Einführung und Prozessgrundlagen Laserpolieren
Da Polierprozesse einen großen Einfluss auf die funktionalen und ästhetischen Eigenschaften haben, spielen sie in vielen Branchen eine entscheidende Rolle in den Fertigungsketten. Derzeitige automatisierte Poliertechniken können häufig nicht für Teile mit Freiformflächen und funktionsrelevanten Kanten verwendet werden. Daher erfolgt die Endbearbeitung dieser Teile häufig manuell. Aufgrund der geringen Bearbeitungsgeschwindigkeit (typischerweise im Bereich von 1 bis 30 min / cm²) und des sequentiellen Arbeitsablaufs ist das manuelle Polieren komplexer Freiformoberflächen zeitaufwändig und kostenintensiv. Darüber hinaus hängt die resultierende Oberflächenqualität von den Fähigkeiten und der Tagesform des Polierers ab. Ein neuer Ansatz zur Automatisierung der Politur auch komplexer Freiformoberflächen stellt das Laserpolieren dar. Die vollständige Automatisierung, die Bearbeitungsgeschwindigkeit und die Beibehaltung der Form sind die drei Hauptvorteile. Zudem ist das Laserpolieren ein sehr sauberes Verfahren, da die Werkstücke nicht mit Schleif- oder Polierstäuben und -mitteln verunreinigt werden.
Beim Laserpolieren wird die Strahlung eines fasergekoppelten Nd: YAG-Lasers (λ = 1030 nm) auf eine metallische Oberfläche fokussiert. Eine dünne Oberflächenschicht wird geschmolzen und aufgrund der Oberflächenspannung kommt es zu einer Materialumverteilung, wodurch die Oberfläche geglättet wird. Ein meist kreisförmiger Laserstrahl wird mit der Vorschubgeschwindigkeit und einem definierten Spurabstand auf konturangepassten Bahnen in einem mäanderförmigen Muster über die Oberfläche geführt. Die Prozessparameter (z. B. Laserleistung, Vorschubgeschwindigkeit, Strahldurchmesser und Spurversatz) müssen an die Ausgangsrauheit, das Material und die gewünschte Rauheit angepasst werden. Um Oxidationen zu vermeiden, findet der Laserpolierprozess unter Inertgasatmosphäre statt. Ähnlich dem manuellen Polieren wird das Laserpolieren meistens in mehreren Schritten durchgeführt werden. Makrostrukturen wie Fräsriefen werden durch kontinuierliche Laserstrahlung (Makropolieren) geglättet, wodurch ein kontinuierliches Schmelzbad entsteht. Die Umschmelztiefen können bis zu 200 µm betragen, liegen aber meist zwischen 30 und 100 µm. Um den Glanzgrad der polierten Oberfläche zu verbessern, wird gepulste Laserstrahlung verwendet (Mikropolieren). Das Mikropolieren ist eine Kombination aus dem Umschmelzen einer dünnen Oberflächenschicht von weniger als 5 µm und dem Verdampfen von Mikropeaks. Im Gegensatz zum kontinuierlichen Umschmelzprozess für das Lasermakropolieren ist das Lasermikropolieren ein diskreter Umschmelzprozess. Das geschmolzene Material ist bereits wieder verfestigt, wenn der nächste Laserpuls auf die Oberfläche trifft und ein neues Schmelzbad erzeugt.
Die Oberflächenqualität laserpolierter Oberflächen hängt von verschiedenen Faktoren ab, insbesondere vom Material und dessen Homogenität sowie der Ausgangsrauheit. Typische Rauheiten nach dem Laserpolieren liegen im Bereich von Ra = 0,1-0,5 um. Somit stellt das Laserpolieren ein automatisiertes Polierverfahren für Anwendungen mit mittleren Qualitätsanforderungen dar.
Maschinentechnik
In Zusammenarbeit mit Industriepartnern hat das Fraunhofer ILT zwei industrielle Laserpoliermaschinen für unterschiedliche Anwendungen im Metallbereich entwickelt. Im Rahmen des vom Bundesministerium für Bildung und Forschung (BMBF) geförderten Projekts „ALPINE“ haben die Maschinenfabrik Arnold, die S & F-Systemtechnik und das Fraunhofer ILT die weltweit erste Laserpoliermaschine entwickelt (siehe Abb. 1, links).
