1 Herausforderungen beim Widerstandspressschweißen von Aluminiumlegierungen
Der anhaltende Trend des Leichtbaus, u. a. in der Automobilbranche, erfordert Fügeverfahren für Leichtbauwerkstoffe wie Aluminiumlegierungen, die kostengünstig ein sicheres und zuverlässiges Ergebnis liefern. Einer der wenigen Prozesse, die diese Anforderungen erfüllen, ist das Widerstandspunktschweißen. Für das effektive Erzeugen eines Schweißpunktes ist aufgrund der geringen Stoffwiderstände und der hohen Wärmeleitfähigkeit von Aluminiumlegierungen eine sehr hohe Stromstärke bei kurzer Schweißzeit notwendig.
An der TU Dresden wird deshalb das Widerstandsschweißen mit Mittelfrequenzinvertertechnik (MF) sowie mit Kondensatorentladungstechnik (KE) untersucht.
Für die MF liegt der Forschungsschwerpunkt in der Verringerung des Elektrodenverschleißes beim Widerstandspunktschweißen sowie der Erhöhung der Prozesssicherheit, welche durch die isolierend wirkende Oxidschicht auf der Oberfläche von Aluminiumlegierungen beeinträchtigt ist. Eine Möglichkeit, den Elektrodenverschleiß zu reduzieren, ist die mechanische Zerstörung der Oxidschicht direkt vor dem Schweißen. Ein Fokus der Forschung liegt auf der reibungsfrei abrollenden und reibungsbehafteten Bewegung der Elektroden in Form einer Rotation um die Y-Achse bzw. einer Bewegung in X-Richtung.
Beim Schweißen mit KE liegt der Schwerpunkt auf der Erforschung des Verbindungsmechanismus sowie der Möglichkeit des Buckelschweißens von Funktionselementen aus Aluminium.
Um die Prozesse mit hoher örtlicher und zeitlicher Auflösung zu charakterisieren, werden Simulationsmodelle des Schweißprozesses, basierend auf der Finite-Elemente-Methode in ANSYS-Multiphysics und als Netzwerkmodell in MATLAB/Simulink erstellt. Das vereinfachte Netzwerkmodell bietet darüber hinaus die Möglichkeit der schnellen In-Situ-Simulation des Aluminiumschweißprozesses. Damit wird die Qualitätsbewertung der aktuell gefertigten Schweißlinse direkt an der Maschine möglich.
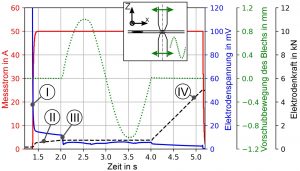
Abbildung 2 – Zeitverlauf der Elektrodenspannung bei reibungsbehafteter Bewegungsüberlagerung
vor dem Schweißstromdurchgang
2 Entwicklung neuartiger Verfahrensansätze für das Widerstandsschweißen
2.1 Widerstandspunktschweißen mit Bewegungsüberlagerung
Um das Widerstandspunktschweißen von Aluminiumwerkstoffen prozesssicher und wirtschaftlich umzusetzen, muss der negative Einfluss des initial sehr hohen und stark streuenden Kontaktwiderstands beherrscht werden. Ein bereits industriell realisierter Ansatz ist die gezielte mechanische Zerstörung der Oxidschicht auf der Blechoberfläche durch rotatorische, translatorische oder schwingende Bewegung der Elektrode. Translatorische und rotatorische Bewegungsüberlagerung werden grundlegend untersucht, um die Wirkzusammenhänge im Kontakt zwischen Elektrode und Blech bzw. zwischen den Blechen zu verstehen und für die Prozesssimulation zugänglich zu machen. Ein für das Widerstandspunktschweißen von Aluminium ausgelegter Versuchsstand mit zusätzlichen Bewegungsachsen (siehe Abbildung 1) bildet die Basis für die experimentellen Untersuchungen. Neben der Zustellbewegung in Z-Richtung (max. ca. 15 kN) ermöglicht die Kinematik die Translation der Bleche in X-Richtung sowie die Rotation der Elektrodenkköpfe um die Y-Achse. Als Stromquelle dient ein MF-Inverter (max. 50 kA). Die Elektrodenköpfe verfügen über Aufnahmen für Elektrodenkappen nach DIN EN ISO 5821 mit einem Nenndurchmesser von 16 oder 20 mm. Das Abrichten der Elektroden erfolgt automatisiert. Es können 15 Probebleche (50 x 50 mm2) eingespannt und in einem Versuchsablauf geschweißt, oder aber lange Blechstreifen sowie Proben im Halbschnitt für die Versuche verwendet werden.
