechend hohe Wärmeleitfähigkeit kann auch dazu beitragen, die lokale thermische Degradation und die durch ohmsche Erwärmung verursachten Schäden zu verringern. Der Synergieeffekt aus elektrischer und thermischer Leitfähigkeit sowie die hervorragenden mechanischen Eigenschaften (z. B. gegen Vogelschlag) machen ZT-CFRP auf dem Luft- und Raumfahrt- sowie dem Verteidigungsmarkt wettbewerbsfähig.
Das Material bringt dank seiner multifunktionalen Eigenschaften ein erweitertes Spektrum an Applikationsmöglichkeiten mit sich, welche während des Projektes in Zusammenarbeit mit den Partnern erforscht werden sollen. Ziel des Projekts ist es, ZT-CFRP bis 2024 auf den Markt zu bringen. ZT-CFRP wird sowohl als Prepreg-Rolle als auch als dünner Harzfilm zur Optimierung herkömmlicher Prepreg-Materialien oder zur klebenden Verbindung zweier Materialien mit verbesserter mechanischer, thermischer und elektrischer Verbindung und Haltbarkeit erhältlich sein.
Vorteile ZT-CFRP – innovatives Nano-Komposit
- Verbesserte mechanische, thermische und elektrische Eigenschaften in allen Richtungen (nicht nur in z-Richtung) durch das 3D-Faser-Verstärkungsnetzwerk.
- Verbesserte mechanische Verstärkung in z-Richtung, Scherverstärkung in x- und y-Richtung und Druckfestigkeit in Längsrichtung (d. h. in x-Richtung).
- ZT-CFRP-Pregeg kann die Kosten, Masse, Energie und Materialien von CFK-Produkten reduzieren und zu nachhaltigeren und leistungsfähigeren Applikationen beitragen.
- Die Erhöhung der thermischen und elektrischen Leitfähigkeit kann neue nützliche Funktionen in CFK-Bauteilen ermöglichen, wie z. B. elektromagnetische Abschirmung und hohe Wärmeableitung in Kombination mit hoher mechanischer Festigkeit, wie sie in Hochleistungs-Verbrennungsmotoren und Hochleistungs-Elektromaschinen erforderlich sind.
- Bessere Prozesseffizienz durch schnelles Aushärten ohne Wärmestau, der das Harz entzünden oder rissig machen könnte. Dies hat das Potenzial, die Herstellungszeiten und -kosten zu senken und gleichzeitig bessere multifunktionale Verbundwerkstoffteile zu liefern.