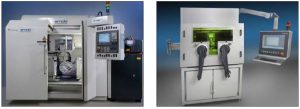
Abbildung 1: links: Laserpoliermaschine „ALPINE“, rechts: Laserpoliermaschine „MediSurf“
Basis der Laserpoliermaschine ist eine 5-Achs-Portalmaschine zur Positionierung des Werkstücks und zur Durchführung von langsamen Vorschubbewegungen. Zur Realisierung für das Laserpolieren benötigter großer Vorschubgeschwindigkeiten und insbesondere großer Beschleunigungen in den Bahnumkehrpunkten wird das 5-Achs-System mit einem hochdynamischen 3-Achs-Laserscanner kombiniert und synchronisiert. Zur Bestimmung der Werkstückposition und -orientierung ist ein taktiler Sensor in die Laserpoliermaschine integriert. Eine bewegliche Schutzgaskammer schützt das Werkstück vor Oxidationen.
Für das Laserpolieren kleinerer Teile, wie z. B. Implantaten für medizinische Anwendungen, ist die „ALPINE“-Bearbeitungsmaschine überdimensioniert und damit unnötig teuer. Daher wurde am Fraunhofer ILT im Rahmen des vom Bundesministerium für Wirtschaft und Energie (BMWi) geförderten Projekts „MediSurf“ eine zweite Werkzeugmaschine für das Laserpolieren von Teilen bis zu 1 Kilogramm entwickelt (siehe Abb. 1, rechts). Diese Maschine enthält einen 6-Achs-Roboter anstelle der herkömmlichen 5-Achs-Portalmaschine der „ALPINE“-Maschine sowie einen 3-Achs-Laserscanner. Der Roboter dient zur Positionierung des Werkstücks während des Poliervorgangs sowie zum Transport der Bauteile. Die Maschine verfügt über eine Vorkammer, so dass die Schutzgasatmosphäre permanent erhalten bleibt, auch wenn Teile in die Prozesskammer eingelegt oder entnommen werden.
CAM-NC-Prozesskette
Die für das 3D-Laserpolieren notwendige konturangepasste Bahnplanung erfolgt mit der Schlichtoperation konventioneller CAM-Software für 5-Achs-Fräsanwendungen (z. B. Power Mill, Siemens NX). Konventionelle Cam-Software ist allerdings nicht in der Lage, die Kombination der zwei kinematischen Systeme (also den 5 mechanischen Achsen/6-Achs-Roboter und den 3 Achsen des Laserscanners) zu verarbeiten und alle für das Laserpolieren relevanten Informationen bereitzustellen. Daher wurde ein Postprozessor speziell für die Laserpolitur entwickelt, der sogenannte „Technologieprozessor“. Dieser konvertiert die Werkzeugbahnen in Laserpolierbahnen unter Berücksichtigung verschiedener Anpassungs- und Bearbeitungsstrategien. Der Laserscanner und die mechanischen Achsen müssen separat angesprochen werden. Deshalb generiert der „Technologieprozessor“ neben dem NC-Programm für die mechanischen Achsen auch die Befehle zur Steuerung des Laserscanners, der von der RTC Scanner-Control-Card gesteuert wird.
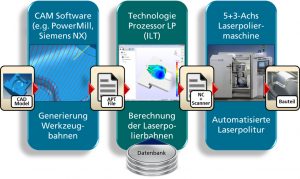
Abbildung 2: CAM-NC Datenkette für das Laserpolieren
Anwendungsbeispiel Laserpolieren
Aktuelle Hauptanwendungsgebiete für die Laserpolitur sind der Werkzeug- und Formenbau, die Medizintechnik sowie der Bereich tribologischer Oberflächen. Als Anwendungsbeispiel wird im Rahmen dieses Artikels eine tribologische Anwendung vorgestellt. Die Firma Audi poliert seit über 10 Jahren die Zylinderwände von TDI-Verbrennungsmotoren aus einem Gusswerkstoff mit Laserstrahlung. Neben der Glättung der Oberfläche verdampfen hierdurch Graphitlamellen im Werkstoff. Dies führt dazu, dass auf der Oberfläche Vertiefungen vorhanden sind, die als Schmierstoffreservoir dienen. Neben der Glättung der Oberfläche wird so das Benetzungsverhalten der Oberfläche mit Schmiermittel verbessert. Beides führt zu einer geringeren Reibung zwischen Kolben und Zylinderwand. Des Weiteren führt die Nutzung einer Stickstoffatmosphäre während der Laserpolitur zu einer Verdopplung der Oberflächenhärte. D.h. das Laserpolieren führt in einem Prozessschritt zur Optimierung dreier tribologischer Eigenschaften. Das zeigt aber auch gleichzeitig, wie komplex das Laserpolieren ist, da sich die resultierende Gefügezusammensetzung und die resultierende Oberfläche beeinflussen lassen.