Der Versuchsstand ist umfassend mit Messtechnik (Schweißstrom, Spannungen, Systemwiderstand, Kräfte und Bewegungsdaten, Temperaturen, optische Erfassung der Elektrodenoberflächen, optional Hochgeschwindigkeitsaufnahmen und Infrarot-Messung) ausgerüstet. Hervorzuheben ist die Messung des Kontaktwiderstands mittels einer zusätzlichen Präzisionsstromquelle und hochpräziser Spannungsmessung direkt an den Elektrodenkappen. Hierzu zeigt Abbildung 2 beispielhaft den Verlauf der am Versuchsstand aufgezeichneten charakteristischen Prozesskenngrößen bei der reibungsbehafteten translatorischen Bewegungsüberlagerung vor dem Schweißstromdurchgang. Anhand des Verlaufs der Anpresskraft FZ und der Elektrodenspannung UE kann der Zeitpunkt der Berührung von Blech und Elektroden bei etwa 1,25 s zugeordnet werden (I). Anschließend wird eine Anpresskraft von ca. 750 N aufgebaut (II). Mit Beginn der Bewegung des Blechvorschubs in X-Richtung bricht die Elektrodenspannung und damit der Kontaktwiderstand ein (III), was auf den gewünschten Effekt der Zerstörung und Verdrängung der Oxidschicht zurückzuführen ist. Nach erfolgter Bewegung des Blechvorschubs wird die Elektrodenkraft weiter bis auf 5 kN erhöht (IV) und kurz vorm Schweißstromdurchgang die Messstromquelle abgeschaltet. Anschließend erfolgt die Schweißung ohne zusätzliche Bewegungsüberlagerung (nicht dargestellt).
Die durchgeführten Versuchsreihen zeigen, dass mit vorgelagerter Bewegungsüberlagerung der Kontaktwiderstand vor dem Stromdurchgang etwa halbiert werden kann. Zudem wird die Streuung der Widerstandswerte verringert, was die Reproduzierbarkeit des Prozesses verbessert. Ziel weiterführender Arbeiten ist es, die ortsaufgelösten und integralen experimentell gewonnenen Daten auf die einzelnen Knoten eines Simulationsmodells zu übertragen, um vertiefende Einblicke in die verdeckt ablaufenden Prozesse in den Kontaktbereichen zu ermöglichen. Dazu kommt die 3D-Multiphysik-Prozesssimulation für das Widerstandspunktschweißen zum Einsatz.
2.2 Kondensatorentladungsschweißen von Aluminiumlegierungen im Kraftanstieg
Beim Buckelschweißen ist ein schnelles Nachsetzen der Elektroden notwendig, um die Kontaktierung der Bauteile aufrecht zu erhalten. Allerdings kommt es in Folge des langsamen Nachsetzens durch die Maschine während der Entfestigung des Buckels zu einem Abfall der Anpresskraft. Um diesen Kraftabfall zu verringern, wird die Entladung des Kondensators während des Kraftanstiegs realisiert. Der Schweißablauf wird so geregelt, dass zunächst eine Startkraft von 6 kN aufgebracht wird. Die Anpresskraft wird ausgehend von der Startkraft mit verschiedenen Kraftanstiegsgeschwindigkeiten dF/dt von 25 bis 100 N/ms um 5 kN auf eine Endkraft von 11 kN erhöht. Die Schweißung wird bei 8,5 kN ausgelöst. Das Vorgehen ist in Abbildung 3 dargestellt.