Entgraten mit Laserstrahlung
Beim Schneiden bzw. Trennen metallischer Blechteile lassen sich oftmals keine grat- und defektfreien Kanten realisieren. Deshalb müssen die Kanten häufig in einem nachfolgenden Prozess entgratet oder verrundet werden. Dabei müssen unterschiedlichste Anforderungen bzgl. Optik, Haptik und Festigkeit berücksichtigt werden.
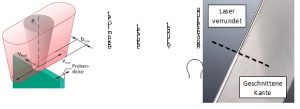
Abbildung 3: links: Verfahrensprinzip zur Laserkantenbearbeitung, mitte: unterschiedliche Kantenzustände, rechts: teilweise laserumgeschmolzene Kante
Das Entgraten und Kantenverrunden von Blechen mit Laserstrahlung ist ein Spezialfall des Laserpolierens. Wie auch beim Laserpolieren basiert das Verfahren auf dem Umschmelzen der Kante mittels Laserstrahlung, so dass die Rauheit der Kante im flüssigen Zustand aufgrund der Oberflächenspannung ausfließen kann und geglättet wird. Auch Grate können so eingeschmolzen werden. Durch eine geeignete Wahl der Verfahrensparameter kann zudem eine definierte Verrundung der Kante bis hin zu einer Randverstärkung eingestellt werden (Abbildung 3, mitte): Bei niedriger Intensität werden die Ecken leicht abgerundet, bei höherer Intensität kann ein Halbkreis oder sogar ein Pilzprofil zur Verstärkung der Kanten erzeugt werden. Durch das berührungslose Laserverfahren wird ein Verschleiß des Entgratwerkzeugs vermieden.
Zum Laserentgraten wird sowohl die Maschinentechnik als auch die CAM-NC Datenkette vom Laserpolieren genutzt. Zur Sicherstellung einer konstanten Kantenqualität ist insbesondere für die Entgratung von Freiformkanten die Nutzung eines Nahtfolgesensors sinnvoll.
Eine erste industrielle Umsetzung des Laserentgratens existiert in der Serienfertigung von Blechringen für CVT-PKW-Getriebe (Abbildung 4). Das Umschmelzen der Schubgliederketten zur Drehmomentübertragung führt zu einer Erhöhung der Dauerfestigkeit um bis zu 200% im Vergleich zum bisherigen Trovalisieren. Bislang wurden deutlich mehr als 1 Millionen Schubriemen laserumgeschmolzen.
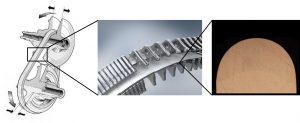
Abbildung 4: Laserumschmelzen von Schubgliederketten für CVT-Getriebe
Das Potenzial der Laserkantenbearbeitung ist damit aber erst im Ansatz erschlossen. Mögliche weitere Anwendungsfelder sind:
- Entgraten von Blechen, z.B. im Bereich Automotive, Konsumgüter, Maschinenbau, …
- Erhöhung der Korrosionsbeständigkeit durch die Entfernung von Graten und die Politur der Kante
- Erhöhung insbesondere der Dauerfestigkeit von Blechteilen durch das Verschmelzen von Mikrorissen und -defekten im Bereich der Kanten
- Verrundung von Blechen in Bereichen, in denen Kabel entlang des Bleches geführt werden. Evtl. lässt sich sogar der Kantenschutz einsparen.
Im Rahmen des Mitte 2020 gestarteten IGF-Vorhabens „LaserEdge – Laserkantenveredlung von Blechwerkstoffen zur Verbesserung der Kanteneigenschaften“ der Forschungsgemeinschaft EFB e.V. untersuchen das Institut für Eisenhüttenkunde IEHK, die RWTH Aachen und das Fraunhofer-Institut für Lasertechnik ILT unter anderem wie sich die Kanten von kaltumformbaren, hochfesten Blechen mit dem Laser entgraten und prozessbedingte Rissbildung verhindert sowie mechanische Eigenschaften in Abhängigkeit der Prozessparameter einstellen lassen. Durch die Durchführung von Lochaufweitungsversuchen konnte unter anderem eindrucksvoll gezeigt werden, dass sich durch die Laserkantenbearbeitung das Lochaufweitungsverhältnis (HER) signifikant steigern lässt.