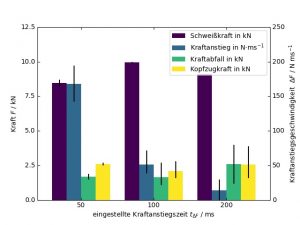
Abbildung 4: Ergebnisse der Schweißversuche, eingestellte Schweißkraft 8,5 kN, Ladeenergie 6,5 kWs, Spitzenstrom ≈ 105 kA, Stromanstiegsgeschwindigkeit 4,6 ms, spez. Energie = 3,5 kWs/50μΩ
Die Schweißkraft, der Kraftanstieg (als Differenz der gemessenen Kraft zwischen dem Auslösezeitpunkt und einer Millisekunde davor) und der auftretende Kraftabfall werden automatisiert ausgewertet. Außerdem wurde die Kopfzugkraft der geschweißten Verbindung ermittelt. In Abbildung 4 sind die Mittelwerte und die Spanne zwischen maximaler und minimaler Kopfzugkraft dargestellt. Daraus geht hervor, dass die Kraftanstiegszeit einen geringen Einfluss auf den Schweißkraftverlauf hat.
Mit steigender Kraftanstiegsgeschwindigkeit sinkt die Streuung der Kopfzugkräfte. Daraus folgt ein stabileres Prozessverhalten. Zusätzlich sinken der Kraftabfall und die Kopfzugkraft bei höheren Kraftanstiegsgeschwindigkeiten. Diese Methodik wurde analog mit einer Schweißkraft von 22 kN (Vorkraft 20 kN, Erhöhung um 5 kN, Anstiegszeiten 50 ms, 100 ms, 200 ms) untersucht. Hierbei entstehen vergleichbare Ergebnisse. Um die Versuche mit unterschiedlichen Schweißkräften zu vergleichen, wird das Verhältnis aus Kraftabfall und Schweißkraft gebildet.
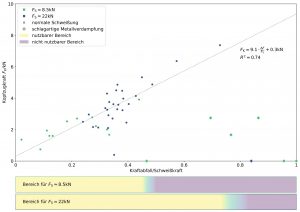
Abbildung 5: Korrelation der Kopfzugkraft mit dem relativen Kraftabfall, Ladeenergie 6,5 kWs (bei FS = 8,5 kN) und 13 kWs (bei FS = 22 kN)
In Abbildung 5 ist die Kopfzugkraft FK in Abhängigkeit dieses Verhältnisses abgebildet. Hierbei wird durch lineare Regression eine gute Korrelation sichtbar. Weiterhin sind Versuche mit schlagartiger Metallverdampfung dargestellt. Diese werden bei der Erstellung der linearen Regression nicht berücksichtigt. Zudem kann festgestellt werden, dass mit steigender Schweißkraft der zulässige Kraftabfall steigt. Bspw. kann bei einer Schweißkraft von 8,5 kN die Elektrodenkraft um 50 % abfallen (bei 22 kN um 80 %). Bei einer Elektrodenkraft unter ≈ 5 kN kam es zur schlagartigen Metallverdampfung. Es stellt sich ein sehr schmaler Übergangsbereich ein. Letztlich sorgt eine hohe Schweißkraft für höhere Kopfzugkräfte und einen größeren Schweißbereich.
3 Simulative Prozessanalyse für das Widerstandsschweißen von Aluminiumlegierungen
3.1 Hochaufgelöste Prozesssimulation von Widerstandsschweißprozessen
Mit der Multiphysikumgebung des Finite-Elemente-Systems ANSYS können Widerstandsschweißprozesse unter Berücksichtigung des Ineinandergreifens der relevanten physikalischen Domänen Elektrik, Thermik und Mechanik detailgetreu abgebildet werden. Dazu stellt die Software eine Vielzahl an Elementtypen, insbesondere auch für die Abbildung des thermisch-elektrisch-mechanischen Kontaktverhaltens, zur Verfügung. Die Simulation von Multiphysikproblemen kann über eine iterative oder direkte Kopplung erfolgen. Bei der direkten Kopplung wird ein Multiphysikelement für den Modellaufbau verwendet. Dieses vereint alle physikalischen Domänen in einer gemeinsamen Ansatzfunktion. Bei der iterativen Kopplung werden die einzelnen physikalischen Domänen sukzessive berechnet und das Ergebnis an die jeweils andere Domäne weitergegeben. Dieses Vorgehen erfordert meist mehr Ressourcen als die direkte Kopplung, ermöglicht aber einen Eingriff in die laufende Simulation, bspw. um eine neue Vernetzung zu erstellen.

Abbildung 6 Darstellung der Simulationsergebnisse der FE-Analyse (direkte Kopplung) für verschiedene Oxidschichtzustände zwischen Elektrode-Blech und Blech-Blech
In Abbildung 6 ist ein Vergleich für den Widerstandspunktschweißprozess von Aluminium für unterschiedliche Oberflächenzustände – mit und ohne Bewegungsüberlagerung, respektive mit und ohne Oxide – dargestellt. Im Vergleich der Ergebnisse zeigt sich, dass die Simulation ohne Bewegungsüberlagerung und somit mit Oxidschichten (Abbildung 6, b)) in allen Kontaktebenen die höchste Temperaturentwicklung aufweist. Eine Zerstörung der Oxidschicht zwischen Elektrode und Blech verringert die Temperatur um etwa 6 % (Abbildung 6, c)). Durch ein Entfernen der Oxidschicht in allen Kontaktbereichen (Abbildung 6, a)) kann eine Reduzierung der Temperatur um etwa 14 % erreicht werden. In beiden Fällen sinkt die Temperatur in der Kontaktzone der Elektrode unter 550 °C, was die Anlasstemperatur des CuCr1Zr Elektrodenwerkstoffs darstellt. Somit bleibt die Härte der Elektrode erhalten, was die Elektrodenstandzeit verbessert.
Aufgrund der starken Deformation bei Buckelschweißprozessen werden iterative Modelle für die Simulation verwendet. Die Wechselwirkung der thermisch-mechanischen und thermisch-elektrischen Umgebung der Simulation ist in Abbildung 7 dargestellt. Die Lösung der einen Domäne dient als Anfangsbedingung der anderen. Durch dieses Vorgehen ist eine Neuvernetzung bei großer Netzverzerrung, die bei hohen Verformungen auftritt, möglich. An der Professur für Fügetechnik und Montage werden mit dieser Methode simulative Analysen zum Einfluss unterschiedlicher Buckelgeometrien auf den Schweißprozess durchgeführt. Dies ermöglicht eine schnelle und kostengünstige Evaluierung von geeigneten Geometrien beim KE-Buckelschweißen von Aluminiumfunktionselementen.
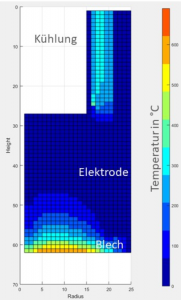
Abbildung 8 – Darstellung des Temperaturfeldes
beim Widerstandspunktschweißen von Aluminium
(Rechengitter eines FDM-Viertelmodells)
3.2 Schnelle In-Situ-Simulation für die Qualitätsbeurteilung im Prozess
Mit dem Einsatz von Leichtbauwerkstoffen wie Aluminium ergeben sich für das Widerstandspunktschweißen engere Prozessfenster bei steigenden Qualitätsanforderungen. Eine sichere Beherrschung des Prozesses bis hin zur Qualitätsbeurteilung jedes einzelnen Schweißpunktes ist notwendig, aber mittels zerstörungsfreier Prüfverfahren kaum wirtschaftlich darstellbar. Mit der Digitalisierung der Fertigung stehen über die gesamte Prozesskette vom Werkstoff zum fertigen Produkt eine Vielzahl von objektspezifischen Daten und Prozessparametern zur Verfügung. Diese können im Sinne des „Digital Twin“ für die simulationsgestützte Analyse des Werkstücks in jedem Prozessschritt herangezogen werden. Dazu soll für jeden Schweißpunkt eine in-Situ-Simulation, also eine prozessnahe und echtzeitfähige Simulation, des Widerstandspunktschweißprozesses mit den jeweils prozessaktuell und werkstückspezifisch gültigen Prozessdaten und Parametern durchgeführt und automatisiert ausgewertet werden. Kritische Verbindungen können so identifiziert und bspw. für die weitere Prüfung ausgewählt werden. Darüber hinaus kann eine auf der in-Situ-Simulation aufgesetzte Visualisierung dem Anlagenbediener einen intuitiven „Einblick“ in die gefertigte Schweißverbindung ermöglichen.
Alternativ zur Finite-Elemente-Methode (FEM) und insbesondere für gleichmäßige Rechengitter wird für die In-Situ-Simulation die Finite-Differenzen-Methode (FDM) zum performanten Lösen der zu Grunde liegenden numerischen Problemstellung eingesetzt. Die reale Schweißkonfiguration kann aufgrund der Rotationssymmetrie der Elektrodenkappe und der Spiegelsymmetrie entlang der Stoßfläche vereinfacht in der R-Z-Ebene eines zylindrischen Koordinatensystems formuliert werden. Unter Berücksichtigung dieser Randbedingungen wurde zunächst ein FDM-basiertes Simulationsmodell für das elektrothermische Verhalten der Schweißlinsenbildung entwickelt und beispielhaft in MATLAB implementiert. Es konnte das transiente Temperaturfeld für das Schweißen eines Aluminiumblechs mit einer Dicke von 2 mm und einem vereinfachten Modell der Elektrodenkappe (Typ ISO 5821 C0-16-23) simuliert werden. In Abbildung 8 ist dazu die auf 905 Gitterpunkten simulierte Temperaturverteilung im Endzustand nach einer Schweißzeit von 50 ms dargestellt. Die Simulation konnte auf einem herkömmlichen Desktoprechner (Intel Core i5-6500 CPU @ 3.2-3.6 GHz) in wenigen Minuten durchgeführt werden.
Im Rahmen der aktuellen Arbeiten wird die In-Situ-Simulation um das mechanische Verhalten (insbesondere plastisches Fließen) erweitert und die in MATLAB implementierte Simulation schließlich auf eine Maschinensteuerung portiert. Die Analyse laufender Prozesse quasi in Echtzeit scheint mit optimierten Modellen und unter Nutzung moderner Rechentechnik – bspw. auch parallele Berechnung auf FPGA – möglich.
4 Danksagung
Die vorgestellten Arbeiten sind im Rahmen der von der Deutschen Forschungsgemeinschaft (DFG) geförderten Projekte „Entwicklung einer Methodik zur simulationsgestützten Analyse von Widerstandspunktschweißprozessen mit Bewegungsüberlagerung am Beispiel von Aluminiumwerkstoffen“ (DFG-Geschäftszeichen: FU-307/11-1 bzw. GR 1458/62-1) und „Grundlagenuntersuchungen zur in-Situ-Simulation von Widerstandspunktschweißprozessen“ (DFG-Geschäftszeichen: FU-307/15-1 bzw. IH124/17-1) sowie im Rahmen des von der Arbeitsgemeinschaft industrieller Forschungsvereinigungen (AiF) geförderten Projekts „Buckelschweißen von Aluminiumlegierungen mittels Kondensatorentladungsschweißen mit veränderlicher Kraft und kraftgesteuertem Auslösen der Entladung“ (IGF-Vorhaben Nr. 19.899B) entstanden. Die Autoren danken für die großzügige Unterstützung der Forschungsarbeiten zum Aluminiumwiderstandsschweißen.
Autoren:
Uwe Füssel, Jörg Zschetzsche, Stefan Heilmann, Johannes Koal (TU Dresden, Institut für Fertigungstechnik, Lehrstuhl für Fügetechnik und Montage, FTM)
Steffen Ihlenfeldt, Jens Müller, Marcel Merx (TU Dresden, Institut für Mechatronischen Maschinenbau, Lehrstuhl für Werkzeugmaschinenentwicklung und adaptive Steuerungen, LWM)